脱炭素社会に貢献するFA用大容量電源の開発
- 電源
- 大容量
- 配線の焼損回避
- 高効率
- カーボンニュートラル
カーボンニュートラル・脱炭素社会への取り組みと並行し、労働人口の減少やサテライト工場の推進から、製造業の自動化が加速している。このため、製造現場の電動機器やセーフティー機器、IoT機器は増加傾向であり、エネルギー消費量増加と装置や制御盤の占有スペース増大が問題となっている。これら問題解決のために電源機器へは、“より小型でより大容量・高効率”であって、故障もしにくい(装置のエネルギー生産性に貢献する)といった進化が求められている。
今回、大容量電源に一次直列二次並列型LLCコンバータを適用することにより、2 kW電源(形S8VK-WA20224)において95.4%の効率を達成、従来の1.5 kW電源の効率88.7%より大幅に向上させた。更に磁気と熱を併用したシミュレーションによって最適な放熱構造を実現し、自然空冷とすることで故障率を低減させている。また、電源を搭載した装置や制御盤の小型化にも着目し、配線電流を電源側で制限する技術を用いることで、使用する配線の線径を小さくし、制御盤のサイズを10%減らすことができた。
今回の技術は、2 kWを超える大容量電源にも適用可能であり、さらなる脱炭素社会実現への貢献が期待される。
1. まえがき
2050 年のカーボンニュートラル実現に向け、脱炭素社会への取り組みが進行している。更には、労働人口の減少やサテライト工場の推進から、製造業の自動化は近年加速している。自動化に伴い電動機器やセーフティー機器、IoT機器などは増加し、使用する電源の容量は大きくなる。しかもコスト低減と環境負荷減少のために、それらによる装置や制御盤の大型化を抑制することが求められている。こういった要求に答えるためには、“より小型でかつ大容量・高効率(低損失)な電源”が必要となる。なお、小型化は、製品の原材料の削減や製品の輸送に伴う温室効果ガス(GHG)低減効果についても期待されている。
従来の技術では大容量の電源は内部の発熱が大きく、強制空冷が必須であるが、強制空冷はファンの寿命や粉塵などの異物の侵入などの観点から自然空冷よりも故障率が高い。より高頻度で装置が停止することになるため、生産性が低下し、装置の待機電力が増え、エネルギー生産性を低下させてしまう。つまりGHG排出量を増加させるという問題がある。
本稿ではこれらの問題に対応できる、制御盤の小型化に貢献しGHGを低減できる大容量電源を実現する技術について説明する。
2. 技術課題
2.1 複数素子の並列接続における電流の均一化
現在100 W~1 kW程度の小~中容量電源では、一次側 MOSFET のゼロ電圧スイッチングと二次側ダイオードのゼロ電流スイッチングによる高効率が達成できるという理由により、ハーフブリッジ型LLCコンバータ(以下LLCコンバータ)が広く採用されている。ただし1 kWを超える大容量電源においてLLCコンバータを採用した場合、パワーデバイスやトランスに共振回路特有の大電流ストレスがかかる。以降で詳細を説明する。
図1にLLCコンバータと従来大容量電源に採用されていたフルブリッジコンバータの二次側のトランスに流れる電流波形を比較したものを示す。LLCコンバータの場合、二次側には正弦波に近い電流が流れるため、フルブリッジコンバータと比較して、ピーク電流、また実効電流が増加しており、従来よりも大電流ストレスがかかることが分かる。
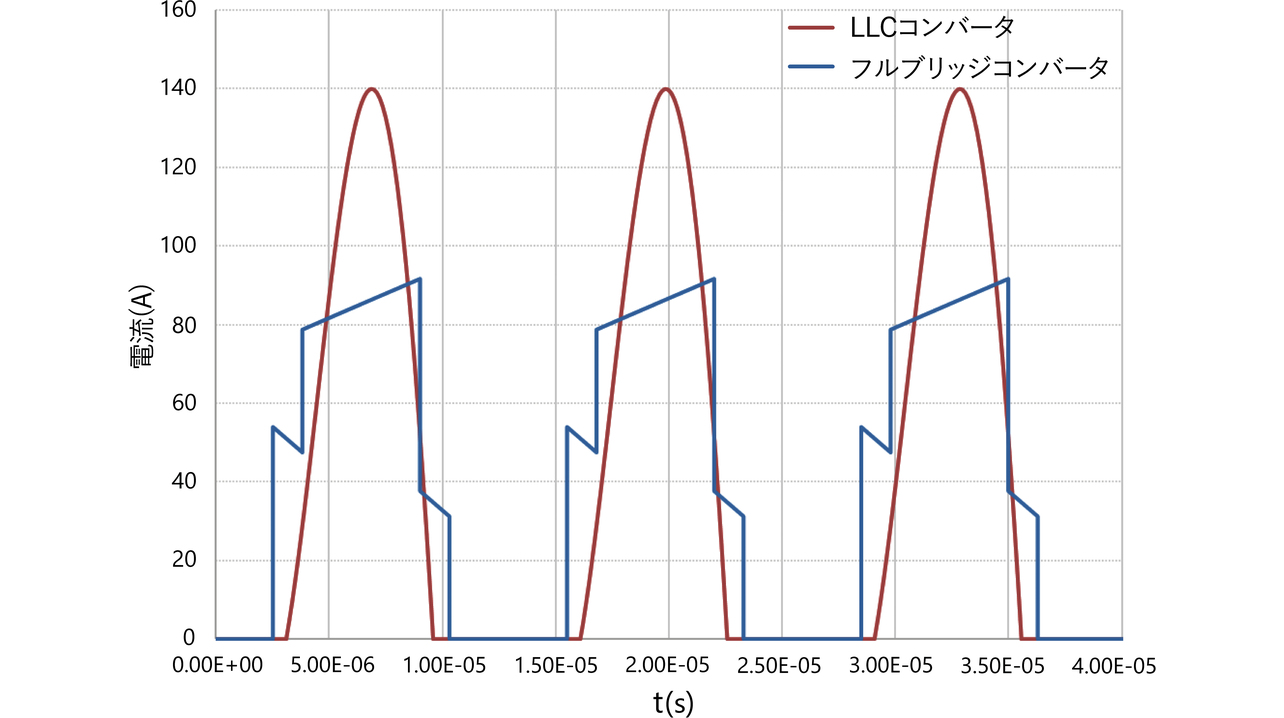
また図2は各電力容量でトランス二次側巻線に流れる実効電流の二乗をLLCコンバータとフルブリッジコンバータで比較したものである。半導体やトランス巻き線などの抵抗分損失は実効電流の2乗に比例しており、抵抗成分が一定の場合、容量が大きくなるほど従来よりも損失が増加するということになる。
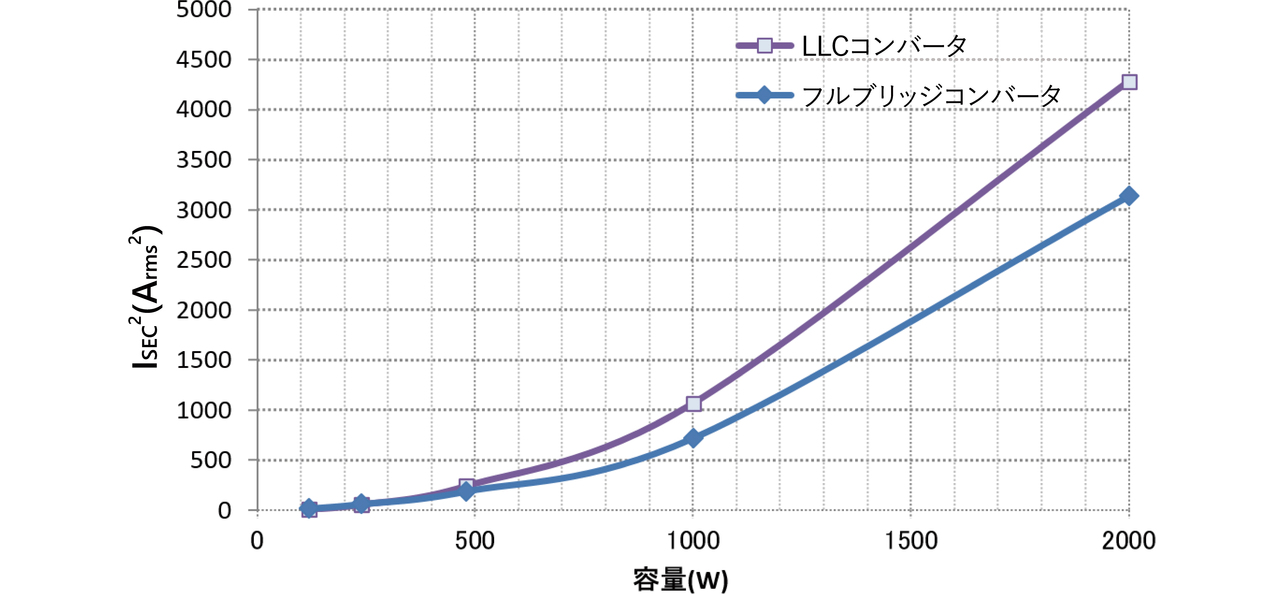
大電流ストレスを回避するためには図3のようにデバイスを並列に接続する方法がある。
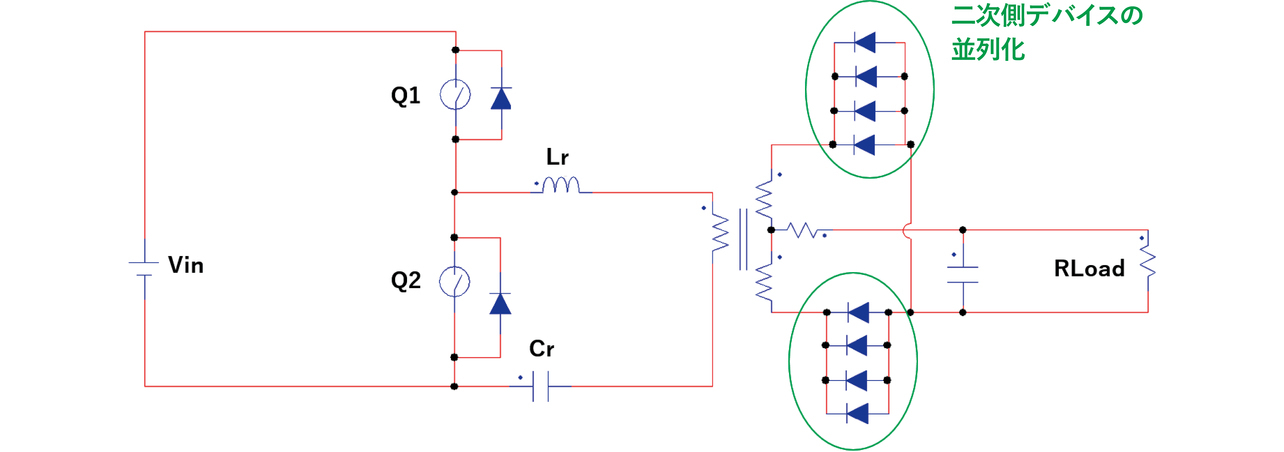
しかしデバイス毎の電流バランスは保証されず一つのデバイスに電流が偏った場合、効率の低下や信頼性低下を招く。この問題を解決するためには、大電流を複数素子に分散させ、かつ各素子に流れる電流を均一にすることが課題となる。
2.2 自然空冷と小型化の両立
1 kWを超える大容量の電源は強制空冷の採用が一般的になっているが、FANの寿命や粉塵などの異物の侵入により、電源が停止することでエネルギー生産性を低下させるという問題がある。そのため、自然空冷の電源のニーズが高まっている。
大容量電源において小型化と自然空冷を両立させるには、発熱部を冷やす最適な放熱構造が必要になり、試作機を用いた試行錯誤により決定していた。しかし図4(2 kW電源の断面図を3Dデータで示したもの)のように大容量では部品点数も多く、構造が複雑なため、試作機を複数種作製するなど開発と検証の期間が莫大となる。そのため熱シミュレーションを活用し、放熱構造を効率的に検討する。
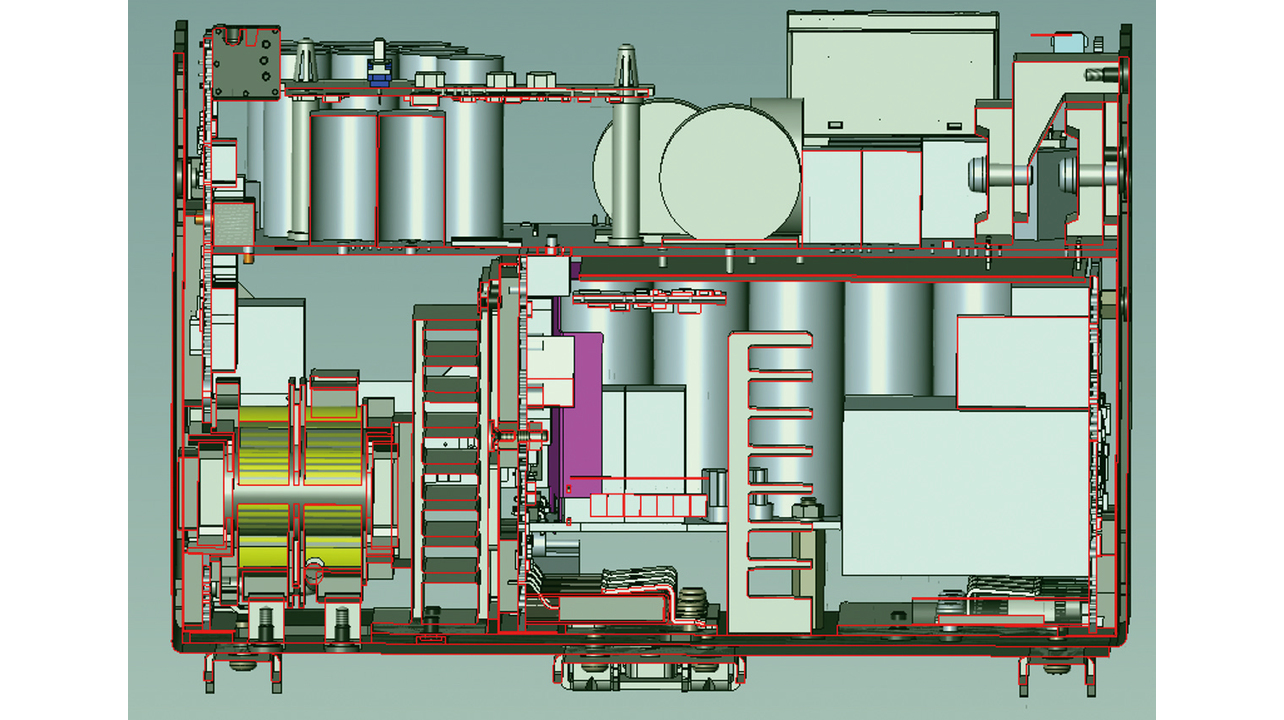
熱シミュレーションでは発熱部品の損失を正しく入力することで精度が高い結果が得られるが、特に発熱の大きいトランスなどの大型磁性部品は損失計算が難しく、熱シミュレーションに必要な精度が確保できないという問題があった。
大型磁性部品の損失において巻き線に電流が流れることによる損失(銅損)を計算する場合、PC =R ×I 2で計算するが、このR、つまり巻き線の抵抗値は近接効果や表皮効果などの影響を受け変動する。また図5のようにコアの中央ギャップからの漏れ磁束が巻き線を通過する。これにより巻き線に渦電流が流れ発生する渦電流損などもあり、計算と一致しない。損失を実機で確認することも考えられるが、上述の現象は部品の内部で発生するため、電流波形などをとらえることができず、トランスの損失を実測することは困難である。
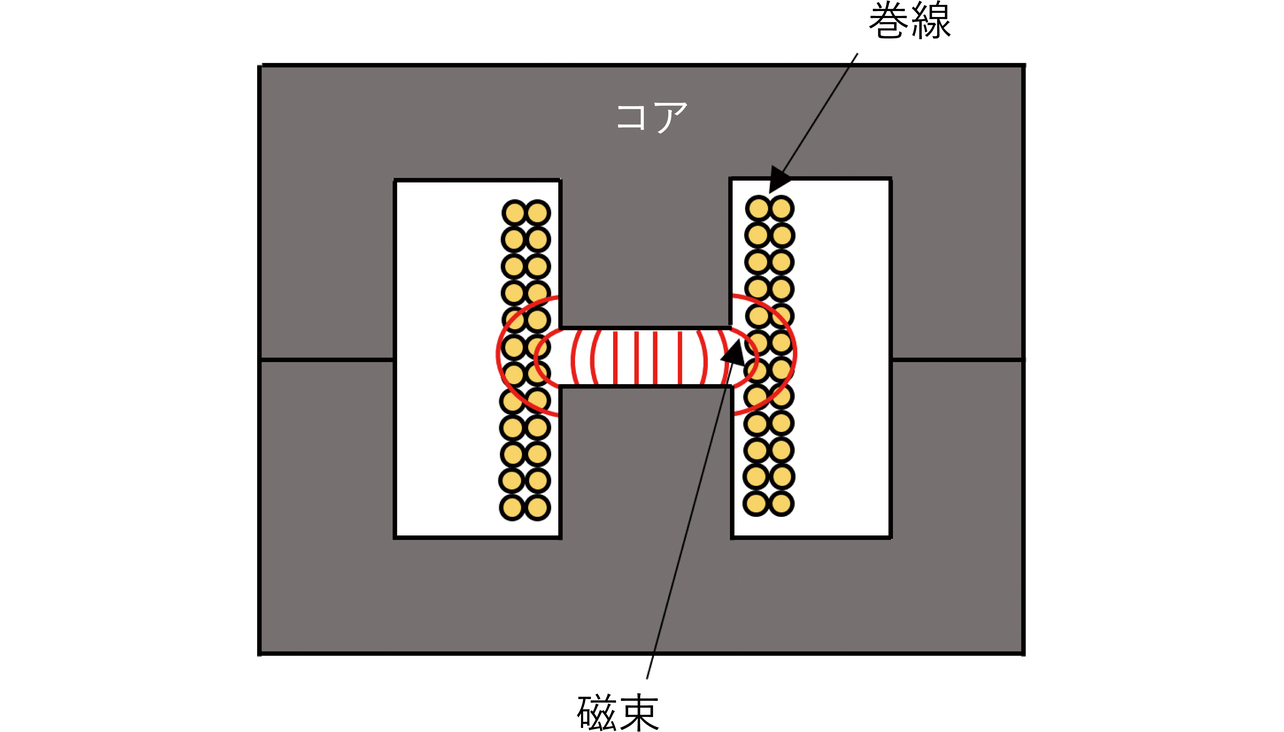
熱シミュレーションで多くのパターンの試行錯誤を短時間で検討し最適な放熱構造を見つけることにより小型・自然空冷の両立を実現するためには、磁気シミュレーションを活用して大型磁性部品の損失を正確に見積もることが課題となる。
2.3 使用線径の制限緩和
2 kWクラスの電源は出力が大電流になり、配線に線径の大きい線を使う必要が出てくる。線径の大きい線は曲げRが大きくなるので制御盤のサイズに影響する。配線を制御盤の上のダクトに入れるなどの目的で曲げる場合、およその曲げRは次式で見積れる。
図6に示す通り、例えば85 A(出力容量2 kW、電圧24 Vの場合に流れる電流)を流すためにはAWG2相当の線が必要になり、制御盤の奥行方向が181 mm必要となってしまう。そこで、曲げRを減らすためには線径の小さい線で複数配線することが考えられる。85 Aを2本の配線で流す場合、AWG6を使うことになり、制御盤の奥行方向は164.5 mmとすることができ、AWG2を使った場合に比べ10%制御盤の体積を削減できる。
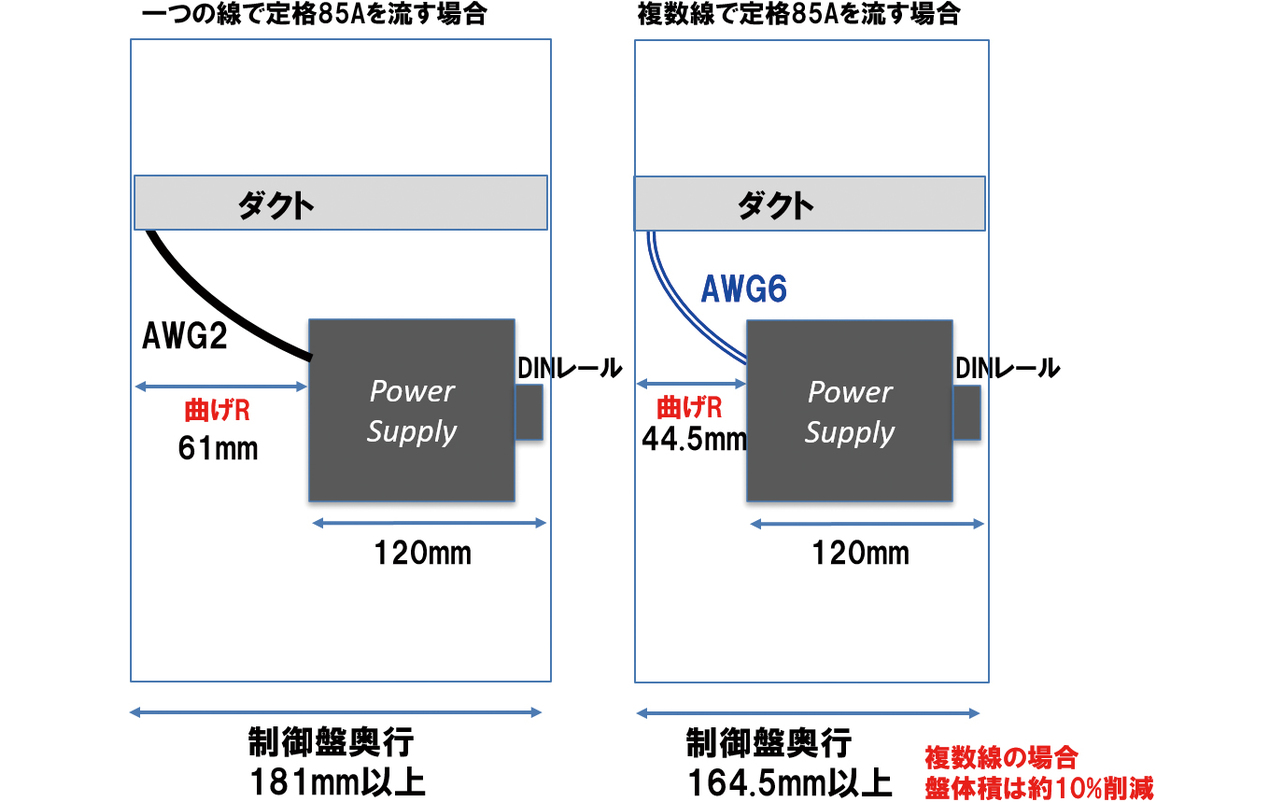
ただし、図7に示す通り、異常時に対する安全設計として、断線時の電流集中や短絡電流を考慮して使用線径を決定する必要があるため、線径が大きい線を採用せざるを得ないという問題がある。
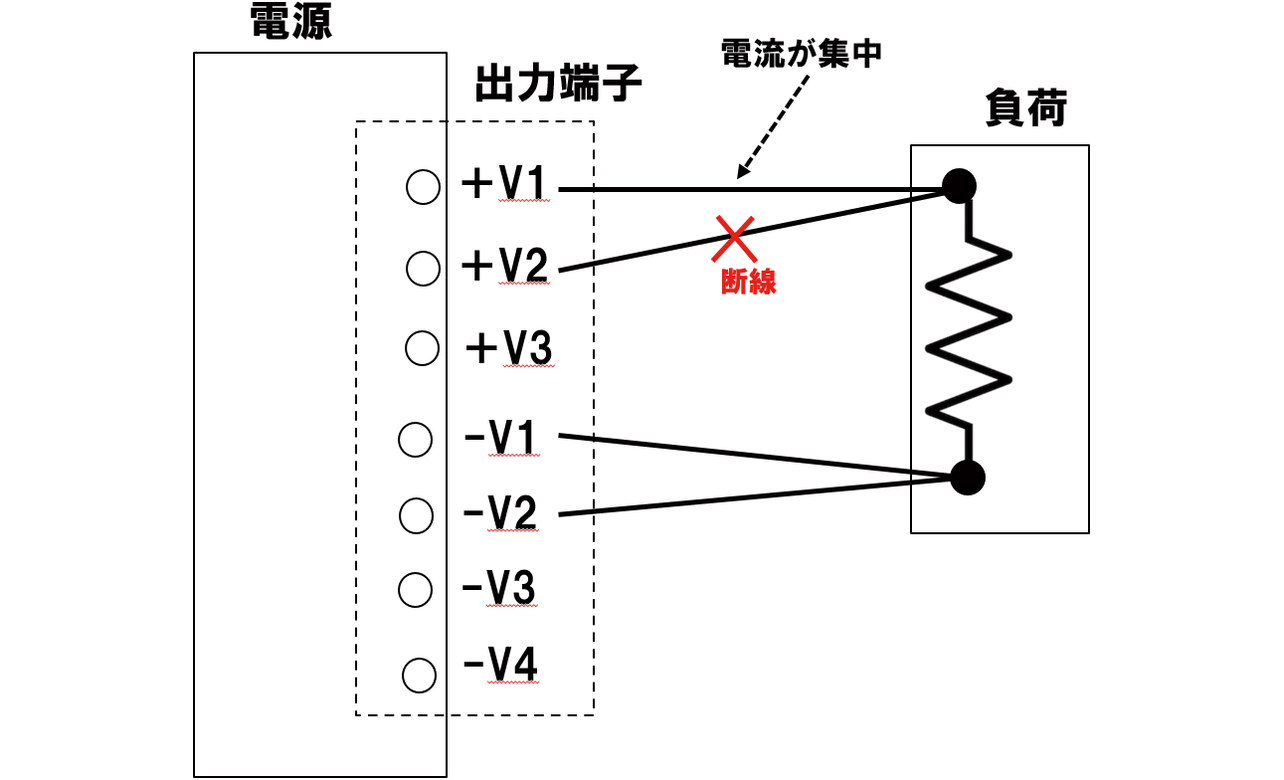
こういった問題に対応するために、異常時でも配線焼損等の事故が起きないように電流制限する技術が課題となる。
3. 解決する技術
3.1 電流バランス技術
3.1.1 高効率回路で電流分散をさせる回路方式
2.1節の課題を解決し小型高効率を実現するためには、トランスやパワーデバイスを複数に分けて電流分散しつつ、各素子に流れる電流を均一にする技術が必要となる。一次側MOSFETのゼロ電圧スイッチングによる低損失を維持しつつ、電流を分散させることでトランスや半導体素子に流れる電流を減らす方策について、その代表的なものを比較して表1に示す。
回路方式 | 長所 | 短所 |
---|---|---|
・フルブリッジ型LLCコンバータ | ・トランス一次側の電流はLLCコンバータの1/2。 | ・トランスの一次側巻き数はLLCコンバータの2倍必要。 ・トランス二次側にはLLCコンバータ同様の電流が流れるため、大容量で使用の場合の電流ストレスの問題が二次側素子(トランス二次側巻き線、半導体)において残る。 |
・LLCコンバータ並列化 ・3相インタリーブLLCコンバータ |
・電流を複数素子に分散させることができるのでトランス、デバイスへの大電流ストレスを軽減でき、高効率化が可能。 ・インタリーブ方式の場合、二次側のリプル電流を小さくでき、出力電解コンの数を減らせる。 |
・各相トランスや共振Cにバラツキが発生した場合に電流バランスが崩れる。電流バランスを良くするためには複雑な回路の追加が必要となる。 |
・一次直列二次並列型LLCコンバータ | ・電流を複数素子に分散させることができるのでトランス、デバイスへの大電流ストレスを軽減でき、高効率化が可能。 ・部品バラツキがあっても各トランスの電流バランスが良好。 |
・インタリーブLLCコンバータと比較すると出力平滑Cのリプル電流を小さくできないため、LLCコンバータ同様の出力電解コンの数が必要。 |
今回大容量2 kWの設計にあたり、フルブリッジ型LLCコンバータでは二次側の電流ストレスに課題が残る。またLLCコンバータの並列化やインタリーブLLCコンバータの場合、電流ストレスの軽減はできるものの、各相の共振コンデンサがばらついた際の電流バランスが課題となり追加のアクティブカレントシェア回路などが必要となる1)。よって、これら二つの方式は今回の大容量電源で効率・信頼性を確保するのに適さない。
その他の方法として、LLCコンバータに使用するトランスを複数に分け、これらの結線について、一次側を直列、二次側を並列に接続する方法がある2)。一次巻き線や二次巻き線を直列または並列に接続した構成のトランスはMatrix Transformerとして知られているが、本稿では、本構成を“一次直列二次並列型LLCコンバータ”と記載している。一次直列二次並列型LLCコンバータでは一次側のトランス巻き線が直列であるため、各トランスの二次側巻き線に流れる電流バランスが良好となる3)。大電流を複数素子に分散させた回路で部品バラツキがある場合でも、各素子に流れる電流を均一にできる利点が大きいことから、今回の大容量電源を開発するにあたって、この方式を採用する。
ここで、設計の際に重要となるのは以下二点となる。一次直列二次並列型LLCコンバータのこれらの点は今回参考にした文献では述べられておらず、本稿で明確にする。
一つ目は周波数―ゲイン特性および共振周波数の算出である。
周波数―ゲイン特性は効率や出力電圧の可変範囲に大きく関わる。図8はLLCコンバータでの周波数―ゲイン特性の一例を示している。ただし、LLCコンバータではスイッチング周波数を変化させることで出力電圧を制御していることから、縦軸はゲインではなく、出力電圧Vo (Vo=1/2×入力電圧×ゲイン)に変換してある。
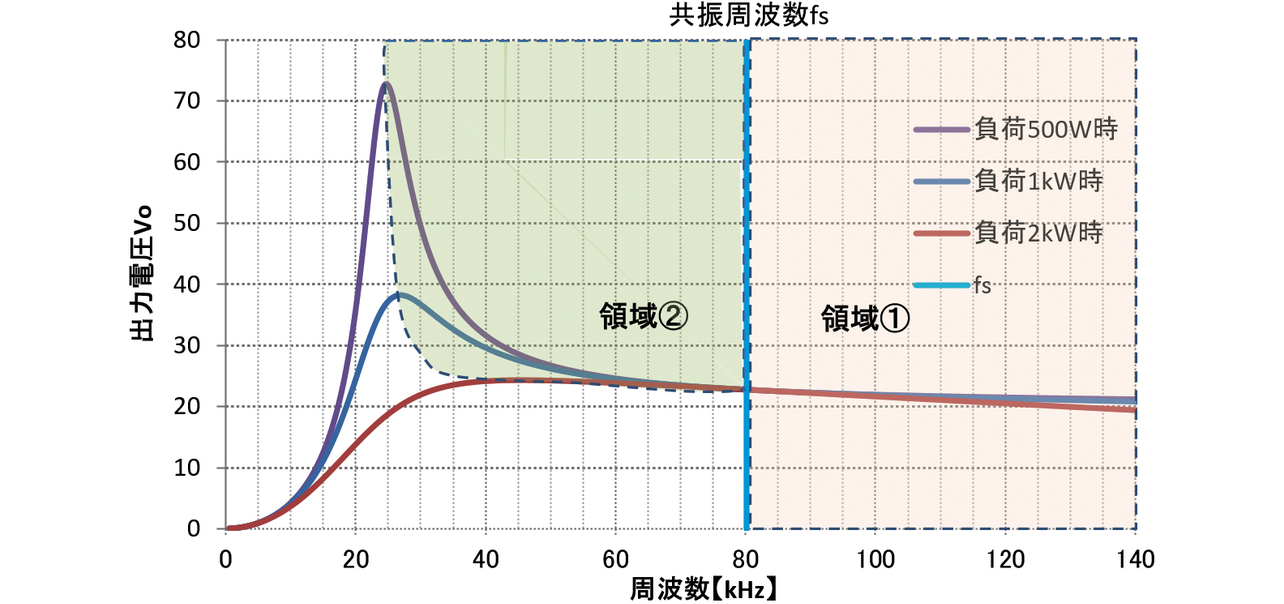
また図に縦線で示すのは共振周波数(fs)であり、この周波数より高い周波数で動作させるか低い周波数で動作させるかにより、LLCコンバータの動作モードが変化する。領域①で動作させる場合、一次側MOSFETのスイッチング損失が増加し、電源の効率に影響を及ぼす4)。またスイッチング周波数を大きく変動させても出力電圧の変化量が小さいため、出力電圧を可変させる電源において、商品仕様を満足できなくなる場合がある。
領域②で動作させる場合は、周波数が低いほど一次側電流が大きくなることにより、導通損失が増加する4)。
これらの要件を考慮するため、一次直列二次並列型LLCコンバータにおける周波数-ゲイン特性、および共振周波数を算出する。
二つ目は電流バランスに対する各部品のバラツキの影響確認である。
一次直列二次並列型LLCコンバータでは、トランスを複数使い、素子に流れる電流を分散する。それらトランスの各パラメータにバラツキがあった場合に、この電流バランスへ与える影響の大きさを確認する必要がある。その上で、各素子に流れる電流バランスについて、5%程度を狙うためのトランスの各パラメータの許容範囲を求め、最適なトランスをカスタマイズ設計する。ここで5%は電源回路の電流バランスを設計する際の当社の設計基準である。
3.1.2 一次直列二次並列型LLCコンバータの周波数―ゲイン特性
一次直列二次並列型LLCコンバータを検討するにあたり、基本波近似法(FHA)を用いて周波数―ゲイン特性についての関係式ゲインM、共振周波数fsを導出する。
図9はこの方式の回路図となる。T1, T2はトランスである。
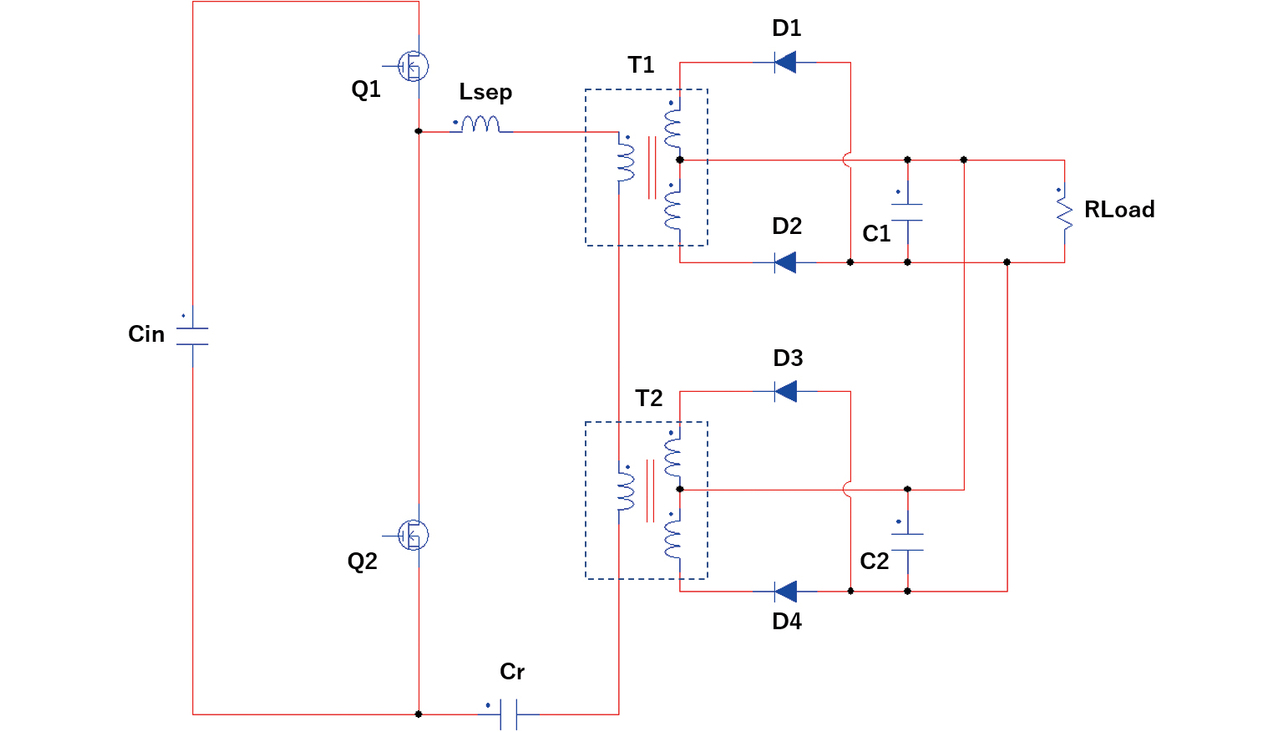
次にFHAでゲインを計算するために図9を変換した等価回路を図10に示す。
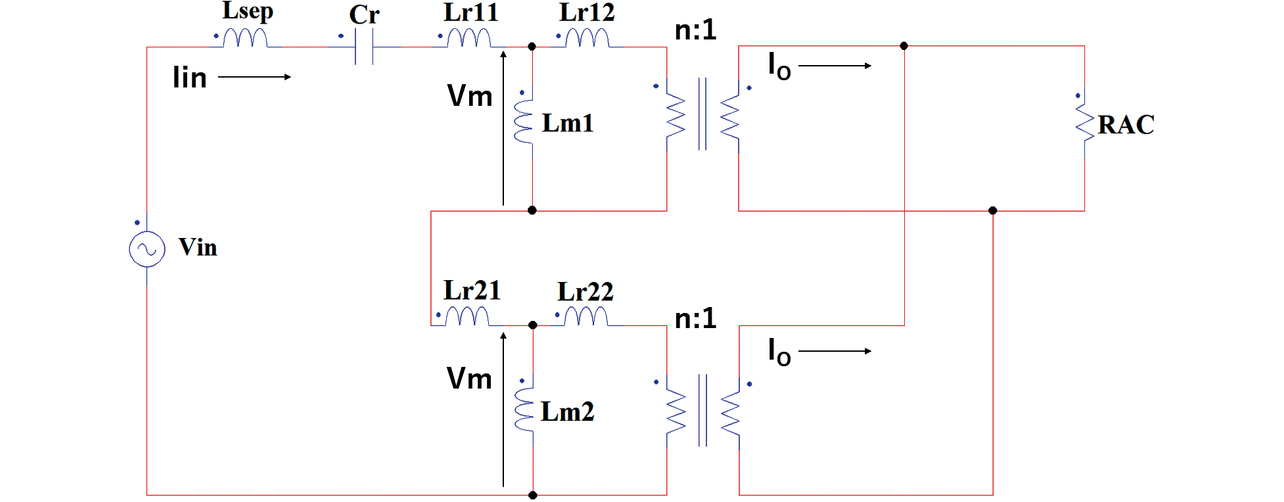
ここで図の各記号はそれぞれ以下を表している。
- Lr11, Lr21:トランスT1,T2の一次側漏れインダクタンス
- Lr12, Lr22:トランスT1,T2の二次側漏れインダクタンス
- Lm1, Lm2:トランスT1,T2の励磁インダクタンス
- Cr:共振コンデンサ
- Lsep:共振用インダクタンス
またRACは以下式により出力負荷抵抗RLOADを交流出力抵抗に変換したものである。
この等価回路においてゲインMを計算する。簡易化のため各パラメータは以下のようにした。
RAC発生電圧をVoとし、M=Vo/Vinを算出する。
等価回路より以下の回路方程式が得られる。
上式より、ゲインMを算出すると、
と得られる。ただし
であり、共振周波数fsは以下となる。
図9においてCinに印加されている直流電圧をVinDCとすると出力電圧Voは導出したゲインMを使い、以下式で表される。
解析結果の妥当性を検証するために、シミュレーション結果との比較を図11に示す。回路シミュレーションにはSCALE(株式会社スマートエナジー研究所)を使用した。図11より、解析とシミュレーション結果は概ね一致しており、一次直列二次並列型LLCコンバータの設計には十分な精度を有していることがわかる。
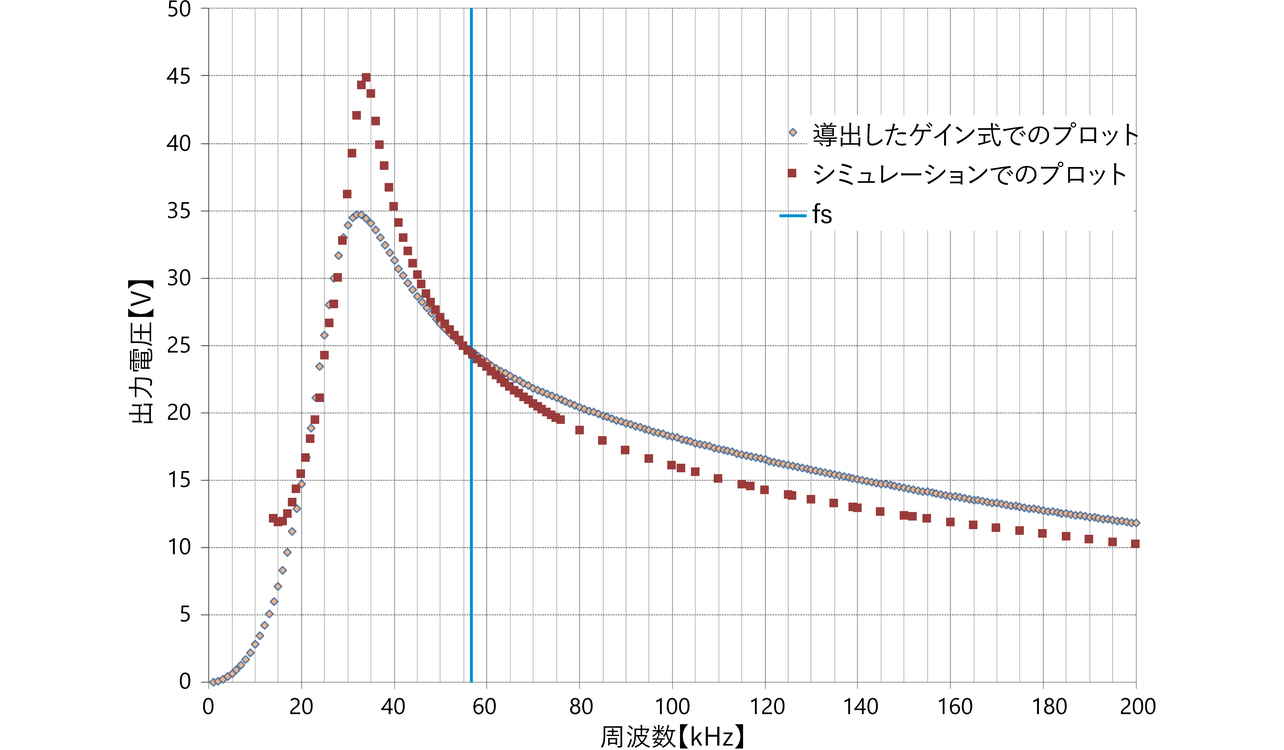
今回、以下のパラメータを利用し確認した。
VinDC=390 V, Lsep=1 uH, Lm=39.7 uH, Cr=376 nF, RLOAD=282 mΩ
3.1.3 電流バランスの検証
一次直列二次並列型LLCコンバータにおいて、共振インダクタを外付けにするかトランスの内蔵漏れインダクタンスを使用するかが重要になるが、製品のサイズを考慮し、今回はトランス内蔵漏れインダクタンスを共振インダクタとした。その際、電流バランスを確保するにはインダクタンス、およびトランス内蔵漏れインダクタンスの許容差が重要になるため、その許容差を求める。
実際にトランスパラメータのLp(一次側インダクタンス)とLLK(トランス内蔵漏れインダクタンス)のバラツキが、電流バランスに与える影響を検証した。ここでLp, LLKのLr, Lmとの関係は以下になっている。
Lp=33 uH(Typ), LLK=7.2 uH(Typ)として図12の回路シミュレーションにてバラツキを与えた場合の実効電流を確認した。図12に示すRsense1, Rsense2の実効電流波形を取得し、その実効電流を表2にて比較している。
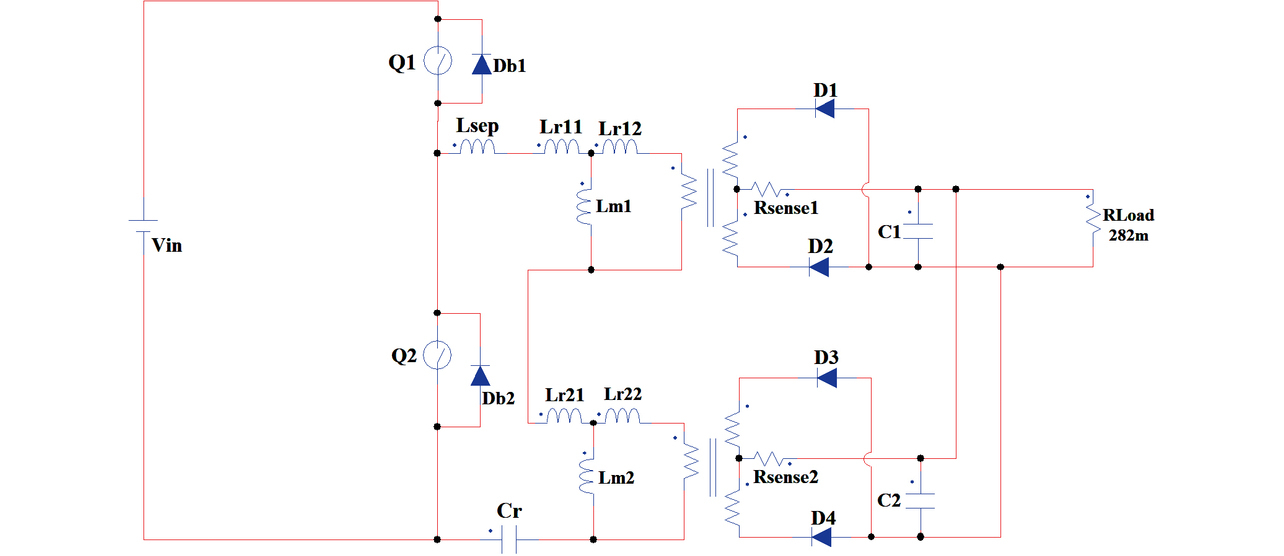
トランス | 項目 | ケースA パラメータ同じ |
ケースB1 Lp±10% LLK±10% |
ケースB2 Lp±20% LLK±20% |
ケースC1 Lp∓10% LLK±10% |
ケースC2 Lp∓20% LLK±20% |
---|---|---|---|---|---|---|
トランス① | Lp | TYP | +10% | +20% | -10% | -20% |
LLK | TYP | +10% | +20% | +10% | +20% | |
I(Rsense1) | 47.6 Arms | 48.29 Arms | 49.92 Arms | 44.74 Arms | 42.09 Arms | |
バランス時(ケースA)に対しての実効電流の増加率 | / | 1.45% | 4.87% | -6.01% | -11.58% | |
トランス② | Lp | TYP | -10% | -20% | +10% | +20% |
LLK | TYP | -10% | -20% | -10% | -20% | |
I(Rsense2) | 47.6 Arms | 46.31 Arms | 44.94 Arms | 50.19 Arms | 54.8 Arms | |
バランス時(ケースA)に対しての実効電流の増加率 | / | -2.71% | -5.59% | 5.44% | 15.13% |
表2において、ケースAはバラツキがない場合のRsense1, Rsense2の実効電流、ケースB1, B2やC1, C2はバラツキがあった場合の実効電流となっている。それぞれ±10%変動させたときはケースC1、±20%変動させたときはケースC2の電流バランスが最も崩れる条件であった。
検討結果より、トランスのLp, Lrはそれぞれ±20%のずれがあると実際にトランスに流れる電流は+15%も増加し、許容することができないが、±10%以下で管理することができれば実際にトランスに流れる電流は増加しても+5.5%程度で収まり、問題ないレベルにできることが分かった。
以上により、電流バランスの要件を満たすためのLp, LLKの許容差要件が分かった。
実際にシミュレーションの確からしさを確認する目的で、表3のバラツキのあるトランスを準備し、実機にて電流波形を取得したものを図13、今回の実験と同様の条件でシミュレーションしたものを図14に示す。絶対値にずれはあるものの二つのトランスに流れる電流の差などはシミュレーションと実機で一致していることが分かり、上記のシミュレーションでの検討が妥当であるといえる。
トランス | 項目 | バラツキ |
---|---|---|
トランス① | Lp | -8% |
LLK | +5% | |
トランス② | Lp | +7% |
LLK | -7% |
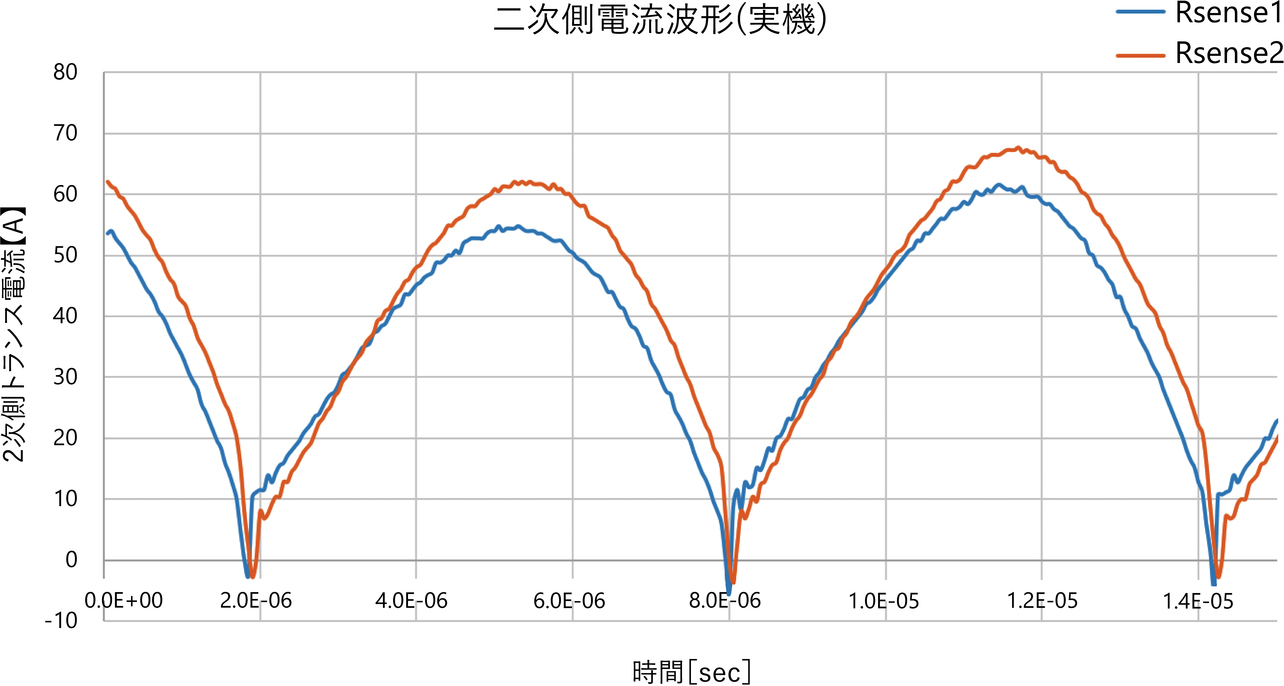
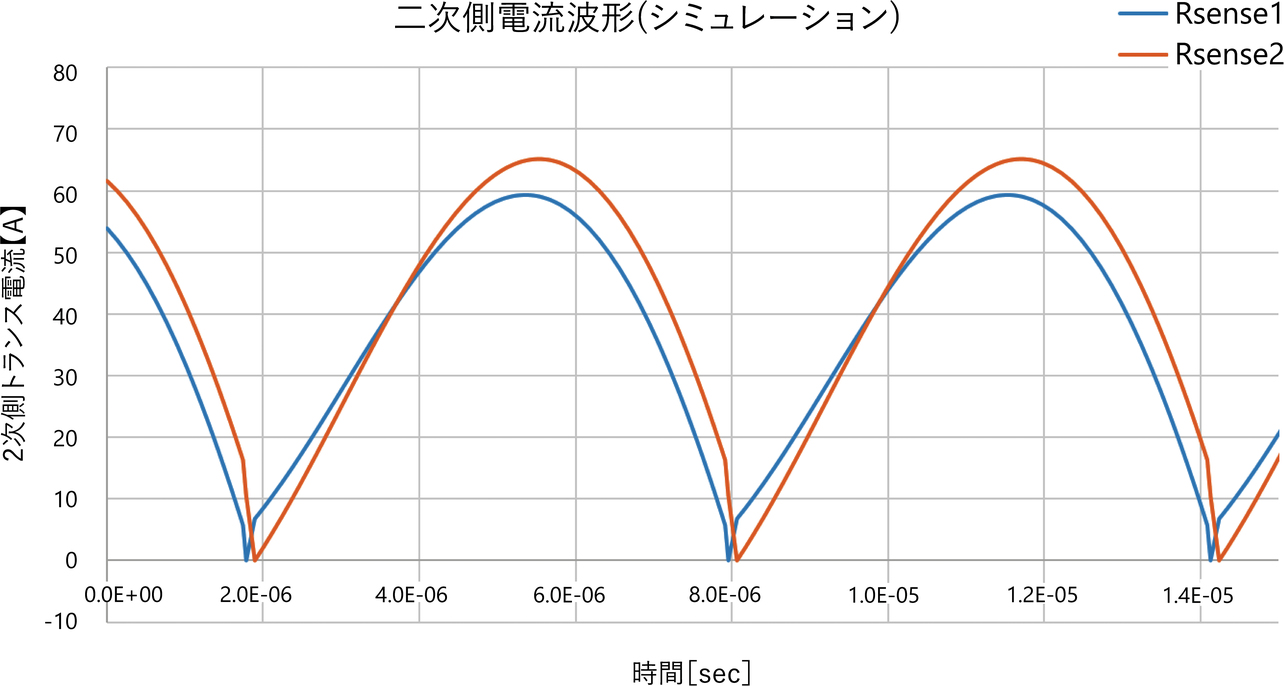
3.1.4 一次直列二次並列型LLCコンバータによる損失改善効果の確認
高効率回路方式の採用、電流経路分散させ、トランス、半導体の電流ストレスを軽減させたことにより、DCDCコンバータ部の効率が上昇し、製品としての効率は図15に示すように95.4%を達成することができた。これは、当社の従来の大容量機種1500 Wの効率が88.7%であったことに対し、大きく上昇させることができている。
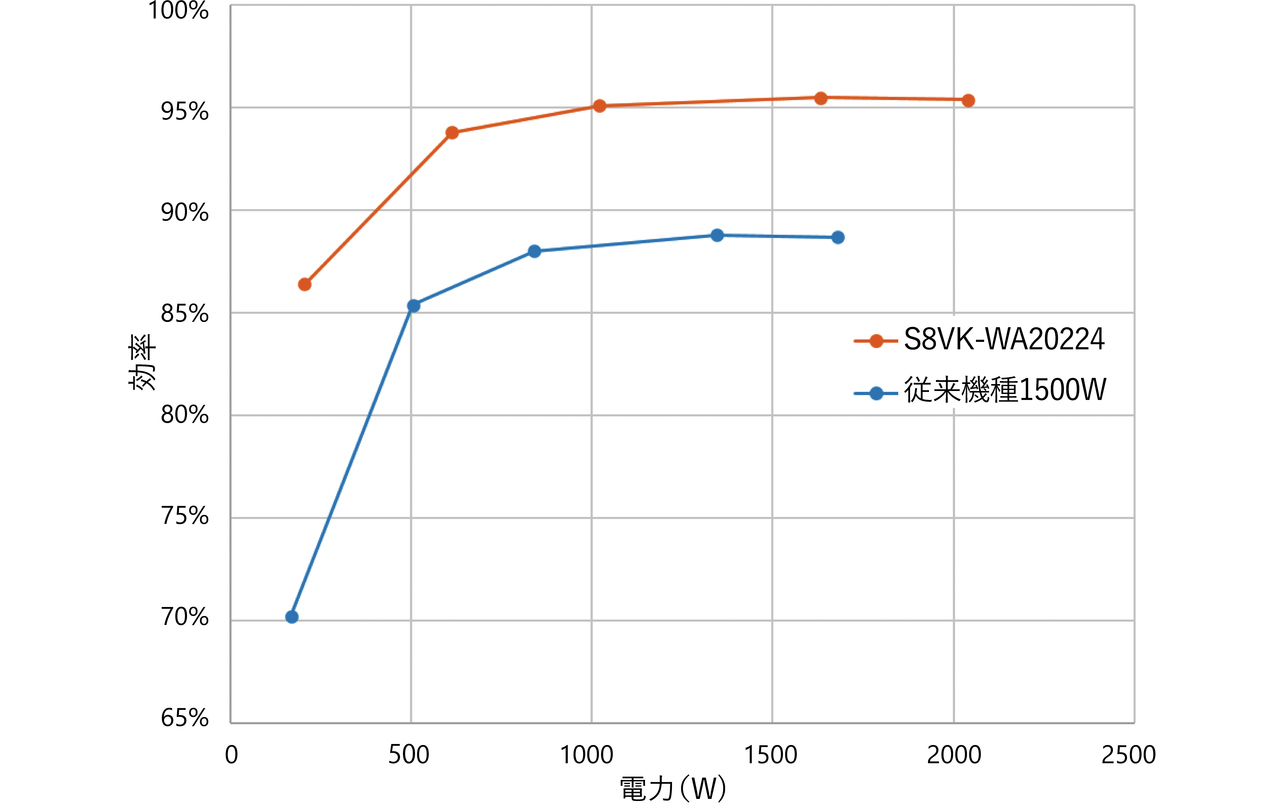
3.2 磁気シミュレーションによる損失の算出
熱シミュレーションでの放熱構造検討にあたり各素子の損失を算出する。
トランスなどの大型磁性部品では前述したように、机上計算でその損失を正確に見積もるのは困難であるため、磁気シミュレーションにより損失を算出した。図16にシミュレーション結果を示す。磁気シミュレーションにはJMAG(株式会社JSOL)を使用した。
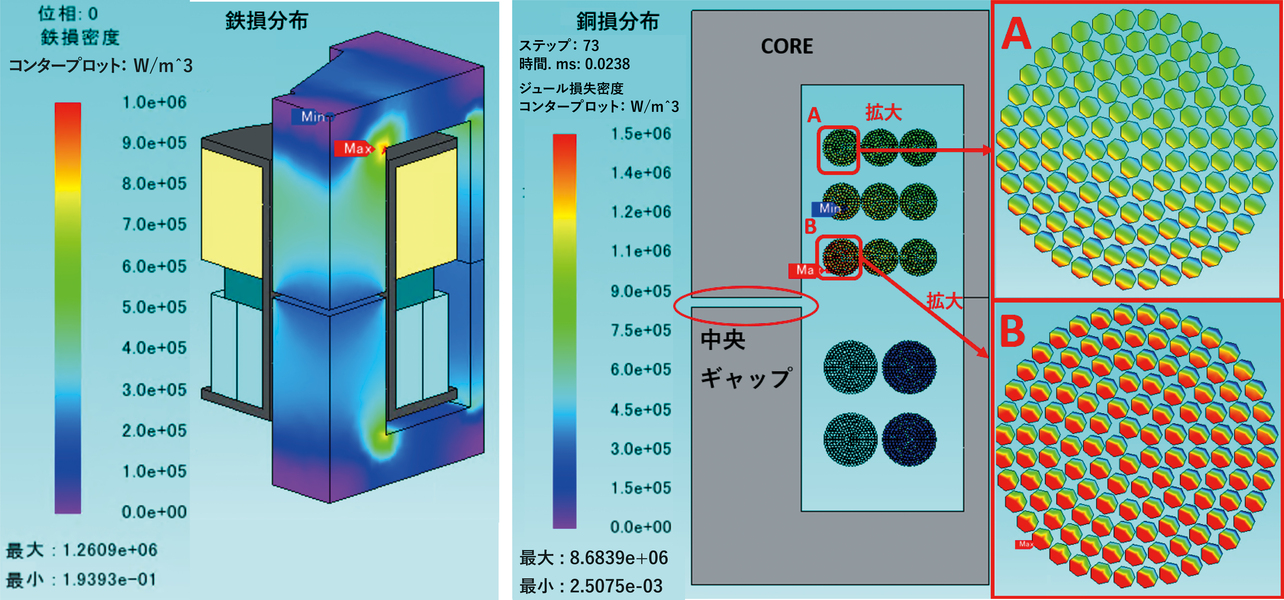
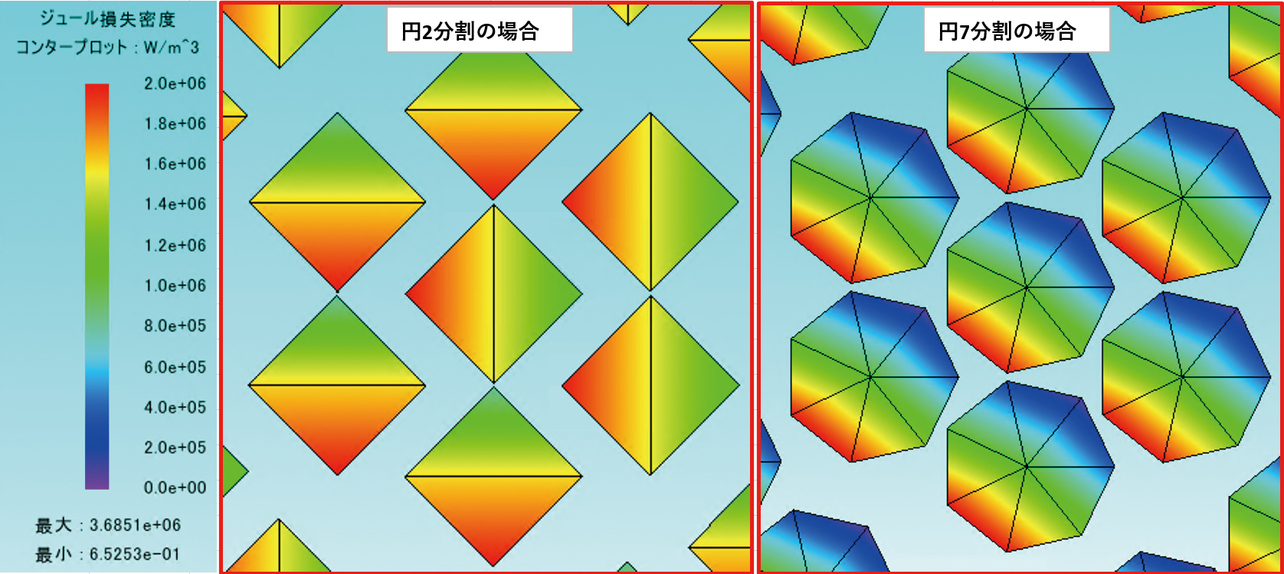
このとき、磁気シミュレーションによる損失の精度を向上させるために以下のような点に留意した。
①図16で示すようにコアの中央ギャップ付近の巻き線(図中のBの巻き線)の損失が大きく、そこから離れた場所の巻き線(図中のAの巻き線)の損失は小さくなっており、中央ギャップからの漏れ磁束により発生する渦電流損の影響がシミュレーションにおいても現れていることが分かる。渦電流損の精度向上のため、シミュレーションモデル構築の際、コアの中央ギャップと巻き線の位置関係をできるだけ実際のトランスに近くなるようにした。
②近接効果・表皮効果の影響の再現には巻き線の素線やコアギャップ付近のメッシュサイズが重要となってくる。具体的には図17に示すように、素線付近のメッシュサイズは円2分割の場合では素線の損失分布において近接効果の影響が十分に反映されていないのに対し、円を7分割した場合では近接効果の影響がシミュレーションで確認でき、損失算出の精度が向上していることが分かる。なお表皮効果については使用線径が0.1 mmと十分小さく、その影響がシミュレーションでも現れていない。ただしメッシュサイズを細かくしすぎるとシミュレーションに要する時間が増えるため、必要な精度がでる最低限のメッシュサイズを損失分布によって確認しながら、シミュレーションのスピードと精度が両立するようにしている。今回の場合は円7分割で実施した。
表4のように、机上計算により算出した損失を元に導出した温度では実測の温度と差異があったが、磁気シミュレーションにより算出した損失を熱シミュレーションで利用した場合には実測との温度差を減らすことができた。熱シミュレーションにはAnsys Icepak(ANSYS社)を使用している。
項目 | 損失 | 温度 |
---|---|---|
机上計算 | 6.81 W | 115.5℃ (熱シミュレーション) |
磁気シミュレーション | 8.81 W | 130℃ (熱シミュレーション) |
実測 | / | 127.5℃(実測) |
これにより最適な放熱構造を熱シミュレーションで検討することができ、自然空冷と小型化を両立することができた。
3.3 端子台過電流保護機能による異常時の安全確保
2.3節で示した電流集中の解決策について、図18を用いて説明する。2 kWの容量の電源では、負荷に約85 A以上の電流を流す能力がある。今回電源の負荷線を接続する端子台ごとに電流検出回路を搭載し、45 A以上の電流を検出すると保護回路により出力電圧を低下させ、電流を制限する機能(端子台過電流保護)を追加した。これにより一つの線が断線した場合、従来であれば意図しない大電流(85 A)が例えば許容電流45 Aの配線に流れていたが、今回上記機能により最大電流を45 Aに制限することで、線径の小さい配線を使用した場合の焼損するリスクを回避することが可能となった。
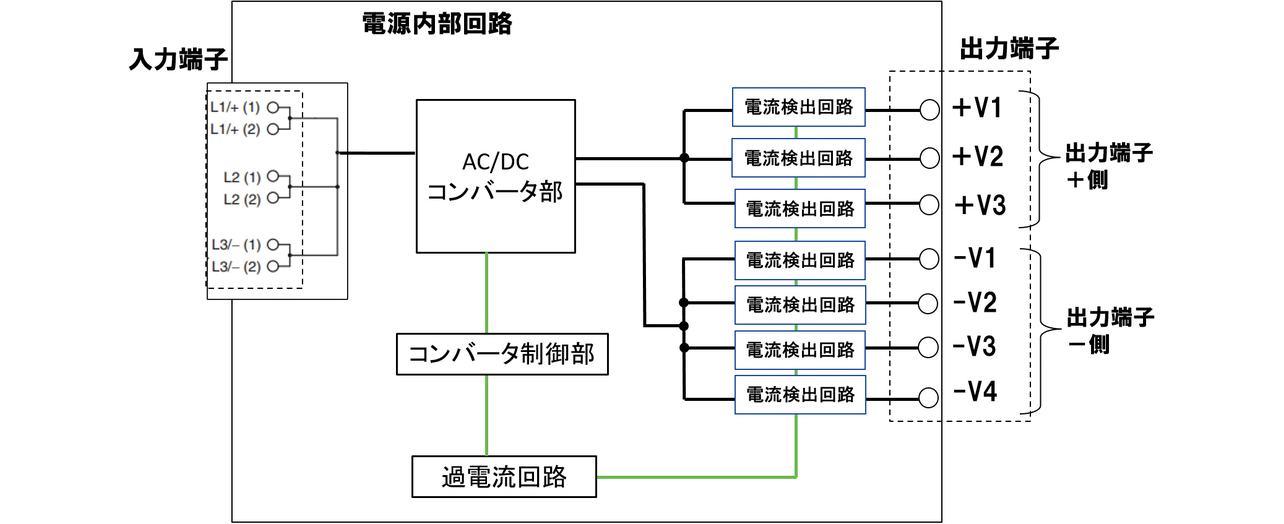
しかしこの端子台過電流保護機能の実現にあたり、各端子台において制限したい電流が仕様(目標値)からずれる問題があった。表5に具体例を示す。端子台-V2の制限電流値が、他の端子台(表5の場合は端子台-V1)に電流が流れることで、変化する現象が発生していた。
端子台-V1に流れる電流 | 端子台-V2の制限電流値 | 目標値45 Aとのずれ |
---|---|---|
0 A | 45 A | 無し |
20 A | 44.4 A | -0.6 A |
40 A | 43.8 A | -1.2 A |
この発生のメカニズムを図19を使って説明する。図19は端子台過電流保護の出力端子の-側(-V1~-V4)に搭載している回路である。なお簡略化のために端子台は2極(-V1, -V2)の場合で記載している。Rs1, Rs2は電流検出抵抗、ra, rb, rcはパターンによる抵抗成分を示している。
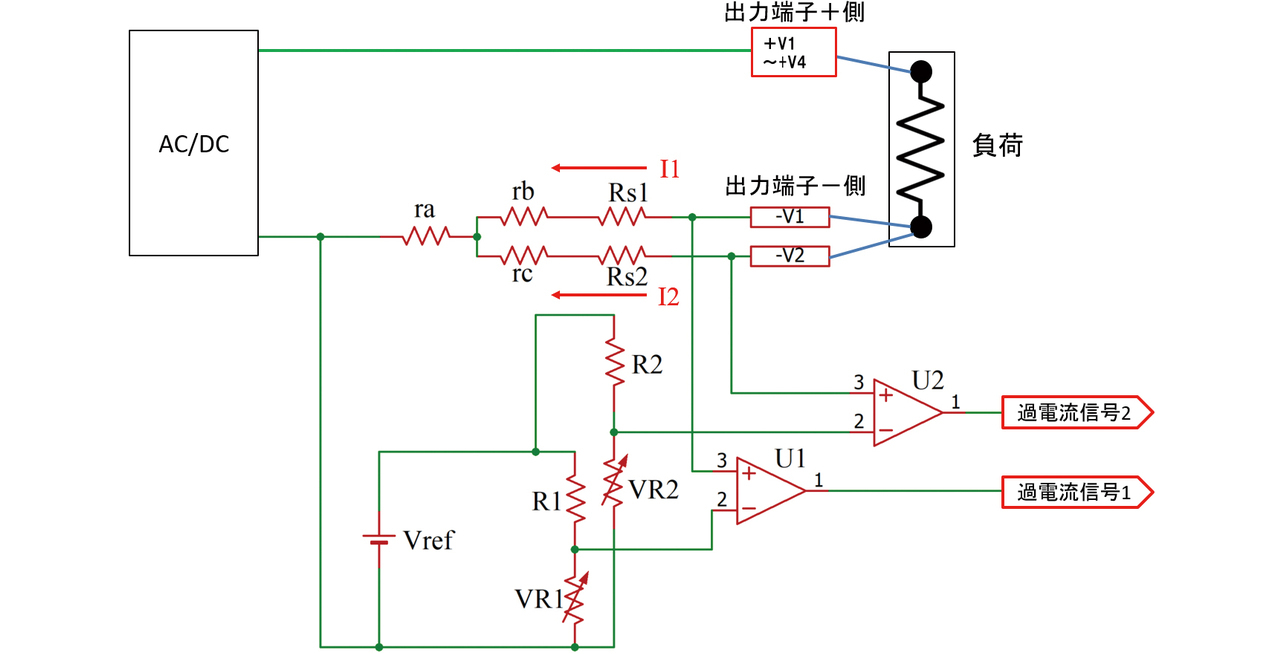
-V2端子を例にすると通常端子台過電流保護は電流が流れることで検出抵抗に発生した電圧(Vs2=Rs2×I2)を検出し、比較電圧(オペアンプのV-の電圧)よりも大きくなった場合に制御側に過電流信号を送る回路となっている。しかし端子台-V2の制限電流は端子台-V1に流れる電流(I1)の大きさによって変化してしまう。この原因は検出抵抗までの共通インピーダンスraによるものである。-V2端子の制限電流は、以下式で表されるようにI1の影響を受けることが分かる。
この共通インピーダンスraを小さくすることは、検出抵抗の部品配置やパターンの工夫で可能だが完全にゼロにすることは難しい。
そこでこの問題を解決するために図20のように検出抵抗Rs1, Rs2付近からそれぞれ個別に比較基準電圧を作った。これにより他の端子に電流が流れているかどうかにかかわらず制限電流を一定にすることができた。これにより、十分実用的な端子台過電流保護機能が実現した。
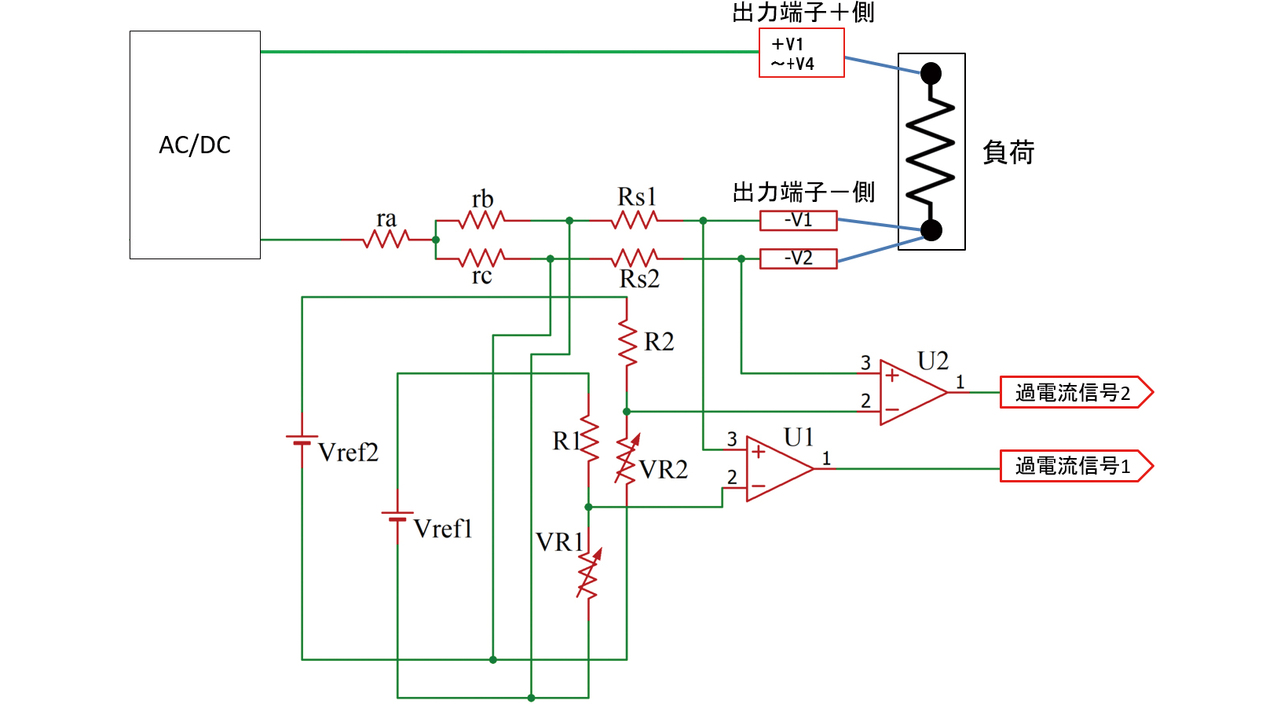
4. むすび
制御盤の小型化に貢献し、GHGを低減できる大容量電源を実現する技術について検討した。
- 流れる電流を複数素子に分散させて損失を低減できる一次直列二次並列型LLCコンバータを採用することで、大容量電源の高効率化を実現した。設計にあたり本稿ではこの回路方式のゲイン特性を明確にし、コンバータの各素子の電流バランスについて5%程度を狙うための各パラメータの許容範囲を求めた。これにより2 kW電源(形S8VK-WA20224)において95.4%の効率を達成、従来の1.5 kW電源の効率88.7%より大幅に向上させ、サイズについては17%の小型化に成功した。
- 磁気シミュレーションによりトランスなどの大型磁性部品の損失を正確に算出し、熱シミュレーションの精度を向上させた。この磁気シミュレーションを併用した熱シミュレーションによって最適な放熱構造を実現し、大容量電源の小型化と自然空冷とを両立させることができた。
- 負荷線を接続する端子台ごとに電流検出回路を搭載し、電流を制限する機能(端子台過電流保護機能)を追加した。この機能により使用する配線の線径を小さくでき、制御盤のサイズを10%減らすことができた。
これら技術により、超小型、低損失の2 kWの電源を開発し、サプライチェーン排出量における「製品の使用」(Scope3 Category11)でのGHG排出量を従来製品比で63%(CO2排出量FROM:286 kg/年 TO:106 kg/年)まで削減できた。
市場ではさらに3 kW, 4 kWといった大容量電源が求められている。そのような大容量電源に対応するためトランスの数をさらに増やした一次直列二次並列型LLCコンバータのバリエーションも考えられ、容量ごとに小型と高効率を実現できる最適なトランスの数とそのサイズ、コンバータの設計パラメータについて今後追及していく。
参考文献
- 1)
- E. Orietti, P. Mattavelli, G. Spiazzi, C. Adragna, and G. Gattavari, “Current sharing in three-phase LLC interleaved resonant converter,” in 2009 IEEE Energy Convers. Congr. Expo. 2009, pp. 1145-1152.
- 2)
- D. Huang, S. Ji, and F. C. Lee, “LLC resonant converter with matrix transformer,” IEEE Trans. Power Electron, vol. 29, no. 8, pp. 4339-4347, Aug, 2014.
- 3)
- J. Yuyang, R. Xinbo, D. Renxi, and X. Ye, “A DCX-LLC Resonant Converter with High Input-Output Voltage Ratio Based on an Integrated Matrix Transformer,” in IEEE Conf. Proc., 2022, vol. 2022, no. IECON, pp. 1-5.
- 4)
- Infineon Technologies. Resonant LLC Converter: Operation and Design. V1.0.(2012). Accessed: Oct. 1, 2023. [Online]. Available: https://www.infineon.com/dgdl/Application_Note_Resonant+LLC+Converter+Operation+and+Design_Infineon.pdf?fileId=db3a30433a047ba0013a4a60e3be64a1
本文に掲載の商品の名称は、各社が商標としている場合があります。