盤異常の早期発見を可能にする到達温度予測技術の開発
- 設備保全
- 予兆
- 温度監視
近年、設備の老朽化に伴う盤内部品の異常な温度上昇による停電や発火事故などが増えてきている。それにより、例えば工場においては製造ラインが停止し、機会損失の発生や、社会的イメージの低下につながる恐れもある。保全員による定期的な設備保全を実施することで異常の発生頻度を抑えているが、温度異常は数日で進行するものも存在するため、完全には抑制できていない。そこで熱電対や赤外線センサ等の温度測定機器を常時設置して、遠隔で温度を監視するニーズが増えている。
一方で、数時間で発火や発煙までに至る異常の場合、温度監視装置で異常温度を検出してからユーザーが現場で対処するまでの時間的余裕がなく、対処が間に合わないケースも存在しており、さらなる早期異常検出が課題である。
著者らは温度の早期異常検出を目指し、異常機器の温度の変化傾向から最終的に到達する温度を予測する「到達温度予測」機能を開発した。より早期な異常検出を実現することで、発火事故や停電に至るまでにユーザーが適切な処置を実行できる時間的余裕を創出した。
本稿では、「到達温度予測」の概要と、それを実現するための技術的手法 について述べる。
1.まえがき
近年、工場の設備の老朽化1)により保全業務は増加傾向にある。また、人口減少などの影響もあり、企業は保全員の追加確保が困難である。それにより、一人当たりの保全作業量は増加していることが想定され、保全不足による設備の停電や発火事故などが増えてきている2)。製造ラインが停止し復旧までに多くの時間を費やすことで機会損失の発生が企業経営に大きな影響を与え、発火事故にまで至る場合は社会的イメージの低下につながる恐れもある。このような事態を回避するために保全員による定期的な設備保全を実施することで異常の発生頻度を抑えているが、温度異常は数日で進行するものも存在するため、定期点検の合間に発生した異常は抑制できていない。そこで熱電対や赤外線センサ等の温度測定機器を常時設置して、遠隔で温度を監視するニーズが増えている。
一方で、数時間で設備の突発停止や発火などの重大事故につながる温度異常もある。温度監視装置で異常温度を検出してからユーザーが現場で対処するまでの時間的余裕がなく、対処が間に合わないケースも存在しており、さらなる早期異常検出が課題である。
以上のような保全課題の解決のため「到達温度予測技術」として、数時間で進行する異常の早期検出技術を確立した。本稿では「到達温度予測技術」について記載する。
なお、上記課題解決のため盤内監視機器K6PM-TH を開発し、到達温度予測技術を本体機能として実装した(図1)。
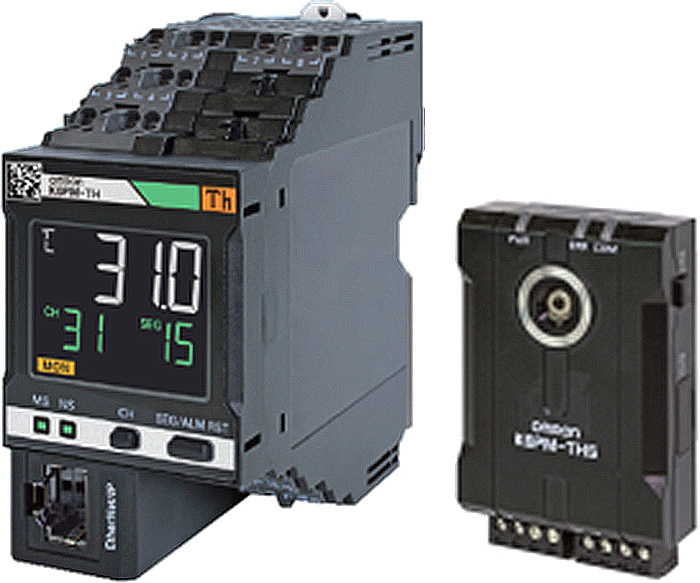
2. 課題
2.1 異常モードの種類
保全業務の効率化に課題感を持つ工場の保全員20名にヒアリングした結果、盤内部品で特に異常発生が多い部品は、50A を超える大電流用の中継端子の配線やトランス、インバータであることがわかっている。これらの製品の異常モードを分析する。
上記部品は複数の異常モードを持つ。大きな分類として「進行型異常モード」と「突発型異常モード」である。「進行型異常モード」は絶縁劣化に代表されるように、環境要因であるガス雰囲気、湿度などによる化学変化(腐食、マイグレーションなど)や機械的ストレスによる機械的変化(クラック、接触不良など)が進行するもので、数日~数十年の間で徐々に温度上昇し故障に至る異常モードである。
一方で「突発型異常モード」は保全員の作業ミスに起因した端子のねじ緩みによる発熱や空冷ファン故障による盤内温度上昇が発生した場合に、数時間で故障に至る異常モードである。
2.2 従来の検知方式
盤内で発生する発火事故や熱起因の故障の保全検知方式としては、保全員が現場でサーモビュワーをかざして温度を計測する人型方式、熱電対などの温度測定装置を常設して計測する常設方式がある。
2.3 各異常モードへの対応
進行型の異常モードは数日~数十年で徐々に温度が変化する異常モードであるため、常設型の検知方式で温度傾向を監視することにより解決することができる。
突発型の異常モードは異常の発現から数時間で設備停止や発火に至る。そのため最終的な温度に到達する前に到達する温度を予測し早期に異常検出することにより保全員が盤内機器の改善修理、安全な停止を実行するための時間的余裕を確保することができる。
表1 に各モードに対する検知方法をまとめている。本研究では常設型でも検出できない「突発型」の異常モードを早期に検出できる技術の確立を目指す。またそれによって他の異常モードに対して誤動作しないことも確認する。
異常モード | 具体例 | 進行単位 | 人型 | 常設型 |
---|---|---|---|---|
進行型 | 腐食、マイグレーション、クラック、接触不良(環境により進行速度は様々) | 年、月 | 対応可能 | 対応可能 |
日 | 対応不可 | 対応可能 | ||
突発型 | 端子ねじの緩み(保全員の作業ミス)空冷ファンの停止 | 時間 | 対応不可 | 対応不可 |
今回の課題解決の評価指標を、異常の発現から本技術で異常を検出できるまでの「通知時間」、およびその通知内容の信頼性を確保するための「通知精度」とし、これらの指標を「通知性能」と総称する。各指標の詳細について次項で示す。
2.5 通知時間
大電流用配線やトランス、インバータの異常は発現から機器表面の温度が上昇し故障リスクのある温度に到達するまで最短でも60 分要することが温度上昇試験から分かった。これはインバータなどの対象機器に電源や負荷を投入してから温度が飽和するまでの時間を測定することで検証した。
保全員は異常を検知してから現場に向かい、設備の停止、修繕の実施などの判断をするまでの時間は現場までの距離によって変化するが、先のヒアリング結果から、9割以上の工場で異常発生現場に到着するまでに15分、現場に到着し異常の原因の調査と分析、対策に約15分要することがわかった。よって異常の発現から対策が完了するまでの時間が30分である。故障リスクのある温度になるまでに60分であるため、30分以内の時間でユーザーに知らせる機能の実現が望まれる。
異常現象の発生から最終的に到達する温度を[℃]、実際の温度
が
×0.95(
-5%と表記する)になるまでの到達時間を
[min]、予測による到達温度(以下、予測温度という)を
[℃]、予測を完了する時間(通知時間)を
[min]とし、
≦30 分を目指す。図2に
=100℃の時の各パラメータの概要を図示する。
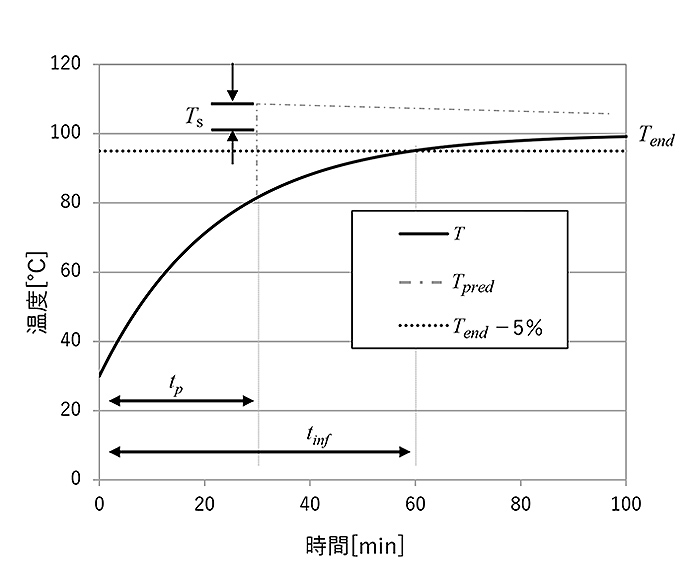
2.6 通知精度
図2の通り、最終的に到達する実際の温度と予測温度
の誤差を通知精度
(=
-
)とする。到達温度予測は装置の停止により発生する機会損失や発火発煙を防止する機能であるため、正常を異常と判定する誤検知よりも、異常を正常と判定することに起因する検知漏れを重要視する。温度センサで計測した場合、通知精度はセンサが持つ固有の精度定格にも依存する。そこで温度センサの精度定格を考慮したうえで検知漏れを最大限に防ぐためマイナス側の誤差目標は-5℃とする。
プラス側の誤差があると過剰通知により保全員に無駄な工数をかけてしまう。盤内に存在する樹脂材の中で最も発煙しやすい材料は配線材料などに使用されるポリ塩化ビニル(PVC)でその熱分解温度はおおよそ180℃程度であると言われている。安全を期して100℃以上が発火発煙リスクを伴う温度と定義する。盤内機器の使用温度範囲は50℃で設計されることがほとんどで、使用環境は50℃が上限と考えられる。また50℃環境で盤内製品を仕様最大負荷で使用した場合、製品表面の温度は最大でも80℃であることが実験結果から分かった。そのため通常の盤内製品の表面温度は80℃以下が動作可能な範囲といえる。それぞれの温度範囲をStepに分けた時、Step1が動作可能範囲で~80℃。Step2が80℃~100℃で注意喚起範囲、Step3が100℃~で緊急対応範囲とする。なお注意喚起範囲は監視対象が通常よりも発熱しており、監視対象の温度を下げる対策を実施したほうが良い温度範囲で、緊急対応範囲は監視対象が故障リスクに入っており、すぐにでも対策を要する温度範囲を意味する。Step2の幅を超える誤差がなければ実際にはStep1でStep3の誤検出が発生することはなく、緊急対応に移行することはない。仮に予測温度がStep3で実際の到達温度がStep2であったとしても、注意喚起範囲であることが通知されるため、そこで改善対応等につなげることもできるため完全に無駄な工数になることもない。よってプラス側の通知精度目標はStep2の幅である+20℃以下に誤差範囲を設定する。よって-5℃≦≦20℃を満たすことを目指す。
2.7 突発型異常モードに対応するための課題
目標として掲げた「通知性能」を達成するために解決すべき課題として以下の3 点を設定した。
- (a)
- 突発型異常モードによる温度変化を熱モデル化する計測した温度データから製品固有のパラメータを算出し、到達温度を予測できる熱モデルを構築する。
- (b)
- 熱モデルを利用して到達温度を予測する先に設定した目標である「通知時間」を満足する予測アルゴリズムを構築する。
- (c)
- 予測の精度を高める先に設定した目標である「通知精度」を満足する予測アルゴリズムを構築する。
3. 到達温度予測機能の開発
3.1 熱モデル化
熱モデル化を実行するにあたって、制御理論を用いて温度を予測できるモデルを構築する。制御理論による温度予測は体温計が瞬間的に人体の温度を予測する技術が知られている3)。体温計の場合、熱源(=人体)が一定の温度を保っており、人体-計測器の間にある構造物の熱容量や熱抵抗(すなわち伝達関数)が一定であるモデルを採用することができる。しかしながら、盤内温度監視の場合は、監視対象の温度は逐次上昇しており、監視対象が持つ伝達関数が未知であるため、計測温度から未知のパラメータを算出して温度予測する必要がある。
突発型異常モードは正常状態から異常状態に瞬間的に変化して温度変化する。この状態の変化をステップ状の状態変化といい、このときの温度変化は1 次遅れ系であることは一般的に知られている4)。これについては制御盤内に一般的に使用されるDC 電源を一定の負荷状態で駆動したときの温度変化を計測したところ、図3 のように1 次遅れ波形になっていることからも明らかである。
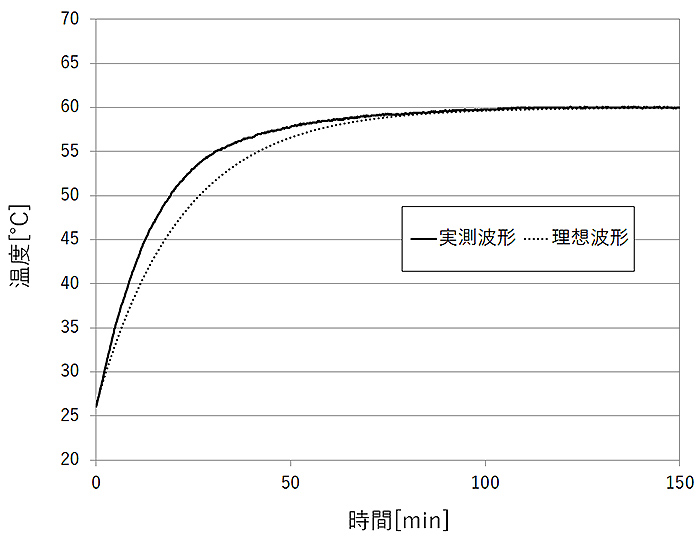
1次遅れ要素の伝達関数は式(1)のように示せる。ただし、はラプラス演算子、
はゲイン定数、
は時定数を表す。
ステップ状信号が入力された場合、時間応答は図4のように表される。一般的にインデンシャル応答、またはステップ応答と呼ばれる。今回の場合、入力は異常の発現を意味する。
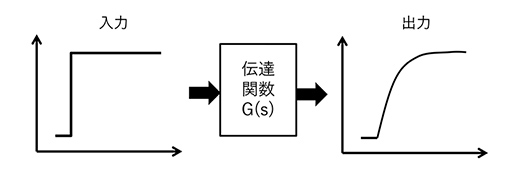
時間応答は次式(2)により求められる。
式(2)のステップ応答の変化率は、式(2)の時間微分で求められる。次に時間微分の式(3)を示す。
この変化率は、時間
から
だけ経過すると、次式(4)のような比率となる。
したがって、どの時刻でも、経過時間
が一定であれば減衰率は一定であることが言える。これは変化率が
経過したとき
倍になることを意味する。一般化するため
と置き換えた時、式(4)は式(5)で表される。これを図で表したものが図5である。
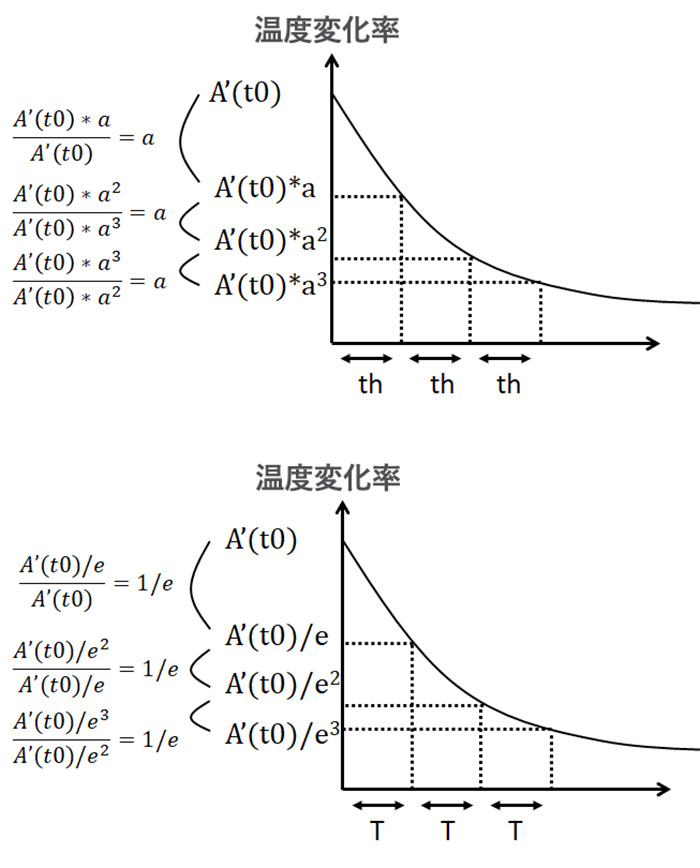
式(5)により、時刻から時間
経過後の温度変化率は式(6)で表される。これにより温度変化率が比率
変化したときの時間
を求めることで任意の時間における変化率を予測することができる。
温度変化率を時刻から
経過までの時間で積分することで時刻
からの温度変化量を求めることができる。まず、ある時刻
での
と
および変化率の減衰期
を計測する。減衰期
は、変化率比が
になるのに要する時間である。
および
を初期値として一定の減衰期
で変化する温度の収束値(予測温度)
=
(
→
)は、次式(7)で計算することができる。なおここでは便宜上
を
として表す。
これにより減衰期を求めることで予測温度を算出する熱モデルを構築することができた。
3.2 予測アルゴリズム
検証のモデルケースとして正常温度30℃、異常温度=100℃、到達時間
=60 分とする。
を算出することで予測温度
を算出できることが分かった。
はある時刻
における変化率が
倍されるまでに経過した時間から算出可能であることが図5 や式(5)から明らかである。
図5 からわかるように異常の発現の直後に温度変化率は最大となる。そのため最大温度変化率から変化率がその倍になるまでの時間を
とすることにより最速での予測が可能となる。このとき
=
となる。
=
≦30 分となるようにモデルケースに適用させ計算した結果
=0.3であれば
≦30分以下となる。シミュレーションによる温度変化の結果を図6に示す。なお、
>100℃の場合でも1次遅れであることが変わらないため同様に成立する。
式(7)に=0.3とした結果を代入することで式(8)を得ることができる。ただし、log は自然対数である。
以上により、予測温度 は、時刻
における温度
、温度変化率
、変化率の減衰期thを用いて式(8)により算出することができる。
上記内容の処理フローを図7に示す。
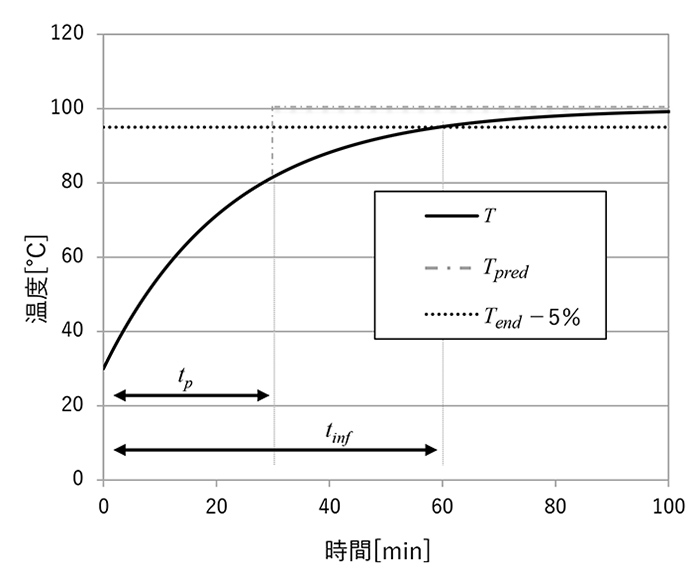
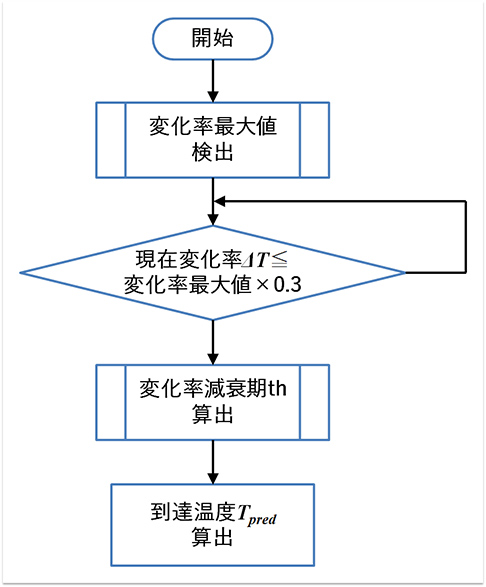
3.3 温度センサを用いた到達温度予測
今回同時に開発した温度センサであるK6PM-THSの性能を表2に示す。
項目 | 性能 |
---|---|
精度定格 | ±5℃ |
連続2 回の計測値の最大バラつき | 1℃/s |
温度変化率によって予測温度の精度が大きく影響することが式(8)からわかる。K6PM-THSの連続する2回の最大変化率は1℃/s以下である。事前に検証した1次遅れ系の温度変化グラフから
=30分、
=1℃/s、最小サンプリング時間である1秒を適用したとき、予測温度
は式(8)から
=
+1℃×0.83×30×60=
+1494℃となる。つまり温度測定値の1℃/sのゆらぎにより予測温度が1494℃変化することを示す。この温度測定値のゆらぎの影響を低減するため、計測温度に対してディジタルフィルタによるノイズ処理を実行する。
ディジタルフィルタは以下の計算式(9)で表される。
ただし
ここで、は時定数、
は基準サンプリング時間(ここでは1秒)となる。注意点として、この時定数
が長くなるほどリアルタイムな温度から遅れた表示となってしまう。すなわち通知時間に遅れが発生する。これは変化率の減衰比率
を調整し、
=
を通知時間の遅れ分だけ小さくすることで対応できる。またディジタルフィルタは式(9)の通り1次遅れでノイズを減衰させるフィルタ処理であるため、製品の1次遅れ温度上昇と乗算され2次の遅れが発生する懸念がある。このとき図8からも明らかであるように2次遅れの最大変化率算出後の変化率は1次遅れの変化率より大きい。これはフィルタ時定数が大きいほど、フィルタ後の変化率も時間的に遅れるためである。そのため、予測温度が大きく出力され、通知精度に影響する。これについては時定数
を調整することで通知精度を満足させる。
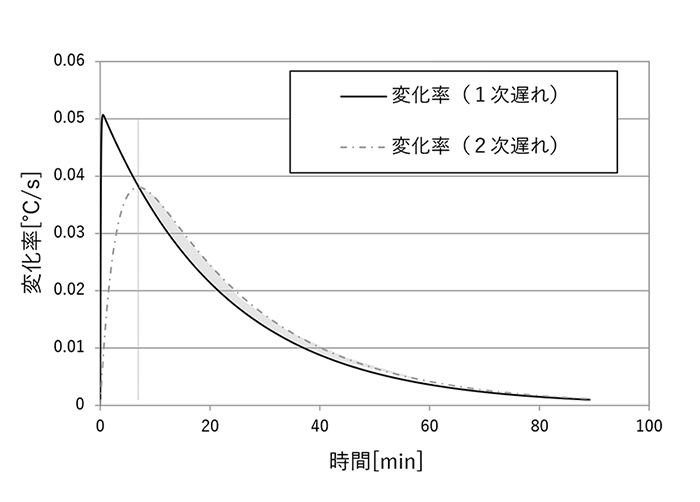
最悪条件において通知時間を満足すると
を決定する。予測式(8)の右辺右項が最大となる直前に連続する2回の計測結果が1℃/sの速さで上昇したときが最悪条件であるため、モデルケースに最悪条件を組み合わせてシミュレーションを実行した。
=0.5、
=3分で通知性能について満足することが分かった。表3にその時の通知性能結果を示す。なお図8で説明した通り、2次遅れを要因にして予測温度をマイナス側に算出することがないのは明らかであり、誤差はセンサが持つ精度定格に依存する。通知精度は目標とする-5℃≦
≦20℃を満たすため問題ない。
通知時間 tp[min] | 通知精度 Ts[℃] |
---|---|
25.1 | +14.1 |
4. 実験結果
4.1 検証結果
今回開発した赤外線センサK6PM-THSを用いて、実際のフィールドで監視対象に各種異常モードを実現し性能評価を実施した。監視対象と異常モードについては表4のとおりである。
実際の発火発煙や故障相当の異常を模擬することは困難なうえに危険を伴うと判断し、温度上昇幅についてはモデルケースに対して大きくない到達温度40 ~ 60℃程度の異常モードで検証した。また、実験対象とした電源やSSR(Solid State Relay)は今回対象と置いているインバータなどに比べて質量が小さく、温度が飽和する時間が短い。1次遅れは線形モデルの性質を持ち、時間方向、温度方向について時定数やゲイン定数を定数倍した場合に相似形であることがわかっている2)。つまり が定数倍された場合、
も定数倍される特性を持つ。よって、目標数値である
=60分のとき
≦30分と同じ比率を用いて、通知時間は
≦
/2 を満足することを目標とした。通知精度は-5℃≦
≦+20℃を目標とした。
検証結果を表5 に示す。いずれの条件においても目標とした通知性能を満足していることがわかる。
監視対象 | 異常モード | 詳細 |
---|---|---|
電源 (60W) |
端子ねじ緩みによる接触不良 | ねじを緩ませた状態で電源投入。 |
SSR (定格20A) |
ファン停止 | 定格電流の100%の条件で電源投入&ファンを駆動。温度が安定してからファンを停止。 |
コンタクタ (定格25A) |
過負荷 | 定格電流の100%の条件で電源投入 |
監視対象 | 異常モード | 通知時間 | 通知精度 Ts[℃] | |
---|---|---|---|---|
通知時間 tp[min] | 到達時間 tinf[min] | |||
電源 | 端子ねじの緩みによる接触不良 | 12.0 | 25.0 | +2.1 |
SSR | ファン停止 | 13.5 | 27.5 | +1.1 |
コンタクタ | 過負荷 | 19.0 | 45.2 | +1.5 |
5. むすび
突発型の異常モード発生に対して、提案するユニークな到達温度予測技術により早期の温度異常の検出が可能となった。さらに、通知性能を満足することで、事故や火災が発生する前に保全員が盤を改修繕する時間的余裕の創出が可能となった。本技術により特に異常発生が多いとされる大電流用の配線やトランス、インバータの温度早期検出ができる。
「盤内監視機器K6PM シリーズ」では盤内監視に必要な小型、広視野角の温度センサをラインナップし、本体には先に説明した到達温度予測機能以外に、外気温の影響をキャンセルする機能や異常と判断するための温度しきい値を自動で設定する機能を有している。これによって、人のスキルに頼らない、省工数の温度監視を実現するとともに、事後保全の最小化と予防保全への転換が図られると考える。
今後は減衰期をより短時間にすることで盤内温度異常のさらなる早期検出を実行していく。そのため、温度センサの高精度化やノイズキャンセル技術を開発していく。
参考文献
- 1)
- JEITA半導体部会半導体生産技術専門委員会.“Φ200mm以下装置の長期利用における半導体製造ライン操業リスクの概観”.2012, 5 p.
- 2)
- 東京海上日動火災保険株式会社.“リスクマネジメント最前線”.2012, 3 p.
- 3)
- オムロン株式会社.電子体温計,特開昭60-209125.1985.
- 4)
- 近藤文治.基礎制御工学.森北出版,1977,p. 35-36,228 p.
本文に掲載の商品の名称は、各社が商標としている場合があります。