制御モデルパラメータを用いた温度管理装置における状態監視機能の開発
- 温度調節器
- 設備保全
- 異常検知
- システム同定
- 状態基準保全
製造業では、少子高齢化などの環境変化により保全を担う技術者が不足している。また、設備の老朽化による突発故障の発生頻度が増えており、生産の稼働率が低下している。このモノづくりの課題を解決するためには、設備の劣化状態を把握して、故障する前に計画的に保全を行う“状態基準保全”に移行していくことが効果的と考えられている。一方で、この状態基準保全を実現するためには、管理基準とすべき状態を特定し、その状態を適正な精度で計測する必要があり、容易には取り組めない。本稿が対象としている温度管理装置においても同様の状況であり、ヒータや温度センサなどの保全は故障後の交換がほとんどである。
著者らは、温度管理装置の状態基準保全を可能とするため、制御工学の分野で一般的に使用される伝達関数を活用して、装置の特徴をベクトル化して扱うことで、保全が必要な箇所、および保全が必要となる時期の目途付けを可能とした。本稿では、この状態基準保全を可能とする状態監視機能の概要と、それを実現するための要素技術について述べる。
1.まえがき
製造業では、少子高齢化や学生の理系離れにより、保全を担う技術者の確保が困難になってきている。また、製造装置の老朽化により突発停止の発生頻度が増加し、生産の稼働率が低下するという経営課題が顕在化している。このようなモノづくりの現場の課題を解決するためには、設備の劣化状態を把握して、故障する前に計画的に保全を行う“状態基準保全1)”へ移行することが必要となる。しかしながら、保全を行うべき現象(以下、状態変化)を把握するための特徴量の抽出や特定が難しかったり、製造設備状態を計測するために、多くのセンシング機器を取り付けることが求められ、多額の設備投資が必要になることが製造業にとっての問題となっている。
製造工程の中で一般的に使用されている成形機、包装機といった温度管理が必要な装置(以下、温度管理装置)においても、状態基準保全が適用できれば、保全業務の効率化が期待できる。著者らは、温度管理装置に対する状態基準保全の特徴量として、システム同定2)によって得られるモデルパラメータ(以下、制御モデルパラメータ)の適用を検討した。
本稿では、制御モデルパラメータを活用して状態基準保全を実現した状態監視機能について説明する。第2章において、検出したい状態変化のメカニズム、および状態基準保全の取り組みを実現する上での問題点について示す。第3章では、目指すべき状態基準保全の概要、および実現するために必要な要素技術について示す。第4章では、要素技術を活用した状態基準保全の実現方法を示す。さらに、第5章にて、検証実験の結果を示す。
2.課題
2.1 温度管理装置における状態変化
図1に温度管理装置の構成を示す。温度管理装置は被加熱物を設定した温度にするために、温度センサで被加熱物の温度を計測し、この温度が一定になるように温度調節器が操作量を調整してヒータの熱量を制御する構成になっている。被加熱物は、成型機のシリンダ、包装機のヒートバーなどの熱伝導物、および製品に相当する。
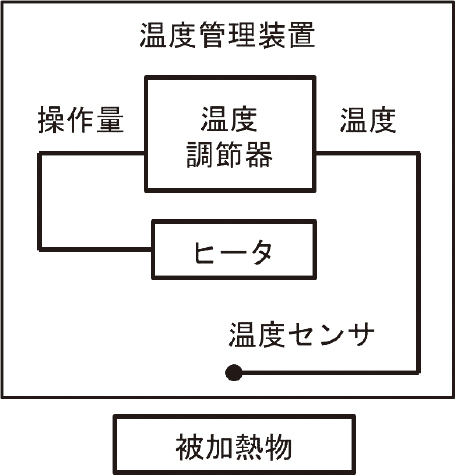
このような温度管理装置において発生する状態変化の例を表1に示す。状態変化は3つに分類することができる。状態変化分類Aは、温度管理装置に取り付けられているヒータ、温度センサなどの機器において、時間の経過によって発生する変化である。状態変化分類Bは、ヒータ、温度センサ、あるいは温度に影響を及ぼす機器が、定期メンテナンス時のヒューマンエラーなどによって取り付け状態が変わってしまうことで発生する変化である。状態変化分類Cは、被加熱物が、湿気を含んでいたり、成分が変わっていたり、大きさが変わっている等によって発生する変化である。
状態変化分類 | 状態変化名 |
---|---|
A | ヒータ容量低下 |
温度センサ起電力低下 | |
B | 温度センサ位置ズレ |
断熱カバー緩み | |
C | 材料変化 |
以降では、表1に示す状態変化の中でも特に発生頻度が高いヒータ容量低下、温度センサ位置ズレを例として、各々の発生メカニズムを2.2節、2.3節に示す。2.4節では状態基準保全を実現する上での課題について説明する。
2.2 ヒータ容量低下
ヒータ容量低下は、ヒータ素線の酸化が原因であり、ヒータとしての加熱能力が低下する現象である。正常時の制御波形(温度および操作量)と、ヒータ容量低下が発生した場合の制御波形を図2に示す。温度波形で比較すると、加熱能力が低下していることによって温度の上昇カーブが緩慢になる。また、操作量波形で比較すると、ヒータ容量低下が発生した場合は低下した加熱能力を補うために操作量が増加する。
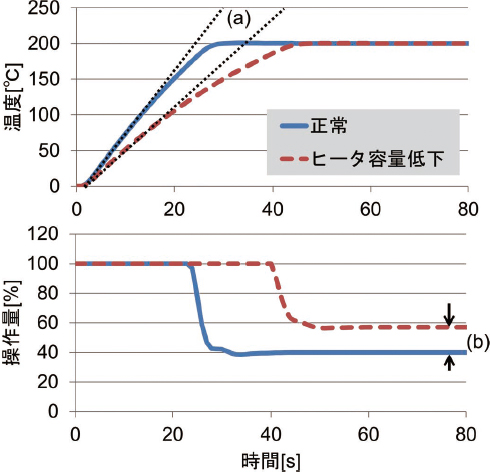
この現象を検出するための特徴量としては、以下の3種類が考えられる。
1)ヒータの酸化によって発生する抵抗値の変化
2)図2の(a)で示した温度上昇の傾き
3)図2の(b)で示した操作量の増加
2.3 温度センサ位置ズレ
温度センサ位置ズレは、ヒューマンエラーよって発生する現象である。図3のa)は、正常な場合の被加熱物の温度分布を示している。正常な場合は、図3のxの位置に温度センサがあるため、被加熱物のx’ の位置が目標の温度(T)となり、x’と離れた位置ではヒータと被加熱物の位置関係等によって温度差が発生していることを表している。
図3のb)は温度センサ位置ズレが発生している状態を表している。温度センサの位置がxの位置ではなく、yの位置に取り付けられている。このことにより、被加熱物ではy’の位置が目標の温度(T)となるように制御が行われる。ヒータと被加熱物との位置関係が変化していないことから、被加熱物上で発生する温度差は、正常な場合と同じになるため図3のb)で示した分布となり、正常時と比べると全体的に温度が上昇してしまう。
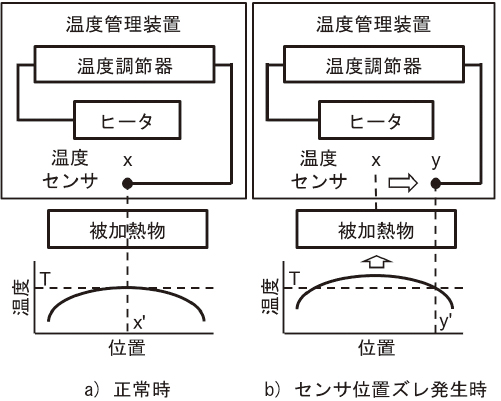
正常時の制御波形と、温度センサ位置ズレが発生した場合の制御波形を図4に示す。温度センサ位置ズレが発生すると、ヒータと温度センサの位置が離れるため、温度波形で比較すると、時間遅れが発生する。また、先に説明した通りに被加熱物の温度が正常よりも高くなることから、操作量波形で比較すると操作量が増加することになる。
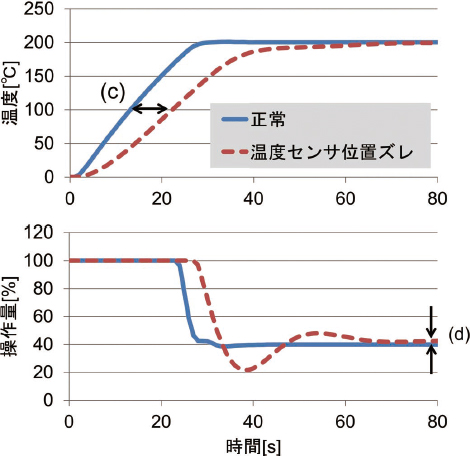
この現象を検出するための特徴量としては、以下の3種類が考えられる。
1)温度センサの取り付け位置
2)図4の(c)で示した温度上昇カーブの遅れ
3)図4の(d)で示した操作量の増加
2.4 状態基準保全を実現する上での課題
表1に示したような状態変化について、その発生メカニズムの解明ができれば、計測すべき特徴量を決定することができる。しかし、例えば2.3節で示した温度センサ位置ズレの場合は、初期段階では製品が正常時よりも僅かに変色しているといった製造不良として発見されるが、温度調節器の温度表示には変化が無く、温度センサの取り付け位置は目視できないといった状況下で、温度センサの位置がずれていることの特定に至るまでには手間を要してしまう。この原因特定の難しさが、状態基準保全への移行が進まない1つの背景となっている。また、保全工数が低減できない要因の1つとして、異常や故障の予兆を捉えることができたとしても、複数ある状態変化のいずれに起因しているのかを特定し、その変化の進行度合いを判定して最適な保全タイミングを決めるには至っていないという現状がある。このような状況から、状態基準保全への移行を容易にするために解決すべき課題として以下の3点を設定した。
1)装置の構成に依存しない共通性の高い特徴量の選択
2)複数存在する状態変化から、どういった種類の状態変化が発生しているのかを見分けること
3)見分けた状態変化の進行度合いを示すこと
3.状態監視機能の開発
3.1 特徴量の選定
特徴量として、2.2節の抵抗値、2.3節の温度センサ位置を計測する方式が考えられるが、装置毎に専用の計測器を取り付ける必要がある。また、図2、図4で示したような制御波形を視覚的に捉える方式も考えられるが、様々な装置、様々なタイミングで動作する制御波形が対象であることを考慮すると共通的な機能としての実現は困難である。そこで、著者らは、温度管理装置の温度と操作量の関係は、制御系の入出力に相当し、伝達関数3)を用いて表すことができることに着目して、化学プラントなどでの活用が提案されている4)制御モデルパラメータを特徴量として活用できると考えた。制御モデルパラメータは、状態変化に応じて変化し、その変化は状態変化の種類に対して再現性があるため、どのような装置に対しても共通して利用できる。
温度と操作量の関係は、伝達関数を用いて式1のように表すことができる。ここで、PV、MV、G、sはそれぞれ温度、操作量、伝達関数、ラプラス演算子を表している。

伝達関数Gは、制御モデルパラメータであるa、b(以下、特徴量a、特徴量b)を含み、一般的に式2のように表す。

特徴量a、bは、温度管理装置において、表2のような特徴を表現することができる。
制御モデルパラメータ | 表現できる特徴 |
---|---|
特徴量a | 温度の応答速度 |
特徴量b | 昇温能力 |
制御モデルパラメータの算出には、検出精度を高めるために装置動作に同期させて波形を収集することが必要であるが、制御波形の全体を入力情報として扱えるため、異なる温度管理装置から収集した視覚的に異なる制御波形であっても、必要な部分を切り出すなどの作業を必要としない。このため、制御モデルパラメータを特徴量として利用する方式は共通性が高い。尚、伝達関数(式2)は、どの程度の近似精度を求めるかによって、組み込む制御モデルパラメータの種類を選択することが可能であるため、対象とする温度管理装置の特性および検出したい状態変化の種類に合わせて最適化できる。本稿においては、分子を定数式、分母を1次式として記述する。
3.2 状態変化の見分け
状態基準保全の実現による保全業務の効率化のため、発生している状態変化の種類を特定できることが求められている。特徴量a、bには、表2に示した熱の伝達特性が現れるため、状態変化に応じた特性の変化を検出できる。状態変化の種類によって、反応する特徴量の組み合わせ、数値の変化方向、数値の大きさが異なるため、それらの変化を判定することで種類を見分けることができる。
正常な状態や、各状態変化が発生した状態の特徴量を図5に示す。正常とは、適切なメンテナンス直後など、状態変化が進行しておらず、良品を生産できる状態のことである。特徴量は、状態変化が進行するにつれて、正常を示す位置から、各状態変化を示す位置に向かって変化する。

状態変化の種類を見分けるためには、図5において正常と異常、さらに異常同士を分類すればよいので、例えば以下に示すような一般的な分類手法が利用できる。
1)コサイン類似度5)
2)サポートベクターマシン6)
3)k近傍法6)
コサイン類似度は、ベクトル同士の方向の近さ(角度)を数値化する指標である。特徴量が正常な状態から外れていく変化をベクトル化し、図6に示す予め登録しておく異常発生時の特徴量のベクトル(以下、異常発生ベクトル)に対して、現在の特徴量ベクトル(以下、現状ベクトル)の近さ(角度)を評価することで、どの状態変化が発生しているのかを見分ける方式である。
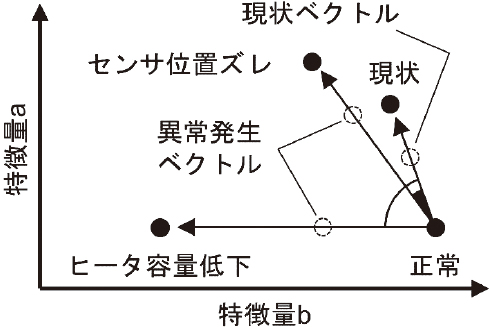
サポートベクターマシンは、最適化計算により図7に示すような境界線を引き、どの領域に含まれているかを見分ける方式である。
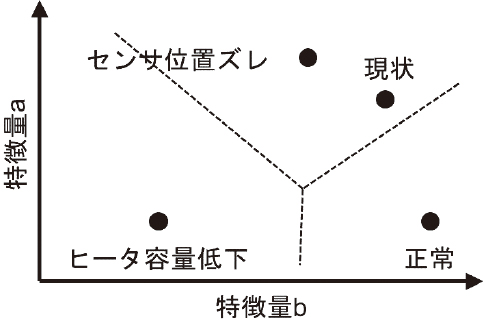
k近傍法は、図8に示すように、現在位置に対して距離によって評価する方式である。
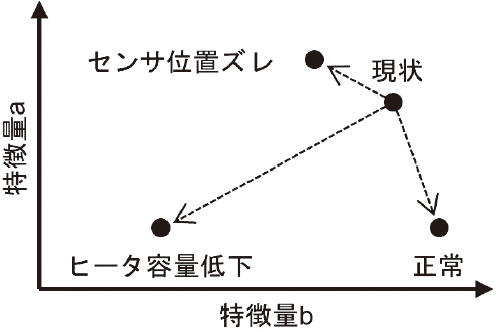
3.3 状態変化の進行度把握
状態基準保全を実現するためには、3.2節で示した分類手法を用いて状態変化を見分けた上、さらに状態変化の進行度を示し、故障に至る以前、あるいは製品の品質が低下する以前のタイミングで保全を行うようにする必要がある。
3.2節で示した分類手法の中で、コサイン類似度については特徴量の変化をベクトルで表現しているため、進行度もベクトルの大きさにより数値化できる。数値化は、図9で示すように、あらかじめ登録している異常発生ベクトルの大きさに対する、現状ベクトルの写像の大きさの比(q/p)で求めることができる。
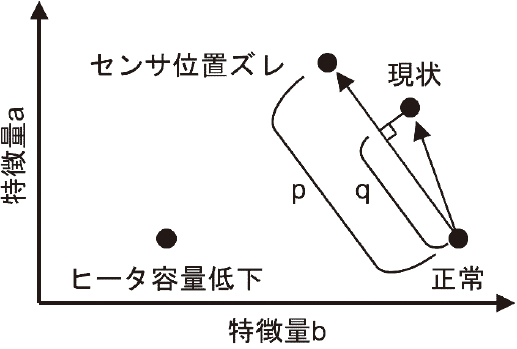
4.状態基準保全の実現
状態基準保全の実現は、3.2節で示したいずれの方式でも可能であるが、保全を担当する技術者が使いこなせる技術にするにはベクトルを使った方式が適していると考え、状態変化の見分けにコサイン類似度、進行度の表現にベクトルの写像を用いることにした。保全の実施手順を以下に示す。後述の計算式を説明するために、異常発生ベクトルをA、現状ベクトルをBと定義する。
Step1 異常発生ベクトルの登録
図6で示した正常位置、および異常位置について特徴量を算出し登録する。制御波形から特徴量を算出する方式には、システム同定法における予測誤差法2)などを用いる。
Step2 現状ベクトルの監視
温度管理装置を稼働する都度で現状位置の特徴量を計測する。
Step3 状態変化を見分ける
異常発生ベクトル、現状ベクトルを算出して、下式で類似度を求める。下式で求まる類似度は、類似性が高いと100%に近づき、類似性が低いと0%に近づく。

Step4 進行度の算出
類似度が高い(100%付近)場合は、下式で進行度を求める。下式で求まる進行度は、あらかじめ登録しておいた異常発生ベクトルと同じ大きさの場合に100%が求まり、小さければ0%に近づき、大きければ100%を超える値が求まる。
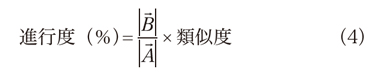
Step5 保全計画の立案実行
類似性が高いとした状態変化、および進行度を目安として、保全の計画を立案し実行する。
以上が、本稿で実現した状態基準保全を実施する基本的な手順となる。尚、上記手順は、異常発生ベクトルが複数存在していても独立して実行できるので、表1に示したような複数の状態変化を同時に監視することができる。また、本方式の特徴により、以下のような派生効果が期待できる。
(1)原因推定
温度管理装置内で、原因の分からない異常や故障が発生した場合でも、特徴量の変化を捉えることで、状態変化の発生していることが分かる。この特徴量と状態変化の相関関係を利用し、温度管理装置内でどのような現象が発生しているかについて推定ができ、原因特定にかかる期間を短縮できる可能性がある。
(2)周辺機器の監視
温度に影響を与える機器であれば、その異常や故障が特徴量に現れることが見込まれるため、例えば熱処理時に使用されるガスや薬液といった触媒の変化についても監視できる可能性がある。
(3)効果検証が容易
温度と操作量のデータが収集できれば、PCと表計算ソフトで効果の検証が可能である。
5.検証結果
5.1 検証実験の内容
この検証実験は、複数の状態変化に対する異常発生ベクトルを登録した状態から、進行度の異なる状態変化を発生させた場合に、状態変化を見分けることができ、進行度を適切に求めることができることを検証する。検証実験は、複数の状態変化を発生できる検証用の温度管理装置(図10)を使用して実施する。被加熱物(製品)を模擬したアルミニウムのプレートに130WのカートリッジヒータとK型熱電対の温度センサを固定した構成になっている。温度と操作量の時系列データは、温度調節器の通信機能を利用してPCに取り込む。PC上では、温度調節器から取得した温度と操作量の時系列データに対して、4章で説明した手順を実行させることで特徴量、類似度、および進行度を算出できる環境を構築している。計測は、実験のばらつきを考慮して、3回ずつ実施し、平均値を採用する。

検証実験は、2章で説明したヒータ容量低下と温度センサ位置ズレの状態変化を発生させて実施した。予め両者の異常発生ベクトル(以下、ヒータ容量低下ベクトル、温度センサ位置ズレベクトル)を登録しておく。期待する実験結果は、ヒータ容量低下を発生させた場合においては、ヒータ容量低下ベクトルに対する類似度と進行度が反応し、温度センサ位置ズレベクトルに対する類似度と進行度は反応しないことである。また、温度センサ位置ズレを発生させた場合は、その逆になることが期待する実験結果である。予め登録する異常発生ベクトルの発生条件は以下の通りである。
・ヒータ容量低下ベクトル:
ヒータ印加電圧10%低下(ヒータ容量19%低下相当)
・温度センサ位置ズレベクトル:
温度センサを1穴分遠い方向に移動
5.2 ヒータ容量低下の実験結果
ヒータ容量低下の検証実験は、ヒータ印加電圧を5%、10%、15%の3通りに低下させた条件で実施した。各条件の実験で得られた制御波形を図11に示す。ヒータ印加電圧の低下によって、2.2節で説明した通り、温度上昇の傾きが低下し、操作量が増加している。
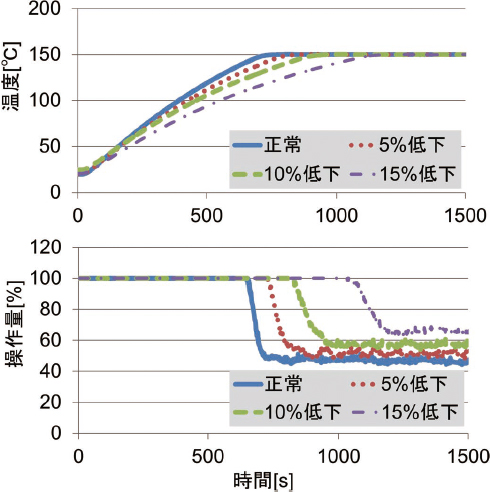
実験で得られた制御波形を用いて、制御モデルパラメータを算出した結果を表3に示す。状態変化が昇温能力を表現する特徴量bに表れている。
制御モデルパラメータ | ||
---|---|---|
印加電圧 | 特徴量a | 特徴量b |
正常 | 1058 | 2.71 |
5%低下 | 1053 | 2.48 |
10%低下 | 1024 | 2.16 |
15%低下 | 1018 | 1.95 |
表3の結果を用いて算出したヒータ容量低下ベクトルに対する類似度と進行度を表4の左側に、温度センサ位置ズレベクトルに対する類似度と進行度を右側に示す。類似度と進行度の数値は、異常ベクトルと一致した時に100%となる。
類似度については、ヒータ容量低下ベクトルによる判定で100%付近の値を示し、温度センサ位置ズレベクトルによる判定で0%付近の値を示していることから、状態変化の種類が正しく判定できていることがわかる。また、進行度については、類似度が高いヒータ容量低下ベクトルの判定結果のみを参照し、印加電圧の低下度合いが進行度の変化として捉えられていることがわかる。
ヒータ容量低下ベクトル による判定 |
温度センサ位置ズレ ベクトルによる判定 |
|||
---|---|---|---|---|
印加電圧 | 類似度 | 進行度 | 類似度 | 進行度 |
5%低下 | 99.8% | 43.1% | 0.0% | ― |
10%低下 | 100.0% | 103.5% | 0.0% | ― |
15%低下 | 100.0% | 142.5% | 0.0% | ― |
5.3 温度センサ位置ズレの実験結果
温度センサ位置ズレの検証実験は、温度センサの位置を1穴分、2穴分の2通りにずらした条件で実施した。各条件の実験で得られた制御波形を図12に示す。温度センサ取り付けミスによって、2.3節で説明した通り、温度上昇カーブが遅れている。
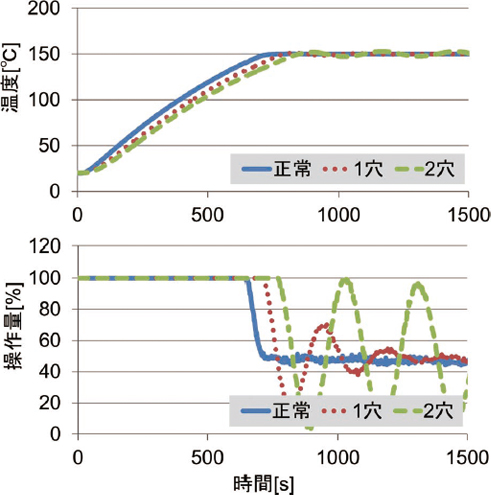
次に、得られた制御波形を用いて、制御モデルパラメータを算出した結果を表5に示す。状態変化が温度の応答速度を表現する特徴量aに表れている。
制御モデルパラメータ | ||
---|---|---|
ずらし量 | 特徴量a | 特徴量b |
正常 | 1058 | 2.71 |
1穴 | 1197 | 2.72 |
2穴 | 1468 | 2.71 |
表5の結果を用いて算出したヒータ容量低下ベクトルに対する類似度と進行度を表6の左側に、温度センサ位置ズレベクトルに対する類似度と進行度を右側に示す。
類似度については、5.2節の実験結果と逆になり、ヒータ容量低下ベクトルによる判定で0%付近の値を示し、温度センサ位置ズレベクトルによる判定で100%付近の値を示していることから、状態変化の種類が正しく判定できていることがわかる。また、進行度については、類似度が高い温度センサ位置ズレベクトルの判定結果のみを参照し、位置をずらした度合いが進行度の変化として捉えられていることがわかる。
ヒータ容量低下ベクトル による判定 |
温度センサ位置ズレ ベクトルによる判定 |
|||
---|---|---|---|---|
ずらし量 | 類似度 | 進行度 | 類似度 | 進行度 |
1穴 | 0.0% | ― | 99.7% | 106.4% |
2穴 | 0.0% | ― | 99.9% | 313.6% |
6.むすび
本稿では、温度管理装置における状態基準保全の実現のため、制御モデルパラメータを特徴量として活用した状態監視機能の開発と、検証実験の結果について示した。特徴量をベクトル化することで、発生している状態変化の種類を見分けることができ、さらに変化の進行度を知ることができるようになった。計測のために特別な機器を購入する必要もなく、容易に取り組みを始めることを可能にした機能である。今後は、制御モデルパラメータ以外の特徴量と組み合わせることによって、検出精度や感度の向上を目指す予定である。最後に、今回の開発および本論文執筆にあたり多大なご協力をいただいた方々に、深く感謝を申し上げる。
参考文献
- 1)
- 滝澤恒夫,金澤忠信.予防・保全システムにおけるサステナビリティ.電気設備学会誌.2014, Vol. 34, No. 6,p.385-388.
- 2)
- 足立修一.システム同定の基礎.東京電機大学出版局,2009,p.245.
- 3)
- 足立修一.制御工学の基礎.東京電機大学出版局,2016,p.284.
- 4)
- 松島洋輔.プラントの故障予測方法.特許第4520819号.2010.
- 5)
- 奥野陽,グラム・ニュービッグ,萩原正人.自然言語処理の基本と技術.翔泳社,2016,p.239.
- 6)
- 平井有三.はじめてのパターン認識.森北出版,2012,p.219.
本文に掲載の商品の名称は、各社が商標としている場合があります。