金属被着体の構造検討による局所加熱での接着剤高速硬化の実現
近年、環境問題に対する気運の高まりから、小型化・軽量化による商品のエネルギ―効率の向上を目的とした異種材接合(金属と樹脂材など)が増えており、接合部には接合信頼性確保のために熱硬化接着剤が多く用いられている。
熱硬化接着剤の硬化工法は、接着される部品(以下:被着材)全体を熱硬化炉に投入、加熱するバッチ処理方式が主流である。この工法では硬化時間が長く生産効率が低い、加熱不要な被着材全体に熱エネルギーを付与するためエネルギー効率が低いという問題点がある。
そこでわれわれは、接着剤周辺の被着材にレーザで局所的に熱エネルギーを付与して接着剤を高速硬化させる省エネルギーかつ生産性の高い工法の開発に取り組んでいる。
本稿では、熱伝導率が大きく局所加熱が難しい金属材における局所加熱での高速接着の実現を目指し、電子機器の筐体フレーム等で多く用いられるアルミ部材に対して熱伝導の通過面積を制御する被着材構造を検討した。その結果、熱硬化炉で数十分かかる接着剤の硬化時間が、本工法では30 秒程度と大幅な硬化時間の短縮を実現した。これにより被着材の適用材質範囲の拡大と生産工程の制約が減り、接着剤工法の汎用性拡大が期待できる。
1.まえがき
近年の環境問題に対する気運の高まりから、溶接・接合工法においても、必要な部分にのみ溶融・反応エネルギーを付与する「局所加熱」の開発が各社で取り組まれている。例えば、レーザを使用したはんだ付け、抵抗溶接を使用したろう付けなどである。
接着接合においては、小型化・軽量化による商品のエネルギー効率の向上を目的とした異種材接合での使用が増加している。異種材(金属-樹脂・ガラスなど)は抵抗溶接、アーク溶接などの溶接工法での接合が困難であり、リベットやボルト締結などの機械的接合工法や接着剤を用いた接合方式が採用されている。
接着接合は、面接着での応力集中の防止、気密性の確保、絶縁性、断熱性などの長所1)があり様々な産業分野で多く用いられている。接着剤の硬化形態には、熱硬化・UV硬化があり、電子部品用途では要求特性に合わせて使い分けられている。UV硬化接着剤では局所エネルギー付与による高速硬化が可能であるが、耐熱性などの接着信頼性の制約や接着剤コストが高いなどの問題点があり使用用途は限定される。これに対して熱硬化接着剤は、耐熱、耐薬品性に優れ、厚膜硬化が可能である、UVに比べ接着剤コストが安価である等の長所があり広く使われている。
オムロンにおける接着接合においても、熱硬化エポキシ接着剤の耐熱、耐水、耐候性、耐薬品性に優れる、隙間充填性がある等の長所2)により、接着固定・封止・充填という機能が要求される用途に使用されている。熱硬化接着剤の硬化方法は、熱硬化炉を用いて被着材と接着剤を同時に長時間加熱して接着剤全体を硬化させるのが一般的である。しかし、熱硬化炉によるバッチ方式は、本来は加熱不要な被着材全体に熱エネルギーを付与するため、製品全体加熱による商品性能への影響や、エネルギー効率が低いため環境負荷が大きく、硬化時間も長いなどの問題点がある。
そこでわれわれは、上記の問題点を解決するために被着材の接着周辺部に局所的に熱エネルギーを付与して加熱し、接着剤を高速硬化させる工法に着目した。この方法では、従来の熱硬化炉方式より少ない時間、少ないエネルギーで接着剤硬化が実現でき、生産効率の向上や省エネルギー化が図れる。さらに、熱硬化炉による一括バッチ処理から局所加熱による個別硬化処理へ移行することにより、生産工程のインライン化や個別品質保証が可能となり、多品種少量生産に適した生産ラインの構築、接着剤硬化工程におけるエネルギー効率や生産効率の観点で効果が大きい。
そこでわれわれは、FA部品・FA機器(リレー、センサー、スマートカメラなど)における異種材部品(金属-樹脂)の接着剤固定・封止を想定して、「高速硬化」、「熱硬化炉レス」を目指した局所加熱硬化による技術開発に取り組んでいる。
本稿では、金属被着体に対する接着剤の高速硬化を目的として、金属被着体に対する局所加熱、局所熱滞留の効果を最大化させられる金属構造について述べる。
2. 局所加熱による接着剤高速硬化工法の取組み
2.1 レーザ局所加熱による接着剤の高速硬化技術
熱硬化炉レスを実現するためには、局所的に熱エネルギーを付加可能で制御容易な加熱方法が必要である。そこでわれわれは、上記要求を満足できるレーザによる局所加熱に着目した。レーザ光源も安価な半導体レーザを使用することで実用的に使えるものを目指した。レーザの指向性を利用して高密度のエネルギーを接着剤に付加することにより接着剤の硬化速度を加速させる。図1 にレーザによる接着剤硬化の原理図を示す。接着剤にレーザ吸収成分を添加し、レーザ吸収成分によってレーザの光エネルギーを熱エネルギーに変換し発熱させ、接着剤の硬化反応を促進する3)。本工法は他社でも検討されており4)、オムロンにおいてもリレーの端子部に、この原理を利用した接着剤と工法を使用して実用化している。
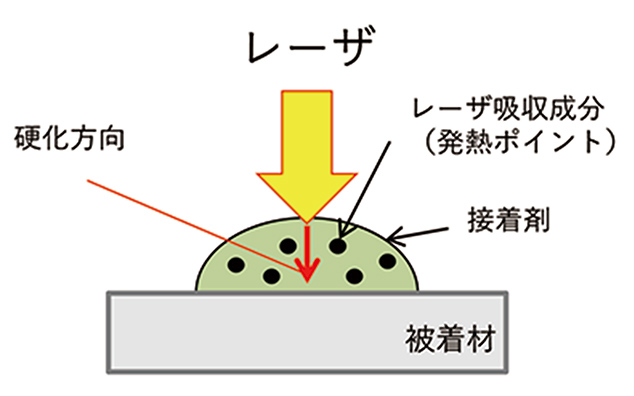
このレーザ吸収式硬化方法では、レーザ照射によって接着剤表面から硬化が始まるため、接着剤が厚くなると被着材との界面の硬化が非常に難しいという問題がある。
この問題を解決するため、図2 に示すレーザ透過型硬化方法5)を考案した。接着剤にレーザ吸収成分を添加せず、接着剤を透過したレーザによって被着材を発熱させ、接着剤を被着材界面から硬化させる方法である。
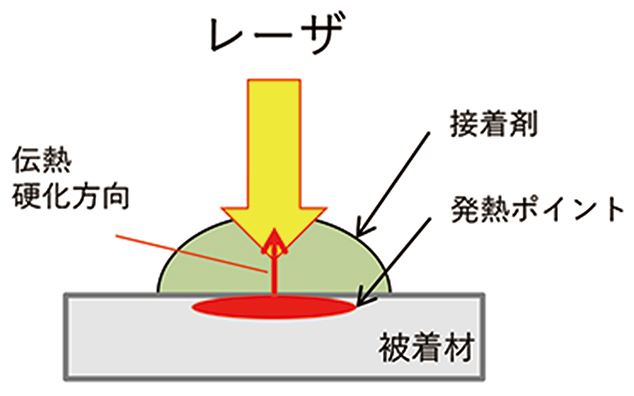
このレーザ透過式硬化方法により、被着材との界面から硬化が進行するため接着剤厚さが数ミリの厚膜硬化や接着強度の確保が実現できた。この方法は熱伝導が小さい被着材には有効であるが、金属のように熱伝導が大きい被着材の場合、レーザによる入熱が金属内部へ伝熱してしまい接着剤に伝わり難く、接着剤が硬化しない問題がある。
オムロン商品においても金属-樹脂の接着接合が多く使われており、局所加熱による接着接合技術の展開を考慮すると、金属部品への高速接着が可能な技術が必要である。
2.2 金属部品への局所加熱接着工法6)の適用
そこで、われわれは被着材が金属でもレーザ局所加熱による接着剤高速硬化が可能な技術を検討した。加熱原理を図3に示す。レーザを接着剤に直接照射せず、被着材の発熱を接着剤に伝熱することで、金属と接着剤の界面から接着剤を硬化させることができる。またレーザが直接接着剤に照射されないため、接着剤成分や色など接着剤の制約が少ない接着剤選定が可能となる。
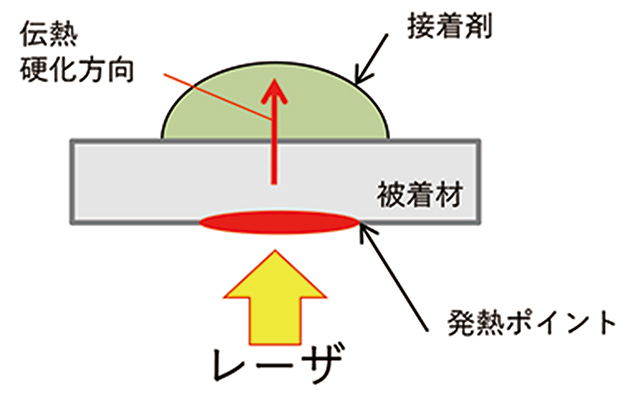
3. レーザ局所加熱による伝熱要因の特定
3.1 レーザ加熱の課題
レーザ照射による金属被着材の局所加熱での接着剤硬化が困難である原因として、被着材が高熱容量・高熱伝導体であることによる入熱エネルギーの局所滞留が難しいことが挙げられる。
このため、レーザ照射による入熱で接着剤高速硬化を実現するには、入熱エネルギーの周辺部への伝熱を抑制して、被着材内部で熱エネルギーを局所滞留させることが重要となる。そこで、被着材周辺部への伝熱要因である部材内への熱伝導、他部材への接触熱伝達、大気中への対流・放射熱伝達の各要因の影響度を確認し、レーザ照射による入熱エネルギーの局所滞留を確保する必要がある。
3.2 実験方法
実験に使用したアルミ部材形状を図4 に示す。レーザ照射での被着材加熱において、被着材の局所滞留への影響が大きい伝熱形態(被着材の熱伝導、接触治具への熱伝達、大気中への対流・放射熱伝達)について、被着材の温度変化に対する各要因の影響度を確認した。これにより、レーザ局所加熱により被着材の局所加熱を効率良く行うための対策方向性を明確にする。
実験サンプル(以下:アルミ部材)として、同一板厚で体積が異なるアルミ部材、同一体積で形状が異なるアルミ部材を用いた。
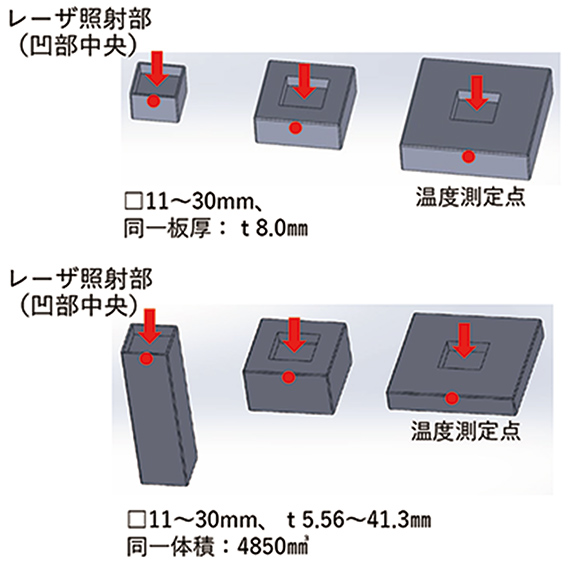
アルミ部材形状、設定条件を表1 に示す。アルミ部材形状による熱伝導、接触治具による熱伝達、表面黒化処理による対流・放射熱伝達による温度上昇への影響を確認できるように条件を設定した。具体的には、アルミ部材形状6種類に対して、3 種類の熱伝達条件(条件①~③)を組み合わせた18 条件で実験した。アルミ部材間の比較により熱容量・熱伝導の影響、条件①と②の比較により対流・放射熱伝達の影響、条件②と③の比較により治具熱伝達の影響を明確に示せるように設定した。これらの実験パターンでレーザ照射による入熱後のアルミ部材の最高温度の比較によって温度上昇に関わる各伝熱形態の影響を確認する。レーザ照射条件を表2 に示す。
伝熱形態 | 比較方法 | 実験パターン | ||
---|---|---|---|---|
1 | 2 | 3 | ||
熱伝導・熱容量 | 部材形状(同一板厚) | □11×11mm | □20×20mm | 30×30mm |
熱伝導 | 部材形状(同一体積) | □11×t41.3mm | □20×t12.5mm | □30×t5.56mm |
治具熱伝達 | 治具接触 | あり | なし | |
対流・放射熱伝達 | 表面黒化処理 | あり | なし |
条件 | 治具熱伝達 | 対流・放射熱伝達 |
---|---|---|
① | あり | なし |
② | あり | あり |
③ | なし | あり |
項目 | 設定値 |
---|---|
レーザ種類 | 半導体(波長:808nm) |
照射径 | φ2mm |
照射出力 | 27W |
照射時間 | 30sec |
実験方法を図5に示す。レーザ照射時のアルミ部材表面温度をサーモグラフィーで測定して、アルミ部材、実験条件に対するレーザ照射30sec後の最高温度の違いを確認した。
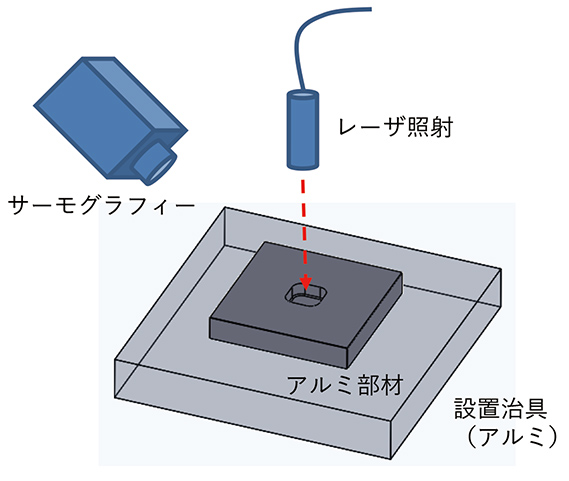
3.3 実験結果
アルミ部材の各条件でレーザ照射による入熱後の最高温度を比較したグラフを図6に示す。図6では、アルミ部材体積(熱容量)、アルミ部材形状(熱伝導形状)により、レーザ照射による入熱後の最高温度に大きな違いがあることがわかる。設置治具接触による熱伝達、対流・放射熱伝達の影響については、同一アルミ形状での条件変化による温度差となり、熱容量、熱伝導に比べると最高温度に与える影響は小さいことがわかる。
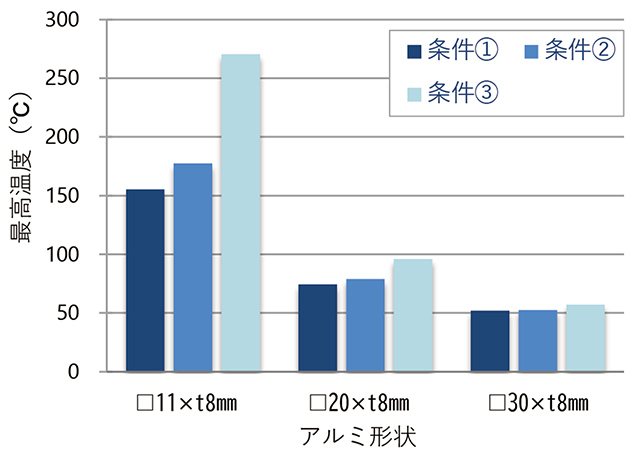
さらに、熱伝導による温度差を確認するため、図7でアルミ部材同一体積でのアルミ部材形状の違いによる最高温度を比較した。その結果、同一形状での各条件間の温度差に比べ、アルミ部材形状の違いによる温度差の方が大きいことがわかる。
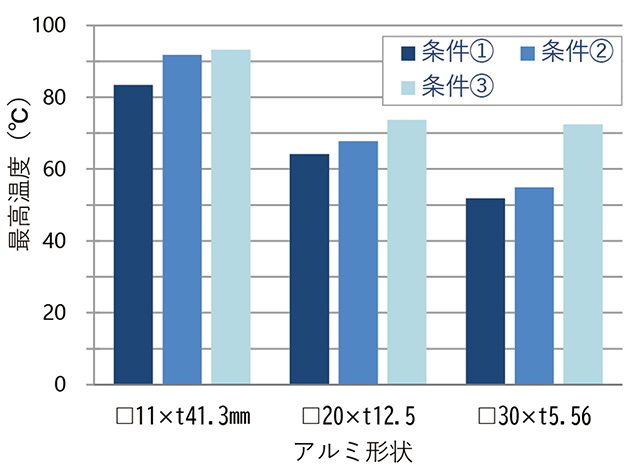
アルミ形状・体積、治具との接触、表面黒化処理の条件による最高温度の違いから、伝熱に影響の大きい3因子(アルミ部材内の熱伝導、接触治具への熱伝達、大気中への対流・放射熱伝達)の最高温度に対する各要因の影響度を算出すると図8、図9に示すようになる。
影響度の算出方法は、表2の条件①~③の比較により発生する温度差と理論温度上昇の計算値を用いた。例えば(条件①-②の温度差)÷(理論温度上昇)により対流・放射熱伝達の影響割合が計算できる。理論温度上昇計算には以下の計算式を用いた。
:熱量、比熱:
、密度:
、体積:
同一板厚・体積違いのアルミ形状の比較を図8に示す。治具への熱伝達は、表面積・体積、板厚が小さい□11×t8mmアルミ部材で接触面積比率が大きくなり影響度が大きくなる。対流・放射熱伝達は、表面積・体積が小さい□11×t8mmアルミ部材では最高温度が大きくなり、以下の放射熱量の計算式からも放射量が大きくなることがわかる。
:面積、
:放射熱伝達率、
:表面温度、
:雰囲気温度
これに対し表面積・体積が大きい□30×t8mmアルミ部材では最高温度が小さく、大気中への対流・放射熱伝達の影響度は小さくなる傾向がある。熱容量・熱伝導は、体積が大きい□30×t8 mmアルミ部材では最高温度が小さくなる。このため治具熱伝達、対流・放射熱伝達の影響度についても周辺部との温度差が小さく、影響度は小さくなっている。
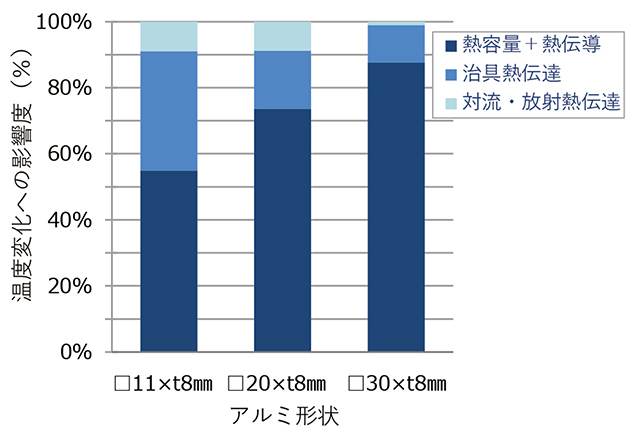
同一体積・板厚違いのアルミ形状の比較を図9に示す。治具への熱伝達は、接触面積が大きい□30 mmの部材で最も影響度が大きくなっている。対流・放射熱伝達は、アルミ部材間の表面積、体積の違いが少なく最高温度がほぼ同じであることから影響度にもあまり差が出ていない。熱容量・熱伝導については、アルミ部材間は同一体積で熱容量差が無いため、アルミ部材内の熱伝導の影響度とみることができる。これについては、治具への熱伝達面積が小さく、アルミ部材内の熱伝導面積も小さい□11×t41.3mmアルミ部材で熱伝導の影響度が大きくなっている。
以上のことから、本実験のアルミ部材形状による各要因の影響度は、大きい順に①アルミ部材内での熱伝導 ②治具接触部への熱伝達、③大気中への対流・放射熱伝達 であることがわかった。特に、アルミ部材内での熱伝導は全てのアルミ部材形状において、温度変化に対する影響度50~80%程度と大きいことがわかる。
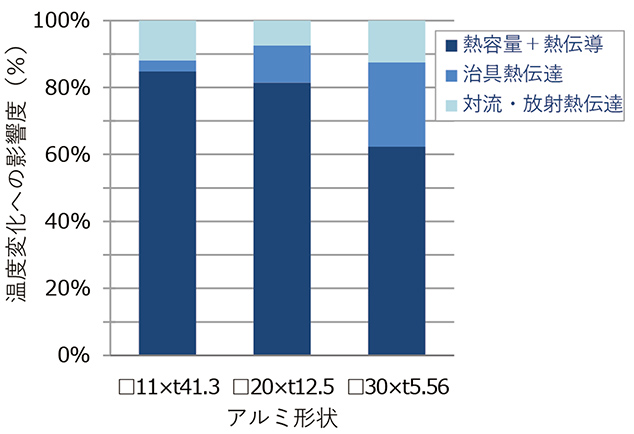
4. レーザ局所加熱による熱伝導の制御
4.1 熱伝導の理論と考え方
3.3 項の実験結果からレーザ照射による入熱で被着材を局所加熱する場合では、アルミ部材形状による熱伝導の影響が大きいことがわかる。つまり、レーザ照射による入熱部から被着材周辺部への伝熱を抑制する被着材形状や被着材構造により、レーザ照射による局所加熱の効果が大きくなる。被着材内部の熱伝導に関しては、フーリエの法則により以下の式で表せる。
:通過熱量、
:熱伝導率、
:温度勾配、
:通過面積
この式から、ある面の通過熱量は、被着材の熱伝導率、温度勾配、通過面積に比例する。つまり、被着材構造により通過面積を小さくしてレーザ入熱部から周辺部への通過熱量を抑制すれば、レーザ照射部付近の温度上昇を最大化することができる。
被着材が高熱伝導材のアルミ部材においても、部材表面に溝を設けてレーザ照射による入熱部から周辺への伝熱量を抑制することにより、入熱エネルギーの局所滞留を確保することが可能と考えられる。
4.2 実験方法
レーザ局所加熱時の伝熱状態を変化させるため、アルミ部材表面に溝加工形状を設ける。図10に示すようなレーザ局所加熱点から同心円状の溝加工を、表3に示す条件でアルミ部材表面への溝幅、溝間隔、溝深さを変化させて、溝加工形状による熱伝導断面積、熱伝導距離の違いによるアルミ部材の温度上昇の変化を確認した。
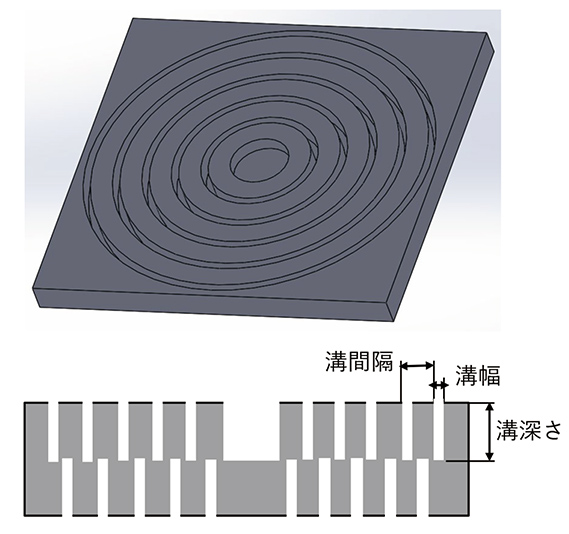
サンプルNo | 外形(mm) | 板厚(mm) | 溝幅(mm) | 溝深さ(mm) | 溝間隔(mm) |
---|---|---|---|---|---|
① | 50×50 | 4 | 1.0 | 3.0 | 1.0 |
② | 1.0 | 2.0 | 1.0 | ||
③ | 1.0 | 1.5 | 1.0 | ||
④ | 0.5 | 1.0 | 0.5 |
実験方法を図11に示す。レーザ照射時のアルミ部材表面温度をサーモグラフィーで測定して、アルミ部材の溝加工形状による温度上昇の違いを確認した。
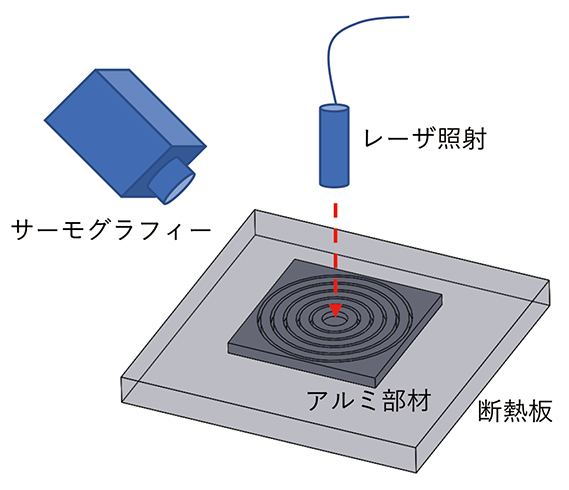
温度評価方法を図12に示す。レーザ照射部付近での局所加熱効果、周辺部での温度変化を確認するため、P1~P3の3点でサーモグラフィー温度を測定した。測定点間隔は、溝幅・溝間隔1mmでは8mm、溝幅・溝間隔0.5mmでは4mmとした。
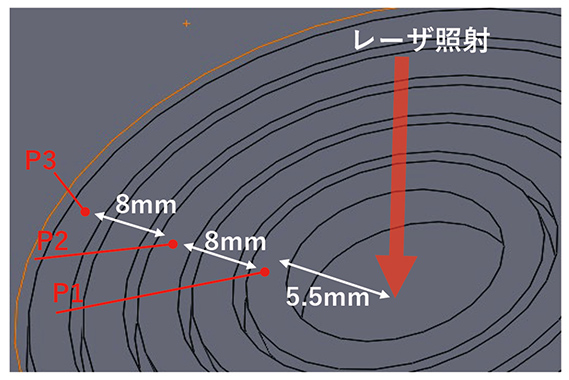
4.3 実験結果
図13 にアルミ部材の溝加工形状による温度上昇の違いを示す。アルミ部材の溝加工が有る形状①~④では、溝加工のないアルミ板形状と比べて、P1温度が上昇しており、最大約1.8 倍(約55℃⇒約100℃)の温度上昇となっている。これはP2・P3 点温度の約1.4倍に比べて、明らかにP1 点での温度上昇割合が大きく、溝加工形状によりアルミ部材のレーザ照射部付近を局所的に効率良く加熱できていることがわかる。溝加工形状因子による違いは、アルミ形状③・④を比較することで溝幅、溝間隔に比べて、溝深さの影響が大きいことがわかる。
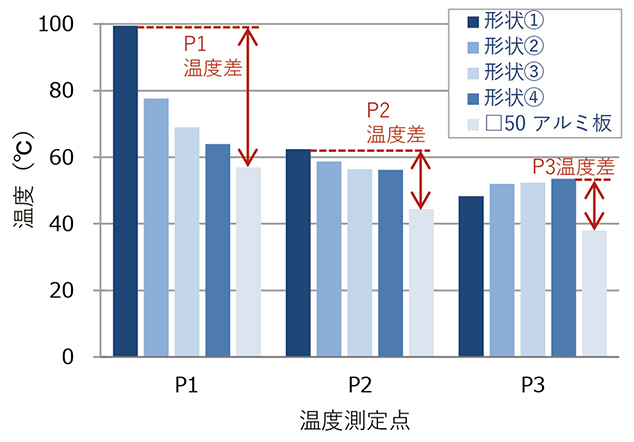
5. 商品展開に向けたレーザ局所加熱の効果検証
5.1 商品相当形状のアルミ部材での効果検証
4章では熱伝導に寄与する通過面積の制御による、熱エネルギーの局所滞留への影響を確認した。本技術を商品へ展開するためには、商品形状に適した溝形状にしなければならない。本章では、商品を想定した溝加工形状でのレーザ照射熱エネルギーの局所滞留効果を確認した。
5.2 実験方法
図14に示す商品形状を模したアルミ部材形状で局所加熱の熱通過面積の制御による効果を確認した。アルミ部材は、材質:A5052、最大外形:130×60mm、板厚2~4mm(レーザ照射部:4mm)、表面処理:黒色アルマイトとした。溝加工は図15に示す溝本数表面:1本、裏面:2本、溝幅:1mm、溝間隔:1mm、溝深さ:2mmとした。
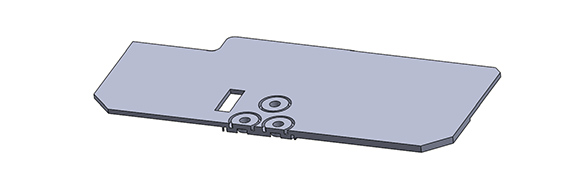
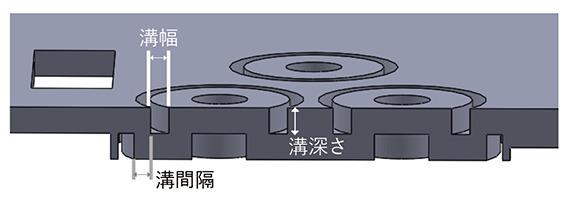
レーザ照射条件は、照射面:裏面、レーザ径:φ4mm、出力:27W、照射時間:30sec、穴①~③に対し1点ずつ照射した。
温度測定点、レーザ照射状態を図16に示す。温度測定はサーモグラフィーで表面から穴底面の最高温度を測定した。
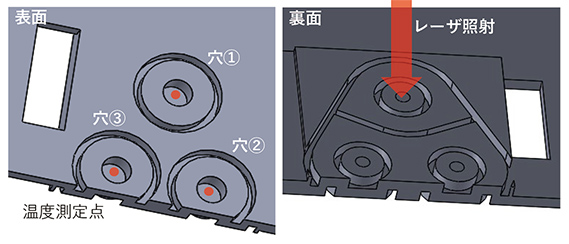
5.3 実験結果
実験の結果、図17に示すように穴①~穴③の温度上昇は80~100℃となっており、溝形状のない□50mm、板厚4mmのアルミ板に比べて、アルミ体積は約2倍にも関わらず1.5~1.8倍の温度上昇をしている。穴①~穴③の温度比較においては、穴①の温度上昇が穴②、穴③に比べて小さい。これは穴①が穴②、穴③に比べて、周辺部への熱が逃げる面積が大きいためと考えられる。
温度上昇時間では、図18に示すようにレーザ照射開始3sec後で86℃まで温度上昇しており、接着剤の高速加熱の観点からもレーザ局所加熱の効果が大きいことがわかる。
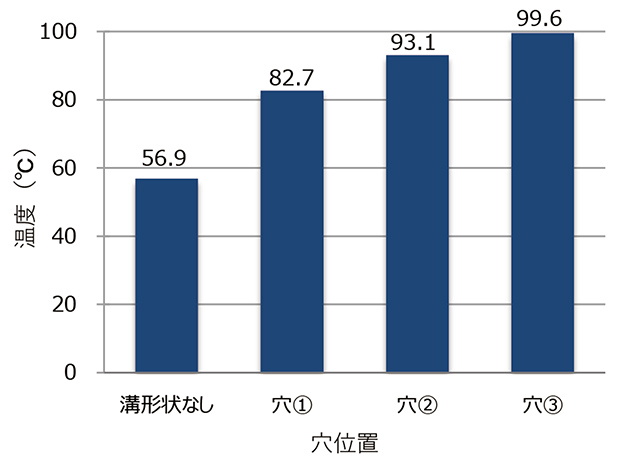
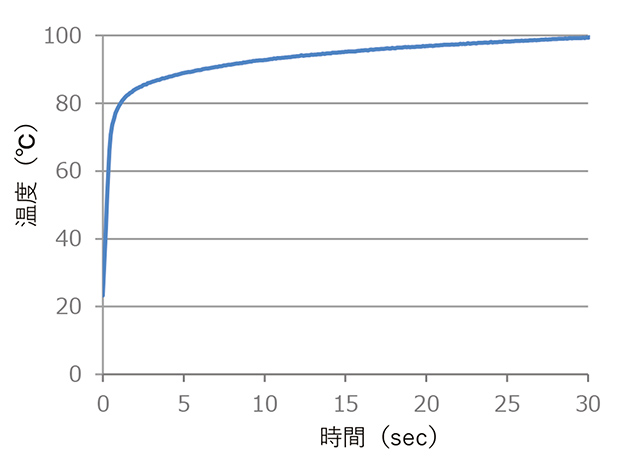
5.4 レーザ局所加熱によるエポキシ接着剤硬化
商品相当構造においても熱の局所滞留が確認できたため、次にレーザ照射による熱硬化接着剤の硬化の実現性を確認した。
図16に示す温度測定点の穴内にエポキシ接着剤を注入し、穴内に樹脂棒を差し込んだ状態で、裏面からレーザ照射しエポキシ樹脂を硬化させた。評価指標として引張り接着強度を測定し、オーブンで加熱硬化したものと比較した。図19にレーザ照射時のサーモグラフィー温度測定状態を示す。図20にそれぞれの加熱条件(レーザ照射27W・15sec、レーザ照射27 W・30sec、オーブン加熱120℃・1 hour)での接着強度を示す。レーザ硬化27 W・30secではオーブン硬化1hourとほぼ同じ接着強度が得られた。これに対し、レーザ照射15 sec では接着強度がオーブン硬化の15%程度まで低下しており、オーブン加熱と同等の接着剤硬化状態および接着強度が得られていないことがわかる。
このように、商品相当形状においても設計の工夫によって、レーザによる局所加熱で短時間で必要な接着強度を確保できることが実証できた。
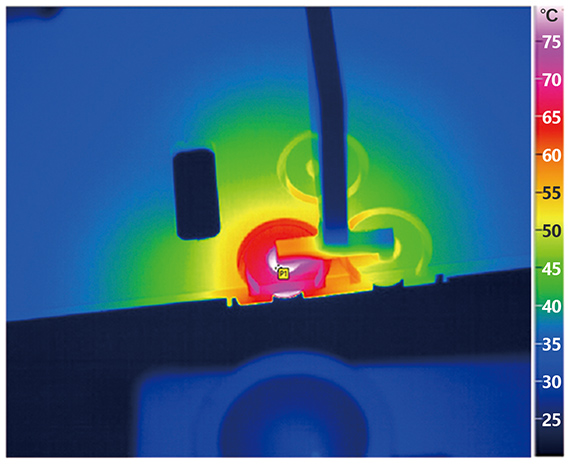
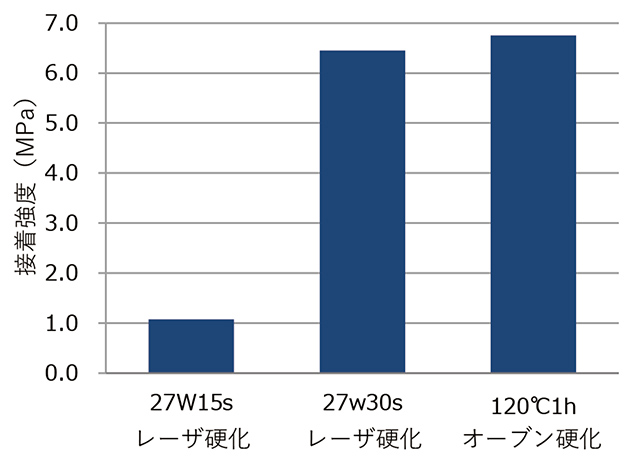
6. むすび
被着材形状、構造を工夫してレーザ照射による入熱エネルギーを効率良く被着材の局所加熱に活用した結果、アルミ被着材における局所的な温度上昇を1.5~1.8倍程度まで高められた。これにより熱硬化接着剤の硬化の実現とオーブン加熱と同等の接着強度が得られることがわかった。
接着接合工法においてアルミ部材のような高熱伝導材での局所加熱が可能になったことで、省エネルギーで環境負荷が少なく、多品種少量生産に適したコンパクトな生産ラインが可能という局所加熱のメリットを保持しながら、被着材材質の適用範囲、接着剤工法の適用範囲を拡げられる。
さらに被着材の局所加熱により、これまで耐熱温度が低い部品があり、熱硬化炉が使用できなかった商品への熱硬化接着剤の適用が可能となる。
本工法の商品展開に向けた課題として、レーザ照射による局所加熱に適した接着材形状、被着材構造の最適化が挙げられる。これには商品設計段階からの被着材形状、接着剤塗布に適した構造設計検討が重要であり、構造設計を効率化するためには、被着材材質、形状、局所加熱条件を変更しながら温度状態を可視化できるCAE 環境の構築が重要となる。
今後は熱CAE を活用した局所加熱構造のシミュレーションにも取組み、商品開発段階での最適な接着構造や工法の提案を行えるように取り組んでいく。
参考文献
- 1)
- 原賀康介.高信頼性接着の実務.日刊工業新聞社、2013,p.3.
- 2)
- 日本接着学会.初心者のための接着技術読本.日刊工業新聞社、2004, p.38.
- 3)
- オムロン.樹脂組成物の硬化方法.特許6331525.2018-05-11.
- 4)
- 杉浦昭夫,鈴木克彦,伊奈治,加藤和生.新硬化技術の開発.デンソーテクニカルレビュー.2009, Vol.14, p.81-87.
- 5)
- オムロン.接着剤組成物の硬化方法および接着構造体の製造方法.特開2019-001936.2019-01-10.
- 6)
- オムロン.接合品の製造方法および接合品.特願2019-126225.2019-07-05.
本文に掲載の商品の名称は、各社が商標としている場合があります。