CT型X線自動検査装置の視野間連続移動による高速検査技術
- CT
- X線
- 自動検査装置
- インライン
- はんだ検査
高度化する自動車の電子基板に対し、目に見えない部品のはんだ接合部の検査を行うため、我々はこれまでCT方式のX線自動検査装置を提供してきている。しかし、当社の従来技術である連続撮像制御を搭載したVT-X750-V1/V2では、検査対象となる視野への撮像系ステージの移動時に、停止と移動を繰り返していたため、加速と制動を行う時間のロスがあった。この問題を解決するため、加速・制動を視野間移動中に行い、視野間移動と連続撮像の連結部で停止しないことで、時間ロスをなくす技術を開発した。その結果、検査の一連動作を一筆書きのように移動することができるようになり、CT検査の高速化を実現した。本技術により、新商品のVT-X750-V3では、従来比で1.5倍速の検査速度を実現し、顧客の基板進化に追従した高速検査を実現した。本稿では、高速化に大きく寄与したオムロンのX線自動検査装置における最新技術について紹介する。
1. まえがき
持続可能な社会に向けたSDGsの浸透により、世界中でゼロエミッションへの取り組みが強化されている。それに伴い、地球温暖化防止のためのCO2排出抑制活動が急務となり、EV(電気自動車)の普及が見込まれている。
このような社会の流れから、自動車業界におけるECU(Electronic Control Unit)などの電子基板は、車内の空間快適性と機能拡充を両立するため、高密度実装となっていく。実装技術ロードマップ1)によれば、電子基板のチップ部品は、0603のサイズからさらに小型の0402の搭載比率も増加していることがわかる。特に自動車業界におけるものづくり品質の要求水準は高く、事故のない安全・安心な社会実現にむけた品質検査が実施されている。例えば、欧米の車載部品工場においては、基板の抜き取り検査ではなく、基板全数を実施することが主流となっており、はんだ形状を計測して接合強度を検査することが求められる。
こうした世の中の流れを受けて、オムロンのX線自動検査装置AXI(Automated X-Ray Inspection system)は、外観では見えない部品下面のはんだ部が検査できる装置としてSMT(Surface Mount Technology)生産ラインへ普及してきた。本稿では、従来技術の課題であった視野間移動に関する検査時間のロスをなくし、更なる高速化を実現したVT-X750-V3の技術をご紹介する(図1)。
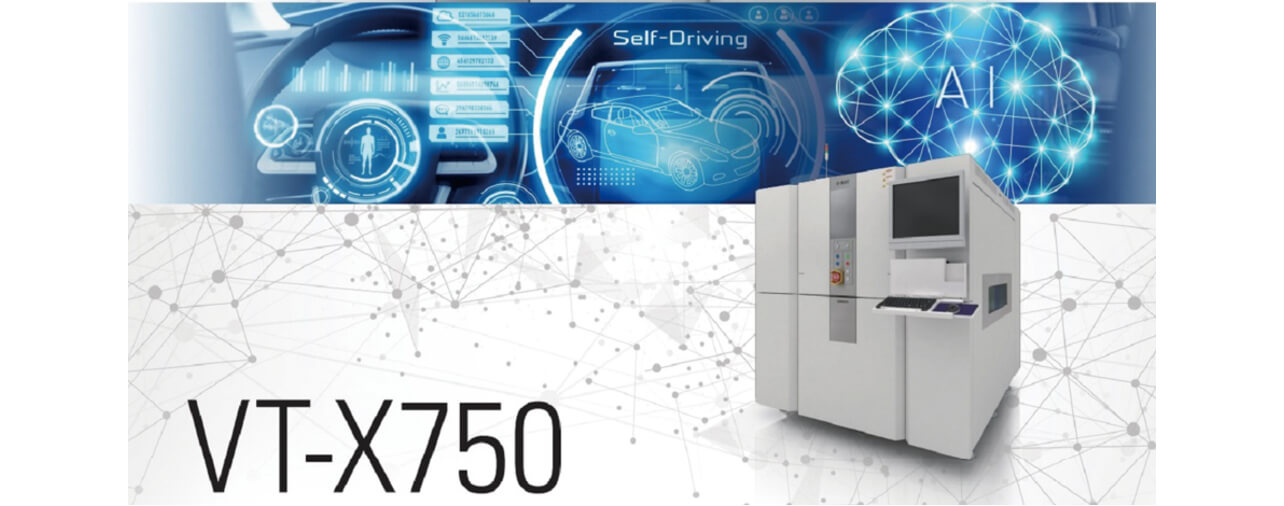
2. 高画質を実現するCT方式を用いたAXI
2.1 不可視部のはんだの不良モード
近年のめざましい電子機器の小型、軽量、高性能化傾向の技術的背景には、構成部品の高集積化、基板のファインパターン、多層実装化があり、AOI(Automated Optical Inspection)などの外観検査では、はんだ接合部の検査が困難な状況が増している。例えばBGA(Ball Grid Array)の検査では、数十~数百μmの微細なボイド(空洞)、不濡れなどのはんだ未溶融の不良モードがある(図2)。これらの電気的な安全性・信頼性を確保するためには、BGA内の1000点以上のはんだ接合部の検査を行う必要がある。
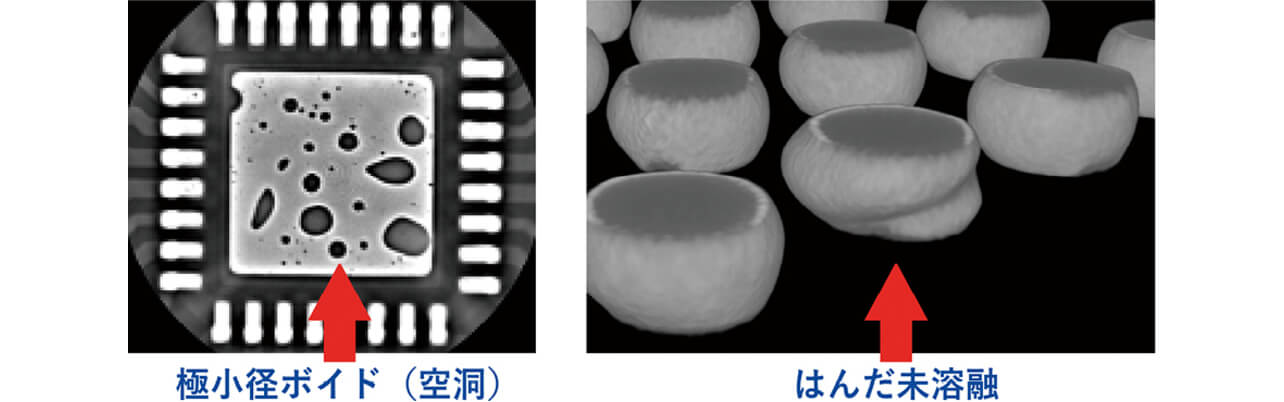
2.2 X線画像診断方式の比較
X線を用いた画像診断は、透過方式とCT方式に大別できる(図3)。
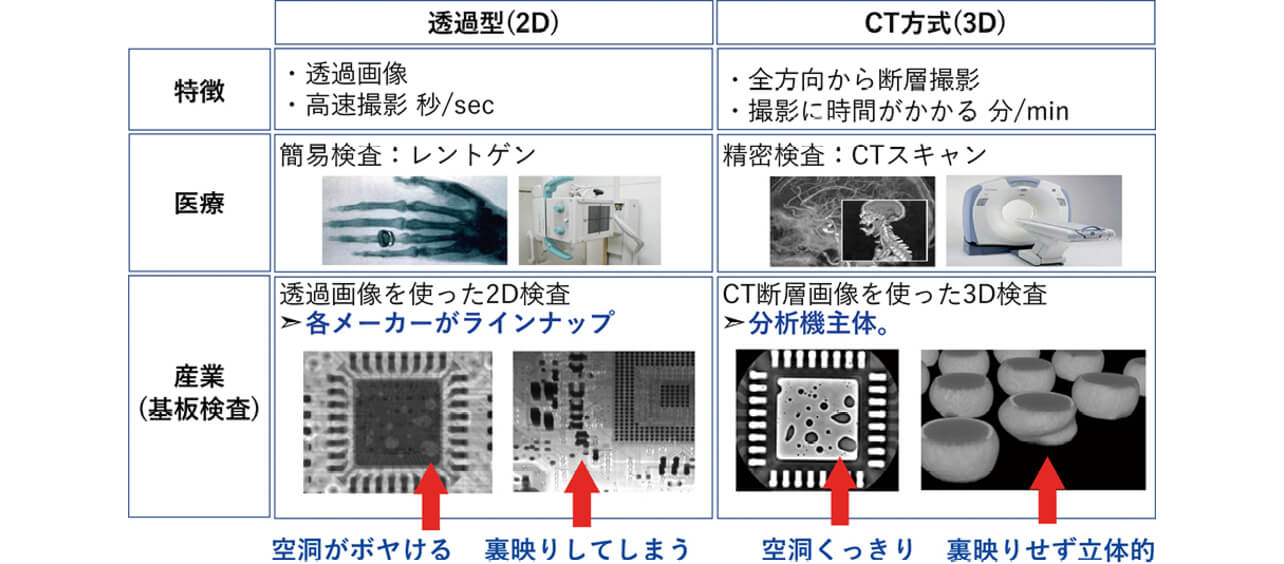
透過方式は、医療業界におけるレントゲン方式の撮影と同様に、2次元(以下2Dと表記)画像を用いた方式である。特徴として、検査点において微細な画像は得にくく、裏面の部品も重なって裏映りしてしまう。しかし、検査速度が速く、データ量も小さいため、高速な検査が求められる基板検査装置においては、2D方式を採用するメーカが多い。
CT方式は、X線カメラなどを360度方向から撮影し複数の画像を取得して、3次元(以下3Dと表記)データへ再構成する。特徴として、再構成した3D画像が鮮明になり、微細な立体的画像を得られ、かつ裏面の部品が裏映りすることはない。しかし、扱うデータ量が多くなる上、360度方向から撮像するため、検査速度は透過方式に比べて時間がかかる。よって、故障品に対する詳細な分析を行う用途として、解析機装置メーカが主に採用している方式である。
2.3 オムロンのAXI
我々は、電子基板の品質を確保し、社会を安心安全なものにしていくために、高精度かつ高速な基板検査装置を提供することが命題であると捉えている。透過型の方式では、ボイドがボヤけたり、基板の裏面部品が裏映りしてしまうため、微細なボイドや、はんだ未溶融部の精密な検査が行えない。そのため、我々はこれまでCT方式のAXIを提供してきた。2009年、VT-X700のリリース以降、2017年にX700比2倍の検査速度を実現したVT-X750-V1、2018年には更なる高分解能化を実現したVT-X750-V2をリリースし、BGAのボイド検査や挿入部品のスルーホール充填率検査などを中心に、多くの顧客の要求にこたえてきた2)。
ここで、当社のAXIの構成技術をご紹介する。当社のAXIには、多岐にわたる技術要素が組み合わさっており、AOIで積み上げた多くの知見をベースとして、高精度な検査を実現している。ここで重要となる技術要素は、高精細な画像を生成する撮像デバイス、高精度なジオメトリ設計と制御、ロバストな画像補正とアルゴリズムである。
2.4 高精細な画像を生成するデバイス(FPDとX線源)
FPD(Flat Panel Detector)は、シンチレータという蛍光体を通してX線を光に変え電気信号に変換し、デジタル画像を取得するためのカメラである。画素単位で輝度情報を読み込むため、鮮鋭性や感度の高い画像を得ることができる。
X線源には、大きく開放管と密閉管という2種類がある。密閉管は開放管に比べ、フィラメントやターゲット寿命が長いため、長時間のインライン検査に適しており、ランニングコストも低減できる。当社のAXIでは、必要十分な線量で、軽量かつ焦点径がμmオーダーのマイクロフォーカス密閉管線源を採用している。
2.5 高精度なジオメトリ設計と制御
2.5.1 ジオメトリ構成
当社のAXIのジオメトリ設計は、回転テーブル式ではなく並行テーブル式を採用している。これは、対象物に対し、X線源やFPDの位置を、XY軸方向の直行動作によって相対的に位置を変えることでCT画像を取得する方式である。この方式を採用している理由は、回転テーブル式では3Dデータの視野が円形となり狭くなってしまい、画像の端でぼやけが発生しやすいことがある。また、回転速度の制限により撮像スピードの高速化に限界があるためである3)。旧機種のVT-X700や他社製の方式は、ステージとカメラを旋回させる方式だが、VT-X750シリーズからは、検査対象物に負担をかけないよう、コンベアステージを旋回させない上下振り方式としている(図4)。
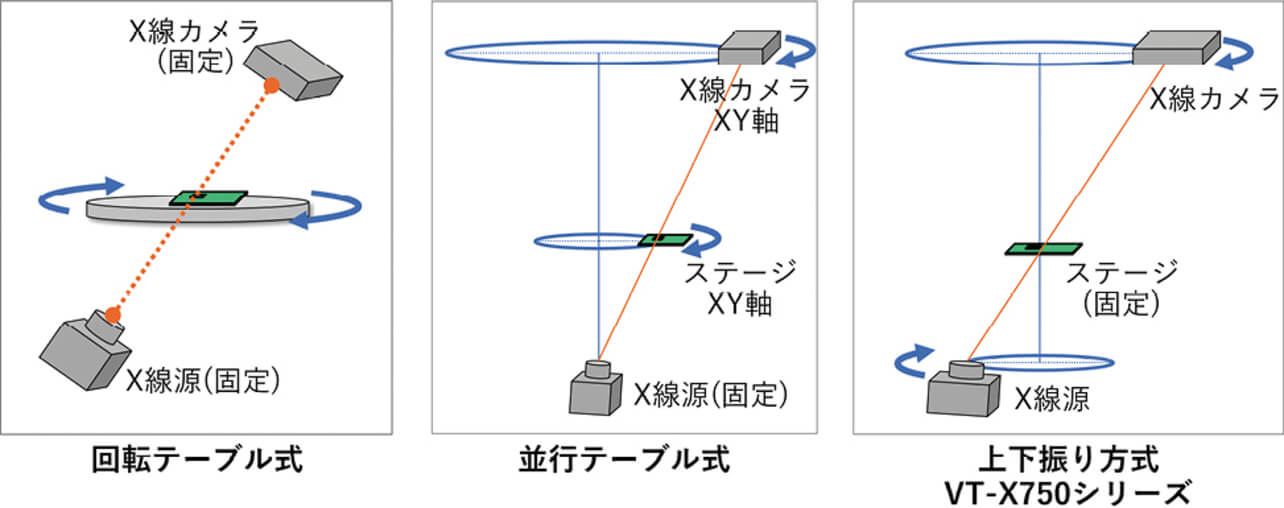
2.5.2 連続撮像技術
以下にVT-X750シリーズから搭載している「連続撮像」制御技術について述べる。大きく2つの特徴がある。
1点目は、旋回撮像時に、X線カメラとX線源のステージが止まらず動き続けるということである。各視野の撮像時間を短縮するため、非停止で連続的に旋回し、1視野分の全画像を取得する技術である(図5)。
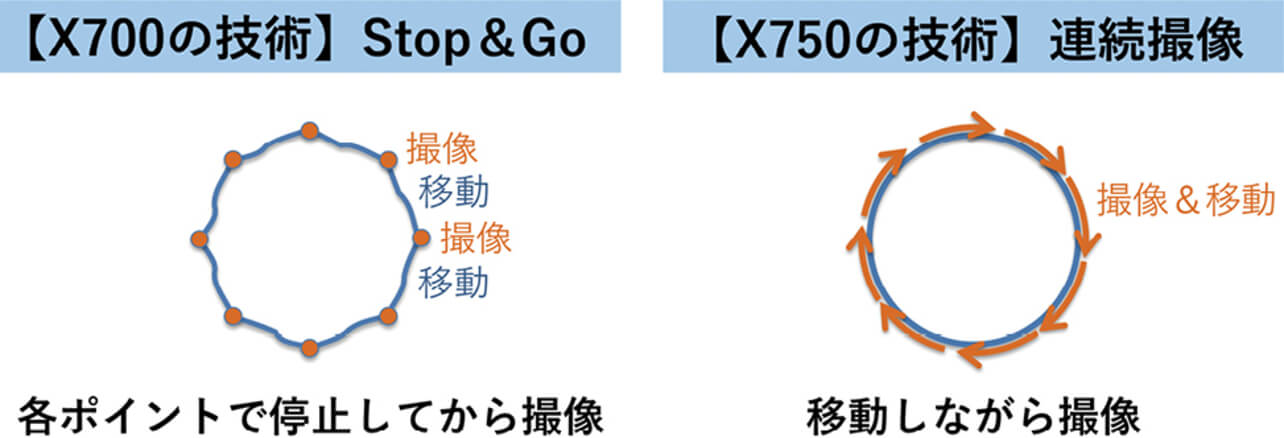
X線カメラとX線源のステージは等速で旋回する動作を繰り返すため、各軸のモータ動作をいかに同期させ、精度のよい旋回軌跡を描くことができるかが重要となる。この技術を支えているのは、オムロン製の製品、PLC(Programmable Logic Controller)のNJ、NXシリーズのコントローラと、サーボモータおよびドライバの1Sシリーズである。これらのデバイスによる多軸同期制御技術、そして、高剛性なハードウェアによって、高精度な連続撮像技術が実現できる。
2点目は、高速に撮像しデータ処理を行うシステム処理速度の高速化である。軸の動作と連動した撮像トリガシステムにて、メカが動作している最中でも高速に画像を取得できるシステムを構築している。ここで、メカが移動中に撮像する場合、画像のブレが起きやすくなることがわかっている4)。これに対し、X750シリーズでは、特殊な再構成技術(3D画像を生成する処理)と高速な撮像露光制御でブレを低減している。主にGPU(Graphics Processing Unit)を活用することによって再構成やシステム全体の処理速度を確保している。
2.6 ロバストな補正処理とアルゴリズム
当社のAXIは、ハードウェアだけでなく、独自のソフトウェアアプリケーションにて、高精度なはんだ接合面の検査を可能としている。
例えば、検査の前段としてワークが装置内へ搬入された時に、基板が停止する位置にはばらつきが存在する。このばらつきを補正するために、可視光波長のLED照明と小型カメラを搭載している。当社のAXIは、可視光波長で取得した画像を用いて、ワークのコンベア上での搬送停止位置のばらつきや回転ずれを補正する。人間の目は、可視光波長の映像・画像に見慣れているため、検査プログラムを作成する際に、設定対象となっている部品の位置確認が行いやすくなる。
高精度に画像処理を行うには、再構成後の正しい断層位置を抽出する精度が要求される。そこで、当社のAXIには、当社製の変位センサとコントローラを搭載しており、ワークの反りやたわみ量を計測して、検査面の高さ位置を補正し高精度な画像を生成している(図6)。
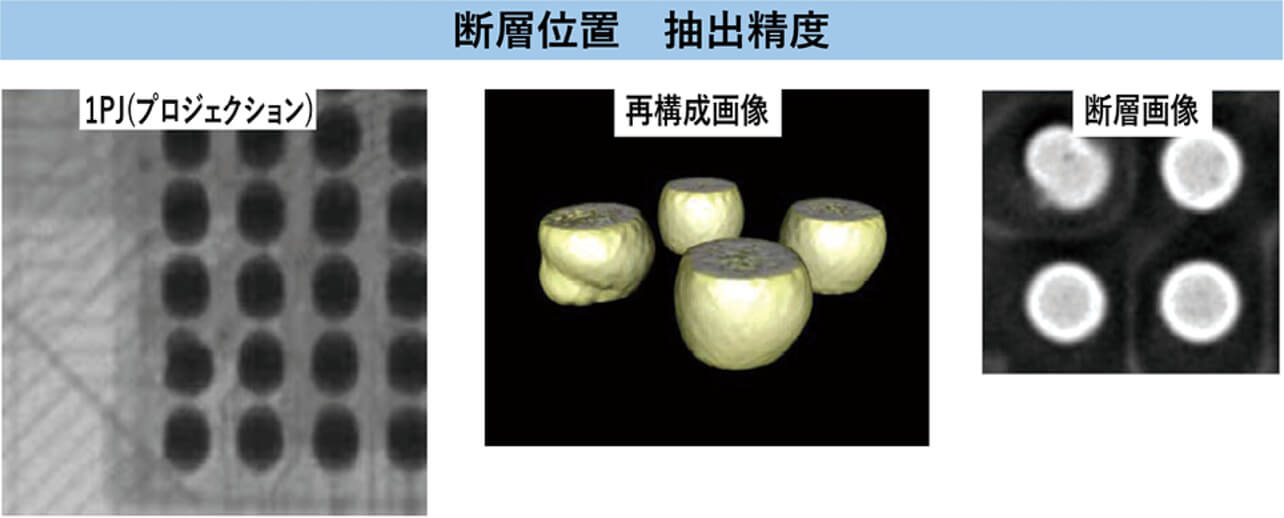
3. 基板進化に追従するための課題
CT方式の検査において、顧客の基板進化に追従しながらインライン検査を実現するためには、大きな課題が存在する。画質を確保した前提で更なる高速検査と低被曝検査の実現である。
3.1 更なる高速検査のための課題
CT撮像方式は、高精度な画質が得られる一方、検査タクト(ワーク1枚を検査する時間のこと)が長くなる。先述したようにCT方式は、360度旋回しながら撮像することが必要となるためである。AXIは基板実装のラインの後工程の装置であるため、インラインでの検査タクトの要求を満たせない場合、ラインの生産効率が低下してしまう。その結果、これまでよりも短い検査タクトや、全数検査を求めるような、要求水準の高い顧客に導入いただけないことになる。AXIの検査速度は、顧客の基板の生産性に関わるため、昨今、高速化の要求がますます高まっている。要求の水準の例としては、約200 mm角のMサイズ基板1枚当たり約30秒以下で検査することが求められるようになってきている。ここで、連続撮像における技術な問題として、視野間移動時に停止していたことによる、旋回撮像ための加速・減速時間のロスがあった。このロスに着目し解消することで、更なる高速化を実現することにした。
3.2 検査ワークへの被曝量の課題
もう1つの課題は、検査ワークへの被曝量の管理である。基板上に被曝耐性の弱い半導体素子、ICなどの部品搭載が増えているため、検査ワークへの被曝量を適切に管理しながら、被曝量を低減することが求められている。
これまでのVT-X750-V1およびV2(以下V1、V2と表記)のシステムでは、基板全体の被曝量を事前に予測し、表示する仕組みを搭載していた。しかし、IC部品個別に被曝する量を算出することができていなかったため、顧客は、基板全体の被曝量をICへの被曝量として試算せざるを得なかった。その結果、IC部品の被曝量としては過剰な値となるため、顧客は照射X線量を下げて設定せざるを得ない状況があった。X線量を下げて撮像すると画質も低下するため、最適な撮像条件で検査できない状態となってしまう。また、その逆もあり過剰にX線量を長く当ててしまう部品も存在していたため、被曝量が増えてしまう場合もあった。
よって、顧客が部品単位での被曝量を適切に管理し、検査ワークへの被曝量を低減していくことが課題であった。
4. 更なる高速検査を実現するVT-X750-V3
我々は、3章で述べたこれらの課題を解決する技術を開発した。まずは、従来技術である「連続撮像技術」と組み合わせ、更なる高速化を実現した「視野間連続移動」技術について述べる。次に、「視野間連続移動」技術の制御を応用することで実現した、被曝量のヒートマップについて示す。
4.1 視野間連続移動
本稿では新たに開発した「視野間連続移動」技術の特徴を詳しく述べる。その前段として、
①視野 ②視野間を移動する
という言葉の意味合いについて述べる。
①視野 とはp>
検査点において、再構成立体画像を生成するための撮像領域のことである。制御観点からすると、装置の天面側方向から装置内を覗き込んだトップビュー視点での撮像デバイスが描く旋回軌跡の領域のことである。これをFOV(Field of View)とよぶ。
②視野間を移動する とは
検査点から検査点へ移動することである。制御観点からすると、FOVと同様、トップビューでの撮像デバイスの旋回円から旋回円への軌跡領域のことである。
それぞれイメージを図7に示す。
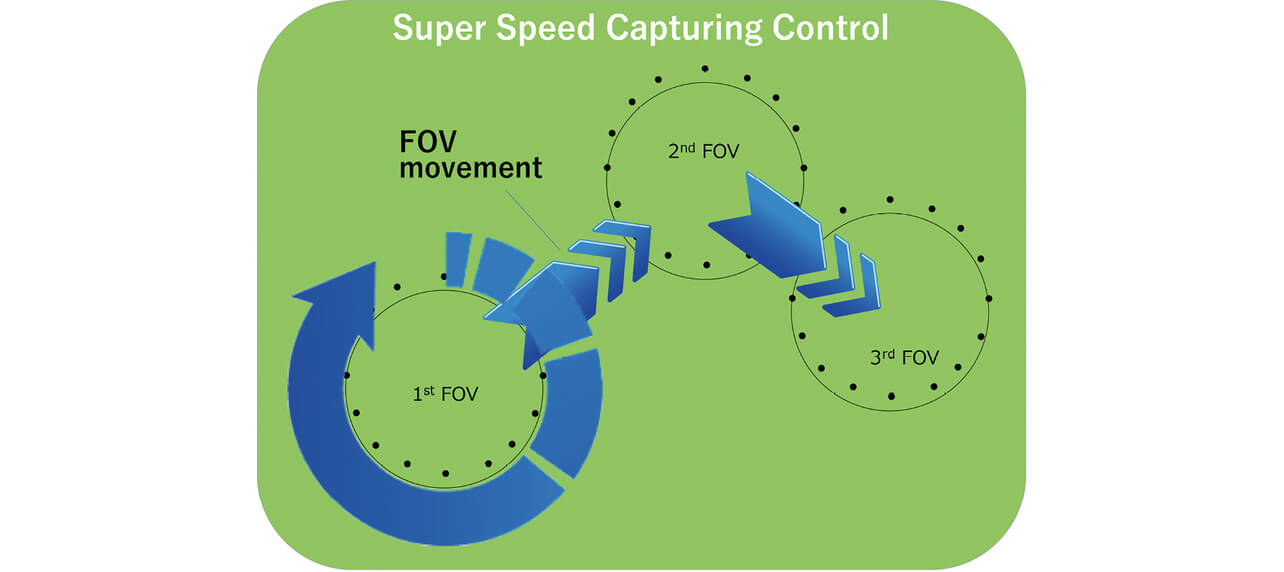
4.1.1 実現手段と特徴
「連続撮像」を行う際、高精度の画像を得るために旋回動作を等速で行う必要がある。V1およびV2までの方式では、1FOVの旋回ごとに停止していたため、等速で旋回するための加速区画と制動するための制動区画が必要となっていた。この加速・制動に時間がかかるため、これらを視野間移動中に行うことを考え、「視野間連続移動」技術を開発した。本技術は、1FOVの旋回ごとにおける加速・制動時間をなくし、視野間移動と連続撮像の連結部も非停止で動作するための技術である(図8)。
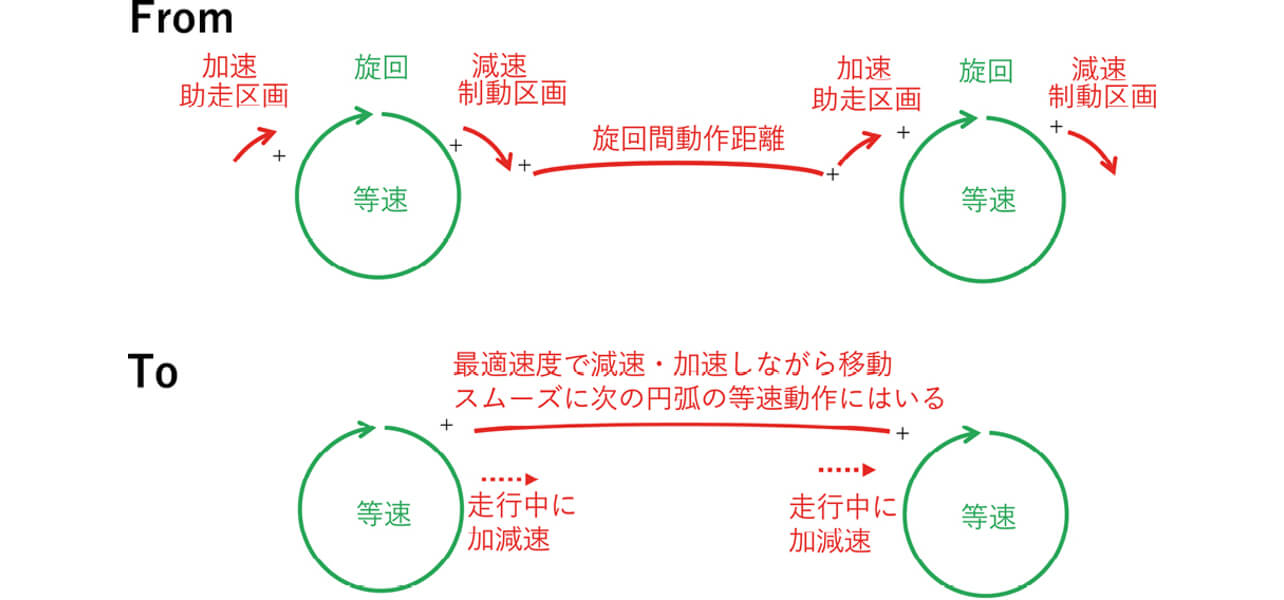
この技術は、オムロン独自の技術として開発したものであり※1、オムロン製のPLC、多軸サーボモータ、制御ソフトウェアのシームレスな同期制御によって実現した。
この「視野間連続移動」技術は、次の4つの特徴をもつ。
- 1.視野間移動において、停止区間がない
前述のとおり、最大の特徴となるのが、視野間の移動中に、次の旋回円での必要な加速を行い、視野間移動で停止区間がないことである。一連の検査を非停止で実現できる。
- 2.デバイスの許容加速度を超えないよう制御できる
視野間移動時の速度に関するパラメータを連続的に制御できる。かつ、次の視野の旋回開始始点において、加速度が0のままで旋回が開始できる。よって、撮像デバイスに対して、負荷をかけずに移動できるようになる。
- 3.最短の時間で移動できる走行ルートを選択する
次の旋回円の始点への入射角度を0°以外の角度でも行えるようになる(図9、図10)。デバイスの許容加速度を超えないような軌跡かつ、速度系の制御パラメータを演算した結果から、最も短時間で移動できる走行軌跡を導き出す。これにより、次の旋回円に移動する時間が短縮できる。
- 4.旋回速度をさらに上げることが可能になる
従来技術のまま、旋回速度を上げようとすると、問題が生じる。それは、旋回制御は、高精度な画質を撮像するために等速で動作する必要があるということに起因する。助走距離、制動距離を設けていた理由がこれである。そのため、旋回速度を速めて等速で動作させるには、これらの助走距離、制動距離も大きくとる必要がでてくる。本技術によって、この問題も解決することが可能となる。本技術は、視野間移動時に加速・制動を兼ねて行うため、旋回速度を高速にしても、助走距離、制動距離が大きくならない(図11)。
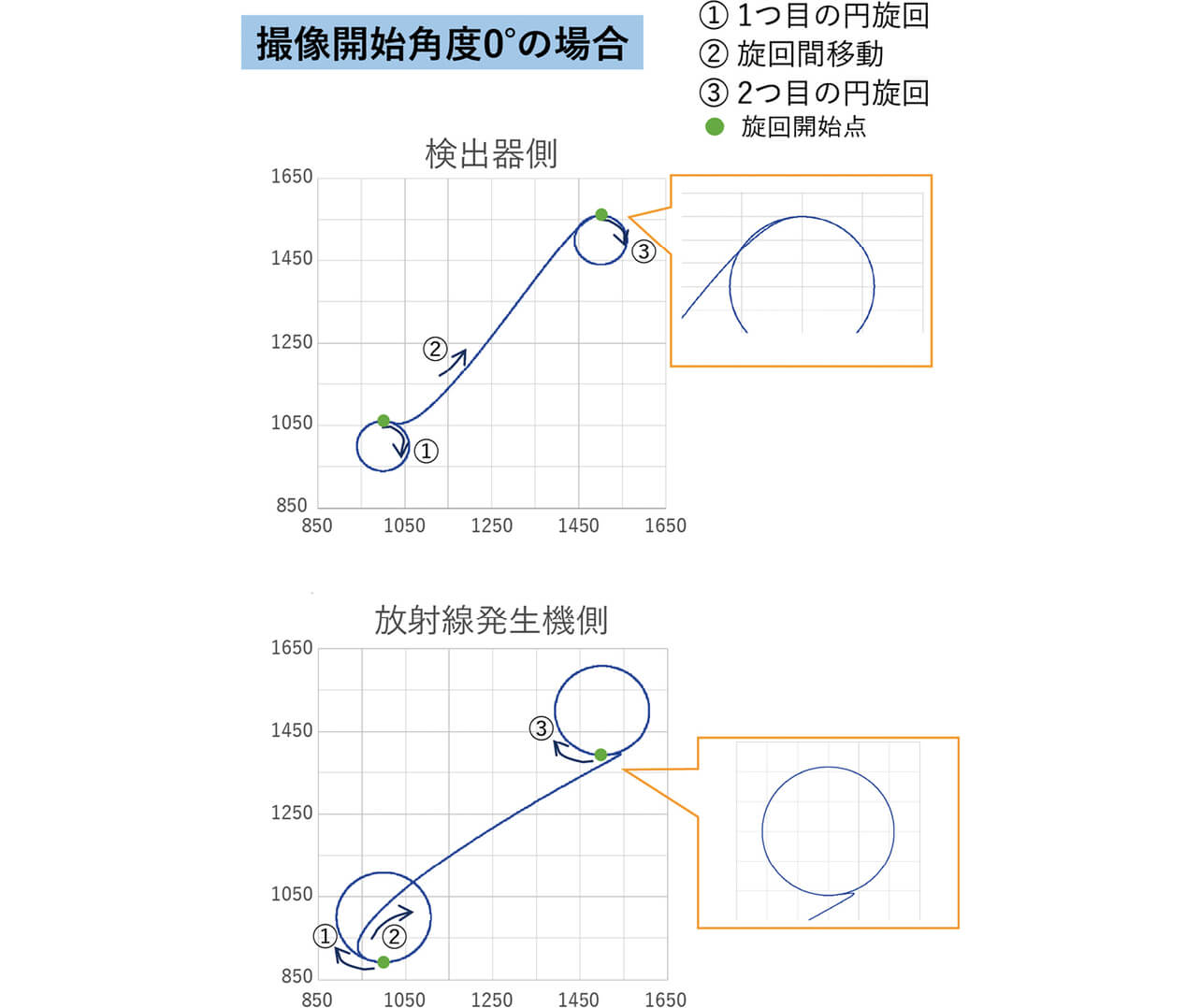
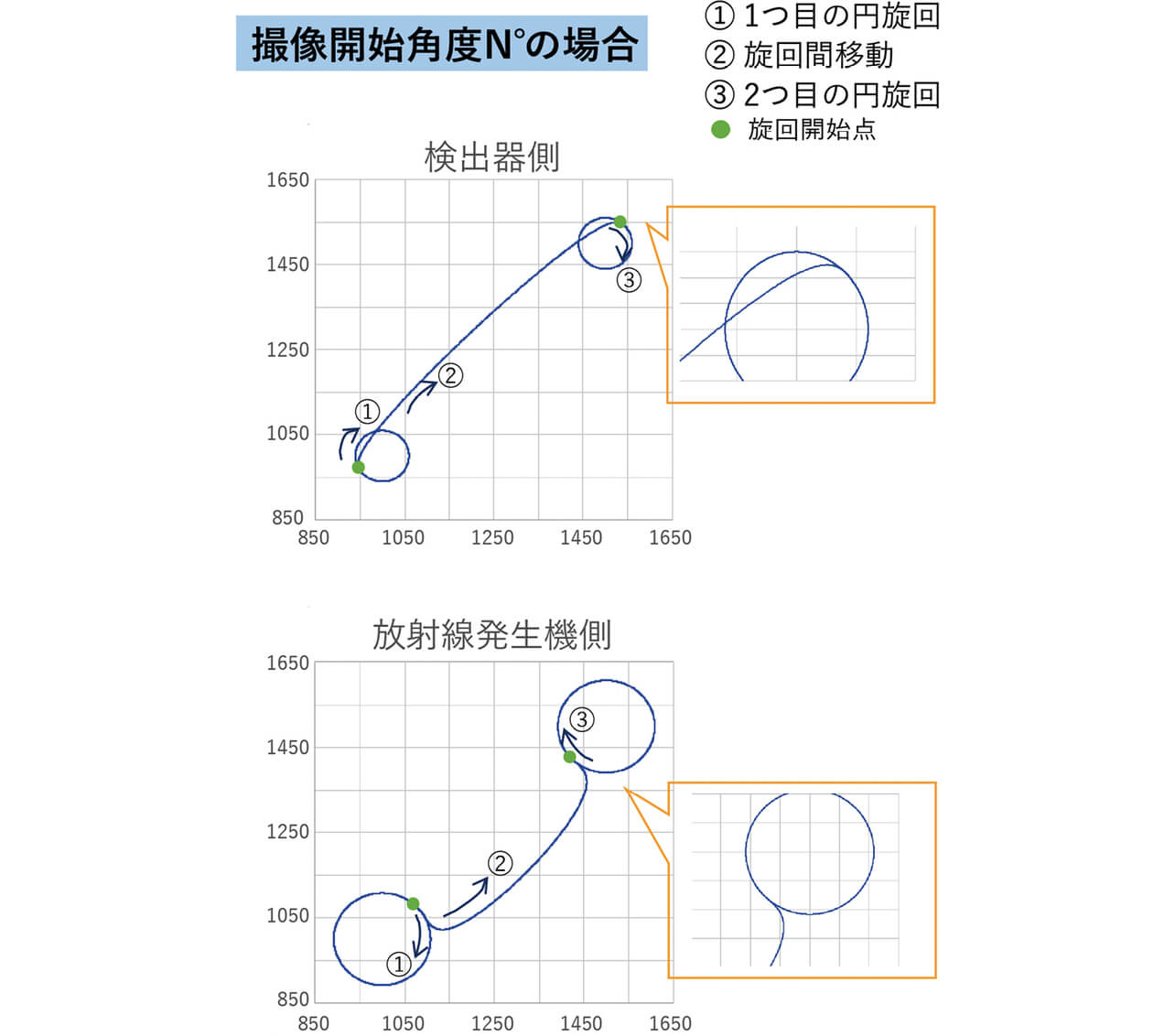
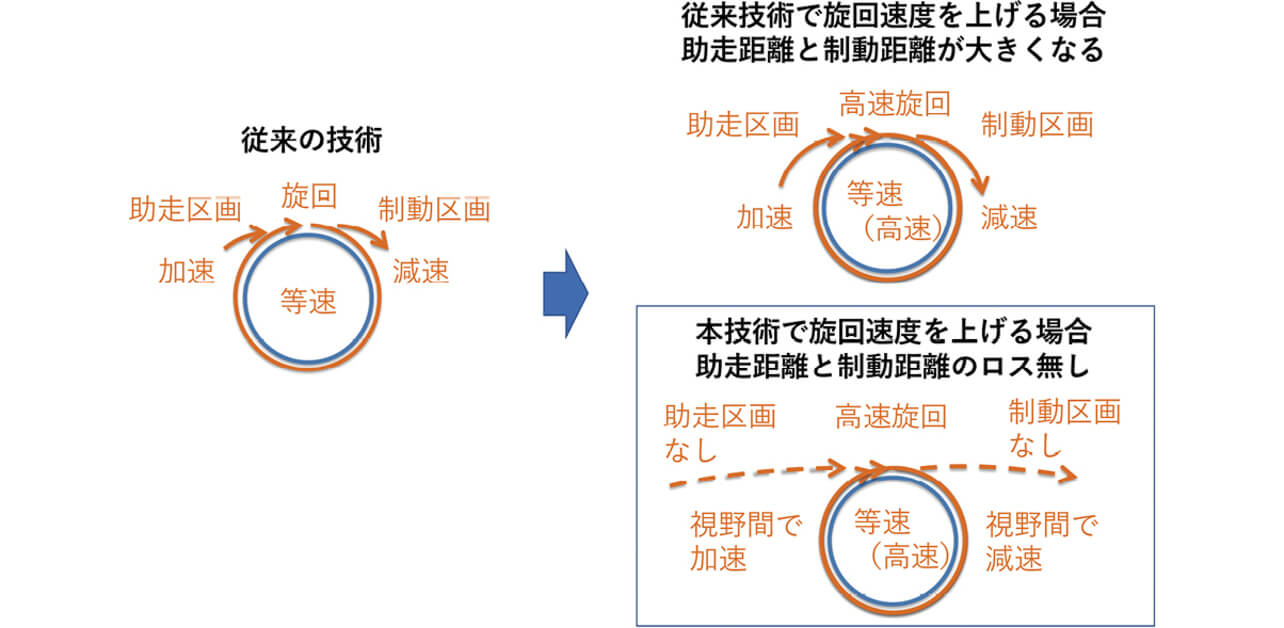
4.1.2 視野間連続移動技術の効果
「視野間連続移動」技術によって、高速化できる効果として理論値と実測値の結果を以下に示す。
計測値としては、旋回時間の中に加速区画、制動区画が含まれていたため、旋回時間としての比較を行う。
確認方法として、PLCを用いたデータトレース方法を行った。そのため、1FOVの旋回中の旋回信号パルス幅(counts)を取得し比較を行った。条件は、加速区間と制動区間がどれだけ削減できているかを確認するため、3視野分の旋回と視野間移動を2回行った際の、2つ目の視野における旋回時間を比較した。従来技術の理論値としては、旋回時間のパルス幅が160(counts)となる見込みである。これが、本技術の理論値では、加速・制動時間がなくなると考え、1FOV 110(counts)となる見込みである。その結果、旋回時間で約30%の時間短縮が可能である見込みであった(図12)。
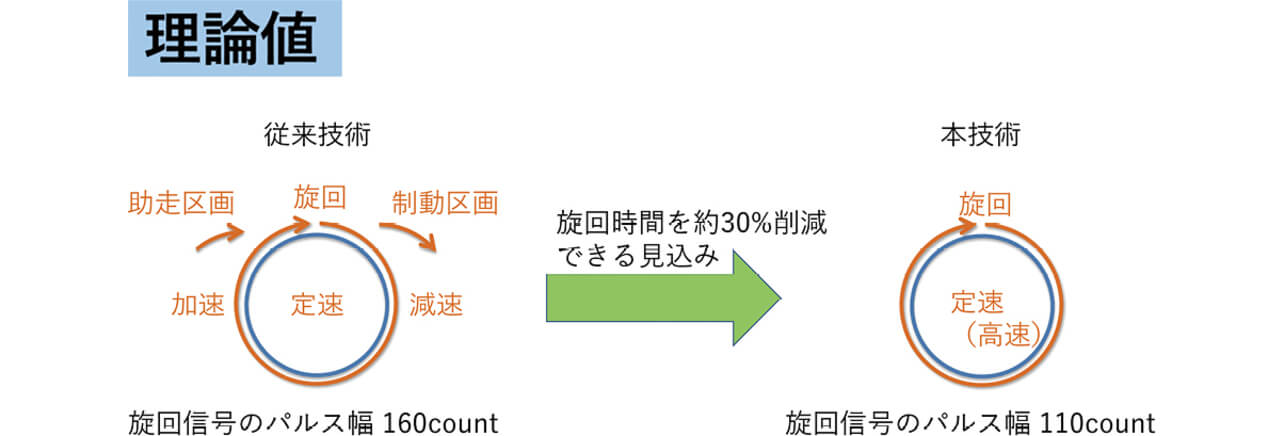
この実測結果について示す。実測の結果、まず、従来技術では、155(counts)、本技術では109(counts)となった(図13)(表1)。従来技術の理論値と実測値との差は、軸の静定時間である。静定時間は6(counts)分存在するため、結果として理論値どおりの実測結果を得ているといえる。従って、旋回時間は約30%の短縮がはかれており、加速・制動時間をなくすことができていることがわかる。
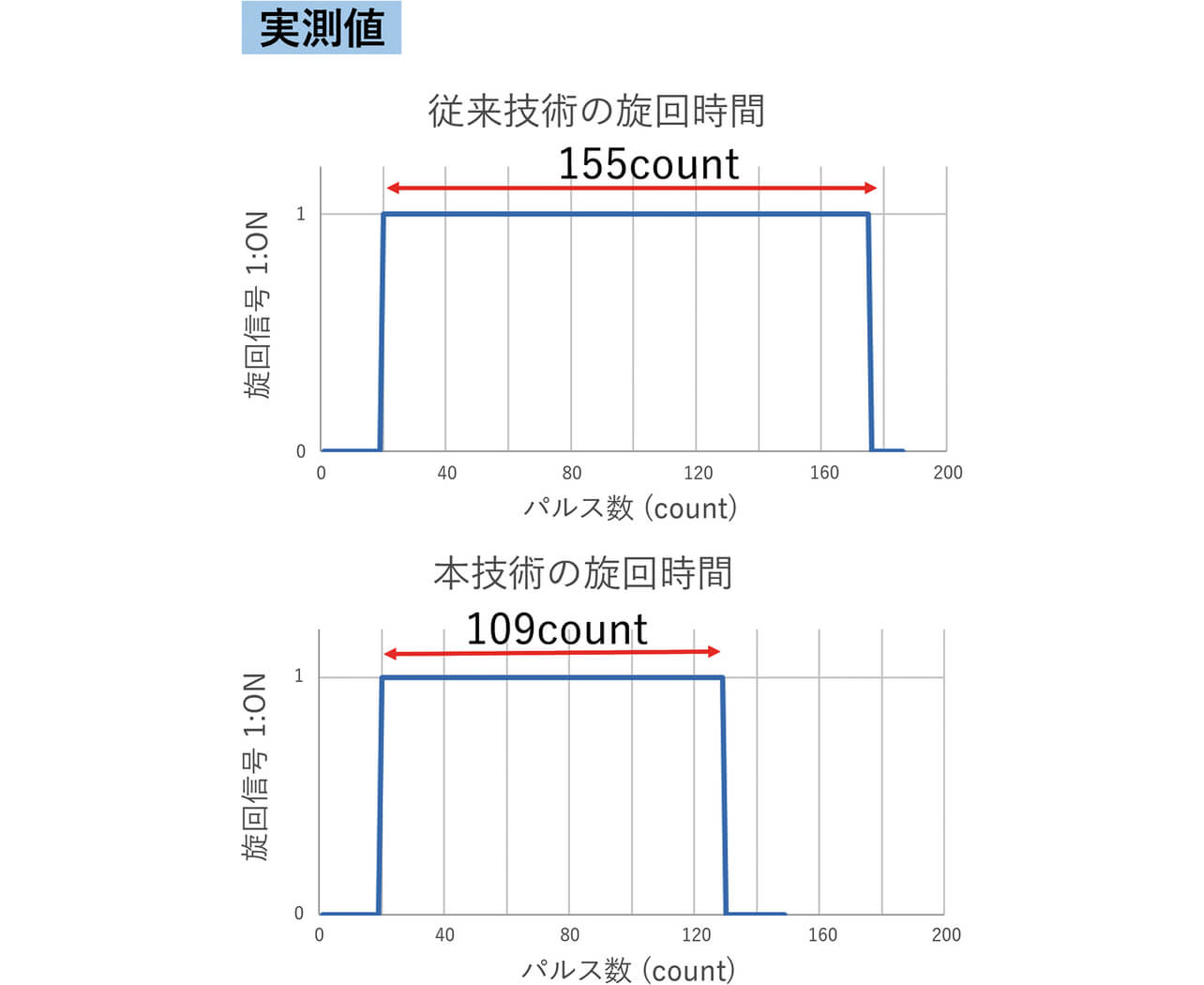
FROM 従来技術 旋回信号のパルス幅 【count】 |
TO 本技術 旋回信号のパルス幅 【count】 |
|
---|---|---|
理論値 | 160 | 110 |
実測値 | 155 | 109 |
4.2 検査時間の高速化効果
次に、「連続撮像」と「視野間連続移動」を組み合わせた実際の基板検査時間の短縮効果を示す。ある顧客基板において、8視野分を撮像する条件で、旋回時間と視野間移動時間の合計を比較した。データ収集は、V2とV3の各装置を使用し、それぞれの装置から出力されるログを集計して計算した。結果として、視野間移動時間は約40%、旋回時間は約30%短縮することができた(図14)※2。以上から、本技術によって、検査速度の1.5倍化を実現することに大きく寄与した。
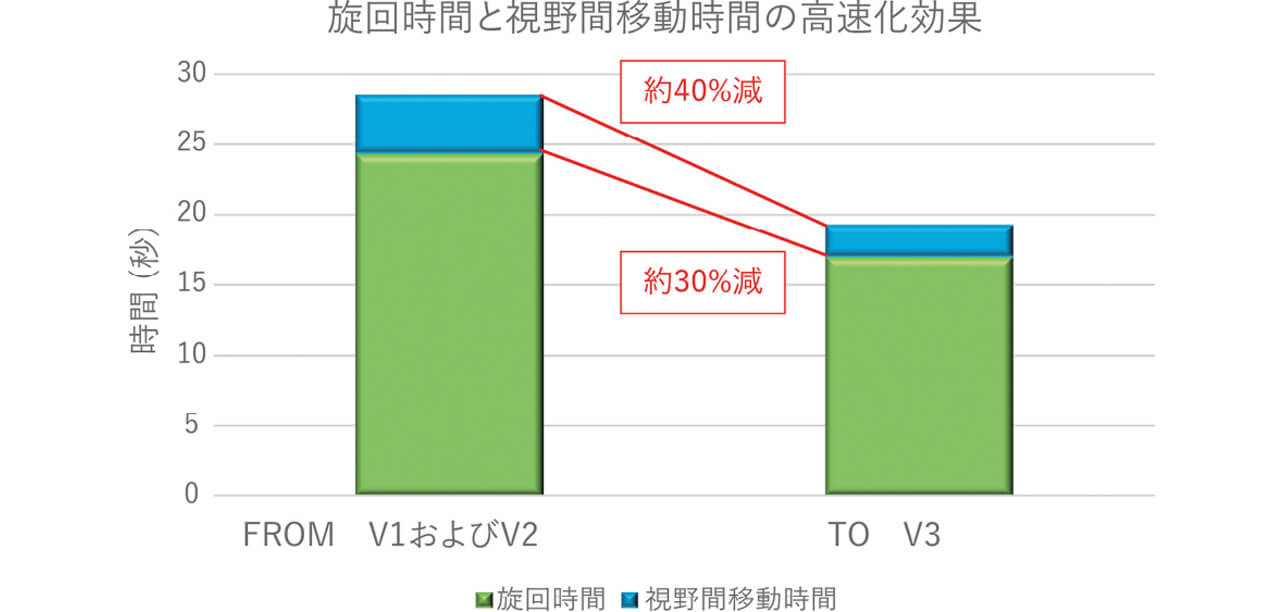
4.3 低被曝CT検査の実現
さらに、「視野間連続移動」技術の効果を示す。本技術により、視野間移動中の軌跡演算のパラメータを応用することで、部品ごとの被曝量を予測し、ヒートマップ形式で表示することが可能となった※3(図15)。このヒートマップによって、顧客やフロントエンジニアが、部品に対する照射条件を最適化して検査プログラムを作成することができるようになった。高速化による低被曝効果とヒートマップでの照射条件最適化によって、本技術を適用したV3では、V1およびV2に対しさらに被曝量を約20%低減することができた。X700比では、40%5)低減することができている※2。
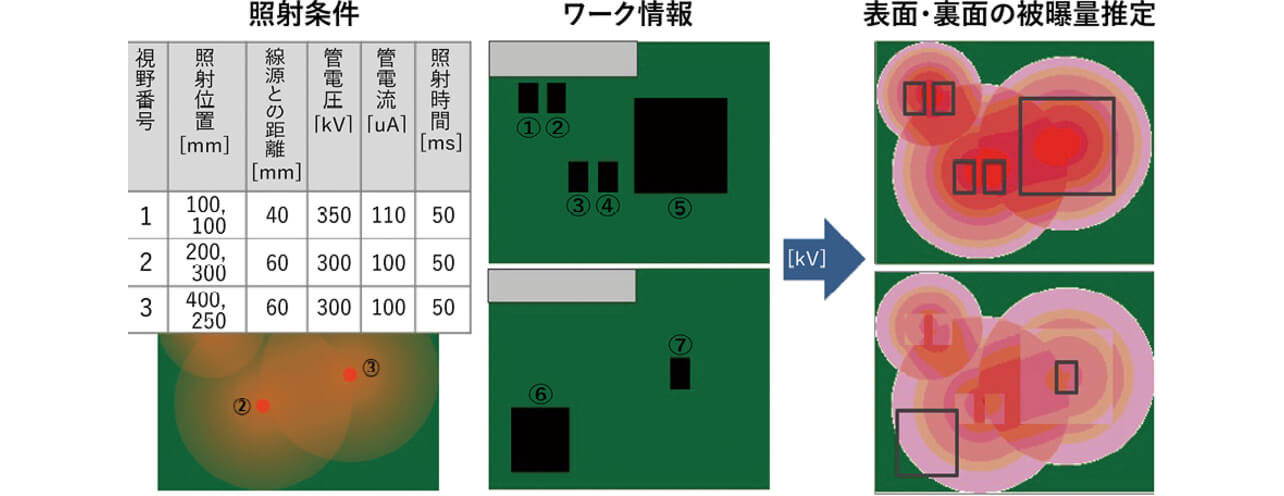
以上により、我々の検査技術の進化によって高速化を実現するとともに、ワークへの被曝量も低減できていることがわかる(図16)。
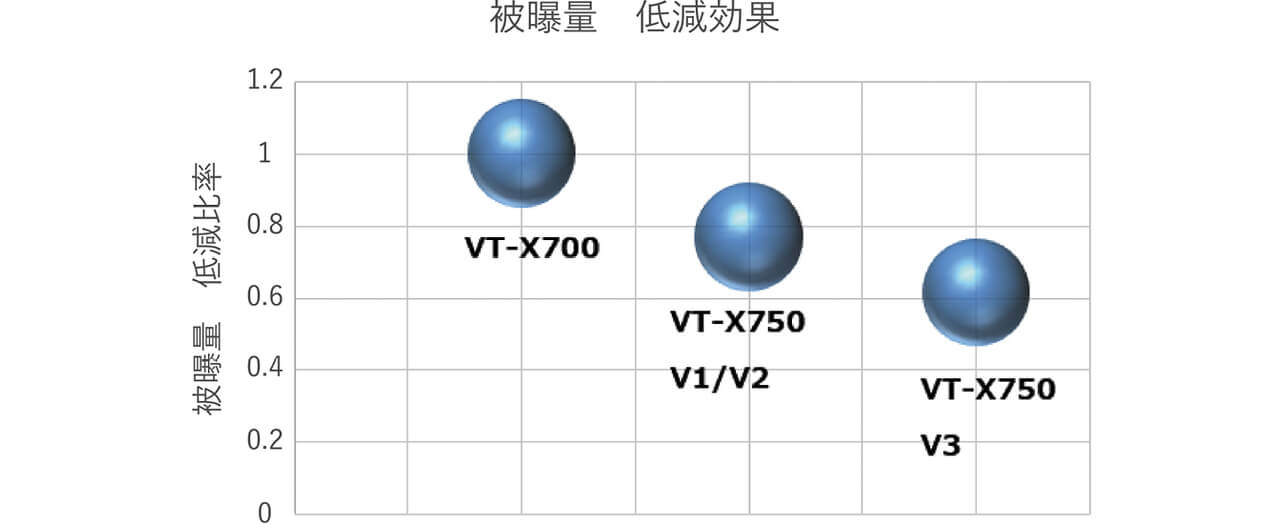
5. むすび
従来の連続撮像技術における視野間移動時ロスの低減という課題を解決するため、「視野間連続移動」技術を開発した。本技術によって、CT方式でありながら、さらなる高速検査を実現させることができた。この技術を搭載したVT-X750-V3にて、より多くの電子基板、顧客の製品が検査できるようになる。本論文の作成にあたり、本技術のリリースに至るまで奮闘くださった当社の開発チームをはじめ、ドライブ事業部の開発チームの皆様に改めて感謝を述べさせていただきたい。
今後の展望としては、顧客の基板や製品の進化へ追従し、更なる高速検査に取り組んでいく。当社の検査技術は、電気自動車の業界だけでなく、多くの電気設備の部品検査に応用ができると考えている。例えば、再生可能エネルギーなどのエネルギーインフラ業界では、天候による再生可能エネルギーの発電量の変動を緩和するための蓄電器、高圧直流送電・超電導ケーブルなどの長距離伝送などの送電効率化設備が普及していく。また、第5世代移動通信システム(5G)をはじめとする情報通信インフラ業界では、大容量・低遅延・多接続な通信を実現するため、基地局や周波数の割り当てが整備され始めている。こうした設備に搭載される基板や部品として、分厚いヒートシンク付きが搭載されたデバイス、IGBT(Insulated Gate Bipolar Transistor)をはじめ、ワイドギャップ半導体であるSiC(シリコンカーバイド)、GaN(ガリウムナイトライド)を用いたFET等のパワーモジュール製品、5G基地局のような大型基板のはんだ不良を検出できるよう低被曝かつ高コントラストな画像を高速に撮像できる技術を探求していく。
フィジカル空間とサイバー空間を融合させた価値やサービスが次々と創出されていく新たな社会が到来しようとしている。我々はこれからも、電化していく社会にむけて、多くの電気部品の製品検査を行い、顧客の製品品質を向上することで、持続可能な社会、安全・安心な社会づくりへ貢献していく。
注釈
- ※1
- 特許権登録済
- ※2
- 社内比
- ※3
- 特許出願中
参考文献
- 1)
- Jisso技術ロードマップ専門員会.2022年度版実装技術ロードマップ.一般社団法人 電子情報技術産業協会,2022,p.352, p.450-451.
- 2)
- 七呂真.超高速CT型X線自動検査装置の開発.OMRON TECHNICS.2019, Vol.51, No.1, p.91-97.
- 3)
- 杉田信治.実装品質保証のカバレッジ拡大に向けた高速CT検査技術.第52回ソルダリング分科会資料.一般社団法人 溶接学会,2011, p.4.
- 4)
- 日本放射線技術学会 監修 市川勝弘,村松禎久.標準X線CT画像計測.オーム社,2009, p.27-28.
- 5)
- 大西貴子.高速・高分解能・低被曝を実現するインライン自動X線検査装置.画像ラボ.2018, Vol.29, No.1, p.67-72.
本文に掲載の商品の名称は、各社が商標としている場合があります。