フローはんだ付け品質安定化における噴流高さ管理の重要性
PCやスマートフォンといった高機能電子製品だけでなく、FA機器やパワーエレクトロニクス製品といった大電流が流れる製品でも小型化が進み、プリント配線板の多層化や厚さ増加によって基板の熱容量が増大している。大型部品のはんだ付けには、加熱性能の高いフローはんだ付け工法が用いられることが多いが、基板と部品の高熱容量化により、十分な加熱が困難になりつつある。基板の高熱容量化に対応できるフロー工程の実現には、フロー装置の管理レベルの向上が必要となるが、現場で経験を積む機会の少ない現代の生産技術者は、装置管理の重要性を体感して理解するのが難しい。そこで、熱供給の観点から、フロー工程のはんだ付け品質にとって最も重要で、かつ最も変動しやすい要素であるはんだ噴流を取り上げて、噴流形状の変動によるはんだ付け状態の変化をデータによって示すことに取り組んだ。噴流形状は生産現場で定量的に計測することが難しいため、適切な噴流形状で生産できるかどうかは、管理する技術者のスキルに依存する。本稿では、噴流形状を代表する値のひとつである噴流高さと、基板および部品端子温度との関係性を示すことで、はんだ付け品質を安定化させるための噴流高さ管理の重要性を明らかにするとともに、高熱容量基板に対応していくためには、より細かい噴流高さ管理が必要となることを示した。
1.まえがき
PCやスマートフォンといった高機能電子製品だけでなく、FA機器やパワーエレクトロニクス製品といった大電流が流れる製品でも小型化が進んでいる。そのため、プリント配線板の多層化や、銅箔厚の増大、これらに伴う基板厚の増大が進み、プリント配線板の熱容量が大きくなってきている。また、これら大電流の製品では、大型の自立型アルミ電解コンデンサが用いられるなど1)、搭載部品の熱容量も大きい。熱容量の大きい部品のはんだ付けは、温度上昇に時間がかかるため2)、加熱性能の高いフローはんだ付け工法が用いられることが多いが、この工法でさえも近年の基板の高熱容量化に対して十分な加熱が困難になりつつある。加熱が不十分だと、スルーホール内をはんだで満たすことができず、接合強度の低下を招く。
フローはんだ付け工法は、溶融はんだを噴出することで基板にはんだと熱を供給しており、溶融はんだの噴流状態によって、はんだ付け品質が左右される。生産現場では、工程管理基準によって噴流状態を一定の範囲内に収めているが、良い噴流とはどのような状態で、それはなぜかということを生産技術者が理解していないと、刻々と状態が変化する噴流を適正範囲で維持しつづけることは難しい。ベテラン技術者は積み重ねてきた現場経験によって、噴流状態の良し悪しの判断を技能として身につけてきたが、今の若手技術者は現場経験を積む機会が少なく、基本的な知識の理解で留まっている。難易度の高い高熱容量基板のフローはんだ付けには高い噴流管理レベルが必要であるが、噴流形状を生産現場で定量的に計測することが難しいため、管理する技術者のスキル向上が不可欠である。そこで我々は、噴流形状の変化がはんだ付け品質に与える影響をデータで示すことで、現場経験の不足を補えるのではないかと考えた。本稿では、熱供給を主な観点として、噴流形状を代表する値のひとつである噴流高さと基板および部品端子温度との関係性を評価し、はんだ付け品質を安定化するための噴流高さ管理の重要性を明らかにした。
ただし、必要な熱供給を実現できた場合でも、フラックス量が不足していると、はんだの濡れが低下し、はんだ付け品質が悪化する。本稿では、十分な加熱条件下において、フラックスの過不足により発生する問題を示した。
2.フロー工程安定化の課題
フローはんだ付け工程の基本構成を図1に示す3)。工程は、フラックス塗布、フローはんだ付けからなり、フローはんだ付け装置では、プリヒート、1次噴流、2次噴流の3段階の加熱が行われる。プリヒートでは、塗布したフラックスに含まれる溶剤の揮発と基板の予備加熱を行う。噴流は2種類で、多数の小さな山状にはんだが吹き上がる1次噴流と、ひとかたまりで穏やかにはんだが流れる2次噴流である。1次噴流はスルーホール内や密集した表面実装部品の接合部にはんだを供給しやすくすることを、2次噴流はフィレット形状を整えることを狙っている。フローはんだ付け工法では、噴流による熱とはんだの供給が、はんだ付け品質にとって最も重要な要素であるが、設備状態や溶融はんだ状態のゆらぎが噴流状態を左右することから、最も変動しやすい要素も噴流である。基板の熱容量が大きくなるほど、はんだ付けに必要な熱量が増えることから、噴流による熱供給の安定化はますます重要になると考え、フローはんだ付け状態の指標のひとつであるフローアップ(スルーホール上面まではんだが満たされている状態)を評価項目として、噴流変動とはんだ付け状態との関係を評価した。
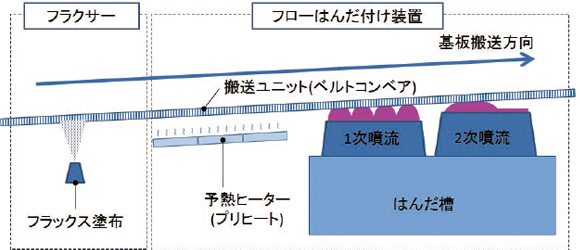
また、熱供給以外の観点として、フローアップにはフラックスの還元作用が必要であることから、フラックス塗布量とはんだ付け状態との関係を評価した。塗布量が不足するとはんだの濡れが悪化し、塗布量が過剰だと濡れは良好となるが、ボイドの発生により信頼性リスクが高まる。
3.実験内容
3.1 実験概要
噴流とフラックスの変動によって、はんだ付け状態がどのように変化するのかを確認するために3つの実験を行った。最初に、フローアップするために必要な温度を確認した。基板および部品の温度とフローアップを紐付けることで、温度測定によるフローアップ評価を可能にした。次に、噴流の変動による温度の変化量を評価し、噴流管理の重要性を確認した。最後に、フラックス塗布量を変化させたときのはんだ付け状態を評価した。実験で使用したはんだの組成はSn96.5/Ag3.0/Cu0.5(質量%)である。
3.2 フローアップ温度確認実験
はんだ付けでは、はんだと母材との間で合金層が形成される必要があるため、母材をはんだ融点以上の温度まで上昇させなければならない。基板上面までのフローアップを狙うため、基板と部品それぞれの基板上面位置を温度測定ポイントとした(図2)。はんだが温度測定ポイントの位置まで濡れ上がったときの母材温度が、フローアップに必要な温度となる。濡れ上がりの判定は、温度プロファイル上で行った。温度測定ポイントに取り付けた熱電対が高温の溶融はんだに接触すると、測定値が急上昇することから、急上昇する直前の温度をフローアップ温度とした。確実にフローアップさせるために、はんだ温度を270℃に設定し、噴流の途中でコンベアを止めて10秒間加熱して測定した。
評価に使用した基板の仕様を表1に示す。部品には大型の自立型電解コンデンサを使用した。導いたフローアップ温度が、使用した評価基板以外でも適用できることを確認するために、同じパターン寸法で層数のみ異なる2層評価基板を用いた測定も行った。
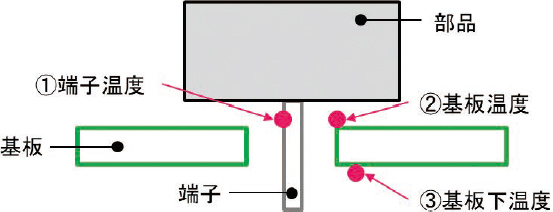
外形寸法 | 50mm×50mm×1.6mm |
---|---|
Cu パターン寸法 | 45mm×45mm×0.035mm |
層数 | 6層、2層 |
スルーホール径 | 2.0mm |
3.3 噴流高さ評価実験
生産現場では、ガラス板観察や温度測定によって噴流の基板への接触を確認している。接触しているかどうかの判断には特別な技能は必要ないが、接触の程度から、加熱性能がどれだけ異なるか、はんだ付け品質に問題がないかを判断するには経験が必要である。基板への熱供給に大きく影響すると考えられる噴流高さについて、その条件と温度の関係を評価した。
評価条件を表2に示す。噴流高さは基板を基準に定義した。図3に示すように、基板が噴流に突入した時に、はんだが基板に乗り上げない限界の噴流高さを基板上限とし、上限高さから基板厚とほぼ同じ1.5mmだけ低くした噴流高さを基板下限とした。上限と下限との噴流高さ変更は、はんだ槽の高さを上下して行った。1次噴流と2次噴流はそれぞれ個別で評価し、コンベア速度1.0m/minのときの1次噴流のはんだ付け時間は約2.5秒、2次噴流のはんだ付け時間は約2.1秒であった。
噴流高さ | 基板上限/基板下限 |
---|---|
はんだ温度 | 260℃ |
コンベア速度 | 1.0m/min |
基板 | 6層評価基板 |
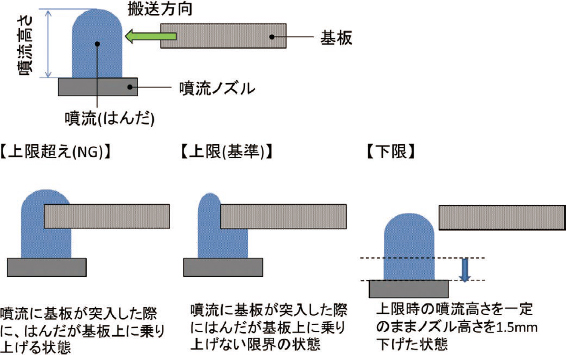
3.4 フラックス塗布量評価実験
フローアップには母材温度だけでなく、フラックスによる母材の酸化膜除去も必要である。母材温度がはんだ付け可能な温度に到達していても、酸化膜が除去されていないと、はんだが濡れず正常な接合ができない。そのため、生産現場ではフラックス塗布量や基板全面にムラなく塗布できていることを確認している。今回、フラックス塗布量を、過少/適量/過多の3通りで設定し、はんだ付け状態への影響を評価した。塗布条件を表3に示す。
フラックス塗布量 ⒜過少、⒝適量、⒞過多 |
(a) 30ml /m2、(b) 100ml/m2、 (c) 100ml/m2+刷毛塗り |
---|---|
コンベア速度 | 1.0m/min |
ノズル速度 | 600mm/s |
4.実験結果
4.1 フローアップ温度の確認結果
測定した温度プロファイルを図4に示す。基板、端子ともに、約180℃で温度が急上昇した。熱容量の小さい2層基板の場合でも、急上昇する温度は同等であった。この結果から、180℃をフローアップ温度として以降の評価を進めることにした。フローアップ温度が、Sn/Ag3.0/Cu0.5はんだの固相点217℃4)よりも低いのは、測定値として出力される温度が母材温度そのものではなく、あくまでも熱電対の温度であるためである。熱電対は母材に接触しているが、外気にも触れているため、母材よりも低い温度が測定温度となる。
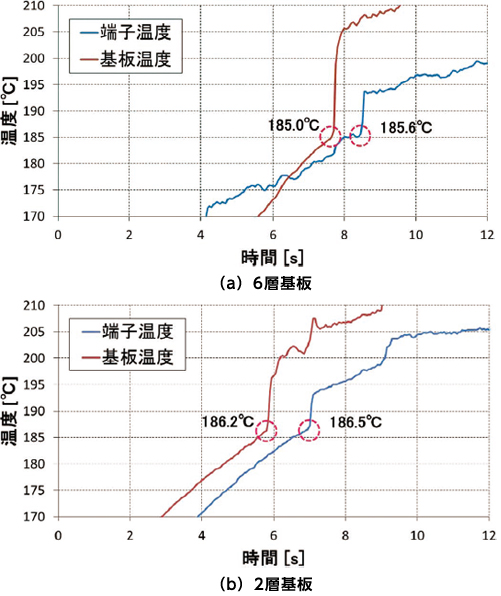
4.2 1次噴流高さの評価結果
1次噴流の噴流高さによる基板接触の様子と温度プロファイルの違いを図5と図6に示す。噴流の基板接触は、基板の代わりにガラス板を搬送し、ガラス板が噴流エリアに到達したときに上から観察することで確認した。噴流高さ下限の場合、基板下温度が一時的に低下することがあった。ガラス板の接触から分かるように、基板上限まで噴流が上がっていれば、噴流列間もはんだが接触しつづけているが、基板下限までの噴流高さだと局所的な接触となり、噴流が離れる領域が存在してしまう。基板上限までの噴流高さがあれば、噴流の非接触による加熱ロスを低減することができることが分かった。フローはんだ付け工程では基板に搭載される部品の仕様によりはんだ付け時間が制約されるため、高熱容量基板では、はんだ付け時間中の加熱ロスを防ぐことが特に重要である。そこで、基板下面の噴流接触状態を定量的に評価するために、基板下温度曲線の面積を算出した。図6の点線で囲った領域の
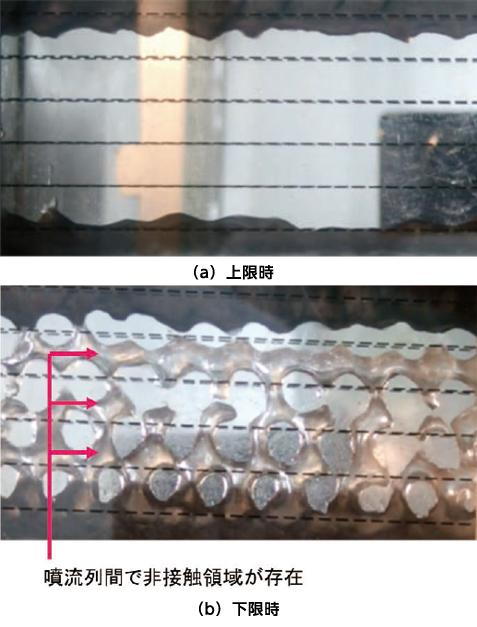
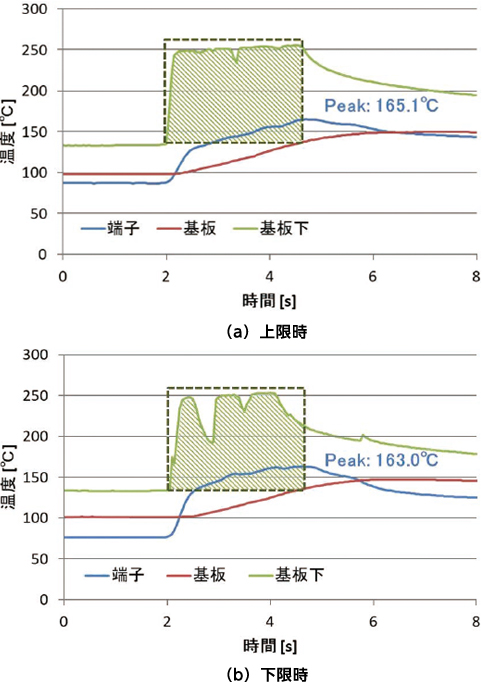
面積から、噴流による加熱量を表せると考え計算した結果、噴流高さ下限では面積が約20%減少することが分かった。しかし、加熱量が20%異なるにもかかわらず、基板と端子のピーク温度は、噴流高さ上限と下限で数℃程度の差しかなく、本評価基板の母材温度は180℃に達しなかった(図6)。1次噴流で端子温度をフローアップ温度周辺まで上げないと、2次噴流完了時のフローアップ達成は難しい。そこで、1次噴流で端子温度を180℃に到達させる手段を検討した。
噴流高さの影響が想定よりも小さかった理由として、噴流高さを基板突入時の高さで定めたために、実際にスルーホール内に進入する噴流の高さとは異なっているのではないかと考えた。スルーホール内で基板上限となるように、装置設定値の変更により噴流高さを基板上限よりさらに2mm上昇させて再度評価を行った(図7)。そのときの温度プロファイルを図8に示す。スルーホール内上限まで噴流を高くすることで端子温度がさらに上昇し、180℃に到達することが分かった。このときスルーホール上面から乗上げが発生してないことは確認している。
本評価で使用した自立型電解コンデンサの端子は、曲げ加工が施されているため、ストレートタイプの端子よりもスルーホール内に噴流が入りづらい。基板をスルーホール中央で切断し、端子が挿入されたときのスルーホール内部の状態を側面から確認したものを図9に示す。端子が曲がっていることによりスルーホール内に噴流が入りづらくなったため、噴流高さの影響が弱められ、温度差が表れにくかったものと考えている。
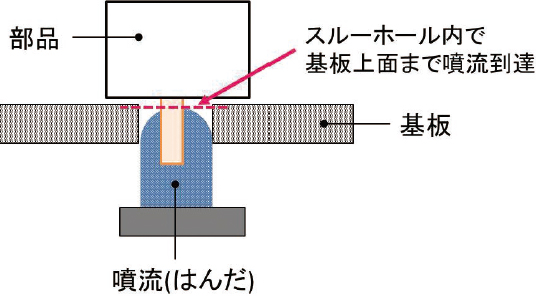
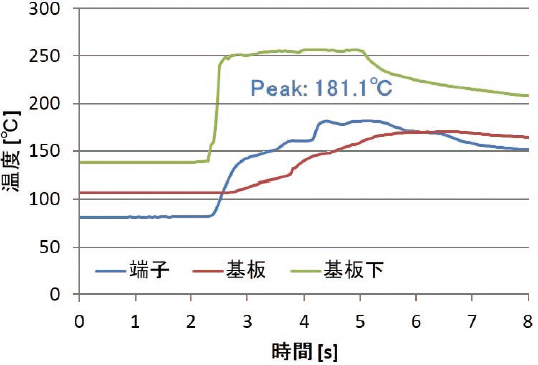
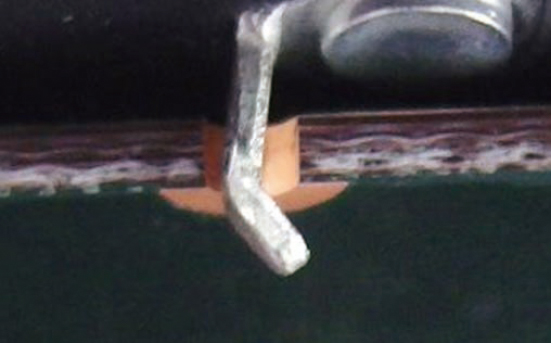
噴流高さによるスルーホール内の濡れ上がりの変化を、X線透過装置を用いて基板側面から観察することで確認した(図10)。噴流高さに合わせて濡れ上がり到達点が上昇しており、端子温度が180℃に到達した条件(噴流高さ:スルーホール内上限)において、基板上面まではんだが到達していることが確認できた。
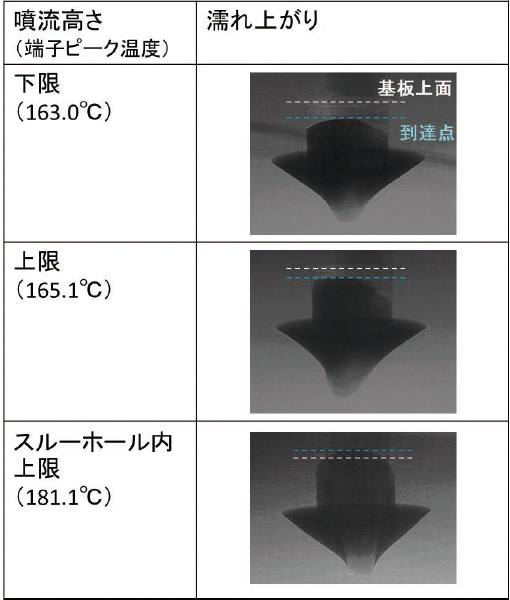
次に、はんだ付け時間について検討した。1次噴流のはんだ付け時間によるピーク温度の変化を図11に示す。はんだ付け時間に比例してピーク温度が上昇していることが分かる。はんだ付け時間を1秒延ばし、3.5秒にすることで180℃に到達することが見込まれる。このように、噴流高さとはんだ付け時間によって端子と基板の温度が変化することが分かった。噴流高さやはんだ付け時間は、ノズル内整流板の詰まりや液面高さなどによって経時的に変動する。噴流高さの影響をデータによって明らかにしたことで、この管理項目の重要性を示すこと
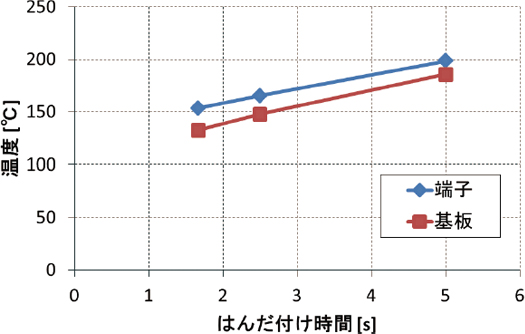
ができた。一方で、今後の高熱容量化に対応するためには、さらにきめ細かい管理をする必要があることも分かった。
4.3 2次噴流高さの評価結果
2次噴流の噴流高さによる基板接触の様子と温度プロファイルの違いを図12と図13に示す。噴流の基板接触は、1次噴流と同様にガラス板を用いて確認した。2次噴流はひとかたまりの大きな噴流であるため、1次噴流のような噴流高さに伴う接触状態の変化はみられず、噴流高さ下限でも基板下温度は安定していた。しかし、山型の噴流形状であるため、下限のときはガラス板の接触幅が狭くなっていた(図12)。2次噴流では、1次噴流のような噴流非接触による加熱ロスは起こらないが、加熱時間短縮による温度低下が起きることが分かった。ただし、ピーク温度差は数℃程度であり、大きな違いはみられなかった。また、使用装置では、2次噴流高さを基板上限を超えて高くすることができなかった。2次噴流では基板上限を超えて噴流を上げることによる加熱性能の向上は難しいことが分かった。
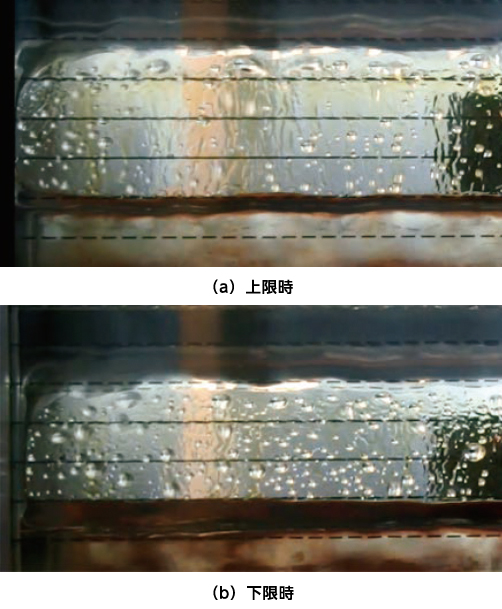
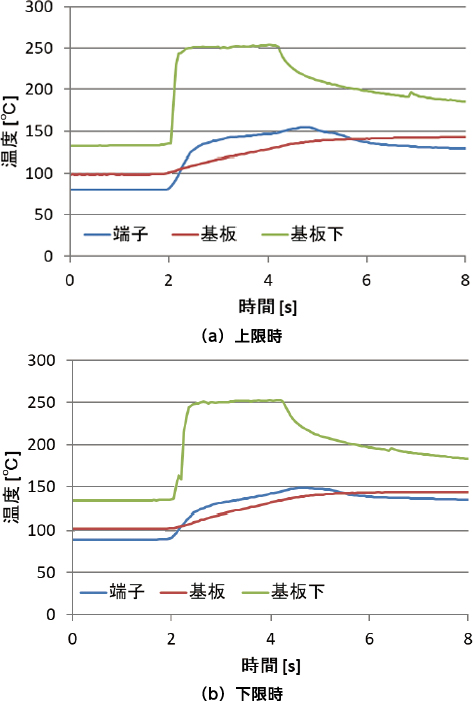
4.4 フラックス塗布量の評価結果
フラックス塗付量を変えた時の基板上面側はんだ付け状態の外観と、X線透過装置によるスルーホール内部のはんだ付け状態を図14に示す。フラックス塗布量が少ない場合、はんだは基板上面まで到達しているが、はんだと端子が濡れておらず、正常な接合ができていない。一方、フラックスを過剰に塗布した場合は、スルーホール内のボイドが増えてしまう。適切なフラックス量を導出するには、詳細な評価が必要だが、少なすぎても多すぎても接合に問題を起こす。フラックス塗布量は、塗布ノズルの詰まりなどによって変動するため、メンテナンスによって塗布不足や塗布ムラを防ぐことが重要である。
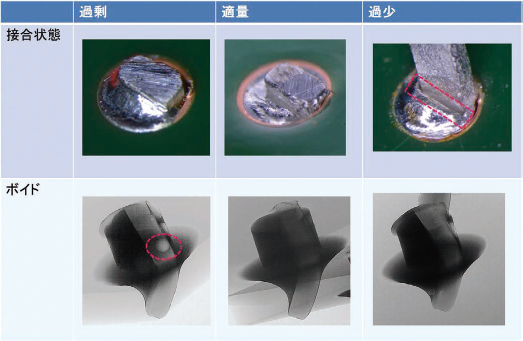
5.むすび
フローはんだ付け品質向上の実現には、技術者の噴流管理スキルの向上が不可欠であることから、噴流高さと基板および部品温度との関係性をデータで示し、噴流管理の重要性を明らかにした。このような取組みは、技術者のスキル向上の助けになるため、継続的に進めていきたい。
一方で、高熱容量基板に対して、これまで以上に細かな噴流管理が必要であることが分かった。従来型の人による管理では、きめ細かな管理には限界があるため、技術者のスキル向上だけでは十分な対策にならない。今後は、噴流高さのような重要な管理項目について、センシング等による数値化と監視について検討していきたい。設備や条件面では、噴流高さとはんだ付け時間の調整が有効であったが、噴流高さを上げると同一基板上の別のスルーホールからのはんだ乗上げが起こるリスクが増大し、はんだ付け時間は搭載部品の耐熱仕様範囲内に抑えなければならないため、いずれも限定的な範囲での対策でしかない。今後、噴流ノズルのカスタマイズといった噴流の加熱性能を向上する技術開発に取り組むことで、高熱容量基板のはんだ付け品質向上を実現したい。
参考文献
- 1)
- JEITA.2017年度実装技術ロードマップ.2017,p.266.
- 2)
- 大澤直.はんだ付の基礎と応用.工業調査会,2000,p.341-342.
- 3)
- 日本溶接協会 マイクロソルダリング教育委員会.標準マイクロソルダリング技術.日刊工業新聞社,2011,p.108.
- 4)
- 日本規格協会.JIS Z 3282.2006,p.602-603.
本文に掲載の商品の名称は、各社が商標としている場合があります。