AI搭載マシンオートメーションコントローラの開発(3)
- AI技術
- リアルタイム異常検知
- 設備保全
- PLC
- 機械学習アルゴリズム
近年、製造業では、熟練技能者の不足や人件費高騰の影響を抑えるためAIやIoTを活用するニーズが高まり続けている。
オムロンでは、設備の稼働率向上と高品質な製品を安定的に生産するため、設備の異常検知を実現する「AI搭載マシンオートメーションコントローラ」を開発した。本来、異常検知を実現するには、データサイエンティストによる装置の因果関係を踏まえたデータ分析を元に、異常検知モデルを生成する必要があるが、属人性の高さおよび、専門性の高さという点で課題がある。
我々は、その課題を解決するため、異常検知モデルの生成の自動化を実現するツールを開発した。機械学習アルゴリズムを活用することで、異常検知モデル生成の自動化を実現し、そのモデルにより高精度な異常検知を実現できることを確認した。
1. まえがき
近年、製造業では、多品種少量生産やグローバルでの最適地生産の流れが加速する中、熟練技能者の不足や人件費高騰の影響を抑え設備の稼働率向上と高品質な製品を安定的に生産するため、モノづくりの現場においてAIやIoTを活用するニーズが高まり続けている。
オムロンでは、AI技術の活用事例の一つとして「AI搭載マシンオートメーションコントローラ(以下AIコントローラ)」を開発した。AIコントローラはマイクロ秒単位で刻々と変化するラインや装置の状態をリアルタイムに監視し、搭載したAIに学習させた「異常検知モデル」を基に機械の“いつもと違う動き”を推定することで、異常が発生する前に安全に装置やラインを制御するというものである 1)2)3)。
製造現場において、異常検知や予知保全を実現するためには、製造装置の異常と測定可能なセンサーデータの因果関係を把握する必要があり、現状、統計処理の知識と、多くの解析のための時間を要するという問題がある。
また、AIコントローラの利用者である製造現場のエンジニアの趣向として、実現した異常検知モデルがどのように生成されたか生成過程が明瞭であることを重視する傾向がある。
我々は、これらの問題や利用者の趣向を踏まえた上で、AIコントローラに不可欠な異常検知モデルの生成を自動で行うツールについて検討した。本稿では、その検討結果について述べるものとする。
2. 課題
2.1 AIコントローラを活用した異常検知の流れ
AIコントローラは、周期的に繰り返し製造を行う装置を対象に、PLC(Programmable Logic Controller)の制御対象である製造装置の各種機器の制御データ(サーボモータのトルク値やファイバセンサの論理信号など)を活用することで、リアルタイムに異常を検知する。AIコントローラでの異常検知の方法は、図1の通りで、まず収集した装置の制御データを製造の周期単位(タクト、サイクル等)に切り出す。次に切り出した区間の波形に対して特徴量を算出する。AIコントローラでは、平均値、標準偏差、歪度、尖度、最大値、最小値の分布の形状を表現する6つの特徴量を扱うことができるため、1つの波形に対して最大で6種の特徴量を得ることができる。この算出した特徴量に対して異常検知アルゴリズムの1種であるIsolation Forest(以下I-Forest)4)を適用し、その結果として異常度合いを示すスコア(以下異常度スコア)を得る。最後に異常度スコアに対してしきい値判定を行うことで、製造の周期単位に異常が起こっているかどうかを判定するというものである。
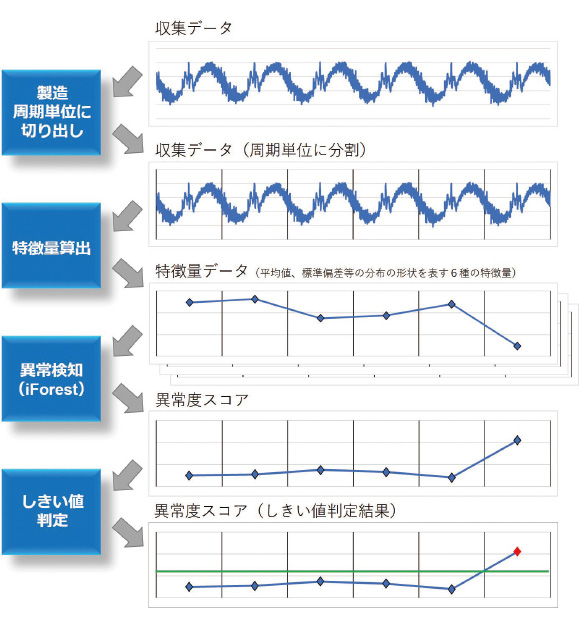
この異常検知方法により、AIコントローラは高い検知性能および処理の高速性を実現している 5)6)。但し、この異常検知の方法を実現するためには、事前に設定しておくべき次の2つの事象がある。
- A)異常検知に有効な変数および特徴量の選択
- B)しきい値の設定
そのため、AIコントローラの利用者は、異常検知を実現する上で、図2に示す収集、分析、活用の3つのフェーズから構成されるプロセスを実行する。
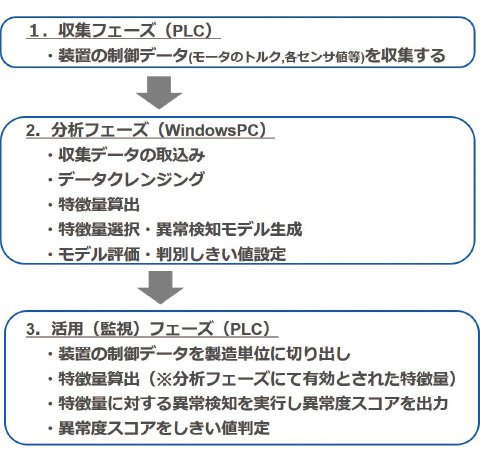
本稿で述べるAIコントローラのモデル生成ツールは、このプロセスにおける分析フェーズにて用いるもので、収集フェーズで収集した装置の制御データを元に、異常検知モデルを生成する役割を持つ。
2.2 製造現場における異常検知モデルの獲得
製造現場において異常検知を実現するためには、製造装置の異常状態を起こすイベントと測定可能なセンサーデータの因果関係を把握する必要がある。通常は、製造装置の知識やノウハウを踏まえた上で、データサイエンティストが装置の因果関係が得られるまで、様々なデータ処理や解析を人手による試行錯誤を含め繰り返す過程を経るものであり、深い統計処理の知識と、多くの解析のための時間を要する。また、解析手法の使用が不適切なためデータの中に潜む重要な情報を見逃す、対象装置の振る舞いの考慮が不十分なため誤った解析結果を導くなど、データサイエンティストの高度な専門性が解析結果の精度に影響を与える。
一般的に、データから目的とする因果関係を踏まえた異常検知モデルを得るためには、高い専門性を持ったデータサイエンティストが図3に示すKDD(Knowledge Discovery in Databases)7)プロセスを何度も繰り返す必要がある。
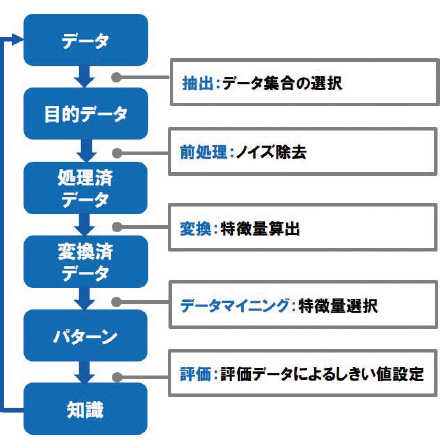
AIコントローラでは、装置の保守者も利用者になり得るため、統計処理の知識のない人でも少ない工数で、最良の異常検知モデルを作成できるようにする必要があり、このKDDプロセスを簡単に実行できるようにすることが鍵となる。
モデル生成ツールでは、上述のAIコントローラ活用の異常検知のプロセスにおいて、分析フェーズを担い、事前に収集した制御データから、目的とする異常検知モデルを生成する。この分析フェーズの流れをモデル生成ツールで実現するにあたり、我々は分析の流れをKDDプロセスに即した形とし、それぞれのプロセスを簡単に実行できるように、可能な限り自動化を目指すこととした。
しかしながら、分析フェーズを自動化することで、モデル生成過程が不透明になるため、生成過程の明瞭性を求める製造現場では適しない面がある。我々はこれらの相反するニーズを解決するため、次の課題を解決する。
- モデル生成ツールによる分析フェーズの自動化
- 異常検知モデルの生成過程の説明性を上げるUI
この2つの課題を解決するために実現した技術について、次章より述べる。
3. 技術内容
3.1 分析フェーズの自動化
我々は、分析フェーズにおける属人性の高さを無くすため、異常検知モデル生成ツールによる分析フェーズの各プロセス(データクレンジング、特徴量算出、特徴量選択、しきい値設定)を自動化する。具体的には、次に述べる通りである。
- A)データクレンジング
収集したデータの中から明らかに分析には活用できないデータ(欠損値、分散ゼロのデータ)を除去することとした。 - B)特徴量算出
2.1章で述べたようにAIコントローラでは、6種の特徴量を扱うことができる。異常検知モデル生成ツール上では、収集データの1波形に対してこれらすべての特徴量を自動的に算出する。 - C)特徴量選択
変数選択の手法として、決定木 8)とロジスティック回帰 8)を活用することで、どの特徴量が正常と異常を判別するのに適しているかを、効率的に探索することを採用した。
図4に特徴量選択の流れを示す。
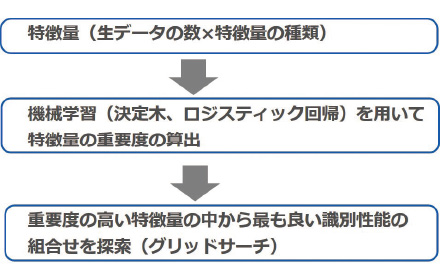
まず収集データにつけられた正常・異常のラベルを目的変数、得られたすべての特徴量を説明変数として、決定木およびロジスティック回帰を実行し、重要度(正常・異常を判別するのに適しているかどうかを見るための指標)を算出する。得られたすべての特徴量の中から、この2つの分析手法で算出した重要度の高い特徴量を選出することで、特徴量の絞り込みを行う。
決定木は、木構造を用いて分類や回帰を行う機械学習の手法の一つで、非線形の問題にも適用できるというメリットがある。本手法の決定木における重要度は、各特徴量で判別したときの判別前後のGini係数の減少量であり、値が大きいほど正常・異常を判別する変数として適していることを表す。
ロジスティック回帰は、0から1の間の値を取るロジスティック関数への回帰であり、本手法では1変数ずつアルゴリズムを適用する。また目的変数(=正常・異常を表すラベル)とのあてはまりの良さを表す尤度を重要度として解釈し、値が大きいほど正常・異常を判別する変数として適していることを表す。1変数ずつ適用しているため説明性が高いというメリットがあるが、非線形の問題には適用できないというデメリットがある。
我々は、これら異なる特徴を持った2つの変数選択の手法を組み合わせることで、偏りのない特徴量の絞り込みを実現した。
次に、AIコントローラの異常検知アルゴリズムとして採用されているI-Forestを適用する中で、実際にどの特徴量の組合せが、高い識別能力を有するか探索する。前の過程で決定木およびロジスティック回帰にて選択した特徴量の中から、すべての組合せを網羅的に検証し、I-Forestを適用した時の識別能力の高さを計測する。このとき識別能力の高さを測る指標として、AUC(Area Under the Curve)9)を採用した。AUCとは、ROC曲線の曲線下面積を表す。ROC曲線とは、しきい値を変化させたときの、偽陽性率(間違って正常を異常と判定した確率)と真陽性率(正しく異常を異常と判定した確率)の関係をプロットしたものである。判別能力の高いモデルとは、この偽陽性率が低い点で、真陽性率が高くなるモデルと表現することができ、この考え方を表した指標がAUCである。本手法では、網羅的な探索からAUCが最も高くなる特徴量の組合せを異常検知モデルの変数として採用することで、自動的な探索を可能にした。
- D)しきい値設定
しきい値の設定は、正答率(正常を正常と、異常を異常と正しく判別した割合)が最も高くなる点をしきい値の初期値として設定する。
このようにA)からD)までを収集データに対して実行することで、自動的に識別能力の高い異常検知モデルを生成することを可能とした。
3.2 モデル生成過程の説明性を上げるUI
3.1により異常検知モデルの生成過程を自動化することができたが、その自動化により、モデル生成過程の透明性が欠けてしまうという問題が発生する。そのため我々はモデル生成過程の説明性を上げるため、モデル生成ツールに次のような工夫を施した。
ひとつが操作フローにおける工夫で、具体的には、自動的に異常検知モデルを生成する際の最終工程において、一旦、ユーザに生成されたモデルの識別能力、および、選ばれた特徴量の組合せやしきい値について確認を促すようにしたことである。もしユーザが識別能力や選ばれた特徴量に疑問がある場合、異常検知モデル生成の各工程に戻り、処理内容や履歴を確認でき、設定内容に納得できない場合、設定内容を調整できる仕組みを構築した。
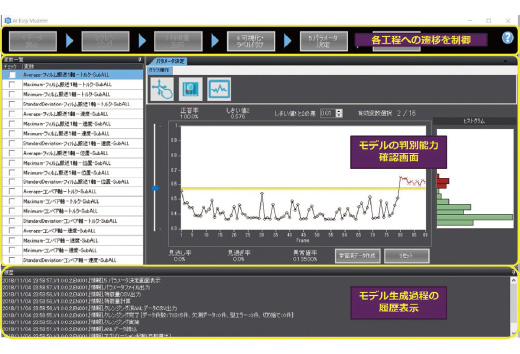
図5は、モデル生成ツールの画面例であるが、異常検知モデル生成の各工程に遷移することができるナビゲーションバー、異常検知モデルの識別能力およびその中身である特徴量の組合せやしきい値を確認する画面、操作履歴を確認する画面を備えている。このような操作フローおよびUIとすることで、ユーザは、異常検知モデル生成の各工程で、どのような処理がなされたかを確認することができ、また、最終的に生成されたモデルの識別能力と、その中身である特徴量の組合せやしきい値について確認することができるため、モデル生成過程の説明性を担保することができると考える。
もうひとつの工夫が、モデルの識別能力を表す指標を複数個持たせることにより、特徴量の組合せの変更やしきい値の調整をしやすくした点である。
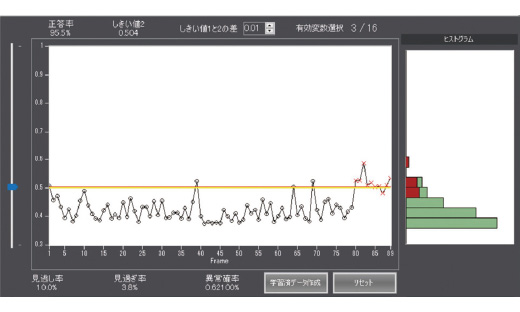
(しきい値の調整画面)
図6は、異常検知モデルの識別能力を確認する画面である。中央のグラフは、異常度スコアとしきい値の関係を示しており、画面周辺部分に異常検知モデルの識別能力として正答率に加えて、見過ぎ率、見逃し率が確認できる。見過ぎ率は、正常データのうち、間違って異常と判定した割合を示し、見逃し率は、異常データのうち、間違って正常と判定した割合を示す。グラフの各点において〇が正常、×が異常を示しており、この図6の例ではしきい値で、正しく判別できていない点が存在している。
製造現場では、異常を正常と誤検知する見逃しが許されない現場もあれば、正常を異常と誤判定する見過ぎが多くなることで、監視機能の結果を、利用者に信じてもらえない状態になることを懸念する現場も存在する。
図6のように生成された異常検知モデルの結果において、正常と異常の領域が重なり、完全に判別できない場合が起こり得る。そのような場合において、この3つの識別能力の指標を確認し、現場の意見を取り入れながら調整することが可能となる。
4. 実験
本章では、弊社製PLCで制御されている横ピロー包装機(図7)を題材として、実際にモデル生成ツールを活用したモデル生成機能の検証結果について述べる。横ピロー包装とは、樹脂製フィルムなどの包材によって製品を枕状に包装する方式である。横ピロー包装機は一般的に、包材の搬送、製品の搬送、製品の梱包と包材胴部の溶着、包材端の溶着と切断の主に4つの機能から構成されており、各機能を実現するためのサーボモータが包装機に搭載されている。この横ピロー包装機について、その主要なイベントである異物噛み込みを検証の対象とした。異物噛み込みは、包材の溶着部分に異物が噛み込むことで、密閉が不十分となる異常であり、製品の品質に大きく影響する重大な不具合である。
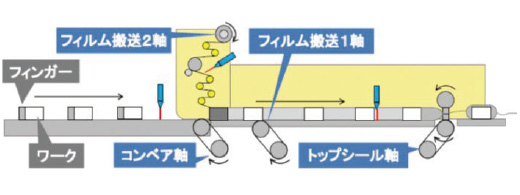
包装機に搭載されているAIコントローラは、4ヵ所のサーボモータ(コンベア軸、フィルム搬送1軸、2軸、トップシール軸)についてそれぞれトルク・速度・位置の実測値と、3ヵ所のファイバセンサの論理値を一定周期(2ms)で収集する。毎秒1個の速度でワークを包装した場合、包装1個あたりサンプル数500点のデータが取得できる。図8にサーボモータのトルク・速度の収集データの一部分を示す。
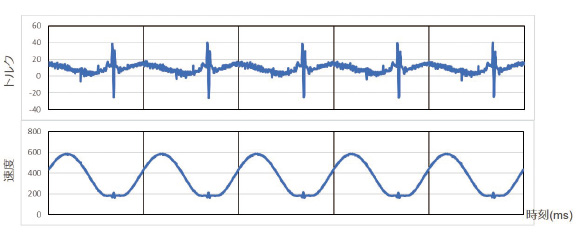
(トップシール軸トルク・速度)
この収集データを、モデル生成ツールに入力し、異常検知モデルを生成する。まず収集データを元に算出された特徴量データは、合計90次元(収集データ15次元×6種の特徴量)が得られた。
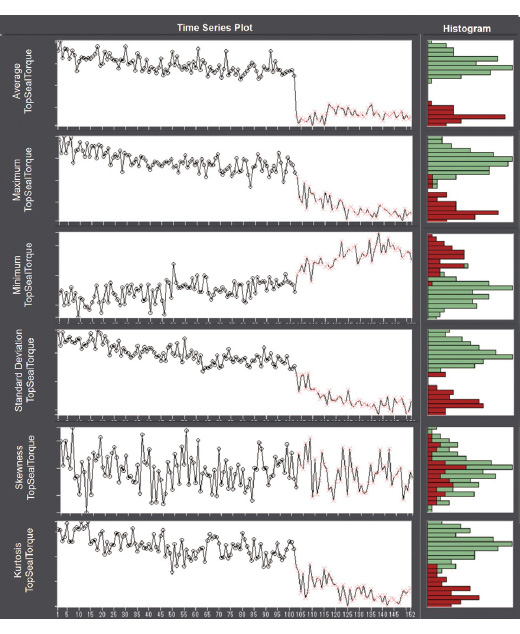
図9にトップシール軸のトルク実測値から得られた6種の特徴量データについて時系列グラフ(縦軸:特徴量、横軸:時刻)を示す。またグラフ上の各点において〇は正常、×は異常を表す。
次に、特徴量算出によって得られた90次元の特徴量データを元に、異常検知に有用な特徴量を選択する。表1にモデル生成ツールにより算出された、各特徴量の重要度(尤度)を示す。決定木、ロジスティック回帰の重要度(尤度)は値が大きいほど、正常・異常を判別するのに適していることを示している。
表1の結果より、トップシール軸トルクの平均値、標準偏差、トップシール軸速度の最大値が最も異常検知に有用な変数であることが確認できる。これは前の図9で示す特徴量のグラフから、トップシール軸トルクの平均値は、正常と異常の領域が分かれていることが読み取れ、そのことからもトップシール軸トルクの平均値が異常検知に有用であることが確認できる。
特徴量名 | 重要度(尤度) | |
---|---|---|
決定木 | ロジスティック回帰 | |
トップシール軸トルク−平均値 | 67.1 | 0 |
トップシール軸トルク−標準偏差 | 67.1 | 0 |
トップシール軸速度−最大値 | 67.1 | 0 |
トップシール軸トルク−最大値 | 63.2 | −6.13 |
トップシール軸トルク−尖度 | 61.2 | −7.79 |
最後に、重要度の高い特徴量の中から、実際に異常検知アルゴリズム(I-Forest)を適用し、最も異常検知精度の高い特徴量の組合せと、しきい値の設定を行う。図10に示す画面は、最終的に選ばれた特徴量の組合せ、しきい値の設定結果、および、その時の、異常度スコアの振舞いと判別性能を示している。
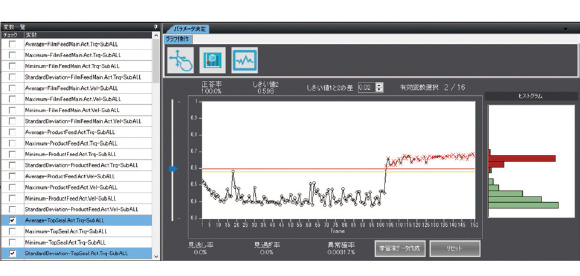
画面左側に表示される変数一覧においてチェックのついているものが選択された特徴量を示している。結果、トップシール軸トルクの平均、標準偏差が選択されたことが確認できる。また、画面右側に表示されるグラフ部分は、I-Forestにて算出された異常度スコア(図9同様、各点において〇は正常、×は異常である)と、しきい値(赤の直線)を示している。正答率100%、見逃し率0%、見過ぎ率0%となる位置にしきい値を設定できていることがわかり、この結果より、適切にモデル生成ができたことが確認できる。
また最終的に選択された特徴量は、トップシール軸トルクの平均値、標準偏差の2つとなったが、理由は、この2つの特徴量で正答率100%となるためで、重要度の高い特徴量のうち、トップシール軸速度の最大値以降の変数は採用されていない。
5. むすび
本稿では、AIコントローラに不可欠な異常検知モデルの生成を行うツールについて検討し、異常検知モデル生成の自動化と、モデル生成過程の説明性向上を実現する手法について検討した。
結果、4章の包装機を用いた実験による検証で、収集したデータから、自動的に正答率100%の判別性能を持つ適切な異常検知モデルを生成できることを確認した。
また、弊社社内の技術者が検証用に本異常検知モデル生成ツールを活用しているが、異常検知モデル生成の性能に加え、ツールとしての操作性においても、生成過程の履歴が追える点や、しきい値や選択特徴量の調整時のUIについて好評を得ている。
また、本手法において、決定木とロジスティック回帰を用いて異常検知モデル生成における特徴量選択を実現したが、得られたデータのみから導出した結果であるため、実際の装置の因果関係として、選ばれた特徴量よりも相応しい特徴量が存在する場合がある。データのみを頼りに異常検知モデル生成をしている以上、実際の装置の因果関係を表すことは、現状困難である。今後は、データ以外の現場情報等の活用により、より現場の知見に沿った因果関係を導き出し、よりよい異常検知モデルの生成を実現したいと考える。
参考文献
- 1)
- オムロン株式会社. マシン制御とAIをリアルタイムに融合「AI搭載マシンオートメーションコントローラ」を開発
http://www.omron.co.jp/press/2017/04/c0425.html,(参照 2018/11/01) - 2)
- 見置 孝昌、出来 仁太郎. AI搭載マシンオートメーションコントローラの開発(1) 保全担当者が使用できるAIシステムの実現とマシンオートメーションコントローラへのAI機能の搭載
- 3)
- 太田 政則、西山 佳秀.AI搭載マシンオートメーションコントローラの開発(2) 制御に同期したデータ収集と時系列データベースの実現
- 4)
- Fei Tony Liu, Kai Ming Ting, and Zhi-Hua Zhou. Isolation-based anomaly detection. ACM Transactions on Knowledge Discovery from Data(TKDD),6(1):3, 2012.
- 5)
- 鶴田 浩輔、峯本 俊文、広橋 佑紀. マシンコントローラに搭載可能なAI技術の開発(1)装置制御用データを利用した生産ラインの異常検知手法について . OMRON TECHNICS 2018 vol.50 no.1 p.6-11
- 6)
- 阿部 泰明、上山 勇樹、阪谷 信之、藤井 高史. マシンコントローラに搭載可能なAI技術の開発(2)異常検知コントローラプロとモデル開発における実証例について
- 7)
- Fayyad, Usama; Piatetsky-Shapiro, Gregory; Smyth, Padhraic. "From Data Mining to Knowledge Discovery in Databases"(1996).
- 8)
- 平井有三.初めてのパターン認識, 森北出版
- 9)
- 井手剛、杉山将. 異常検知と変化検知,講談社
本文に掲載の商品名は、各社が商標としている場合があります。