マシンコントローラに搭載可能なAI技術の開発(1)
- AI技術
- リアルタイム異常検知
- 設備保全
- PLC
- 機械学習アルゴリズム
AI・IoT・ビッグデータが、これまで人の経験・ノウハウに依存してきた製造現場の生産管理や設備保全を変えようとしている。熟練者は、現場の装置の挙動を五感で常に感じ取ることで生産設備の「いつもと異なる状態」を察知し、経験や知識をもとに速やかな対策を行っている。そのため、現場熟練者と同じような設備の目利きを可能にするためには、現場で高速に動作する装置の動きを十分に捉えることができる高頻度で計測されたデータの解析が必要になる。本稿では、装置を制御するコントローラから取得できる制御データを活用した生産設備の異常検知手法を提案する。また、提案手法によるデータ解析結果に基づいてコントローラがリアルタイムに異常を検知できることを、実験用包装機を用いて実証する。
1. まえがき
少子高齢化の影響により、我が国における生産年齢人口の割合は年々減少を続けている。総務省の国勢調査によると、生産年齢人口比率は1995年をピークに減少に転じており、将来的な労働力不足が懸念される。ドイツなどの経済大国でもこの傾向は共通しており、今後、世界共通の課題になると予想される。また、世界の工場としての役割を担う中国やその他新興国の人件費も高騰が続いており、労働力の確保はますます難しくなっている。このような状況のもと、製造分野においては、AI (Artificial Intelligence)やIoT (Internet of Things)を活用した省人化の動きが加速しており、特に生産管理や設備保全などの業務に対して技術導入が盛んに検討されている 1)- 3)。
最新の製造現場においては、IoTによって膨大な量の制御データがクラウドに収集され、ビッグデータ分析による生産性の改善を狙う商品・サービスが導入されはじめている。これらを活用することで、日次レベルの生産改善に対して有効な生産管理や設備保全が可能となり、生産ラインの稼働率向上が期待できる。一方で、保全ノウハウの多くは未だ現場に常駐する熟練者の勘や経験に強く依存している。熟練者は、現場の装置の挙動を常に五感で感じ取ることで生産設備の「いつもと異なる状態」を察知し、過去の経験や知識をもとにその異常現象の要因を推定することで速やかな対策立案・実行を行っている。そのため、データに基づいた保全の質のさらなる向上には、少なくとも現場で動作する設備の挙動を十分に捉えられるサンプリング周期(例えば、ミリ秒周期)でデータを収集し、その解析結果を作業者にリアルタイムにフィードバックする必要があると考えられる。そこで我々は、生産設備の制御に用いられる産業用コントローラに着目し、非熟練者であっても熟練者と同等の設備の目利きを可能とすべく、設備の制御周期で高速・高精度に収集される制御機器の入出力情報を活用した異常検知手法について検討を行った。
本稿では、周期的に繰り返し生産を行う製造装置を対象に、装置を制御するコントローラから取得できる制御データを活用した異常検知手法を提案する。また、提案手法によるデータ解析結果に基づいてプログラムされたコントローラがリアルタイムに異常を検知できることを、実験用に準備した包装機を用いて実証する。
2. 課題
製造現場において用いられる代表的なコントローラであるPLC (Programmable Logic Controller)は、生産ラインの自動化に使われていた電磁リレーの置き換えのために誕生した。PLCはプログラムによってあらかじめ定められた順序に従い制御を行うシーケンス制御を主に実行するが、最近はモーション制御やネットワーク通信の機能を備えるなど高機能化が進み、製造現場情報と上位の生産管理システムとのインタフェースとしての役割も果たしている。この種のコントローラは、リレー接点のON/OFFやサーボモータのトルクなど生産設備を構成する様々な制御機器の入出力情報(以後、制御データとよぶ)を数100 µsから数msのサイクルで収集できる。
コントローラで収集できる制御データを活用することで次のような利点が考えられる。
- 新たにセンサを設置せずとも制御に活用されているセンサ、サーボモータなどの機器の装置挙動の変化を捉えることが可能
- クラウドのサブシステムとしてコントローラをとらえたとき、データの解析方法(前処理や装置異常の検知方法など)を事前にプログラミングしておけば、全てのデータを上位システムに送る必要がなくなり、通信負荷を軽減させることが可能
これらの価値を実現するために、我々は次の2つを解決すべき課題と置いた。
- 装置単位で異常を捉えるためのデータ解析
- コントローラ上でのデータ解析の実行
次章からはこの2つの課題を解決するための方法論について述べる。
3. 技術内容
3.1 包装機
3.2節以降の説明のため、はじめに実験用包装機について紹介する。本稿で取り扱う包装機は、樹脂製フィルムによって製品を枕状に包装する横型ピロー包装機である。図1に示すシステム構成のとおり、この包装機は4つのサーボモータと3つのファイバセンサから構成されており、これらを用いてコントローラが巧みな制御を行うことで包装を自動化している。本包装機では、ワーク搬入工程、センタシール工程、エンドシール工程の3工程を経ることでワークを枕状に包装する。
4つサーボモータそれぞれのトルク・速度・位置と3つのファイバセンサの論理信号の計15個の信号は、包装機を制御するコントローラにフィールドバスを介して一定周期で収集される。収集されたデータの一例として、トップシール軸のトルク・速度・位置とワーク検知センサの論理信号を図2に示す。これらのデータの挙動を見ると、およそ1秒間隔の周期性をもつことが分かる。これは、包装機が毎秒1個の速度でワークを包装しているためである。
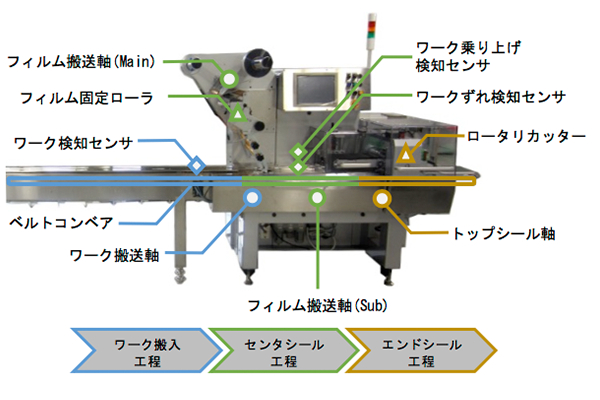
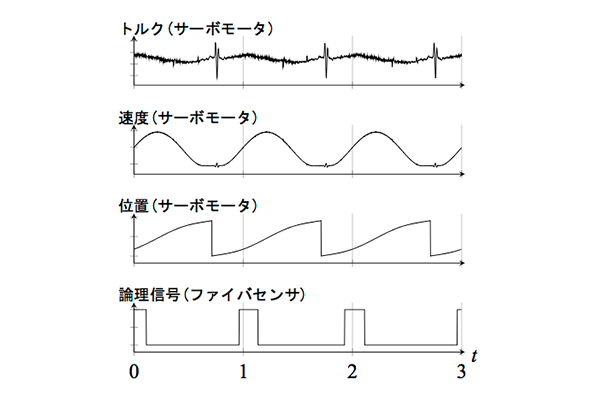
3.2 制御データを用いた生産設備の異常検知
2章で述べた2つの課題を解決するために、我々はコントローラへの機械学習アルゴリズムの導入を検討した。高い信頼性が要求される工場現場では、推定結果が得られた理由についての説明性の高さが重要となる。そこで本提案手法では、コントローラで異常検知を運用する前に、アルゴリズムで使用する特徴量をデータ解析で決定しておき、どの特徴を用いて異常検知が実行されるかを明確化することで推定結果の説明性を担保する。また、計算リソースの少ない既存のコントローラでもリアルタイムに異常検知を実行可能にするため、運用時に計算コストが低い手法を外れ値検知アルゴリズムとして採用する。
提案手法の概念図を図3に示す。具体的には次のような手順で制御データを用いた異常検知を実現する。
- 制御データを収集し、特徴抽出・選択、外れ値検知を行うことによってオフラインで異常を検知(パラメータ算出)
- データ解析で得られた結果(見るべき特徴量と閾値)をコントローラにパラメータとして与え、コントローラでリアルタイム異常検知を運用
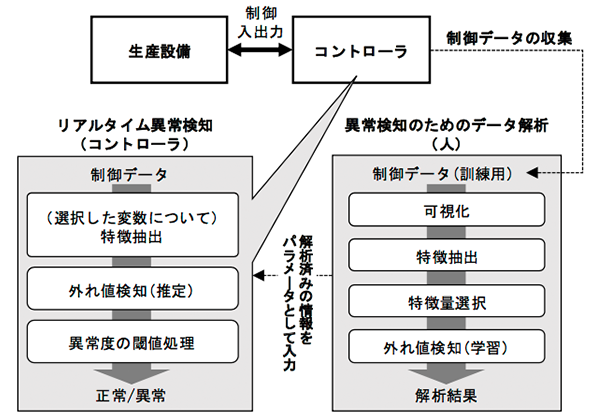
3.3 可視化
人が現状を把握するために、コントローラのデータを用いて最初に行うのは可視化である。正しくデータが取得できているか確認する。
3.4 特徴抽出
本稿では、生産設備の繰り返し動作の区間をフレームと呼ぶ。前述の包装機を例に挙げると、一つのワークが包装される1秒の区間が一つのフレームに相当する。本提案手法では、制御データをフレームごとに区切って特徴量を算出する。また、データが連続値をとる場合とONとOFFの二値の論理値をとる場合で、それぞれ別の特徴量を用いる。次にその特徴量について説明する。
ある制御データの i 番目のフレームのデータを

とおく。ここで、n はトルクや速度といった制御データの種別、Ni はフレーム i のデータ総数を意味する。なお、フレーム i の開始時刻をとすると、フレーム i の j 番目のデータXn(i, j)が取得された時刻ti,j は、

と表すことができる。ここで、δt は制御データのサンプリング周期である。
Xn(i,j)が連続値をとる場合の特徴量算出の概念を図4に示す。この特徴量算出は、フレームごとの分布の変化を統計的な特徴としてとらえるものである。以下に連続値についての特徴量の算出式を示す。
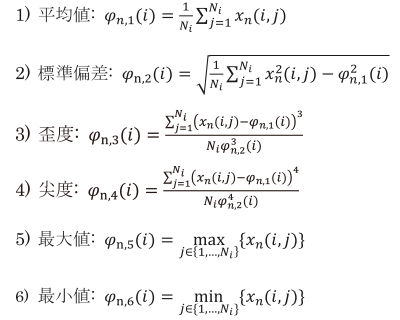
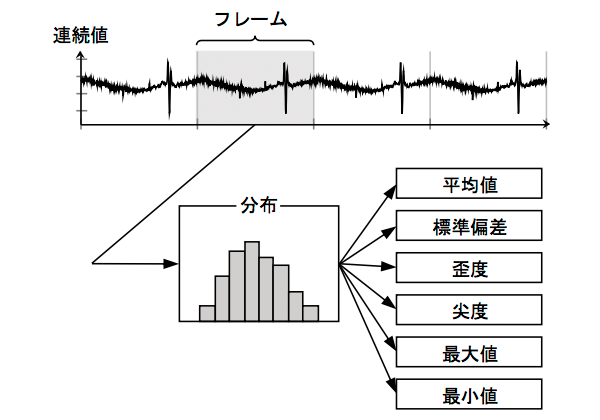
Xn(i,j)が論理値をとる場合の特徴量算出の概念を図5に示す。この特徴量算出は、フレームごとの論理値が反転するタイミングの変化を時間幅の特徴でとらえるものである。以下に論理値についての特徴量の算出式を示す。
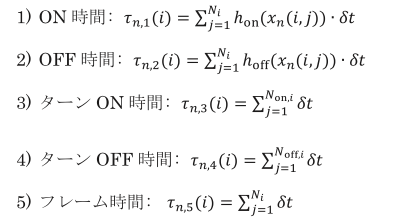
ここで、hon は入力がONのときに1、OFFのときに0を出力する関数、hoff は入力がOFFのときに1、ONのときに0を出力する関数である。また、Non,i はフレームi において論理値がOFFからONにはじめて切り替わるまでのデータ数、Noff,iはONからOFFにはじめて切り替わるまでのデータ数を意味する。
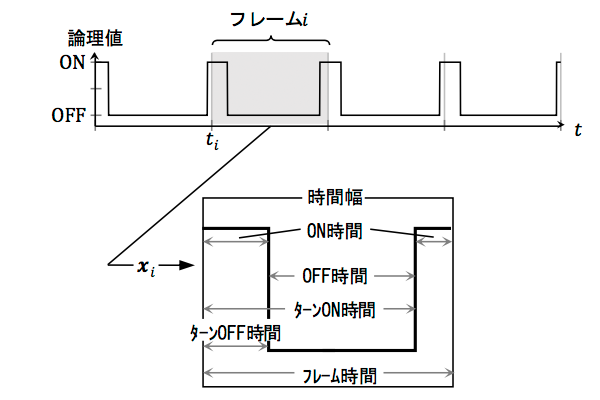
3.5 特徴量選択
算出したすべての特徴量について、人がその意味をひとつずつ確認することは非常に煩わしい。また、すべての特徴量をコントローラで一様に監視させると、計算リソースが不足してしまう。そこで、何らかの方法で見るべき変数を絞り込むことが必要となる。もちろん、対象の生産設備について詳細を知っており、見るべきポイントがわかっているならば、その変数を使ってしまえばよい。しかし、生産設備について詳細を知る人間は極少数であることが多く、知見だけで見るべき変数を選択することは一般的には難しい。そのような場合は、データ解析によって異常検知に有用な変数の選択を行う。変数選択の手法としては、決定木 5)やロジスティック回帰などの機械学習を用いる。具体的には、訓練データに付けられた正常・異常のラベルを目的変数、制御データの各フレームから算出した全ての特徴量を説明変数とおき、目的変数を説明するために最も適した説明変数を選択する。そのため、この変数選択には正常・異常のラベルがつけられた訓練データが必要になる。
データ解析によって異常検知に使用する特徴量を絞っておくことで、計算リソースが潤沢でないコントローラであっても、選択済みの特徴量に対してのみ処理を実行すればよいため、リアルタイム性能を維持しやすくなる。
3.6 外れ値検知
外れ値検知は、特徴量を入力に、対象データの正常からの乖離を異常度として算出する。実用化されている外れ値検知手法として、対象データの分布に依存しないLocal Outlier Factor、One Class SVM(Support Vector Machine)などが挙げられる。外れ値検知手法には、様々な手法があるが、5章の実験では高速・軽量に処理が可能なIsolation Forest 4)を採用した。
Isolation Forestは、データの疎密に基づいた木構造ベースの外れ値検知手法であり、ランダムに決定した座標軸に垂直な超平面によって訓練データを再帰的に分割することで2分木を生成し、複数生成した2分木のノードの深さ情報をもとに異常度を算出する手法である。データ解析時には訓練データを用いて2分木構造を生成し、外れ値検知を行うモデルの学習を行う必要がある。また、外れ値検知モデルが出力する異常度に対して任意の閾値を設定することによって、訓練データを基準とする外れ値の判別が可能となる。
4. 概念実証実験
本章では、3.1節で述べた実験用包装機を制御するコントローラを用いて、提案手法の実用性について検証した結果を述べる。
4.1 実験概要
包装機で発生する包装不良の一つに「シール位置ずれ」がある。「シール位置ずれ」は、センタシール工程においてフィルムを溶着する際、何らかの原因によってフィルムが適切に供給されず、フィルムが左右にずれた状態で溶着されてしまう不良である。ずれた状態でフィルムが溶着されることで密封が不十分になるなど、重大な製品不具合につながる。図6は「シール位置ずれ」を結果とした場合の因果関係を示している。これは、「フィルム固定不足」、「革ベルト摩耗」、「不均一なフィルム巻き」、「ポリベルト伸び」が原因で生じた「フィルム蛇行」という現象が、最終的に「シール位置ずれ」を発生させたという関係を表している。
本実験では、異なる原因から生じる「フィルム蛇行」を「シール位置ずれ」が発生する予兆として異常検知することを試みる。「フィルム蛇行」を「シール位置ずれ」の予兆として検知できれば、「シール位置ずれ」が発生する前に対策をうつことが可能になるため、不良発生を未然防止できると考えられる。具体的には、3.1節で示したように4つのモータそれぞれのトルク・速度・位置と、3つのファイバセンサの論理値の合計15個の信号を計測し、これらのデータを入力として3.2節から3.6節で説明した手順を実行する。なお、実験時の包装機の稼働条件は表1のように設定した。
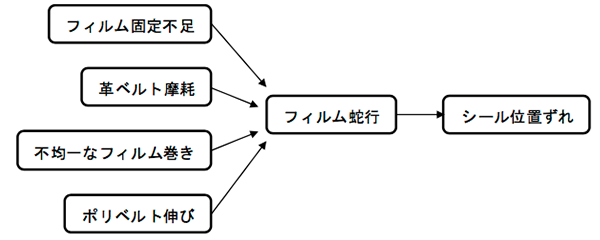
包装長 | 190mm |
---|---|
包装速度 | 60袋/分 |
サンプリング周期 | 2ms |
ワーク | 消しゴム (幅24mm×奥行き65mm×高さ13mm) |
4.2 異常検知のためのデータ解析
包装機が正常稼働しているときのワーク400個分と、「フィルム蛇行」が発生しているときのワーク100個分の制御データを異常検知のための訓練データとして収集した。なお、「フィルム蛇行」は、図7に示すようにフィルム固定用のロッキングレバーを完全に緩めることで再現した。その後、収集した訓練データについて特徴量を算出し、異常検知に用いるための特徴量の選択、外れ値検知モデルの学習、正常と異常を判別するための閾値の決定を行った。
訓練データの一部を図8に示す。このデータを決定木によって解析した結果、表2に示す5つの特徴量が「フィルム蛇行」を検知するために有用な特徴量として選択された。
選択した特徴量を使用して外れ値検知モデルの学習を行い、訓練データを外れ値検知モデルに入力したときに出力される異常度の分布を図9に示す。詳細は後述するが、ここでは0.505を正常と異常を判別する閾値として採用した。
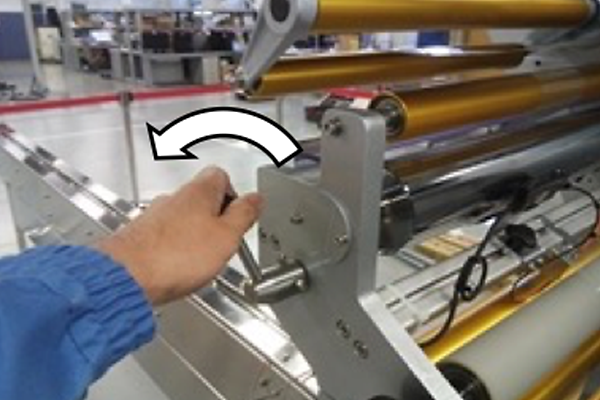
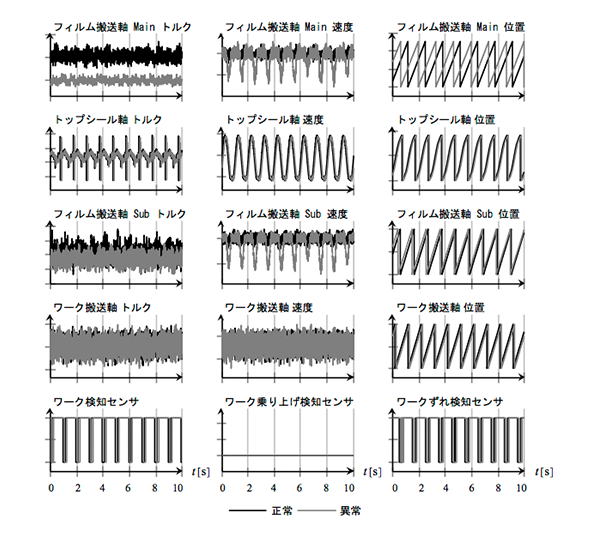
データ | 特徴量 |
---|---|
フィルム搬送軸Mainトルク | 平均値 |
フィルム搬送軸Subトルク | 平均値 |
フィルム搬送軸Mainトルク | 最大値 |
フィルム搬送軸Mainトルク | 最小値 |
フィルム搬送軸Mainトルク | 標準偏差 |
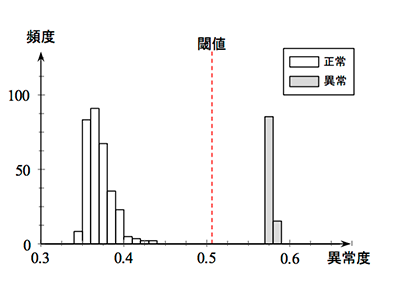
4.3 リアルタイム異常検知
前節のデータ解析で選択した特徴量、学習した外れ値検知モデル、異常判別のための閾値を実際のコントローラに組み込み、「フィルム蛇行」の異常検知をリアルタイムに実行した。本実験では、次の①から④の手順で包装機を動作させた。
①包装機を通常稼働する
②10秒ごとにロッキングレバーの角度を5°ずつ段階的に緩め、「フィルム蛇行」発生させる
③包装機を非常停止させロッキングレバーを元の位置に戻し、復旧作業を実施する
④安全を確認して包装機を再稼働する
図10に外れ値検知モデルが出力した異常度の時間変化を示す。異常度は値が高いほど正常状態から乖離していることを意味する。なお、図中に示した①から④の番号は上述の実験手順と対応している。また、包装機停止中は異常度の算出を行っていないため、その区間のプロットは省略した。
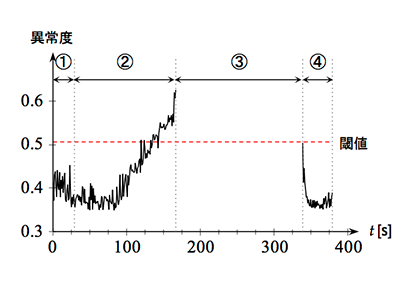
4.4 考察
前節で示した図10の異常度の時間変化に示されるとおり、ステータス②では、ロッキングレバーを緩めることで発生した「フィルム蛇行」によって異常度が上昇しており、最終的に閾値を超えていることが確認できる。さらに、ステータス③で包装機の復旧作業を実施した後、再稼働を行ったステータス④では異常度が閾値以下に戻っていることも確認できる。なお、緩め始めで異常度に変化が見られないのは、ロッキングレバーにあそびがあるためである。以上の結果から、模擬的に起こした「フィルム蛇行」が提案手法によって正しく検知できているといえる。また、「フィルム蛇行」の発生に応じて異常度が段階的に上昇していることから、異常度の傾向を監視することで、非熟練者であっても装置の「いつもと異なる状態」を知ることができると考えられる。例えば異常度に対して段階的な閾値を設けることで、適切なメンテナンスのタイミングを作業者に通知することも可能になる。
本実験では、図9に示したとおり、正常データから算出された異常度の最大値と異常データから算出された異常度の最小値の中間点を閾値として用いたが、この閾値は異常の誤検知と見逃しのトレードオフを決めるものであり、実際は検知対象とする異常の特性に応じて調整が必要である。さらに、設備の運用中に異常度の分布の特性が変化する場合も十分想定されるため、その特性に応じて閾値を更新する必要もある。
今回検知対象とした異常は「フィルム搬送軸Mainトルク」の生のデータに対して閾値を設定することでも検知可能であることが図8からわかる。しかし、特定の異常を検知するためにどの信号を監視すればよいかを人が判断するには、3.5節で述べたような煩雑な確認作業が必要となる。本提案手法を用いると、異常検知に有用な特徴量を一連のデータ解析によって自動的に決定できることに加え、機械学習に基づくアルゴリズムを採用したことで、複雑なルールを必要としない単純な閾値設定による異常判定の設定が可能となりうる。
本提案手法は、これまで熟練者の勘や経験に依存して判断していた装置の健康状態を一定のデータ解析の手順を踏むことによって客観的な数値としてとらえることができるため、装置の稼働率向上を実現する強力な手段となる。
5. むすび
本稿では、生産設備を制御するコントローラのデータを活用し、異常検知を行う方法を提案するとともに、実際の包装機への適用事例を示した。
今後は、社内外の検証や技術開発を通じて提案技術の適用事例の拡大を図るとともに、多種多様な製造業の改善ニーズに対応可能なAI機能の研究開発を継続し、様々な現場課題を解決できる技術へと進化させていきたい。なお、本稿で紹介した技術は、「AI搭載マシンオートメーションコントローラ」6)で採用されている。
最後に、今回の実験や検証にあたり、多大なご協力をいただいたコントローラの技術開発および商品開発に携わった方々に深く感謝申し上げる。
参考文献
- 1)
- オムロン株式会社. "オムロン草津工場事例: ビッグデータから見える製造現場". http://www.fa.omron.co.jp/solution/sysmac/technology/bigdata/index.html, (参照 2018/03/01).
- 2)
- 日本アイ・ビー・エム株式会社. "予知保全(PQM) 資産の障害を予知/予防し、稼働率や歩留まりの向上を実現". https://www-01.ibm.com/software/jp/info/predictive-maintenance/,(参照2018/03/01).
- 3)
- 日本電気株式会社. " "いつもと違う"を発見し、故障や異常を未然に防ぐ。インバリアント分析". http://jpn.nec.com/ai/analyze/invariant.html (参照2018/03/01).
- 4)
- John Ross Quinlan. Induction of decision trees. Machine learning, Vol. 1. Issue.1, pp.81-106, 1986.
- 5)
- Fei Tony Liu; Kai Ming Ting; Zhi-Hua Zhou. Isolation-based anomaly detection. ACM Transactions on Knowledge Discovery from Data (TKDD), Vol. 6, No. 1, p. 3, 2012.
- 6)
- オムロン株式会社. "マシン制御とAIをリアルタイムに融合「AI搭載マシンオートメーションコントローラ」を開発". http://www.omron.co.jp/press/2017/04/c0425.html, (参照 2018/03/01).