AOIとマウンタの連携による故障予兆検知システムQ-upAuto
- リアルタイム異常検知
- 不良未然防止
- 品質管理
- SMT
- はんだ検査装置
近年、プリント実装基板の実装現場には、ますます高い品質とコスト競争力が要求されてきており、できるだけ人のスキルや工数を必要としない、自律的に高い品質を維持する生産ラインが求められている。
オムロン株式会社 検査システム事業部では、従来からプリント実装基板を3D計測し、定量化された品質基準に従って検査を行うAOIを販売しており、多くの生産現場で、不良流出防止に貢献している。
さらに不良を作らない生産ライン作りに貢献するため、AOI(Automated Optical Inspection)とチップマウンタを連携させ、生産工程の異常や故障の予兆を、リアルタイムかつ自動的に捉え、是正のための情報を提供するM2Mシステム、Q-upAutoを開発した。
このシステムを量産フィールドに導入し、品質維持改善の効果が得られた。
1. まえがき
近年、自動車の安全設備やハイブリッド車の普及が急速に進み、自動車に搭載される電子部品基板が急速に増加している。自動車に搭載される部品には高い品質が求められるため、プリント実装基板の実装ラインは不良を流出させないだけでなく、手直しで良品とすることも禁じられる場合があり、不良を作らないことが必要になっている。
また、豊富な経験と知識を持つ熟練した実装ライン担当者、製造技術者の高齢化が進み、高い品質を達成し維持する人材がこの10年に渡り減少し続けている。そういった人材が確保できている現場においても、コスト競争力が求められるため、改善に多くの工数を使うことができない。また業界のグローバル化が進み、海外拠点の支援のため不在となることも多く、品質の維持向上の取り組みが難しい状況である。
従来より、検査システム事業部ではQ-upNaviという品質管理システムを販売している。これは、SPI(Solder Paste Inspection/はんだ印刷検査機)、マウント後AOI(外観検査機)、リフロ後AOIの検査情報を蓄積し、SPIやAOIごと、および製品ごとの不良発生状況を集計するパレート(図1)、不良の原因を分析するために、各工程の画像や計測値などを確認できる工程照合(図2)といった機能を備えている。
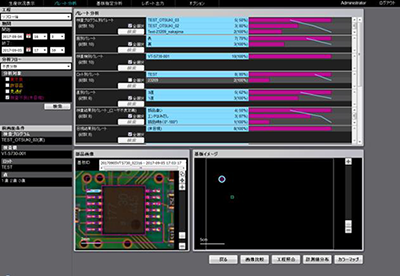
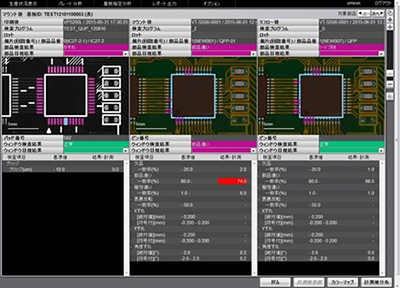
しかし、検査情報は不良が発生した後の状態を確認できるだけであり、不良の原因は、画像などからユーザが推定したり、実装ラインに立ち会って調査する必要がある。前述の通り、そういった分析ができる人材は少ない上に時間をかけられないので、品質改善を進めることが難しい。しかも、不良が発生してからの取り組みとなるので、不良を未然に防ぐことはできない。
こういった状況を踏まえ、さらに多くの情報収集と分析、監視を自動化した、極めて少ないユーザの作業時間で、不良の発生原因を突き止め、さらには未然防止するシステムQ-upAutoの開発を行っている。その第1弾として、マウント工程をターゲットとした商品を開発した。2017年より限定リリースとしていくつかの量産フィールドでの運用を開始し、2018年より正式リリースとなった。
これまでのフィールドでの取り組みにおいて、品質維持改善の効果が得られたので、Q-upAutoの仕組みと効果を紹介する。
2. 背景
2.1 マウント工程の不良原因
プリント実装基板の実装工程は次のように構成される。先頭から、はんだ印刷機、SPI、チップマウンタ(以降マウンタと呼ぶ)、マウント後AOI、リフロ炉、リフロ後AOIが並ぶ。それらの装置は図3のように一直線に配置され、上流から下流(この図の場合左から右)にプリント配線板(以降基板と呼ぶ)を流しながら実装を行う。はんだ印刷機は基板にステンシル状の金属板を介してはんだを印刷し、SPIは印刷されたはんだの印刷状態を検査する。マウンタはそのはんだの上に電子部品を搭載し、マウント後AOIはその部品の搭載状態を検査する。リフロ炉は部品を実装した基板を加熱してはんだを溶融させ、基板を冷却させることではんだを硬化させて電子部品を基板に固定する。リフロ後AOIは、このようにして実装された完成品を検査する。
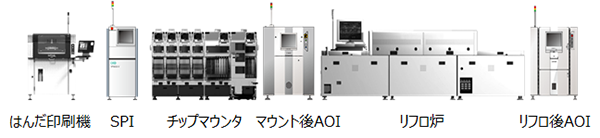
マウンタは電子部品を基板の上に搭載する装置である。実装品質に最も関わりのある、電子部品を実装する機構は次のようになっている。マウンタの構造を図4に示す。
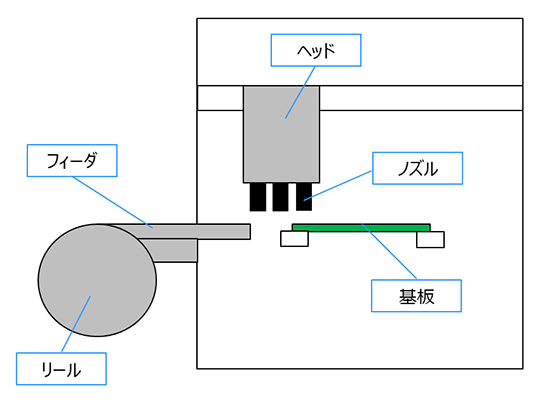
まず電子部品は、フィーダで供給される。フィーダはテープに装填された電子部品を巻いたリールを装着するもので、ここから1つずつ電子部品を送り出しながら供給していくものである。この電子部品を送り出す部分が消耗すると、部品の供給位置がばらつき、実装品質を低下させる要因になる。
次に、電子部品はノズルで吸着され、部品チェックを経て、しかるべき基板上の位置に運ばれ、基板に装着される(図5)。
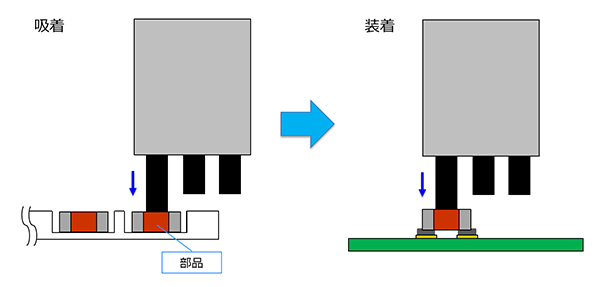
電子部品はノズルとの接触部分を真空にすることでノズルに吸着される。ノズルには多数の種類があり、電子部品に対してノズルの選択が不適切だったり、消耗によって真空を作る機構の動きが悪くなると、真空が保てなくなり、電子部品を落下させたり、吸着位置がずれたりして、不良を発生させる原因となる。
このノズルは、ヘッドに取り付けられており、ヘッドが上下したり水平移動したりすることによって、電子部品の吸着、チェック、装着が行われる。1つのヘッドには同時に10個程度のノズルが取り付けられる。ヘッドが消耗すると真空圧の低下や、電子部品吸着、装着のためにノズルを押し下げる位置がばらつきによって電子部品の姿勢が不安定になるため、不良の原因となる。
これらフィーダ、ノズル、ヘッドについては、消耗だけでなく、電子部品を吸着する座標、装着する座標、電子部品の高さ、電子部品の形状モデルなど、それぞれに対して設定される実装パラメータがあり、それらが不適切な場合に、不良の原因となる。
製造設備の技術革新により、実装品質自体は以前よりも向上している。とはいえ、例えばマウンタにおいては大量の部品を高速で実装するため、実装用の機構の消耗が激しく、実装不良を引き起こす。さらに、電子部品や基板などの材料の品質ばらつきが多いため、しばしば実装条件の調整が必要になる。そのため、マウント工程では、生産量にもよるが、1ライン、1日あたり実装不良が数個~数10個発生しており、品質維持改善の取り組みが依然として必要である。
2.2 マウント工程の従来の不良再発防止方法
マウント後AOI、リフロ後AOIを活用することで、どの機種のどの位置で不良が発生したか、不良になった電子部品がどういう部品品番であるかを確認することができる。また、パレート図などQC7つ道具などを活用することで、不良が発生しやすい部品品番や位置を確認することができる。しかし、前項で説明したような、マウンタの不良原因を突き止めることはできない。
また、マウンタにも不良予防、および不良原因分析のための集計機能が備わっており、ノズルやフィーダの使用回数や、吸着ミスなどの実装エラーの累積回数を確認できる。これを利用して、消耗していると思われるノズルやフィーダを選択し、使用回数の多いもののメンテナンスや交換をすることができる。しかし、実際にそれらが不良を実装したノズルやフィーダかどうかは、確認することができないため、必要のないメンテナンスを行う、不良原因であるノズルやフィーダを見逃し、不良を再発させる、という可能性がある。
通常、1枚の基板を実装するために、複数のマウンタを1ラインに並べて設置し、それぞれのマウンタで別々の電子部品を実装する。これは1台のマウンタに装着できるフィーダ数に限りがあることと、ラインタクトを短くするためである。また、同一部品品番の部品であっても、使用する個数が多い場合は、複数のフィーダで供給したり、複数のノズルで同時に吸着、装着することで、ラインタクトを短縮するのが一般的である。さらに吸着ミスなどの実装エラーが発生すると実装リトライを行うので、通常と異なるフィーダやノズルが使用される。
不良の原因を突き止めるには、発生した不良がどのマウンタのどのヘッド、ノズル、フィーダで実装されたかを特定する必要がある。しかし、AOI から得られる情報とマウンタから得られる情報は独立しており、それぞれから情報を引き出して照合する必要がある。通常は、単純に部品品番や基板上の位置から特定することはできず、基板1枚1枚の実装情報を保存しておき、基板に刻印されたシリアル番号と個片番号、回路番号を照合する必要があり、多くの手間を必要とする。現実には、それだけの時間をかけられないため、このような作業を行うのは困難であるし、仮にできたとしても、時間が経過し生産している機種が変わり、マウンタに装着されたフィーダやノズルが入れ替わっていたりするため、処置ができないといった問題がある。
2.3 マウント工程の従来の不良未然防止方法
不良を未然に防ぐには、不良になる前の品質の変動をリアルタイムに監視し、不良の予兆を検知したら速やかに製造設備に対して処置を行う必要がある。品質の変動を捉えるにはAOIの情報を利用するが、単に良不良を判別するだけのAOIでは、不良になる前の情報を得ることはできない。オムロン製AOI(例えばVT-S730、VT-S530)はワークの位置、姿勢、はんだ付け状態といった品質評価項目を定量化して計測した上で、数値で定義された品質基準に従って、合否の判定を行っている。数値化された品質基準としてはIPC-A-610 1)が業界でよく用いられるが、ユーザごとにさらに品質評価や検討を行い、固有の検査基準を設定することも多い。
ところで、品質とはプリント基板に形成されたランドと電子部品の電極の接合状態で評価されるものである(図6) 2)。プリント基板のフィデューシャルマークとCADで指定された座標から計算される位置に正確に電子部品が実装されたとしても、プリント基板の反りや歪み、製造時に発生するランドのずれがあるため、そこにCADデータ通りにランドが存在するとは限らない。オムロン製AOIは、基板ごとにランド位置を抽出した上で、電子部品の電極との位置関係を計測するため、実装品質を正確に計測することができる。
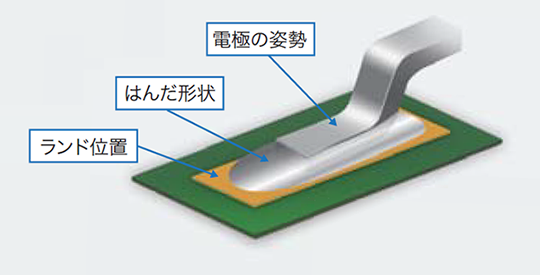
不良になる前の品質変動を捉えるには、単に品質評価項目が数値化されるだけではなく、良品から不良の間で変化するワークの状態を物理的に計測した、不良との近さに比例した数値である必要がある。AOIで撮像された画像に対し、設定された明るさや色に合致した画素の数や割合を数値化するといった従来のAOIでは、こういった計測はできない。
品質変動を監視する手法としては、管理図 3)がある。これは、数十個以上のワークを計測した計測値に統計処理を行い、ばらつきや平均のずれを品質基準に照らし合わせて、不良が発生する可能性のある状態を検知するものである。しかしこの手法は非常に計算量が多く、全ての基板、電子部品に対して実施するには多くのコンピュータリソースが必要である。さらに、製造設備の情報がないため、品質が低下したことしかわからず、不良未然防止のための対策を行うには役に立たない。そのため、電子基板実装工程では、ほとんど利用されていない。
3. 目的
こういった従来方法の問題点を解決し、従来実施できなかった不良再発防止、不良未然防止が、製造技術者やラインオペレータの手を必要とせずに、リアルタイムに行える実装ラインを実現することが目的である。最終的にはマウンタへの処置も自動化し、自律的に良品を生産できるようにすることを目指すが、今回は、不良を発生させる可能性のあるヘッドやノズル、フィーダを自動で特定し、是正するための情報を提供する機能を開発した。
4. 課題と解決方法
1つ目の課題は、検査情報とマウンタの実装情報の紐付けである。マウンタから必要な情報を取得するためのインタフェースを設計し、マウンタメーカと提携し情報を取得できるようにした。これによって、すべての基板のすべての電子部品について、基板のシリアル番号と個片番号、回路番号ごとに、実装を行ったマウンタ名、ヘッドID、ノズルID、フィーダID(以降これら3つをまとめてマウンタデバイスID と呼ぶ)と、それらが装着されている位置が取得できる。これらの情報を各マウンタが実装を完了した直後に取得し、リアルタイム処理ができるようにする。検査結果との紐付けは、基板のシリアル番号と個片番号、回路番号を用いる(図7)。
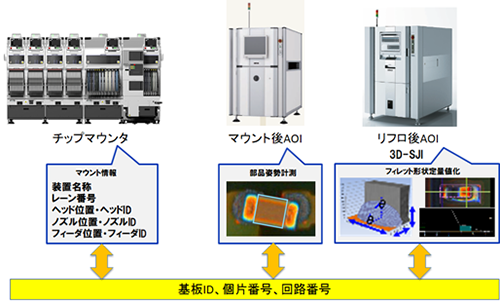
2つ目の課題は、マウント工程の不良原因や不良予兆に対してのみ検知、通知を行うことである。マウント工程以外の印刷工程、リフロ工程に原因がある場合に、マウント工程への処置を行うと、無駄なコストが発生してしまう。これについては、まずマウント工程に原因があることで発生する不良種別、および品質低下が発生する計測項目に監視対象を絞る。さらに、マウンタデバイスIDごとに品質の観測を行うことで、マウント工程の要因による品質変動を的確に観測できる。一方、印刷工程やリフロ工程の要因は、影響が及ぶ範囲がマウンタデバイスとは異なるので、特定のマウンタデバイスIDの品質低下に寄与する割合が低くなり、虚報となる可能性が低くなる。例えば印刷工程では基板上の特定の位置ではんだ体積が過多または過少となることが多いが、ノズルはそれらが実装する電子部品が決まっており、それらの位置は基板上に散らばっているので、印刷工程とは影響が異なる。
不良の再発防止については、マウンタデバイスIDごとに、不良部品の実装を行った回数を集計し、ヘッド、ノズル、フィーダごとに回数の多い順にマウンタデバイスIDと回数を通知する、不良通知機能を設けた(図8)。マウンタごとに集計結果を表示するようになっており、不良が発生した時にそのマウンタ集計結果に切り替わる。左側にマウンタ名が一覧表示されており、不良が発生したマウンタは赤色表示され、マウンタ名を選択することで表示を切り替えられる。
集計の対象は、マウント工程に不良原因がある、欠品、部品違い、極性違い、Xずれ、Yずれ、角度ずれ、電極サイドはみ出し、電極エンドはみ出し、部品浮き、部品傾きである。また、表示したマウンタデバイスIDはそれが装着されているマウンタ名、マウンタモジュール、ノズルがセットされたノズルピット番号、フィーダが装着されたステージ上の位置を表示する。これによって、不良発生が集中しているマウンタデバイスID と、それがどこに装着されているかが調査なしでわかるため、速やかに処置を行うことができる。
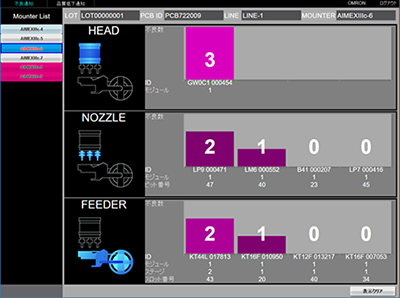
不良の未然防止については、ヘッドID、ノズルID、フィーダIDごとに、それらが実装したすべての電子部品について、計測項目ごとに工程能力指数を算出し、工程能力指数が低下したマウンタデバイスIDを通知し、工程能力指数の推移をグラフ表示する、品質低下通知機能を設けた(図9)。計測項目は、不良になる前の部品位置、姿勢が計測できる、Xずれ、Yずれ、角度ずれ、電極サイドはみ出し、電極エンドはみ出し、部品浮き、部品傾きである。こちらも、速やかに処置ができるように、マウンタデバイスIDの装着位置を表示する。下段には過去の通知のリストがあり、選択することで過去の通知の内容を上部に表示し、確認することができる。
不良原因としてはマウンタデバイスの消耗以外にも、部品品番ごとの実装パラメータが不適切である場合がある。実装パラメータの多くは、部品品番ごとに設定されるので、マウンタデバイスIDと部品品番の組み合わせごとの工程能力指数の低い順に、部品品番をリスト表示する。これにより、特定のマウンタデバイスIDと部品品番の組み合わせだけで品質が低下しているのか、部品品番に関わらず品質が低下しているのかを切り分けられるようにした。これにより、マウンタデバイスのメンテナンスや交換を行うべきか、実装パラメータの変更を行うべきかが判断できる。
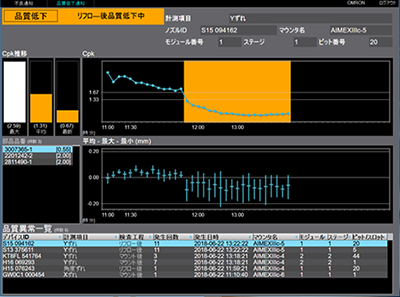
不良予兆を検知する方法としては、連続20枚の基板の工程能力指数の平均値が、しきい値を下回った時に不良予兆が発生したと判断するようにした。これは、不良予兆の検知方法をブラックボックス化せずに、ユーザが理解し説明できる方法とするためである。特に車載業界においては、品質マネジメントシステムの国際規格IATF16949 4)で、工程能力指数などの統計的手法を用いたプロセスの監視、測定および分析が要求されており、標準的な手法を採用する必要がある。
マウンタデバイスIDごとの工程能力指数だけでは処置内容を決定するには不十分である。工程能力指数は、ばらつきが増えた時も平均値がシフトした時も低下するため、どちらの現象が起こったのかが確認できない。これに対しては、Xbar-R管理図の手法を利用し、平均値とバラツキの推移を確認できるようにした。部品品番を選択すると、計測値の平均値、最大値、最小値の推移グラフが表示されるようにした(初期状態では、最も工程能力指数が低い部品品番が選択される)。このグラフには検査基準も表示される。計測値の分布の推移が確認できることで、不良にどれくらい近いのか、平均値がどちらにシフトしているのか、あるいは平均が変わらずにばらつきが大きくなったのか、といった現象や、その現象が突発的であるか継続的であるかが把握でき、処置内容が決定できるようになる。
例えばXずれやYずれの平均値が継続的にシフトしている場合は、実装位置がずれていることが原因であるので、実装位置パラメータを修正する、平均値のシフトがなくばらつきが徐々に大きくなっている場合は、マウンタデバイスの消耗が原因であるので、マウンタデバイスのメンテナンスを行う、といった処置を行う。
なお、上記2つの機能は、マウント後の計測値、リフロ後の計測値の両方を対象とする。ワークがリフロ炉に搬入され、はんだが溶ける時に電子部品が移動するため、マウント後とリフロ後では部品姿勢が変化する。多くの場合はセルフアライメント現象によりずれ量が小さくなる方向に変化するが、よりずれ量が大きくなる場合もある。そのため、両方の工程で監視を行う必要がある。リフロ後は、ワークが製品として出荷される状態であるので、製品の品質を直接計測したものになる。したがって、より緊急性、重要性が高い不良予兆を検知できる。一方マウント後では、マウンタが電子部品を装着した状態を直接計測できるので、不良原因の影響が顕著に現れる。マウント後の品質が低下していても、リフロ後では処置が必要なほど品質が低下するとは限らないので、緊急性、重要性が低い不良予兆も検知するため、予防保全的な意味合いも含まれる。
5. 結果
量産ラインにQ-upAuto を導入し、品質維持改善の効果が得られた事例をいくつか紹介する。
1つ目はノズルの型式変更の事例である。あるノズルIDで不良予兆が検知されたが(図10)、同じ部品品番について、他のノズルIDでも不良予兆が検知された(図11)。複数のノズルIDで品質が低下しているため、部品品番とノズルの型式が不適切であると考えられる。処置としては、ノズルの型式の変更を行った。変更前は、この部品品番の不良率が1.00%であったが、変更後は0.00%となった(表1)
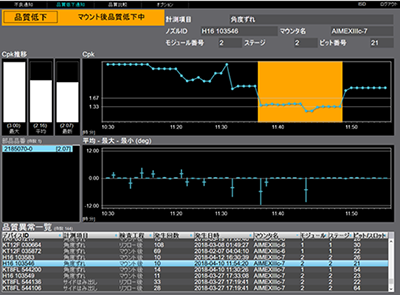
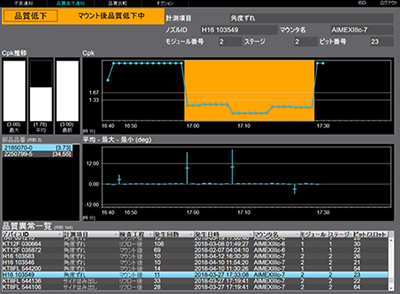
処置前 | 処置後 | |
---|---|---|
検査部品数 | 5620 | 5662 |
不良数 | 56 | 0 |
不良率 | 1.00% | 0.00% |
2つ目はノズルのメンテナンスの事例である。あるノズルIDで不良予兆が検知された(図12)。ノズルの動作を手で確認したところ、摺動動作に違和感があったため、ノズルチェック装置でテストしたところ、エラーとなった。メンテナンスを実施し、ラインに戻した。この事例では不良は発生していないが、検査基準に近いXずれが発生していた。また、459枚の基板を実装する間に、37回の吸着エラーが発生していた。1台のマウンタには数10個のノズルがセットされており、1つ1つテストする手間をかけることなく、メンテナンスを要するノズルを見つけ出すことができた。
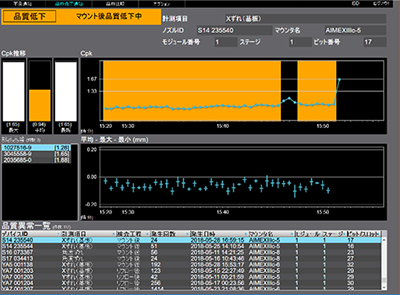
最後は、継続的な部品ずれを検知した事例である。マウント後のXずれで継続的に不良予兆が検知された(図13)。グラフを確認すると、工程能力指数が1.0を下回る状態が継続しており、Xずれの計測値の平均は-X方向に100~200μm程度シフトしていた。最小値は検査基準までにまだ余裕があり、処置は行わなかったが、検査基準に近い場合は、部品実装座標を修正する必要がある。
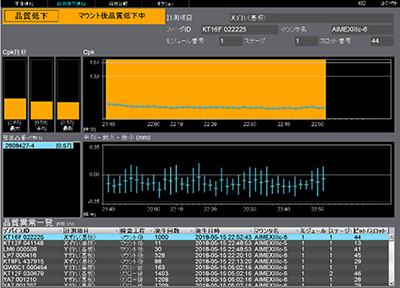
このように、Q-upAutoを導入することで、製造技術者やオペレータなどの工数を使うことなく、実装パラメータが不適切な状況やメンテナンスが必要な状況など、不良が発生する可能性が高い状況を検知し、何に対して是正を行えばよいかがわかるようになる。また、従来、こういった検知を行うには大きな工数と時間が必要であり、リアルタイムには実施できなかったことが実施できるようになるため、不良が発生する前に是正処置を行い、品質の維持向上ができるようになるといえる。
6. むすび
今回、AOIの検査データとマウンタの実装データを活用した不良予兆検知システムQ-upAutoを開発し、実際の生産ラインで品質維持改善の効果を確認できた。
今後は、印刷機、リフロ炉も対象としてSMT(Surface Mount Technology)ライン全体の監視を行うとともに、不良予兆の検知結果を元にマウンタなどの製造設備への自動フィードバックを行うようにし、より人手やスキルを必要とせずに、より高い品質を実現するシステムに進化させていく予定である。
最後に、今回の開発及び効果検証に多大なご協力をいただいた検査システム事業部の方々、生産現場の方々に、深く感謝申し上げます。
参考文献
- 1)
- Institute for Interconnecting Packaging Electronics Circuits. Acceptability of Electronic Assemblies. IPCA-610G. October 2017
- 2)
- 杉山 俊幸, 岸本 真由子, 藤井 心平, 杉田 信治. SJI(Solder-Joint-Inspection)30年と3D技術で解決すること. エレクトロニクス実装学会 第31回春季講演大会, 2017.
- 3)
- 永田 靖, 棟近 雅彦. 工程能力指数 実践方法とその理論. 日本規格協会, p.41
- 4)
- International Automotive Task Force. IATF 16949:2016. October 2016