無線押ボタンスイッチの伝送状態を可視化する通知機能の開発
- 無線押ボタンスイッチ
- 無線通信
- 通信信頼性
- 通知機能
- エナジーハーベスティング
製造業の多品種少量生産化の流れに伴い、工場内のレイアウト変更に対して柔軟に対応できる生産設備が求められている。無線押ボタンスイッチは、信号線が不要であり、さらに発電機能の内蔵によって電源線をも不要としているため、有線の押ボタンスイッチと比べて設置の自由度が高く、配線工数が低減できるという利点から、生産現場への導入が進みつつある。
一方で、工場内では電波強度が変動しやすく通信に失敗する可能性があること、操作時に発生する限られた電力量で無線通信を行うため通信失敗時の再送信機能の搭載が難しいことから、信頼性の面で課題がある。
著者らは、ユーザと無線押ボタンスイッチの協調による信頼性の向上を目指し、無線の伝送状態(通信の成否や電波強度)をユーザに通知する「受信通知機能」を開発した。伝送状態を即座に把握できるようにしたことで、ユーザは通信が失敗した際に生産稼働率を低下させることなく再操作できるようになった。また、十分な電波強度が確保できる設置場所を容易に特定できるようになった。
本稿では、「受信通知機能」の概要と、それを実現するための技術的手法について述べる。
1. はじめに
市場ニーズの多様化に対応するため多くの製造業が多品種少量生産へ移行しており、生産ラインのレイアウト変更が頻繁に行われるようになっている。レイアウト変更にかかる工数の増加は生産稼働率の低下に直結しており、組み換えが容易な柔軟性の高い生産ラインが必要となっている1)。そのような背景から、配線作業が不要でレイアウトの自由度が高い無線通信の生産現場への普及が進んでいる。産業用ネットワークに関する調査によると、無線通信のシェアは2018年現在6% 程度であるが、IoT化の流れも受けて年率30%以上の高いペースで増加している2)。
生産現場で無線通信を行う制御機器の一つに、無線押ボタンスイッチ(以下、無線スイッチ)が挙げられる。従来の押ボタンスイッチでは図1(a)のように制御対象との間を有線で接続するのに対し、無線スイッチは図1(b)のように、無線信号を送信する子機と受信する親機の組み合わせで構成される。子機は信号線や電源線を必要としないため、生産ラインのレイアウト変更時の配線工数を低減できる。また、ユーザが子機を携帯して任意の位置から操作するなど、新しいアプリケーションへの応用も期待されている。一方で無線通信の特性上、通信が失敗する可能性をゼロにすることが難しいという問題がある。
著者らは無線スイッチの開発にあたり、無線スイッチにおける「信頼性」を「ユーザの意図通りの制御ができる能力」と定義した。そして信頼性を高めるべく、機器の性能とユーザビリティの両面から様々な検討を行ってきた。本稿ではその中から、無線の伝送状態を即座にユーザへ通知する機能について説明する。
まず第2章において、工場内の無線通信の問題点と、無線スイッチの信頼性向上を実現するために解決すべき課題について示す。第3章では課題解決のために開発した伝送状態の通知機能の概要と、それを実現するための3つの技術的検討項目について示す。さらに、第4章にて実際の生産現場での実験結果を示す。
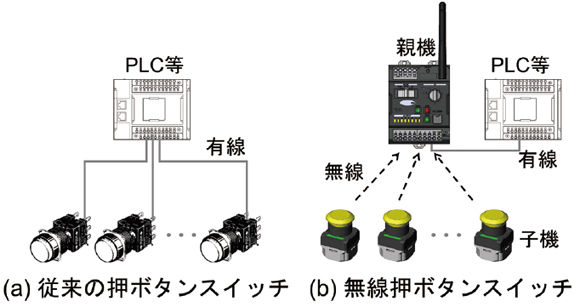
2.課題
2.1 工場における無線通信の問題
一般的に無線機器が発した電波は、回折や反射などの影響を受けながら空間中を伝搬していく。障害物やノイズが多いほどその現象は複雑化し、電波強度の変動や電波同士の干渉による通信障害が発生しやすくなる。特に閉空間かつ障害物の多い製造現場では、下記のような現象による通信障害への懸念が指摘されている3)。
・障害物による回折
・空間伝搬中の損失
・直接波と反射波による相互干渉(フェージング)
・他の無線システムが発する電波や工場外からの外来波との干渉
・生産設備からの放射ノイズ
これらは無線スイッチにおいても当てはまり、あらゆる環境で通信障害が発生する確率をゼロにするのは難しい。
2.2 発電量の制約の問題
無線スイッチ特有の問題点としては、電力量の制約が挙げられる。無線スイッチの子機は、電池式のものと、操作力を利用して発電する自己発電式に大別されるが、近年はエナジーハーベスティング技術の進歩4)によって電池交換を必要としない自己発電式が主流になっている。自己発電式の無線スイッチは一度の操作で使用できる電力量に制約があり、通信が失敗した際に自動的に信号を再送するリトライ機能を持たせるのが難しい。この点も無線スイッチの信頼性低下を招く要因となっている。
2.3 信頼性向上のための課題
2.1節、2.2節の問題はいずれも通信の信頼性に関わる内容であるが、現在の通信技術や発電技術では根本的な解決が難しい。しかし著者らは、ユーザの適切なオペレーションを促す仕組みを作り出すことでこれらの問題点を補うことができると考えた。
例えば何らかの理由で通信に失敗した際、ユーザがそれに気づいて即座に再操作することができれば、リトライ機能の代替手段として通信成功率を向上できる。またユーザが2.1節で述べたような現象を考慮し、通信障害が発生しにくい場所に無線スイッチを設置することによっても、通信成功率の向上が期待できる。
著者らはこのような特性を鑑み、通信の信頼性を最大化する手段として、ユーザと無線スイッチが一体となったオペレーション、すなわち人と機器の協調性の向上が有効であると考えた。そして、その実現のための課題として以下の2点を設定した。
・通信が成功したか否かの判別をしやすくすること
・通信に適した場所へ設置しやすくすること
これらの詳細を、それぞれ2.4節、2.5節で説明する。
2.4 通信成否の判別性向上
協調性向上のための課題の一つは、ユーザが通信の成否を判別しやすくすることである。障害物の多い生産現場では、図2のように制御対象が直接見えない場所から子機を操作することが考えられる。このとき、次のような問題が発生しうる。
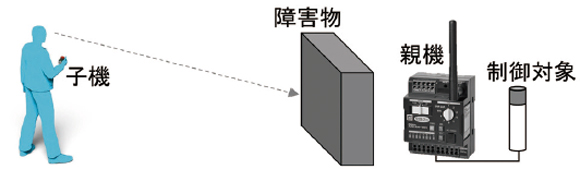
まずは何らかの原因で通信が失敗したケースを考える。このとき、ユーザは通信失敗に気づいて子機を再操作しなければならない。しかし制御対象が見えない場合や動き出しの遅いアプリケーションでは通信失敗に気づきにくく、再操作までに時間がかかってしまう。結果として生産の遅延や、無線スイッチが適用できるアプリケーションの限定につながってしまう。
反対に、通信が成功したことをユーザが認識できないケースも考えられる。この場合、既に制御が開始しているにも関わらず、ユーザがもう一度子機を操作してしまう可能性がある。アプリケーションによっては、このような重複した操作を受けても誤動作しないような対策が必要になる。
このように、リトライ機能をユーザの再操作で補う自己発電式の無線スイッチにおいて、通信成否の判別性向上は重要な課題であるといえる。
2.5 通信に適した場所への設置のしやすさ
もう一つの課題は、通信に適した場所へ設置しやすくすることである。安定した通信を行うためには、伝搬中に電波の減衰や干渉が発生しても一定以上の電波強度を保てるような位置に設置することが有効である。しかし、これを無線の専門知識を有さないユーザが適切に実施するのは容易ではない。例えば障害物が多く、電波が大きく減衰する場所に設置してしまうと、通信が頻繁に失敗し、信頼性の低下を招く。一方で親機と子機を近距離に設置するように制限を設けてしまうと、電波の減衰は軽減され通信成功率は高まるが、レイアウト設計の自由度が低下してしまう。適切な位置で無線スイッチを使用するには、設置時に位置を変えながら通信テストを繰り返さなければならず、さらに設置後の微調整が必要になる場合もある。このように、従来の無線スイッチでは設置場所の検討におけるユーザの負担が大きく、ユーザと機器の協調は十分とはいえない。また、設置場所の検討に要する時間が長くなれば、配線工数低減という無線スイッチの利点が失われてしまう。
3.受信通知機能の開発
3.1 受信通知機能の概要
2.4節、2.5節で述べた2つの課題は、①子機を操作する位置や制御対象によらず通信成否が確認できること、②通信時に十分な電波強度が確保できているかが分かることの2点によって解決できる。
そこで著者らは、子機に搭載したLEDによって伝送状態をユーザへ通知する「受信通知機能」を開発した。LEDを搭載した子機を図3に、動作イメージを図4に示す。
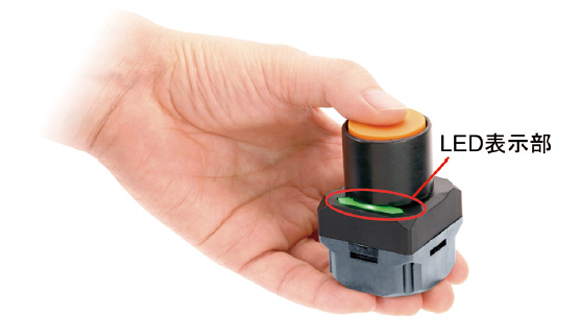
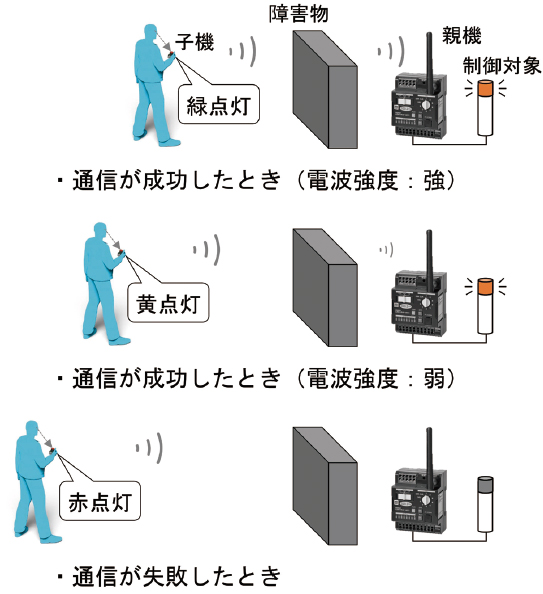
ユーザが子機を操作すると無線信号が送信され、その直後に子機のLED が点灯する。LED の点灯色は3色であり、通信成功し、かつ十分な電波強度が確保できている場合は緑色、通信成功したものの電波強度が弱い場合は黄色、そして通信失敗した場合は赤色が点灯する。ユーザはLEDを見ながら子機を操作することで、制御対象が見えない場合でもすぐに通信の成否を知ることが可能となる。通信に失敗した場合には赤色のLED が点灯するため、ユーザは即座に子機を再操作し、通信をリトライできる。また無線スイッチの設置場所を検討する際は、子機を何度か操作して緑色のLED が安定して点灯する領域内から選択すれば、レイアウト設計の自由度を損なうことなく高い通信成功率を確保できる。
このように受信通知機能は、ユーザと無線スイッチの協調性向上、ひいては信頼性向上に大きな改善効果が期待できる。さらに、これを電力量の制約のある自己発電型の無線スイッチで実現した点において、他に類を見ない技術であるといえる。
受信通知機能の実現のためには、新たにいくつかの技術や手法が必要になる。主要な検討項目とその概要を表1に示す。これらの詳細について、それぞれ3.2節~3.4節で述べる。
技術・手法 | 概要 |
---|---|
双方向通信処理フロー | 伝送状態を子機へ返信し、LEDの点灯色を決定する手段の考案 |
電波強度閾値の決定 | 緑色LEDと黄色LEDの点灯を切り替える電波強度の閾値決定 |
発電量の確保 | 双方向通信処理フローの動作に必要な電力量の確保手段 |
3.2 双方向通信処理フロー
従来の無線スイッチの処理フローを図5に示す。子機が操作されると親機への無線信号が送信され、親機が信号を受信すると制御出力をONするという単方向通信の処理フローである。
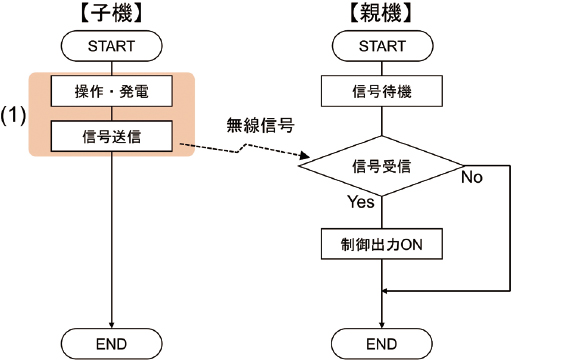
これに対し、3.1節のような受信通知機能実現のために著者らが開発した処理フローを図6に示す。本処理フローは、従来の子機から親機への通信に加えて、親機から子機への通信、LED制御という3段階かつ双方向通信の構成となっている5,6)。
ユーザが子機を操作すると、子機は内部で発電し、親機に向けた信号(SYN)を送信する。SYN送信後、子機は親機からの返信待ちの状態に移行する。親機はSYNを受信すると、その電波強度がある閾値以上か否かを判定する。その後、制御出力をONするとともに、子機に向けて受信確認信号(ACK)を送信する。なお、ACKにはSYNの電波強度の判定結果の情報(FLG)が含まれている。子機は受信したACKの強度を測定し、ACKとSYNの強度がともに閾値以上の場合は緑色のLEDを、そうでない場合は黄色のLEDを点灯する。一方、親機が子機のSYNを受信できなかった場合、当然ながら親機はACKを送信しない。返信待ちの状態が一定時間経過した子機は通信失敗と判定し、赤色のLEDを点灯する。
本処理フローは最小限のデータのやり取りで通信の成否と電波強度の判別が可能である。そのため通信プロトコルを単純化でき、低遅延かつ低消費電力での動作を実現している。3.4節で後述するが、電力量の制約がある子機に通知機能を搭載するにあたり、低消費電力であることは重要なポイントである。
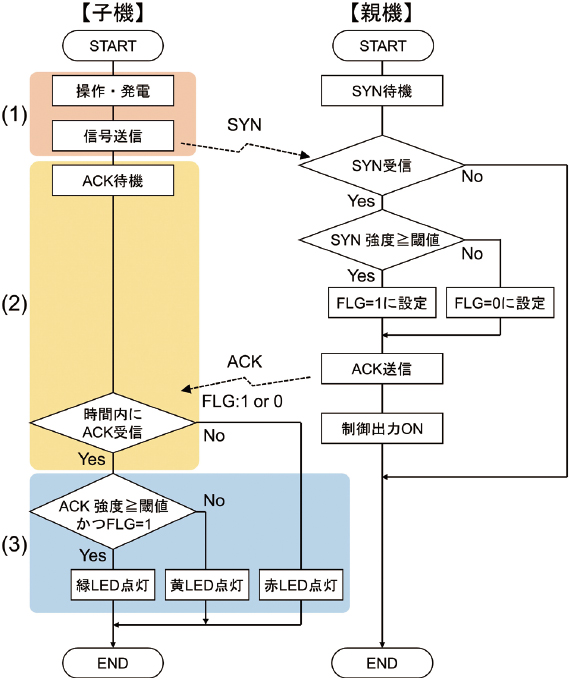
3.3 電波強度閾値の決定
先述の双方向通信処理フローにより、通信成功した際に電波強度が閾値以上か否かを通知することができるようになった。これを通信状態の良し悪しの指標として用いるためには、閾値(以下、Pth[dBm])をどこに定めるかが重要である。
親機が受信する電波強度の変動が極めて小さいとき、親機の通信成功率は図7のような傾向となる。Rminは製品仕様として要求される通信成功率、Pmin[dBm]はRminを維持するために必要な電波強度の最小値である。
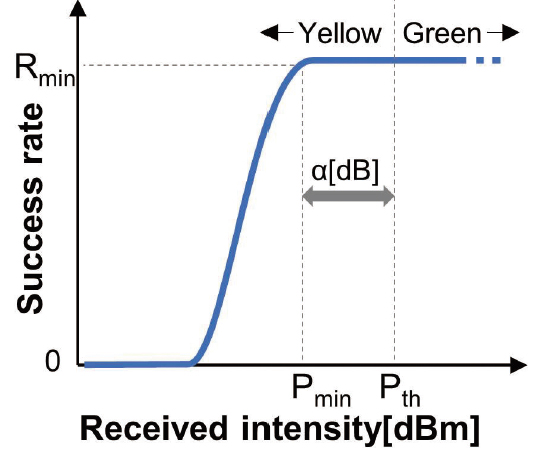
実際の生産現場では、親機が受信する電波強度は周囲の障害物などの影響によって絶えず変動する。そこで、工場内で発生する典型的な電波強度変動(特に減衰方向)のレベルをα[dB]とし、これを加味して次式のようにPthを設定すればよい。
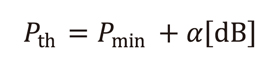
αの値は過去の研究事例を参考に決定する。文献7の実験結果によると、生産現場における電波強度の変動は次式の仲上-ライス分布fK(p)で表される。
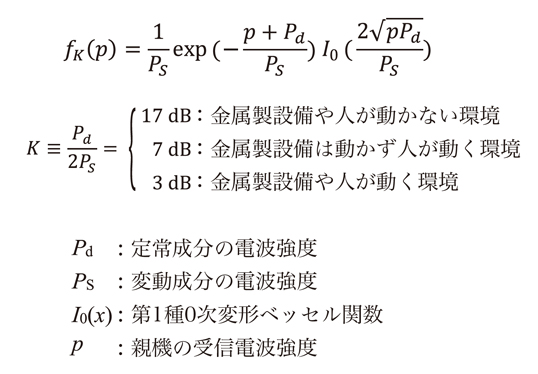
Kは定常成分と変動成分の比に相当するパラメータであり、値が小さいほど電波強度の変動は激しくなる。それぞれのKに対する分布関数fK(p)を図8に示す。Pavgは変動する受信電波強度の平均値である。
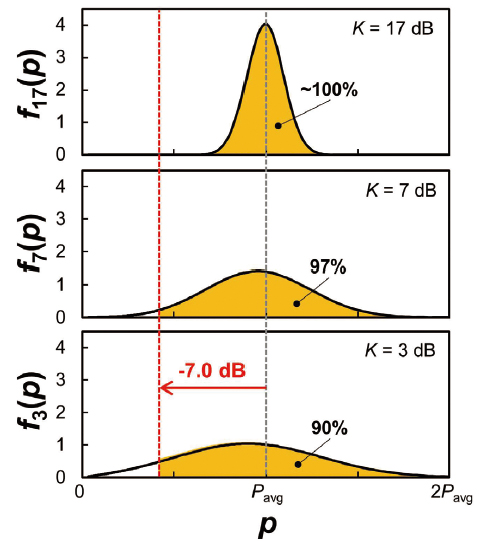
図8より、親機が受信する電波強度の変動のレベルはKの値、すなわち金属製設備や人の動きの有無によって大きく変わることが分かる。Pthの決定にあたり、最も厳しい条件(K=3dB)の変動をすべてカバーしようとすると、αの値を大きくとる必要がある。しかしその場合、通信成功率が高い条件でも黄色のLEDが頻繁に点灯してしまい、かえって実用性が損なわれてしまう。そこで、K=3dBの条件で90%の電波強度変動をカバーすることを目安にα=7dBとし、Pthを次式のように決定した。
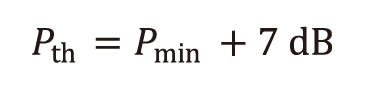
3.4 発電量の確保
3.2節で示した処理フローのうち、図6の(2)や(3)の動作は受信通知機能の追加によって新たに必要となったものである。これらに必要な電力量を、子機の発電によって確保しなければならない。まずは、処理フローの動作に最低限必要な電力量を実験により求めた結果を図9に示す。LEDが緑・黄・赤に点灯するときの消費電力量をそれぞれEG、EY、ERと定義し、測定は図6の(1)~(3)の3段階に分けて行っている。
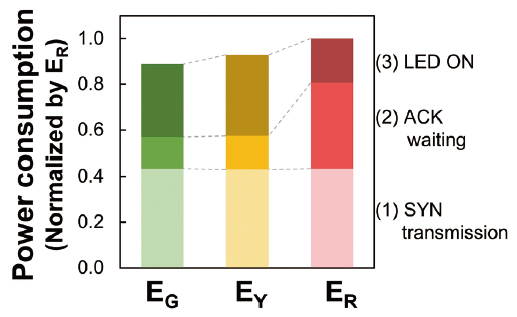
従来の無線スイッチに相当する(1)のみの場合と比べると、(2)と(3)の追加によって消費電力量が約2倍に増えていることが分かる。EG、EY、ERの比較でERが最も大きくなっているのは、赤色LEDが点灯する条件では(2)の状態をタイムアウトまで維持しなければならないためである。したがって、双方向通信処理フローを動作させるためには、発電する電力量がERを上回らなければならない。子機は発電モジュールを内蔵しており、電磁誘導により発電する。発電量はモジュールを押し込む速度に依存するため、操作部と発電モジュールが連動する単純な機構では必要な電力量が得られなかった。発電量を増加させるためには、内部構造で操作速度を増幅させる必要がある。そこで、非常停止用押ボタンスイッチの技術を応用し、図10のようなトリガアクション機構を考案した5,6)。
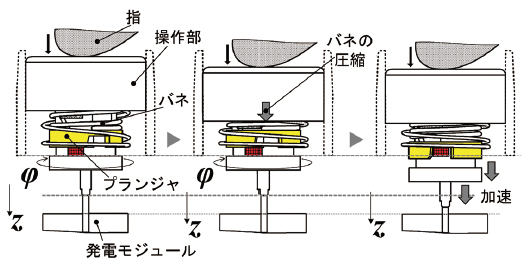
トリガアクションでは、z方向の操作力を一度φ方向の動きに変換する。ユーザが操作部をz方向に押し込むと、プランジャが内部の溝に沿ってφ方向へ回転する。一定の角度まで回転するとバネの力が解放されてプランジャがz方向へ飛び出す。飛び出し速度はバネの弾性で決まり、子機の操作速度によらず概ね一定となる。トリガアクションの有無による、発電量の差を測定した結果を図11に示す。横軸は操作部の操作速度、縦軸は発電量でありERで正規化している。すなわち、縦軸が1を超えると必要な電力量を満足していることになる。トリガアクションなしの場合、操作速度に応じて発電量が変動しているが、いずれの操作速度でもERに到達していない。それに対しトリガアクション搭載時は発電量が大幅に増加しており、操作速度によらずERを上回る電力量が得られている。トリガアクション機構の搭載によって、ユーザの押し方によらず受信通知機能に必要な電力量を確保できるようになった。これにより、自己発電方式の電池交換不要という利点と、受信通知機能による信頼性向上を両立することに成功している。
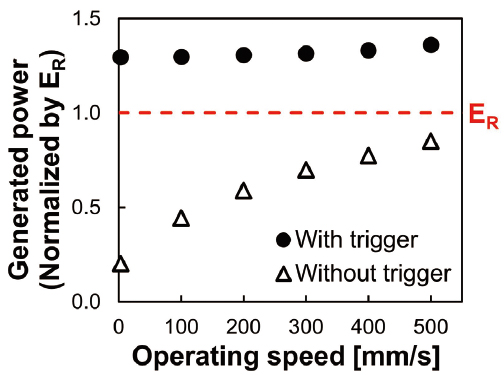
4.生産現場での検証結果
本章では稼働中の生産現場における、受信通知機能の検証結果を報告する。試験に使用した工場の概略図を図12、内観を図13に示す。電子機器の実装、組み立て用のラインが複数存在しており、生産設備や棚の高さは概ね1〜2m程度である。また製品を組み立てる自動機が稼働しており、人の移動も多いことから、無線通信環境は変動しやすい状態にある。
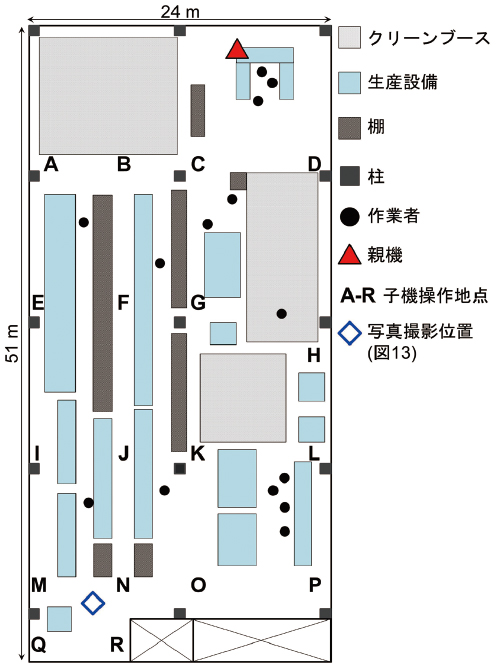
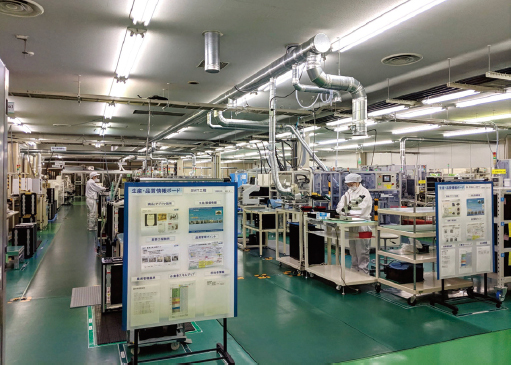
ここで、親機を図12に示す位置に設置し、地点A~Rのそれぞれで子機を20回ずつ操作した際に点灯するLEDの色の割合を確認した。実験条件を表2に、結果を図14に示す。
中心周波数 | 929.2 MHz |
---|---|
通信方式 | GFSK 単信通信方式 |
送信電力 | 0 dBm max. |
親機アンテナ利得 | 2 dBi |
親機設置高さ | 約1.2 m |
子機設置高さ | 約1.2 m |
子機操作方法 | 手動(操作間隔:約1 sec) |
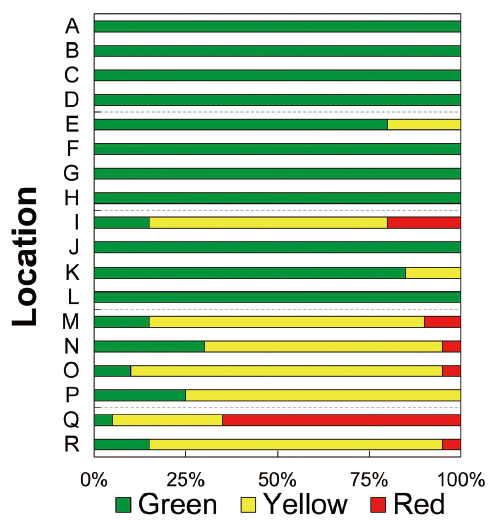
各地点のうちで親機が設置されたラインを見通せるのは、比較的障害物の少ない地点C、D、F、Gのみである。したがって受信通知機能がない従来の無線スイッチでは、上記4点以外から操作する際に通信の成否を目視で確認することが難しい。中でも地点I、M、N、O、Q、Rでは通信成功率が100%を下回っており、ユーザの再操作までに遅延が生じる可能性がある。しかし今回の受信通知機能を搭載した子機では、地点A〜Rのどの場所からでも即座に通信成否を確認できる。そのため、通信失敗した場合にもすぐに再操作することで通信をリトライでき、遅延を最小限に抑えることができる。
また、無線スイッチの子機の設置場所を検討する場合、緑色が常時点灯する地点A〜D、F〜H、J、Lの中から選択すれば、周囲環境による電波強度の変動があっても比較的高い通信成功率を維持することが期待される。それに対して地点Pでは、通信成功率は100%であるものの、過半数が黄色であり、電波強度の変動に対する余裕度が小さいことが分かる。そのため、通信失敗時の再操作を極力減らしたい場合は点Pへの設置は避けることが望ましい。このように、受信通知機能によってユーザは各地点での伝送状態を容易に確認することができ、アプリケーションに求められる通信成功率に応じて設置場所を選択することができるようになった。
本検証の結果から、2.3節で設定した「通信成否の判別のしにくさ」、「通信に適した設置場所の分かりにくさ」という2つの課題の改善が確認できた。人と無線スイッチの協調性向上が実現することで、信頼性の確保に大きく寄与していると考えられる。
5.むすび
本稿では無線スイッチの信頼性向上を目指し、ユーザとの協調性を向上する受信通知機能の概要および検討項目と、実際の生産現場における実験結果について示した。著者らが開発した無線スイッチでは本稿で述べた内容以外にも、機器自体の基本性能を高めることで通信の信頼性の最大化に取り組んでいる。今後は多様な環境下での無線機器の使われ方への知見を得て、より信頼性と自由度の高い無線スイッチの開発を目指していく。また、押ボタンスイッチ以外の制御機器の無線化についても検討し、よりレイアウト自由度の高い生産設備の実現に向けて取り組んでいく予定である。
最後に、今回の開発および本論文執筆にあたり多大なご協力をいただいた方々に、深く感謝申し上げる。
参考文献
- 1)
- 情報通信審議会 情報通信技術分科会 技術戦略委員会(第14回). 狭空間ワイヤレスプロジェクトの推進. 総務省.2017-2-27. http://www.soumu.go.jp/main_sosiki/joho_tsusin/policyreports/joho_tsusin/gijutsusenryaku/02tsushin03_04000245.html,(accessed 2019-1-11).
- 2)
- Michela Nalin. Industrial Ethernet is now bigger thanf ieldbuses. HMS Industrial Networks.2018-2-27.https://www.hms-networks.com/press/2018/02/27/industrial-ethernet-is-now-bigger-than-fieldbuses,(accessed 2018-12-12)
- 3)
- 板谷聡子. 無線通信技術を活用したスマート工場実現に向けて. 情報通信研究機構研究報告. 2017, vol. 63, no. 2, p.35-39.
- 4)
- Paul D. Mitcheson, et al. Energy Harvesting FromHuman and Machine Motion for Wireless ElectronicDevices. PROCEEDINGS OF THE IEEE. 2008, vol.96,no.9, p.1457-1486.
- 5)
- OMRON Corporation. WIRELESS SWITCH. U.S. Patent 2018/0158626A1. 2018-6-7.
- 6)
- OMRON Corporation. POWER GENERATION APPARATUSAND WIRELESS SWITCH. U.S. Patent 2018/0156632A1.2018-6-7.
- 7)
- 小澤尚志、藤本卓也、片山正昭. 工場における高信頼性制御無線実現にむけた電波伝搬特性の測定とモデル化. 信学技報, 2015, vol. 115, no. 366, p191-196.
本文に掲載の商品の名称は、各社が商標としている場合があります。