製造現場での機械学習運用におけるコンセプトドリフト検知手法の提案
- 異常検知
- コンセプトドリフト
- 因果関係
- 機械学習
近年は機械学習の普及に伴い、Factory Automation(FA)領域の製造現場においても、製品不良を予測するために異常検知を適用する事例が増えている。しかしながら、昨今の製品多様化や製造技術の複雑化により、FA製造現場では、Man(人)、Machine(機械)、Material(材料)、Method(方法)の4M変動の頻度が増加している。変動前に構築された異常検知モデルをそのまま運用している場合、誤検知が発生する。そしてこれへの対処が遅れると、製品不良率の増加につながる。
異常検知を運用中に入力データと推論結果の関係が、4M変動などによって運用前の学習時から変化することをコンセプトドリフトと呼ぶ。従来は平均値などを用いてこの変動によるコンセプトドリフトを対策していた。しかしこれでは、検知が遅れてしまい、課題があった。
本稿では、因果関係を考慮して、複数の異常検知モデルを統合することにより、製品不良の予測と4M変動によるコンセプトドリフト検知を両立する手法を提案する。この提案の有効性を、製造現場で使用される射出成型機を用いて検証した。
1. まえがき
近年は機械学習の普及に伴い、Factory Automation(FA)領域の製造現場においても、機械学習を用いて、製品不良を予測する事例が増加している。製造現場では良品率を向上させるために、少量の不良ラベルデータに適した異常検知が運用されることが多い。オムロンにおいても、AI搭載マシンオートメーションコントローラ1)を製品化しており、製造装置から収集したセンシングデータを入力として異常検知を行うことが可能となっている。
しかしながら、昨今の製品多様化や製造技術の複雑化により、FA製造現場では、Man(人)、Machine(機械)、Material(材料)、Method(方法)の4M変動の頻度が増加している。変動前に構築された異常検知モデルをそのまま運用している場合、誤検知が発生する。そしてこれへの対処が遅れると、製品不良率の増加につながる。
異常検知を運用中に入力データと推論結果の関係が、4M変動などによって運用前の学習時から変化することをコンセプトドリフト2)と呼ぶ。これへの対策として、従来は移動平均や、管理図の中心値に対して連続した高低を評価する連を使用した手法3)がとられてきた。しかし、これらの手法はリアルタイム性と運用スキル、工数の問題があった。
本稿では、因果関係を考慮して、製品不良の要因となる変数群と、それらの変数に影響を与える4M変動の変数群を特定する。それぞれの変数群から生成される複数の異常検知モデルを統合することにより、製品不良の予兆と4M変動によるコンセプトドリフト検知を両立する手法を提案する。さらに、提案手法によって、それぞれの事象を検知できることを製造現場で使用される射出成型機を用いて実証する。
2. 課題
本章では、対象システムの振る舞いを説明したうえで、解析対象の異常検知を行う際に発生するコンセプトドリフトの課題について説明する。
2.1 対象システム
対象となる射出成型機について、図1に紹介する。
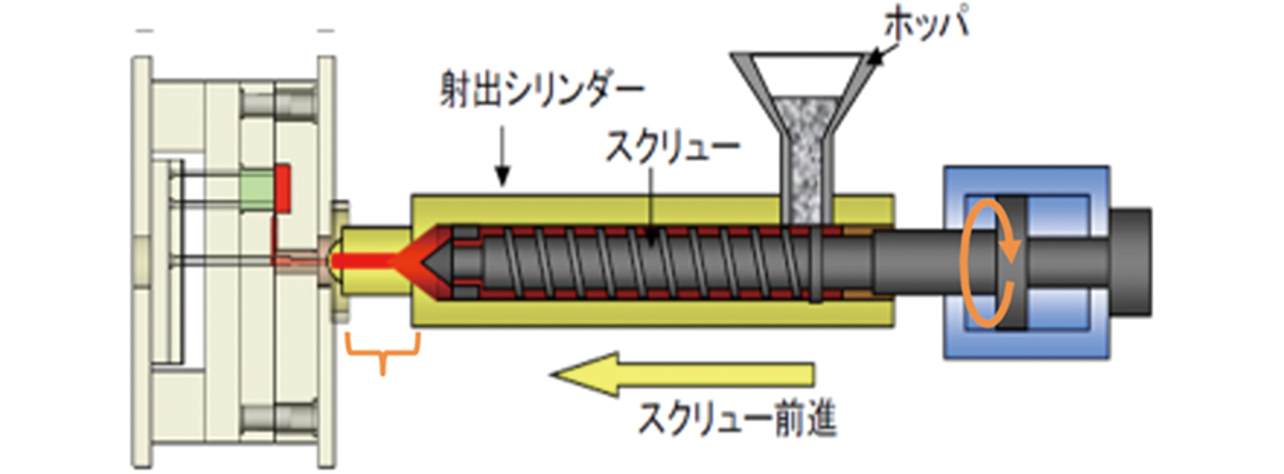
射出成型機は、金型内に可塑化溶融した樹脂(図1の赤部分)を高圧かつ高速で菅(図1の左)方内に射出することで、複雑な形状のプラスチック部品を精密かつ大量に生産できる4)。また、製品の型式毎に射出条件を変更することで、多品種の生産に対応できることが特徴となる。しかしながら、不適切な条件設定やスクリューに樹脂が残ることで、樹脂が金型内に十分に充填されない時には不良品となる。この不良品が発生する兆候を検知するために、圧力や時間、射出量などの変数を監視する。設定されたしきい値を超えた場合、不良が発生する前に、条件変更や清掃などの対策を実施することができる。
2.2 課題
成型不良の要因となる変数は、前節に示した通り圧力や時間、射出量など70種類程度存在する。従来は、ある条件下で発生した不良について、決定木の重要度による寄与度の高い変数を選択し、異常検知モデルを構築して、成型不良の予兆を監視していた5)。異常検知は正常データのみで学習モデルを構築できるため、不良データの少ない製造現場では有効な手法である。この方式を採用しているオムロンの製品であるAI搭載マシンオートメーションコントローラと同様の従来手法を用いて異常検知を実施した例を図2に示す。
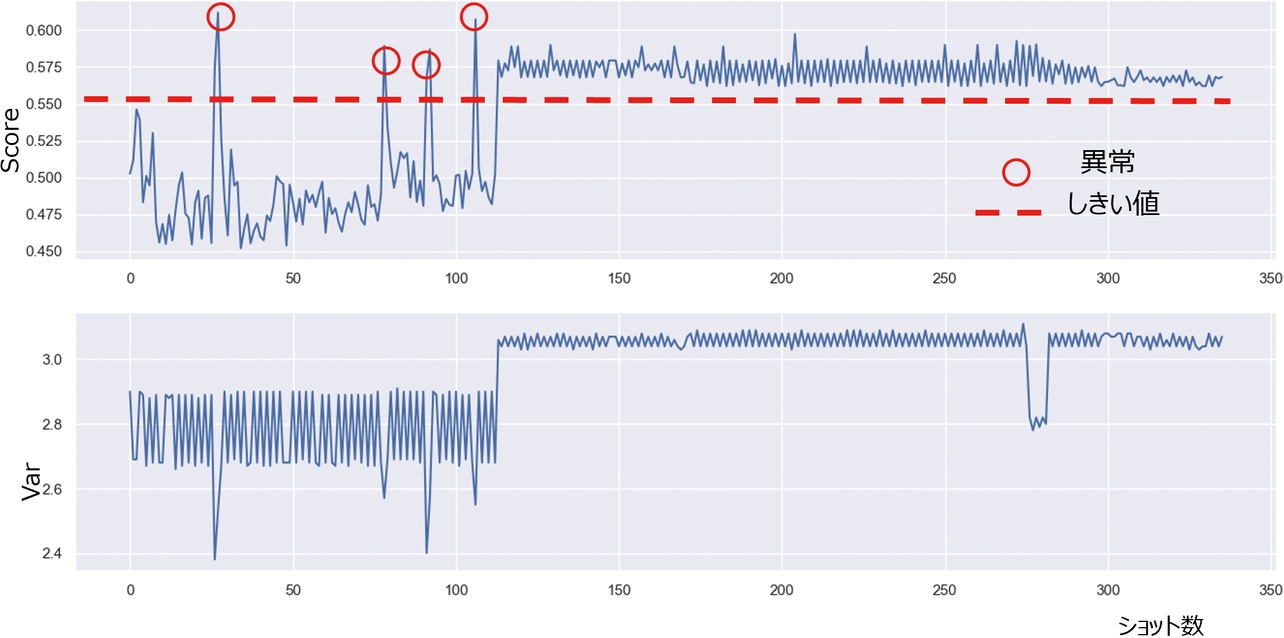
図2上のグラフは、異常検知の指標である異常度を示すスコアで、下のグラフは異常検知モデルを構成する説明変数の1つである。このモデルは異常度のしきい値を0.555として、成型不良の予兆検知を実施する。図2左の前半は、目論見通りの異常検知結果が得られているが、右となる後半の114ショット以降は、常にしきい値を超えている。これは、114ショット以降で生産している製品の型式が変更となったためである。結果として、型式変更後の異常を適切に検知できないことになる。型式変更後の不良を検知するためには、114ショットの時点で再学習をすることが必要になるが、このタイミングでは再学習することの判断が出来ない。そのため、長期に亘って不良を検知できないまま生産が続いてしまう。型式変更を即時に検知して再学習することにより、製品不良率の低減が見込まれる。
以上から、本稿では、成型不良の予兆検知の運用中に型式変更を検知することを課題とする。
2.3 提案手法に対する要件
前節で示したように、異常検知を運用中に入力データと推論結果の関係が学習時から変化することをコンセプトドリフトと呼ぶ。コンセプトドリフトには、時間経過に伴って変化するものと、突発的に変化するものがあり、製造する製品の型式変更などの4M変動は突発的に発生するものに分類される。対象となる成型機では、不良品生産を防ぐため、不良の予兆検知のリアルタイム性が要求される。
よって前節で示した課題は、製造現場での異常検知を運用中に、突発的なコンセプトドリフトを検知する手法によって解決される。
従来手法として、まずは連続してしきい値を超える状況を検知する方法が考えられる。具体的には、移動平均や管理図の連を用いるものがある。しかしながら、移動平均を使う方法は突発的な変動に対する追従が遅れるため、リアルタイム性の観点で適さない。さらに、連を用いた手法では、管理値などのしきい値以外のパラメータを決める難易度が高く、スキル面の問題がある。よって、スキルレスで運用するために調整するパラメータが不要であることが望ましい。
次に、製品の型式毎に異常検知モデルを構築することが考えられる。しかし、昨今の製品多様化のために型式数は10種類を超えるものが大半であり、それぞれについて異常検知モデルを構築して運用することは、データ管理やモデル生成、しきい値の設定など、運用工数面の問題がある。よって、運用中に監視する異常検知モデルは1つであることが望ましい。
以上から本稿では、まずリアルタイム性を持つコンセプトドリフト検知が必要となる。さらに、スキルレス運用のためにパラメータ調整が不要なことと、製品不良の予兆検知と4M変動としての型式変更の検知を両立することを要件とする。
3. 提案手法
3.1 提案手法の概要
本提案手法では、多岐に渡る異常検知アルゴリズム6)の中から、Isolation Forest7)を採用する。Isolation Forestは高速な推論を特徴としており、リアルタイムな検知が可能である。また、運用上しきい値以外のパラメータを考慮する必要が無く、運用スキル面の問題も少ない。本稿ではIsolation Forestを使用して、製品不良の予兆検知と4M変動である型式変更の検知を両立し、1つの異常検知モデルとして統合することを考える。不良の予兆検知と型式変更検知は、それぞれのしきい値を設定するのみである。これによって、運用工数減・スキルの簡易化・リアルタイム性の向上が可能となる。
以下、3.2節でIsolation Forestの概要を記載し、3.3節で製品型式と不良要因それぞれの影響・要因特定、3.4節で異常検知の統合、3.5節で異常度の算出について記載する。
3.2 Isolation Forestの概要
Isolation Forestは、正常、異常のラベルがついていない学習データからモデルを構築し、データの疎密に基づいて正常データと異常データを分類する異常検知アルゴリズムである。疎密は、データを一点になるまで分離するために必要なパーティションの数で判断される。疎な部分に属している点は図3 a)のように比較的少ないパーティション数で一点までに分割され、密な部分に属している点は図3 b)のように一点までのパーティションが多くなる。このパーティション数は図4に示すように2分木の深さとなり、これをもとに異常度を算出する。
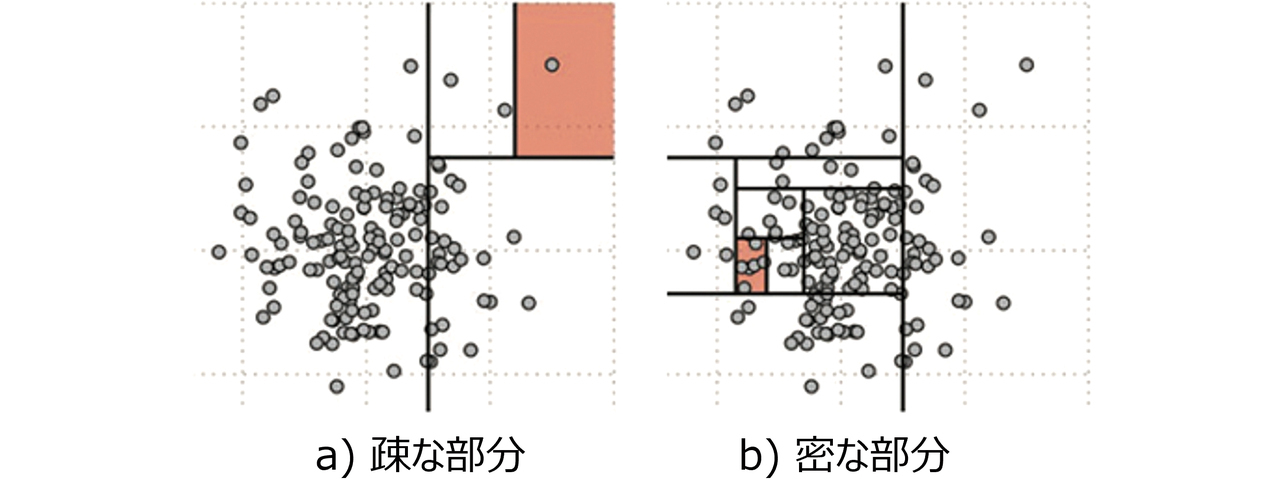
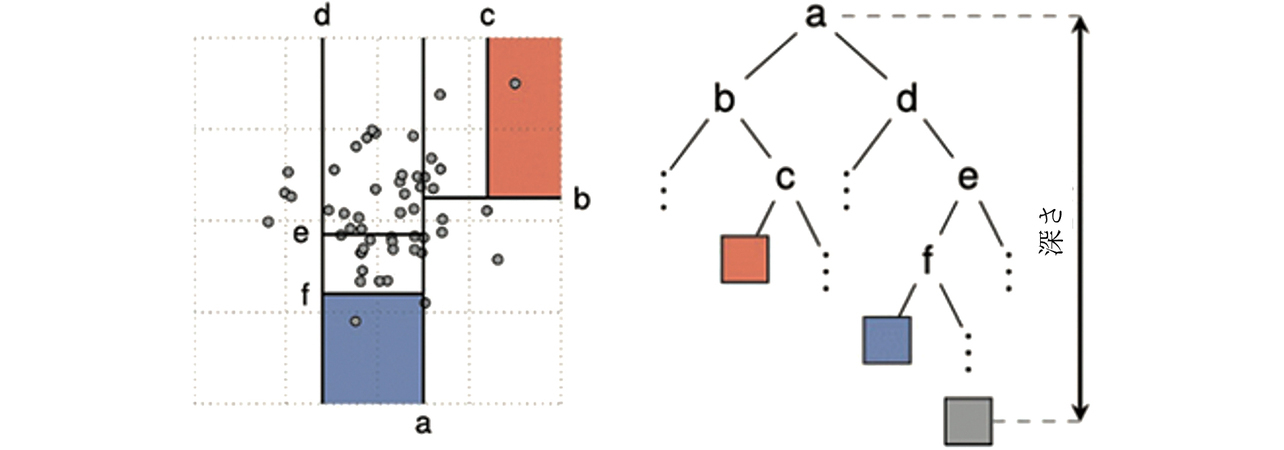
異常度は、サンプリングされた学習データX={x1, x2, x3, ... xn} から2分木を構築し、評価するデータについての深さ情報から式(1)によって算出される。具体的には、以下の操作を行う。
ここで、h(x)は、n点のサンプリングされたデータから構築された2分木において、評価点であるxの深さを表す。例えば256(=28)点のサンプリングデータにおいては、2分木の深さは1から8の値を取りうる。複数の2分木における評価点xの深さの期待値であるE(h(x))を正規化することにより、異常度は(0,1]の範囲をとる。この異常度に対してしきい値を設定することで異常検知を行う。なお、γはオイラー定数(≈0.57721)である。
3.3 影響・要因特定
本節では、製品不良と型式変更の要因となる変数の特定について記す。
3.3.1 製品不良の要因特定
まずは、成形不良に至る要因を特定する。成形機で収集された変数の集合をmeasured dataとして、これらの変数(var1, var2, var3, var4, …)が成型不良に影響している様子を図5に示す。
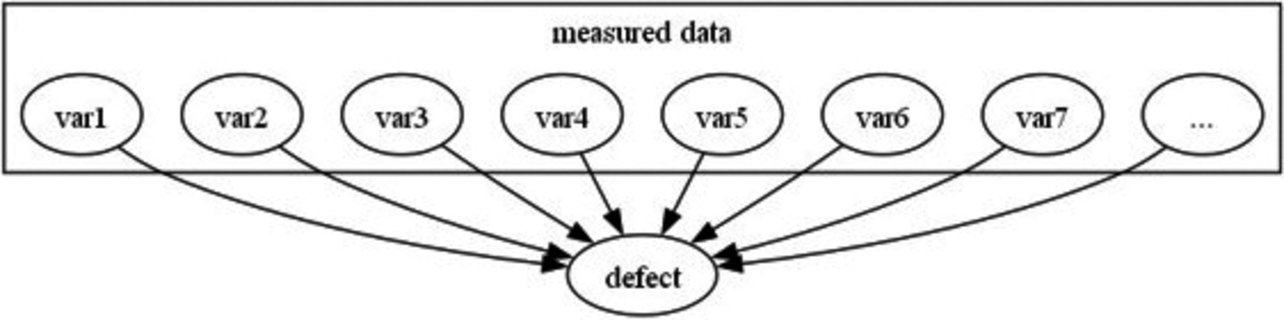
特定された次に成形不良の要因となる変数の集合は式(2)により算出される。
ここで、xは成型機から収集される温度や圧力など変数の集合である。Importancedefect–factorsは製品不良と正常品を離散変数としてラベル付けしたxについてRandom Forestの重要度を算出する。Xdefect–factorsは、前述で算出した重要度について、任意のしきい値Thdefect–factorsで条件付けした変数の集合である。
3.3.2 製品型式変更の影響変数の特定
次に製品型式の変更により、影響を受ける変数を特定する。型式の変更が成型機で収集された変数に影響する様子を図6に示す。
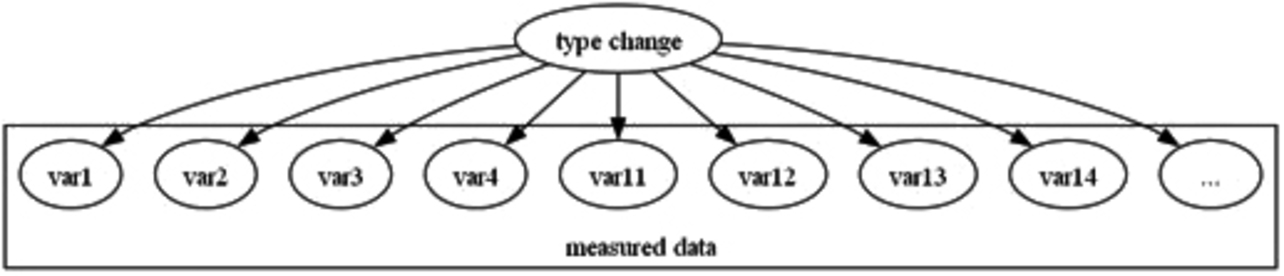
型式変更の影響を受ける変数は、図5に示された成形不良の要因である変数(var1, var2, var3, var4)と、成形不良の要因ではない変数(var11, var12, var13, var14, …)から構成される。
次に型式変更が影響する変数の集合を式(3)により算出する。
型式変更が影響する変数の集合Xtype–factorsは式(2)と同様に型式を離散変数でラベル付けしたxに対する重要度を任意のしきい値で条件づけたものである。
3.4 異常検知モデルの生成
本節では、品質不良と型式変更を検知する異常検知モデルを生成する。図7に示すように、品質不良の予兆を検知するモデル(anomaly model1)は型式変更に影響を受け、不良の要因となる変数の集合から構成される。型式の変更を検知するモデル(anomaly model2)は、型式変更の影響は受けるが、不良の要因とはならない変数の集合から構成される。
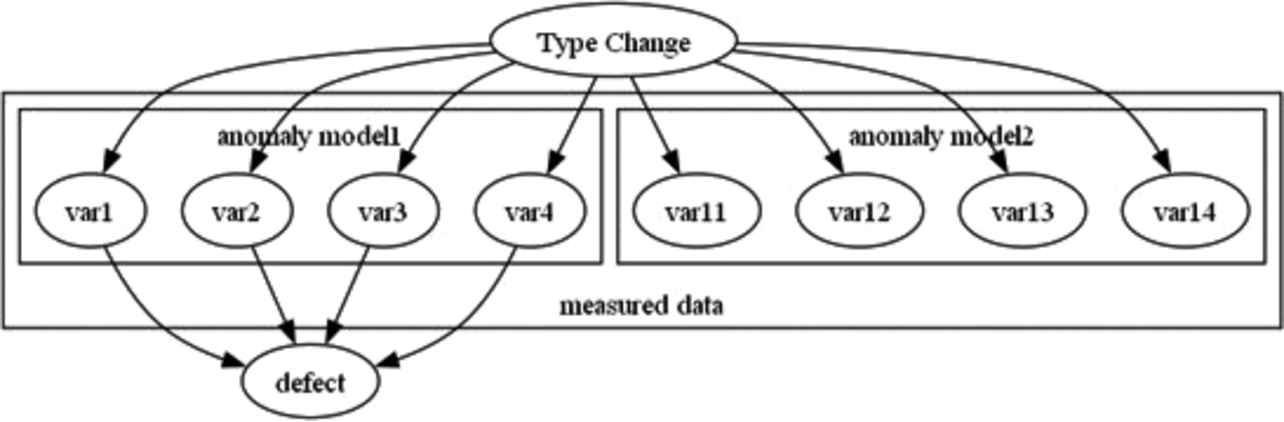
3.4.1 製品不良予兆の異常検知モデル
製品不良の予兆検知を行う異常検知モデルの学習データを式(4)に示す。
このようにXanomaly–model1は、製品不良の要因と製品型式の影響の積集合となる。
次に、本モデルの異常度sanomaly–model1の算出方法を式(5)に記す。
ここで、xanomaly–model1は、学習データXanomaly–model1から構成された異常検知モデルで評価されるデータである。
本モデルは、正常である学習データが異常度を超えない任意の、Thresholdanomaly–model1をしきい値とする。
3.4.2 製品型式変更の異常検知モデル
製品型式変更を検知する異常検知モデルの学習データを式(6)に示す。
このようにXanomaly–model2は、製品不良の要因ではない集合と製品型式が影響する集合の積集合となる。
次に、本モデルの異常度の算出方法sanomaly–model2を式(5)と同様に、式(7)に記す。
xanomaly–model2は、学習データXanomaly–model2から構成された異常検知モデルで評価されるデータである。
本モデルは、正常である学習データが異常度を超えない任意の、Thresholdanomaly–model2をしきい値とする。
3.5 異常度の算出
本節では、成型不良の予兆検知であるanomaly-model1と型式変更の検知を行うanomaly-model2を統合する異常度の算出としきい値について述べる。
式(8)に本手法で提案する複数の異常検知モデルを統合した異常度を示す。
3.2節で示した通り、Isolation Forestの異常度は、評価するデータの深さの期待値を正規化したものである。よって、2つの異常検知モデルにおいて、同じデータxunionを評価した場合、指数法則により、異常度のスコアの乗算の平方根で表すことができる。
統合された異常度であるsunionは、Isolation Forestの異常度と同じ(0,1]の範囲をとるため、成型不良の予兆検知のしきい値は3.3.1節で記した、Thresholdanomaly–model1を使用し、型式変更検知のしきい値はThresholdanomaly–model2を使用する。
4. 検証
本章では、2.1節で示した射出成型機で収集したデータを用いて、提案手法の有効性について検証した結果を述べる。比較する従来手法は、2.2節で示したAI搭載マシンオートメーションコントローラと同様の従来手法を用いた異常検知手法である。
4.1 検証内容
検証したデータの概要を表1に示す。
製品型式 | ショット数 | 収集変数の数 | 異常検知と判定 すべきショット数 |
---|---|---|---|
A | 113 | 70 | 4 |
B | 223 | 70 | 70 |
製造する製品型式は2種類であり、A型式を113ショット製造後に、B型式の製造に移行する。本検証の目的は、A型式で4ショットの予兆検知を判定した後、B型式への変更を検知することである。
なお、本稿においては、機密上の観点から具体的な説明変数の内容は記載しない。
4.2 異常検知モデル
提案手法により生成した異常検知モデルの内容を表2に示す。
異常検知モデル | 異常検知モデルの説明変数 | サンプル数 |
---|---|---|
anomaly model1 | var1, var2, var3, var4 | 40 |
anomaly model2 | var11, var12, var13, var14 | 40 |
3.4節に記載した、anomaly model1とanomaly mode2の2種類の異常検知モデルを生成する。モデル生成のサンプル数は製品型式Aの40ショット分とした。説明変数は3.3節にしたがい、それぞれ4変数を選択する。それぞれの説明変数のヒストグラムを、図8に示す。
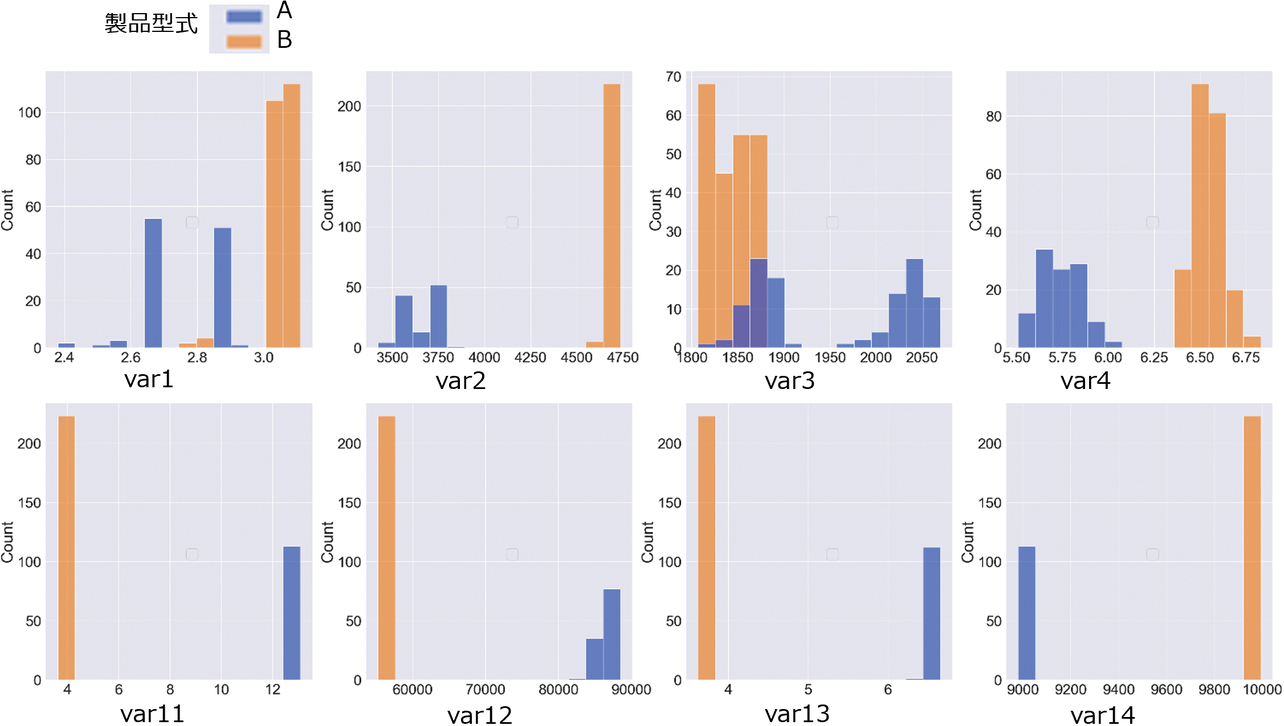
Anomaly model1を構成する変数var1, var2, var3, var4は、特に不良を含む製品型式Aにおいて分布のばらつきが確認される。これらの変数による異常検知で製品不良の予兆検知を行う。一方で、Anomaly model2を構成する変数のvar11, var12, var13, var14は、製品型式毎のばらつきは確認されない。これらの変数による異常検知は製品型式を判定することに適していることが分かる。
4.3 検証結果
3.4.1節と3.4.2節にしたがい、anomaly model1, anomaly model2の異常検知モデルについて、学習した結果の異常度から正常の異常度を超えない値を、それぞれしきい値1、しきい値2として設定した。
表3に、anomaly model1, anomaly model2それぞれのしきい値を記す。
異常検知モデル | しきい値の名称 | しきい値の用途 | しきい値 |
---|---|---|---|
anomaly model1 | しきい値1 | 不良予兆の検知 | 0.550 |
anomaly model2 | しきい値2 | 製品型式変更の検知 | 0.570 |
提案手法での異常度の評価結果を図9に示す。
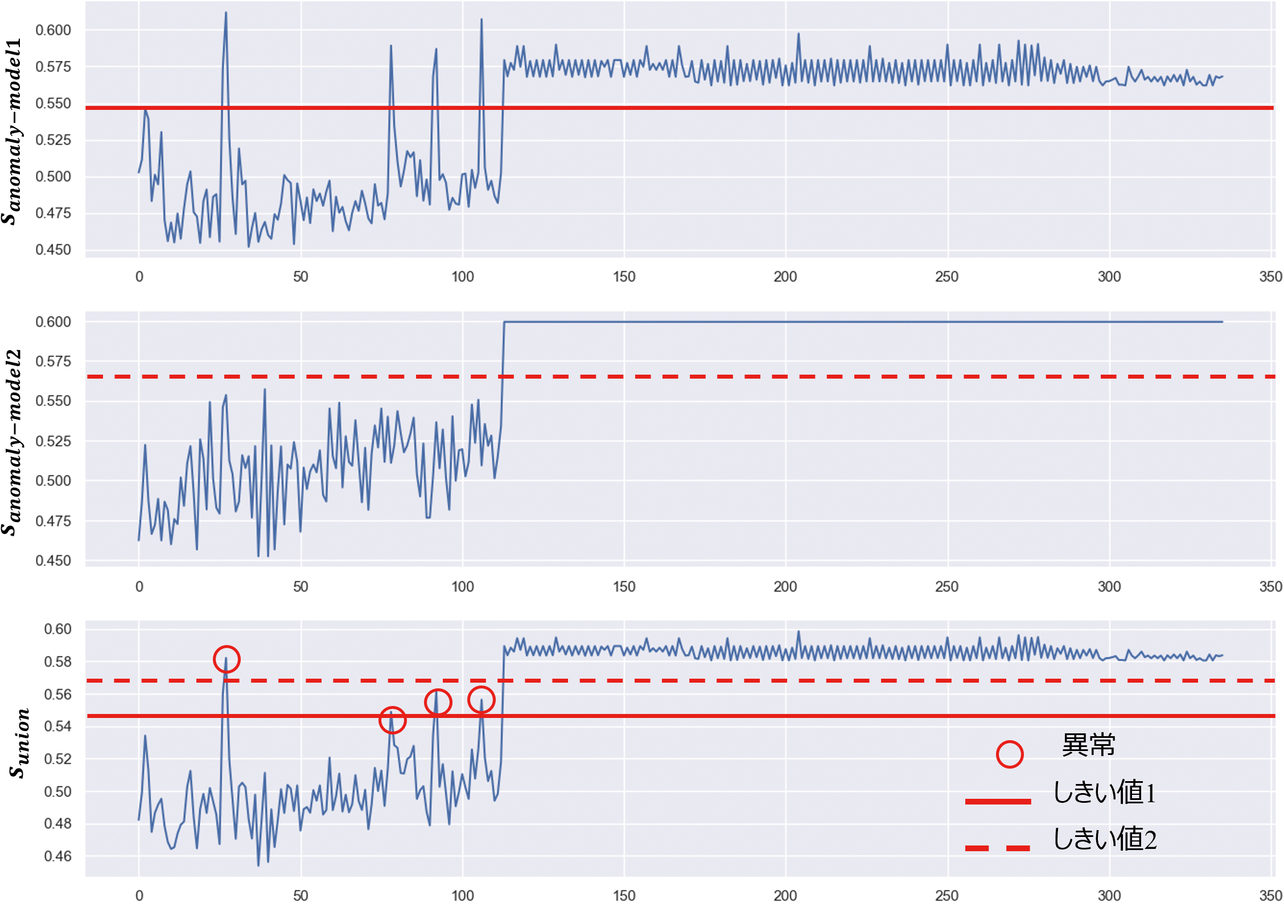
グラフは上から、anomaly model1の異常度sanomaly–model1、anomaly model2の異常度sanomaly–model2、異常検知モデルを統合した異常度sunionである。
1つめのグラフのsanomaly–model1は従来手法である製品不良の要因となる変数で構築された異常検知モデルの結果である。前半の4つの不良は判定できているが、型式変更後はすべての異常度がしきい値を超えているため、不良と判断されることがわかる。
2つめのグラフsanomaly–model2は、製品不良の判定はできていないが、型式変更をすべて検知できていることが分かる。
3つめのグラフのsunionは提案手法での結果となる。製品不良と型式変更について、すべて検知できている。さらに、しきい値1としきい値2により、製品不良と型式変更の違いについては37番目の1ショットを除いて分類することができた。
本検証の評価結果を表4にまとめる。
製品 型式 |
ショット数 | 収集変数の数 | 異常検知と判定 すべきショット数 |
正答率 |
---|---|---|---|---|
A | 113 | 70 | 4(不良予兆) | 99.1% |
B | 223 | 70 | 223(製品型式) | 100% |
製品型式Aの評価データについては、37番目のショットデータについて、製品不良と型式変更の違いを分類できていないため、正答率は99.1%となった。製品型式Bの評価データについては、型式変更をすべて検知できている。
4.4 考察
検証データにおいて、製品型式A, B区間の正答率はそれぞれ99.1%, 100%となった。提案手法で示した異常度については、ほぼ意図通りの振る舞いを確認できたものの、1ショットは正しく検知できない結果となった。
37番目のショットで異常度がしきい値2を超えて型式変更前のショットを型式変更として検知してしまった原因は、異常度の変動範囲が前半と後半で異なることが考えられる。sanomaly–model2を確認すると、前半である型式A区間の異常度は0.45から0.55の範囲で変動しているが、後半である型式B区間の異常度は、ほぼ一定となっている。sanomaly–model1とsanomaly–model2 を統合したsunionについても、前半の型式A区間の異常度の変動が影響して、不良予兆検知の異常度が大きくなり、しきい値2を超えていると考えられる。
これを対策するには、異常度を合成する前に、それぞれの異常度の変動範囲を調整する必要があり、今後の検討事項となる。
改善すべき点があるものの、1つのリアルタイムな異常検知モデルで、製品不良の予兆検知と型式変更検知を両立できるため、2.3節で示した要件を満たすことができる。結果として、2.2節で示した不良率の低減を実現することが可能となる。
異常検知モデルの運用面で考えると、複数の異常度の乗算で統合して評価できることは、管理上容易である。過去のスコアのみを使って新たに評価が出来ることは、多数の異常検知モデルの統合も容易になるため、今後さらなる利用の展開が見込まれる。
5. むすび
本稿では、4M変動によるコンセプトドリフト検知する課題に対して、リアルタイム性を持つこと、スキルレス運用のためにパラメータ調整が不要なことと、製品不良の予兆検知と型式変更の検知を両立することの3点を要件とした。解決手法では、因果関係を考慮して製品不良の要因となる変数群と、それらの変数に影響を与える4M変動の変数群を特定し、それぞれの変数群から生成される複数の異常検知モデルを統合する手法を提案した。検証においては、1つの異常検知モデルで、1ショットを除いて、製品不良と型式変更を意図通りに分類して検知できることを確認した。本稿では1事例のみの評価となったが、今後は提案手法を改善し、事例を積み上げることで、多くの製造現場での不良率低減が見込まれる。
製造現場では、機械学習の運用が難しいことが課題となっており、今後の機械学習運用を広げていくうえで有用な手法になり得ると考える。本手法は異常度のみで演算可能なことから、過去の異常度を用いての新たな評価や多数の異常検知モデルの統合など、用途を拡大できる可能性を見出した。
今後は本手法を改善して実際の製造現場に適用し、詳細な評価を実施する。将来的には、大規模なデータで評価を行い、汎用性を高めていくことと、3つ以上の異常検知モデルを組み合わせることで、多数の異常検知モデルの管理を効率化するソリューションへと展開していく。
参考文献
- 1)
- オムロン株式会社. “AI搭載マシンオートメーションコントローラ.” https://www.fa.omron.co.jp/product/special/sysmac/featured-products/ai-controller.html(Accessed: Mar. 14, 2024).
- 2)
- 大川佳寛, 小林健一, “ラベルなし運用データに対するコンセプトドリフト適応技術に関するサーベイ,” 2021年度人工知能学会全国大会(第35回), 2021, 2G4GS2f03.
- 3)
- 杉山昭, 宮田陽一, 現場で役立つ射出成形の基本と仕組み, 秀和システム, 2014, p. 15.
- 4)
- 杉原哲郎, “製造現場の突発的な変動の影響を受けたデータにおける異常検知の改善,” OMRON TECHNICS, vol. 56, no. 1, pp. 48-57, 2024.
- 5)
- 鶴田浩輔 他, “マシンコントローラに搭載可能なAI技術の開発(1)装置制御用データを利用した生産ラインの異常検知手法について,” OMRON TECHNICS, vol. 50, no. 1, pp. 6-11, 2018.
- 6)
- 阿部泰明 他, “マシンコントローラに搭載可能なAI技術の開発(2)異常検知コントローラプロトモデル開発における実証例について,” OMRON TECHNICS, vol. 50, no. 1, pp. 12-17, 2018.
- 7)
- F. T. Liu et al., “Isolation-based anomaly detection,” ACM Trans. Knowl. Discovery Data(TKDD), vol. 6, no. 1, p. 3, 2012.
本文に掲載の商品の名称は、各社が商標としている場合があります。