超高速CT型X線自動検査装置の開発
- CT
- X線
- 自動検査装置
- インライン
- はんだ検査
基板実装の世界では、はんだが見えず外観検査困難な部品や基板が増加している。また、自動車業界をはじめ、はんだの接合強度や全面検査など高品質を担保するための要求が増えている。これらの要求に答えるべく、CT型X線自動検査装置において、最たる課題であったインライン全面検査に必要なタクトを実現するための最新技術を紹介する。
高精度なモーションコントロール技術と高速画像センシング技術、これらの組合せにより開発された非停止で撮像する連続撮像技術を搭載したVT-X750は、従来機から2倍以上の大幅なタクト改善をはかり、低被曝検査を実現し、業界で初めてインラインでの全面検査を可能とした。信頼性を向上した新たなハードウェアを土台とし、時代とともに進化するオムロンのAXI(Automated X-RAY Inspection system) を紹介する。
1. まえがき
近年技術進歩が目覚ましい、EV(電気自動車)や自動運転などのADAS(先進運転支援システム)により、基板実装の世界は、さらに高密度化されていく流れとなっている。また、はんだが見えず外観検査困難な部品や基板も増加している。フィレットレスのチップ部品、接合部がパッケージの下面に配置されたBGA(Ball Grid Array)などがその代表である。市場の中でも、自動車業界が要求する品質保証のレベルは非常に厳しく、抜き取りでなく基板全数を検査すること、そして、はんだ形状を計測して接合強度まで検査することが求められるケースも多い。さらには、生産現場における労働者不足もあいまって、高精度・高品質検査の自動化ニーズの拡大が急速に進んでいる。そのため、実装業界における基板の品質課題や製造ライン停止といった事象が顧客の重大リスクとなり、不良基板が流出すれば、人々や社会の安全を脅かしかねない危機に直結する。よって、不良基板を世の中に出さない・出せない仕組みを提供し、我々の顧客の製品品質を向上させることが重要となってきている。
こうした世の中の流れを受けて、オムロンのX線自動検査装置AXI(Automated X-RAY Inspection system)は、部品の下面にはんだ部が存在するような外観では見えないものが検査できる装置としてSMT(Surface Mount
Technology)生産ラインへ普及してきた。しかし、従来の装置ではタクトに課題があり、オフラインでの抜き取り、あるいは重要部品に限定したインライン検査としての使われ方が主となっていた。本稿では、この課題を大幅に改善し、自動車業界の基板実装工程においても、インラインとして導入できるレベルの高速化を実現し、基板の品質を全数保証することを可能としたCT型インライン自動X 線検査装置VT-X750の技術を紹介する(図1)。
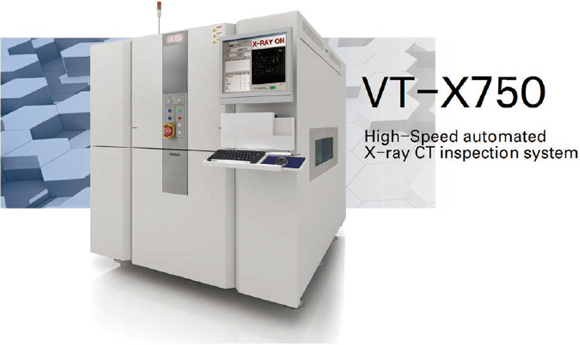
2.高画質を実現するCT 方式を用いたAXI
2.1 X線画像診断方式の比較
X線をつかった画像診断の方式としては主に透過・トモシンセシス・CT(ComputedTomography)といった種類がある。それぞれの方式ごとには次のような特徴がある。
透過方式は、X線源とワーク、X線カメラを垂直に配置し1枚の画像を取得する方式である(図2)。投影した画像は2次元(2D)データであり画像取得のための撮像時間は少ないが、扱うデータ量も少ないため、画質は他の方式に劣る(図3)。
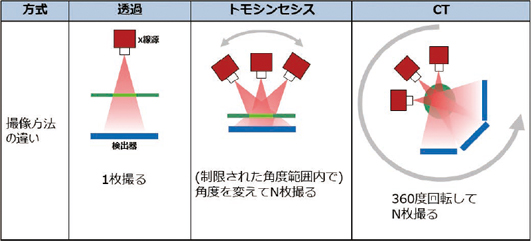
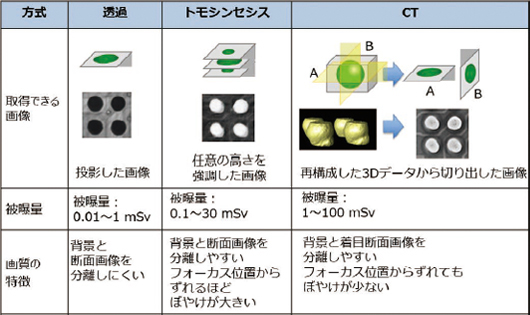
トモシンセシス方式は、X線源とワーク・X線カメラの位置関係において、制限された角度範囲内でN枚画像を取得する方式であり、任意の高さを強調した断層画像を取得することが可能となる(図3)。
透過方式にくらべ、撮像に時間がかかるがCT方式よりは速く取得することが可能である。画質は透過方式よりはよいが、X線源とX線カメラのフォーカス位置から離れた断層像においてはCTにくらべてぼやけた画質になる傾向がある(図3)。CT方式は、X線源・X線カメラとワークの位置関係において、360度回転してN枚の画像を取得し、3次元(3D)データを再構成する方式である(図2)。他の方式に比べ扱うデータが多いため、画質が最もよく、再構成した3Dデータから縦横だけでなく、高さ方向にもデータが活用できることが利点であり、X線源とX線カメラのフォーカス位置から離れた断層画像においてぼやけが少ない鮮明な画質を得ることができる。ただし、撮像においては時間がかかり、その分ワークへの被曝量も多くなるのが一般的である(図3)。
2.2 オムロンのAXI
我々は、はんだの接合面の形状を正確に検査するため、3Dデータ中の任意箇所を特定し画像で診断できるCT方式を採用している。2009年に、CT撮像方式での自動検査装置VT-X700をリリースして以降、BGAのボイド検査などを中心に多くの顧客の検査要求にこたえてきた。当社のAXIには、多岐にわたる技術要素が組み合わさっており、外観検査装置で積み上げた多くの知見をベースとして、基板の裏面の制約を受けないCT方式の利点を活かし、高精度な検査を実現している。大きな技術要素として、安全で屈強かつ高精度なセンシングを実現するハードウェア、応答性に優れ高速なコントロールを実現するソフトウェアから成り立っている。ハードウェアにおいては、大きくはメカ、エレキ、撮像の分野から構成されており、電気機械安全・遮蔽・軸の動作精度・制御応答性・画質・撮像速度などの設計パラメータが装置の性能において重要である。ソフトウェアにおいては、機差を補正するための組み立て調整ソフト、検査プログラムを作成する本体アプリケーション、撮像した画像を3Dデータとして作り上げる再構成処理、取得した3Dデータに対して検査を実施するアルゴリズムの分野からなる。これらの技術要素は互いに複雑に絡み合うため、機能モジュールごとの関係性をシームレスに精度よく動作させることが、高精度かつ高速な検査において必要となる。また、技術のコアである高品質なCT画像の取得のためには、特に撮像デバイスの基本性能、高精度なジオメトリ設計と制御、ロバストな補正処理と検査アルゴリズムが重要である。
2.3 撮像デバイスの基本性能(FPD とX 線源)
FPD(フラットパネルディテクタ)は、シンチレータという蛍光体を通してX線を光に変え、電気信号として変換し、デジタル画像を取得するためのカメラである。画素単位で読み込むため、鮮鋭性や感度の高い画像を得ることができる。当社では、対象物を鮮鋭に撮像するため、CMOS(ComplementaryMetalOxideSemiconductor)タイプのFPDを搭載し、検査で切り分けたい部品や対象に応じて、最適なコントラスト画像を得られるようパラメータを設計している。
X線源には、大きく開放管と密閉管という2種類がある。開放型のX線源は、線源外部に真空ポンプなどを配置する必要があり、フィラメントなどの寿命が短いことなどコストが高くなるうえに、線源自体の重量が重くなってしまうというデメリットがある。これに対し、密閉管は、X線発生部がガラスなどの密閉容器で常時真空に保たれているため、管外にポンプを設置する必要がなく、線源自体が小型であるのが特徴である。当社は、軽量でかつ焦点径の小さいマイクロフォーカス密閉管線源を選定し、搭載している。
2.4 高精度なジオメトリ設計と制御
当社のインライン型AXIのジオメトリ設計は、回転テーブル式ではなく並行テーブル式を採用している(図4)。これは、対象物に対しX線源やX線カメラ(FPD)の物理的な位置を変えることでCT画像を取得する方式である。この理由は、回転テーブル式では3Dデータの視野が円形で狭く、画像の端でぼやけが発生しやすいことや、回転速度の制限により撮像スピードの高速化に限界があるためである1)。
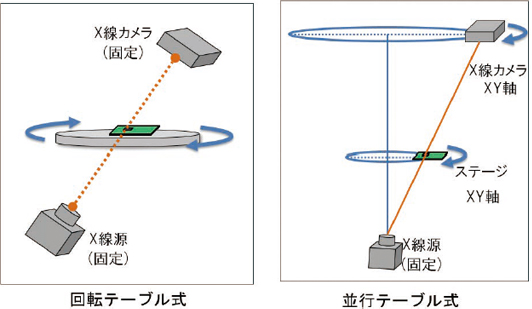
この並行テーブル式において特に重要となるのは、XY軸の旋回軌跡の位置精度である。また、Z軸については検査分解能を切り替える際や、変位系にて計測するワークの反りへの追従する際に駆動するため、Z方向の軸の位置決め精度も必要となる。
各軸には高精度なガイドを設け、当社独自のモータ制御技術にてμmオーダーの位置決め精度を実現している。特に、XY軸の旋回の精度は、旋回軌跡を真円に近づけるほど良好なCT画像が得られる。その土台となっているのが、必要な平行・真直度で組み付けられた品質のよいメカ部品、高精度の同期駆動を可能とする当社製のPLC(ProgrammableLogicController)やサーボモータによる制御技術である。また撮像デバイスは、剛性の高いフレームによって支えられ、末端部品が振動の影響を受けないよう屈強なハードウェアアーキテクチャで設計されている。
このように鮮明なCT画像を得るには、単に先述した撮像デバイスの基本性能や画質に起因するパラメータを追求するだけではなく、機械要素に起因するパラメータも考慮しながら設計することが重要となる(図5)。機械要素に起因するパラメータとは、装置の機械的剛性や重量バランス、どのように撮像デバイスを旋回させるかというジオメトリ設計、そしていかに高精度な軸の位置決め制御を実現するかという装置のアーキテクチャのことを示す。
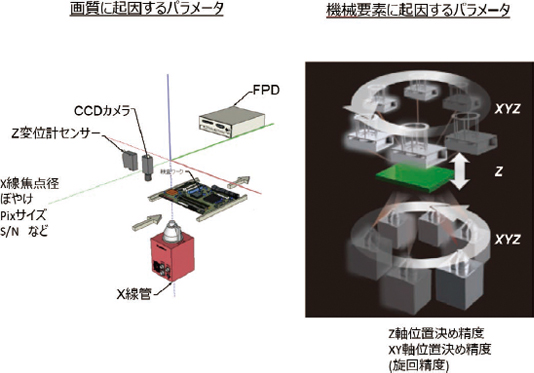
2.5 ロバストな補正処理とアルゴリズム
我々のAXIは、ハードウェアだけでなく、独自の再構成処理とアルゴリズム、外観検査装置での知見をベースに構築したソフトウェアアプリケーションにて、センシングした情報をスピーディに処理・コントロールを実施することで、高いはんだの形状再現性を実現し、接合面の検査を可能としている。
例えば、検査前にワークが装置内へ搬入された時に、停止する位置にはばらつきが存在するため、当社のAXIには、可視光照明とカメラを搭載しており、可視光で取得した画像を用いて、ワークのコンベア上での搬送停止位置のばらつきや回転ずれを補正する技術を搭載している。
また、正確なアルゴリズムの処理を行うには、再構成後の画像にて正しい断層位置を抽出する精度が要求されるが、装置内には、当社製の変位センサとコントローラを搭載しており、ワークの反りやたわみ量を計測して、Z軸の高さ位置を補正している(図6)。

3.インライン全面検査に向けた課題
インライン全面検査の実現に向けた課題としては、主にタクト、装置ハードウェアの信頼性向上があげられる。装置ハードウェアの信頼性とは、筐体重量とサイズ、検査ワークへの被曝量、メンテナンス性についてのことである。下記にそれぞれの課題を述べる。
3.1 タクトの課題
CT撮像方式は、高精度な画質が得られる一方で、360度旋回しながら撮像することが必要となるため、それに要するタクトが大幅にかかってしまい、インラインでのタクトが満たせないという課題があった。
実際に当社の従来機VT-X700では、ある顧客の基板においては、1枚当たりの検査時間が約70秒かかっていたが、インライン用途で検査するには、37秒以下にする必要があった。よって、従来機であるVT-X700は、オフライン型として導入され検査を実施するケースが多くなっていた。当社のAXIをSMTのインライン用途で普及させるためには、いかにタクトの高速化を実現できるかということが大きな課題であった。
数多くの技術検証を実施した結果、特に大きな改善を必要としていたのが、メカの移動速度、その中でもXY軸の旋回速度であった。VT-X700はSTOP&GOという撮像方式を用いており、旋回中の1PJ(プロジェクション:再構成の前段階における旋回中のある角度で取得した1枚の画像)ごとの画像撮像時には軸を停止させて画像を取得していたため、1旋回あたりのタクトが大幅にかかっていた。このSTOP&GOという方式は、確実に軸が停止してから撮像するので画像のブレは起きにくいが、旋回させるハードウェアユニットには、大きな振動や衝撃がかかるため、X線源は固定式にせざるを得ず、どうしてもステージとFPDを旋回させる構造にする必要があった。そのため、FPDの旋回半径が大きくなり、CT画像を得るまでの1旋回あたりにかかる時間が大きくなっているというメカニズムになっていた。
3.2 筐体サイズと重量の課題
インライン化を実現するためには、主に装置の筐体サイズと筐体重量にも配慮する必要がある。これは、X線検査装置は、SMT設備の中でも大きく重たいため、顧客の生産ラインへの運送や設置を考慮した際に標準的なサイズのコンテナで輸送できるか、搬入経路や床の耐久性は十分かなど検討する必要がでてくるためである。このため、機械部品は、剛性を高めすぎてユニット重量やサイズが増加すると、装置が重く大きくなってしまい、輸送や設置にかかる作業負担とコストが増えて設備投資の導入障壁となる。これらはSMT市場において、インラインの設備として生産ラインに導入するには重要な要素となる。
VT-X700シリーズにおいて、検査対象となるワークサイズは250mm角のMサイズといわれるものまでしか検査できなかったが、第3世代のモデルVT-X700-Lでは、500mm角以上の大きな基板まで検査できる構造とした。しかし、この機種における装置の筐体サイズは2m以上となり、装置重量が5トン以上となった。そのため、顧客のラインへ設置するための運搬も特殊設備が必要で、顧客が大きな額の設備投資をする必要があった。また、線源が固定のままでステージとFPDが旋回する従来のジオメトリ構造のままで検査対象ワークサイズのカバレッジを広げると、ステージが巨大化しFPDの旋回半径がより大きくなるためタクトはさらに遅くなってしまう傾向となっていた。上記のように、いかに重量とサイズを抑え、運用設置性を考慮し、連続撮像時に画像にブレが発生しないようメカの剛性を確保するかが課題となる。
3.3 検査ワークへの被曝量の課題
検査ワークへの被曝量は、大きな基板や検査部品が増えるほど照射時間が増え、基板全体への被曝量も大きくなる。また、基板上に被曝耐性の弱い半導体素子などの部品が搭載されることも増えていく傾向があるため、継続的に基板への被曝量を低減する技術を検討することが必要である。
3.4 メンテナンス性の課題
従来機では、検査空間とデバイス格納ユニットが同一遮蔽空間内に存在しており、かつ各デバイスは立体配置となっており、手が入れにくい、腰をかがめないと見えない、工具が入りづらいといったように、メンテナンス性に課題があった。顧客の生産でインライン運用をするということは、装置の稼働率が増えるという事である。また、装置の隣には別の装置が存在するため、保守時などで装置を止められる時間を最小限にしなければならず、かつ、装置前後から確実にすべての部品のメンテナンスができるよう改善する必要があった。
4.インライン全面検査を実現するVT-X750
我々は長年、これらの課題を解決する技術を模索検討し、タクト課題を解決する「連続撮像」という強力な技術と、信頼性を向上したハードウェア設計にて、これらの課題を解決した商品VT-X750を開発した。
4.1タクト課題を解決する連続撮像技術
以下にVT-X750に搭載している「連続撮像」技術の特徴を述べる。
4.1.1実現手段
1つめのポイントは、旋回撮像時メカが止まらず動き続けるということである。各視野の撮像時間を短縮するため、従来機種のSTOP&GO方式のように画像1枚ごとに移動・停止・撮像を繰り返すのではなく、非停止で旋回し、1視野分の全画像を取得する技術を構築した(図7)。
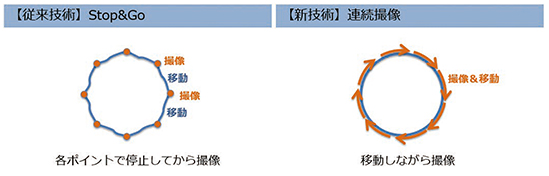
メカは等速で旋回する動作を繰り返すため、各軸の動作をいかに同期させ、旋回軌跡を真円に近い状態とすることができるかが重要となる。この技術を支えているのは、当社製のPLC NJコントローラと1Sサーボシステムによる真円の軌跡同期制御技術である。ただ単純に軸の動作を速く旋回させるだけではなく、動的かつ高精度に各軸の同期制御を実現している。
2つめのポイントは、高速で画像取得しデータ処理するシステムである。独自の回路網で発行する撮像トリガシステムにて、メカが動作している最中でも次々に画像を取得できるシステムを構築している。メカが移動中に高速で撮像する場合、画像のブレが起きやすくなることがわかっているが2)、1PJごとの撮像開始時間を記憶し、その時間におけるFPDとX線源の位置関係を考慮した再構成技術でブレを低減している。処理の速度についても、GPU(GraphicsProcessingUnit)を活用しながら、連続で高速伝送される画像を処理するスピードを確保することに成功した。
4.1.2 結果と効果
このように、高精度なモーションコントロールと高速なセンシング技術の組合せが連続撮像技術である。2017年にリリースしたVT-X750は、この連続撮像技術によってインライン検査に必要なタクトでCT検査を可能とするという革新的な技術進歩を遂げた。従来機種であるVT-X700と比較して、両面実装基板の標準的な検査条件における1視野の旋回撮像時間を7.7秒から3.2秒という倍以上の高速化に成功した。その結果、ある車載業界の顧客の基板の例では1枚あたりの検査時間が約70秒から35秒に短縮され、約2倍のタクトで検査が可能となった(図8)。
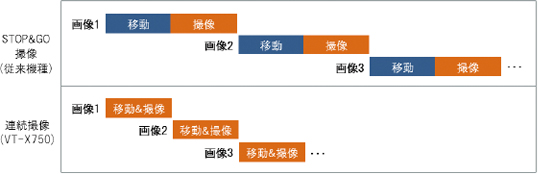
この技術の利点は、等速な軸動作のため旋回するハードウェアユニットに対する振動・衝撃が小さくできることである。そのため、X線源を旋回させ、重量物であるステージ部を固定にするジオメトリ構造とすることが可能となった。その結果として、FPDやX線源の旋回半径を従来の約60%に抑え、1旋回にかかる速度を大幅に短縮することを可能とした(図9)。旋回半径を小さくしたことでも上述した画像のブレは低減した。
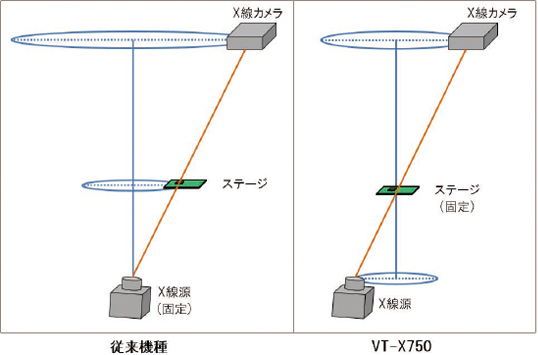
VT-X750のアーキテクチャは、シームレスな同期制御が核となる要素であり、これらは当社製1SサーボドライバとNJコントローラによって実現している。また、こうしたキーデバイスは、新機能を搭載したデバイスがリリースされれば、それらを即時装置へ設計反映できるようEtherCATベースの汎用IF(InterFace)のものを採用している。
その結果、さらに進化したサーボドライバを即時搭載することができ、2019年度にはVT-X750VER2.0をリリースする予定である。VT-X750VER2.0では、今後の検査対象部品の微小化に備え、より軸精度を向上させ高分解能での検査を実現するための開発を実行した。当社サーボドライバの開発部門との共同研究の末、複数軸の同期制御に適した2次補間機能(図10)を搭載したサーボドライバへデバイスをバージョンアップし、そのサーボドライバを装置へ搭載して位置決め精度の更なる改善を実行した。
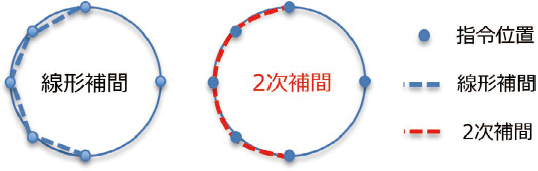
この機能を用いることで、サーボドライバ・NJコントローラと各モータの同期制御において、指令値に対する位置偏差の精度をさらに向上させることが可能となり、旋回における真円の軌跡の位置偏差量を最大で約4μm程度改善することに成功した(図11)。
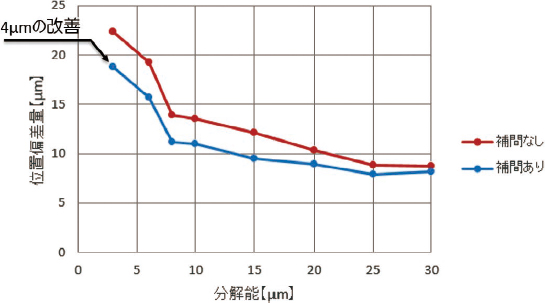
線形補間機能から2次補間機能ができるよう改善したことで、位置指令速度を階段状から連続に行うことができるようになるため、指令値との誤差が改善され、トルク変動を抑制することができ、旋回軌跡をより真円に近づけることが可能となった(図12)。
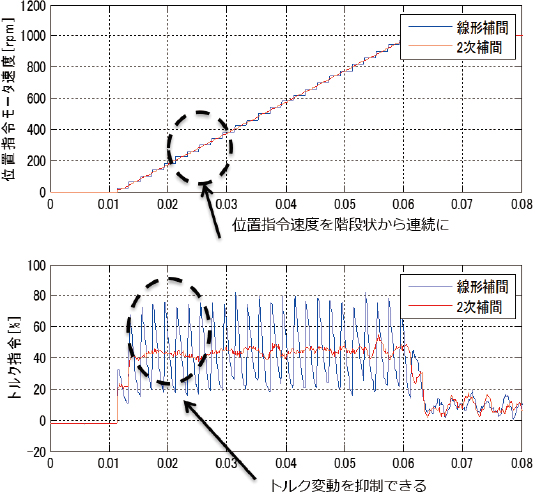
このように軸精度を改善したことで、VT-X750VER1.0では30μm~6μmまでであった検査分解能を、VT-X750VER2.0においては、30μm~3μmまでの高分解能帯までカバレッジを拡大することに成功した。こうした補正技術を用い、進化したデバイスをスピーディに装置へ反映することでハードウェアコストを上げずに高精度化を実現した。
4.2 インライン化のためのハードウェア高信頼性技術
4.2.1 高精度高速旋回に耐える省スペース高剛性技術
連続撮像によって、省スペースで旋回できるようになったため、VT-X750では検査空間と制御盤を分離したハードウェア設計とすることが可能となった。そのため、鉛遮蔽するエリアも小さく最適化でき、装置サイズと重量の観点でも改善することができた。VT-X750は、従来機のVT-X700のMサイズ検査用の装置とほぼ同サイズの筐体でありながら、検査対象基板は500mm角以上のVT-X700-L同等までのワークを検査可能とした。結果として、連続撮像によって軸の旋回速度が速くなっても画像のブレが発生しないようにメカの剛性を十分確保しながら、設置面積を45%、装置重量を2トン減らすことができた(図13)
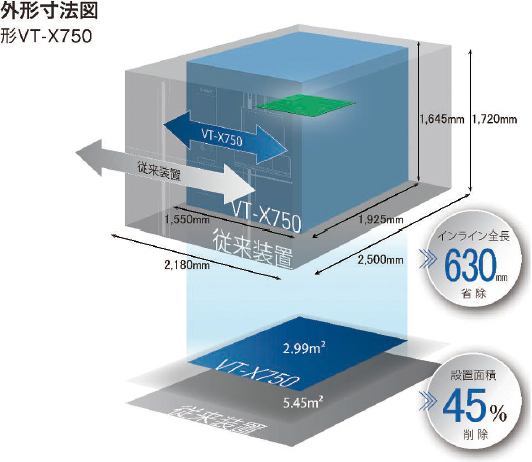
4.2.2 低被曝CT 検査を実現するフィルタリング技術
VT-X750は、従来機よりもワークへの被曝量は小さくなるよう設計している。まず、タクトが大幅にUPしたことでワークへのX線照射量自体が低減したため従来機より大幅に改善されている。
さらには、X線源照射窓にAlフィルタを標準搭載する設計としており、X線源のエネルギースペクトルにおいて、メモリや半導体などのアナログ素子部品に影響を及ぼす低エネルギー帯をカットしている。その結果、従来のVT-X700シリーズの23%までワークへの被曝量を低減することに成功した(図14)3)。
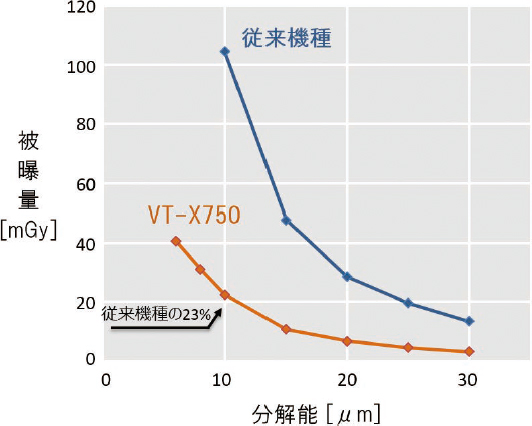
4.2.3 高可用性ハードウェアアーキテクチャ
VT-X750は、遮蔽された検査空間と制御盤を分離した構造とし、すべてのデバイスを正面からアクセスできるよう設計しメンテナンス性を改善した。特に制御盤の構造においては、漏電ブレーカと連動したドア機構を設け、保守時には装置のブレーカを落としてからでないと制御盤のドアを開けられないよう安全性を確保した設計となっている。また、汎用IFを用いて省配線化されておりケーブルのメンテナンスもしやすくなっている。無理な姿勢で作業しないよう、人体にかかる負荷も考慮した。これらはすべてSEMI(SemiconductorEquipmentMaterialsInternational)スタンダード4)における人体工学の考え方に基づき設計しているため、インラインで稼働する設備においても、故障時に顧客の生産ラインをとめる時間を極小化するよう、安全かつ素早く保守できるようになった。
5.むすび
このように洗練されたアーキテクチャは、連続撮像技術の強みを最大化させることができる。そして、これまでより高速にインラインでのCT検査が可能になったことで、従来でのオフラインでの抜き取り検査の場合よりも遥かに多くの基板を検査することができ、来る自動運転社会に備え、顧客の生産ラインにおいてより多くの基板の製品品質向上に貢献できるということである。
本稿では、CTでの検出力を保ちながら高速化を実現するための連続撮像技術、刷新したハードウェア構造をもつVT-X750について概説した。今回は主にハードウェアの分野を中心に述べたが、自動検査アルゴリズムについても独自の技術が数多く搭載されている。優れた形状再現性を持ち、CTの特徴に基づいて最適化された検査アルゴリズムは、撮像システムの高速性に後れを取らずインライン検査可能なタクトで処理を実現している。
今後の展望としては、はんだ接合部をより正確に形状再現し定量的に測定するための検査アルゴリズムの改善に加え、外観検査装置と連携した効率的な検査工程設計、プログラミング作業の時間短縮による運用支援などの開発を進めていく。また、AXIのタクトをさらに高速化する技術を探求していくことで、部品の下面にのみはんだが存在するような基板に対しても全数検査を実現できるようになる5)。そのため、今後も自動車業界をはじめとするSMT市場において、オムロンのAXIを普及させ、顧客の製品品質を向上することに貢献していく。
参考文献
- 1)
- 杉田信治.実装品質保証のカバレッジ拡大に向けた高速CT検査技術.第52回ソルダリング分科会資料,一般社団法人溶接学会,2011,p.4.
- 2)
- 日本放射線技術学会監修市川勝弘・村松禎久.標準X線CT画像計測,オーム社,2009,p.27-28.
- 3)
- 大西貴子.高速・高分解能・低被曝を実現するインライン自動X線検査装置.画像ラボ.2018,Vol.29,No.1,p.67-72.
- 4)
- SEMI S8-1116, Safety Guidelines For Ergonomic Engineeringof Semiconductor Manufacturing Equipment,SEMI International Standards, 2016.
- 5)
- Jisso技術ロードマップ専門員会.2015年度版実装技術ロードマップ.一般社団法人 電子情報技術産業協会,2015,p.354-355.
本文に掲載の商品の名称は、各社が商標としている場合があります。