超小型自律走行ロボットによる新生産システムの開発
- 超小型自律走行ロボット
- 新生産システム
- 機能別投資分析
- ローコストピックアンドプレースロボット
- 非同期搬送
近年、電子部品事業(エレクトロニック&メカニカル コンポーネンツ 以下EMCと呼ぶ)を取り巻く環境において競争力を維持しながら、顧客価値を提供できるものづくりを実現する必要がある。この顧客価値には絶対的な品質の確保と顧客の事業に合わせた価格や納期での商品の提供が求められる。
従来のEMC商品の生産方式は自動機生産が主流となっていたが、月産10万個以下の小量領域での自動機生産は次の二つの問題が発生している。一つ目は小量領域では設備投資が難しく、人手に頼った組立により品質への影響が懸念される、二つ目は設備製作期間の長期化である。この課題を解決するための新しい生産システムを考案した。
2016年にスイッチの生産向けに立ち上げたラインでは、本システムを実用化し価値を生まない工程の投資を抑え品質に影響のある工程の自動化率を上げた。また、設備製作期間を1/2とすることで顧客へ価値を提供するものづくりを実現することができた。
本稿では超小型自律走行ロボットによる柔軟な搬送技術を主に新たな生産システムの開発とその成果、今後の展開について報告する。
1. まえがき
近年、顧客ニーズが変化・多様化する中、顧客ごとにカスタマイズした商品を提供することと開発期間の短縮が求められている。また、生産現場においては人件費の高騰や生産人員確保などの課題解決も必要である。あわせて新興国をはじめとする競合の成長も著しく、コスト面だけでなく品質面においても脅威となってきている。このような電子部品事業(エレクトロニック メカニカル コンポーネンツ 以下EMCと呼ぶ)を取り巻く環境において競争力を維持しながら、さらに成長していくためには、顧客のさまざまな要求に応えるものづくりを実現する必要がある。
ここでは、これらの課題を解決し、顧客満足と経営満足を両立するために開発した小量領域での新しい生産システムの取り組みについて報告する。
2. 新しい生産システムの必要性
従来のEMC商品の生産方式は自動機での生産が主流となっており、月産100万個以上の大量領域では生産タクトが速いため自動機生産方式は有効だが、小量領域の生産での自動機投資は以下の課題が残る。自動機では組立や検査精度に影響しないよう精度の高い部品で構成された治具部分や高速で次工程に送り、高精度で停止させるために高精度や高剛性の構造が必要なため、重厚かつ剛性の高い架台フレームを持った自動機の基礎部分が必要となる。
この基礎部分をベースマシンと呼ぶが、数量の少ないカスタマイズ商品で使用すると、償却費が大幅に上がり原価を圧迫する。また、自動機で生産するには将来の需要増を見越した売上計画をもとに投資を実施することとなり、すぐに必要でない性能(高速の搬送スピードや空き工程)を持った高額な投資が立ち上げ当初の数量が少ない時期から発生する。
この自動機におけるベースマシンを乗客を輸送する鉄道で例えると、新幹線が在来線の各駅に停車するようなものである。新幹線が走れる強靭な線路やホーム、乗客を運ぶエスカレータやエレベータを完備しても乗客はほとんどいない。将来、駅周辺の発展を予想してのことだが、だれもが今すべきではない投資だと判断できる。しかし実際の生産ラインではこのような投資となることも散見される。
商品ライフサイクルでいう成熟期を見越した生産能力を持った自動機を導入期で準備するのではなく、導入期は数量に見合った投資での立ち上げを行い、成長期は事業の拡大に比例した生産能力の増強を細かな単位で行う。衰退期には成長期で投資した部分を他機種に転用することで有効活用が可能となる。
2.1 数量に見合った軽い立ち上げ
顧客のさまざまな要求の一つである少ない数量の商談に応えるためには、少ない数量でも製造原価を抑えることが求められる。小量領域での自動機投資は難しく、自動機をベースにした投資削減は限界にきている。一方、人手による手組生産では人件費の高騰や人員の確保が非常に困難な状況となっている。現状の生産方式では人手による組立作業の自動化と投資削減を両立することは非常に困難である。
例としてEMC商品であるスイッチの新商品では80%以上が初年度の数量が月産10万個以下、その開発期間の短縮も求められている。月産100万個以上に適用する自動機生産方式では、製造原価が高くなり顧客の要求に応えられない。要求に応えられなければ採用に至らず他社に切り替えられて事業の機会をなくすことになる。
立ち上げ当初の数量が少ない商品ライフサイクルの導入期では実際の顧客要求数量に見合った軽い立上げ、すなわち数量に見合った設備投資で早く生産ラインを立ち上げることが顧客満足と経営満足を両立することに繋がる。
2.2 数量の増加に追従した段階投資
前述したように導入期では顧客の要求数量に見合った設備投資での立ち上げを求められる一方、発売開始後は顧客の満足する供給を続けながら数量の増加に柔軟に対応することが求められる。これはEMC商品が搭載された顧客の商品の販売数の増加や他顧客への展開などにより、要求数量が刻々と変化するためである。
従来の自動機生産では成熟期を見越した生産能力を持った自動機を導入期で準備し対応してきたが、この理由は成長期における数量の増加に追従した生産能力の増強が従来の自動機生産では対応できないからである。
ただし、成熟期を見越した導入期での自動機投資は予測数量に達しない場合は生産ラインが停止することになる。すなわち生産をしない、利益を生まない自動機が工場に鎮座する。逆に他社での採用などで受注が大幅に増加する場合は、2ライン目を立ち上げることになるが、前述したのと同様のロスを生むことになる。この従来の自動機生産での問題を解決するためには、2.1項で説明した要求数量に見合った投資が可能となる新しい生産システムを作り、そのシステムで要求数量の増加に比例した生産能力を確保するための細かな段階投資をすることである。
2.3 数量の減少に伴った他機種転用
2.1項や2.2項で導入期における軽い立ち上げや要求数量の増加に比例した段階投資で顧客の要求に応えることが可能になる。ただし、成熟期を終え顧客要求数量の少なくなる衰退期では稼働しない自動機は負の遺産になる。
ここで要求数量に比例した段階投資ができる生産システムがあれば、その強みが有効に働く。なぜならば要求に比例した投資とは要求数量が増加するだけでなく減少する場合にも適用できるからである。方法としては段階投資で増やした部分を他のラインに転用するだけで数量の減少に対応でき、さらなるメリットとしては、そのユニットを他機種で使用できることだ。ROICで言う資産回転率の向上と他機種の開発期間の短縮に大きく寄与できる。
新しい生産システムの必要性を満足するためには従来の自動機生産とは全く違う考え方で検討を進めた。その考え方について以降に説明する。
3. 新しいシステムの考え方(V=F/C)
投資をより有効活用するために、生産ラインのどの部分にどのくらいの投資が発生しているかを調査した結果、新しい生産システムを検討するうえでの考え方を決定した。機能別の投資分析から、ものを運ぶ(以下、搬送と呼ぶ)、部品や製品を供給(以下、供給と呼ぶ)するといった、ものづくりでは排除できないが、製品の形を変えるという付加価値を生まない(以下、非付加価値)工程、すなわち補助的な工程で多くの投資がかかっていることがわかった。またこの工程は商品群の違いに関係なくすべての生産において共通的な機能であることもわかった(図1)。
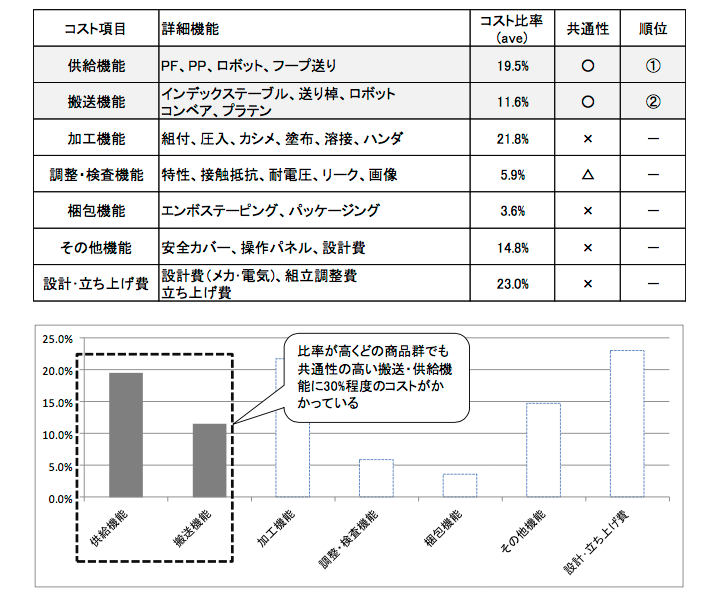
さらにこれらの搬送や供給工程では市販ユニットを多用しているため生産に必要以上の性能を持っている工程が多い。たとえば次の工程に1秒以下で移動する搬送装置や数kgのものを1秒以下で運べるロボットである。
顧客の要求数量に見合った生産システムの決定に当たってはこの搬送と供給をいかに柔軟にするかが大きなポイントとなる。数量の増加に追従した段階投資ができるようステーションや搬送装置を追加して工程を増やせるシステムとした。また従来だと1サイクルで一回の動作しかしない同期した搬送装置だが、今回は非同期の搬送装置(個々の装置が自立走行するプラテン、以下自走プラテンと呼ぶ)とし、個々の動きやスピードを都度変えられる、機種によっては不要な工程は飛ばして搬送することも可能なシステムとした。これにより工程ごとにばらつきのあるサイクルタイムを平準化できる工程設計が可能になった。
早く立ち上げができ、段階投資も可能、また他機種への転用もできる投資の安い生産システムであることに加えて工程品質を確保することも大きな要求の一つである。投資削減と品質確保の二つを両立する生産システムを作り上げるために搬送と供給機能に対して品質機能展開(QFD)を作成し、必要な機能と品質の関係を明確にした。
品質への影響が少ない工程には、その工程に見合った性能を満足する投資額を決定し実現する手段を考え抜いた。品質に影響を及ぼす可能性が高い工程には徹底した自動化を行う。もちろん品質第一の考え方は第一義としてあるため、削減した投資を品質向上のための投資として使うこともできる。
ここでは徹底した投資削減を行う上で用いた考え方について紹介する。それはV=F/Cという価値工学の式による考え方である。Cはコストを表し、Fは工程での必要な機能となるが組み立てる、検査するといった必要な機能そのものは変えることができないため、機能はその商品の生産に見合った性能に置き換えた。またVはその工程の価値と見做し、この式をC=F/Vに変換してCを削減するために以下の二つの観点で検討を進めた(図2)。
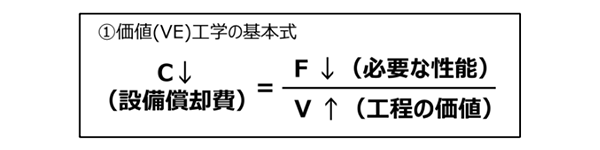
(1) 工程としての価値Vを上げる
工程としての価値とは何か、部品を組立てる、半田付けする、圧入するなど様々な工程がある。従来のシステムでもこの価値を満足する工程となっていることは言うまでもない。一つの結論として価値を上げるとは一つの工程で複数の作業ができることとした。具体例で言うと組立、塗布、組立、塗布といった繰り返しの塗布作業を一つの工程に集約するといった考え方である。この考えは一つの工程の価値を上げるとともに、塗布装置が1台となるため品質を管理するといった観点からも有効な考え方である。
(2) EMC商品の生産に必要な性能Fに絞る
EMC商品を生産するうえで必要な性能とは何か、工程には供給、搬送、加工、調整検査などの機能を持った装置が設置されているが、多くの場合、市販の装置を使用した自動機の設計を行う。事例としては従来の搬送装置ではベースマシンやインデックスと呼ばれる市販の搬送装置を用いている。これらは大量生産領域である、タクトの早い生産では有効な搬送装置だが小量領域では必要ない。また供給においても市販の産業用ロボットなどを多用している。近年ロボット技術の高度化により低価格にはなってきているが、小量領域で使うにはまだまだ高価である。市場には高機能で高価格な装置は多くあるが、EMC商品のように電子部品の生産に必要な性能に見合った装置はない。逆にEMC商品の生産に見合った性能を持つ装置を特注すると装置自体が高価になる。そのため、投資削減と品質確保を両立する生産システムを自前で作ることとし、開発に着手した。
4. 開発の概要
新しい生産システムを構築するために開発した搬送と供給の二つのユニットについて紹介する。
4.1 自走式搬送ロボット
各工程間をワーク積載して自律走行する自走式搬送ロボット(以下自走プラテンと呼ぶ、図3)で必要な性能は以下とした。
①積載荷重を500 g以下
②走行スピードは0.5 m/秒以上
③停止位置±2 mm(最終位置決めは位置決めピン)
④電池交換などで設備停止をさせないこと
⑤工程ごとに走行条件を都度通信できること
上記の必要な性能は品質機能展開などから決定したものである。①の積載荷重はEMC商品を対象とした場合にほとんどの商品の搬送が可能な荷重である。②の走行スピードについては月産10万個を生産するのに必要なサイクルタイムから算出した。③の停止位置は停止した自走プラテンを外部から位置決めするために必要な停止精度から割り出したものだが、①②③はトレードオフの関係にあり、すべての性能を満足するための取り組みとして、走行スピードと停止位置の関係について紹介する。
近年のバッテリ技術の進化はすさまじいが8時間以上連続して使用できる安価で小型のバッテリは存在しない。モータを動かす駆動源はバッテリであるという固定概念から脱し、8時間充電なしで走り続けるという性能ではなく、次の工程までワークを0.5 m/秒以上のスピードで搬送する性能を満足ことができればよいという考え方からキャパシタでのモータ駆動という手段を選択した。また、キャパシタは電子部品のため充電時間も非常に短い。工程で組立や検査をしている時間内で充電することが可能となった。これにより④の電池交換などで設備停止をさせないこともクリアした。⑤の工程ごとに走行条件を都度通信できることについては自由な搬送を実現するためには、工程間の距離も工程ごとに違う。工程間毎に必要な時間で走りきる走行条件の送信や走行状態の受信が必要となる。この送受信はテレビリモコンなどで一般的に使用されている赤外線通信を採用した。素子自体も電子部品で安価なうえ入手性も高い。各工程での混信が発生しないよう配慮をしたうえ使用している。

- 10
- 自走プラテン(自走 搬送車)
- 11
- プラテン本体部
- 11b
- 載置板
- 12a
- 車輪
- 12b
- 従動輪
- 12c
- モータ(移動用モータ)
- 14
- 位置検出装置
- 14c
- 警報ブザー
- 15
- L E D ランプ
- 16
- プラテン側赤外線モジュール(送信部)
- 17
- キャパシタ
- 17a
- 制御電源用キャパシタ
- 17b
- モータ駆動用キャパシタ
- 18
- 停止位置決め装置
- 18a
- 赤外光発光部(発光装置)
- 18b
- 赤外光受光部(受光装置)
- 30A
- メイン基板
4.2 ローコストピックアンドプレースロボット
部品の供給やワークの移載を行う小型水平多関節型のローコストピックアンドプレースロボット(以下LCPP、図4)に必要な性能は以下とした。
①可搬重量 800 g以下
②移載スピード 3秒以下
(上下30 mm左右300 mmのゲートモーション)
③停止精度 ±0.015 mm以下
④動作条件や停止位置の設定をパソコンで行う
自走プラテン同様①〜③は重量、スピード、精度の面で、EMC商品の生産に必要な性能として決定した。④の動作条件や停止位置の設定も現場でのユーザビリティを考慮し安価でも必要な機能とした。
重たいものを早く運ぶ性能の高いFA用ロボットは数多くあるが、逆に可搬重量は軽く、スピードも遅い研究用や学習用のロボットも存在する。この研究用や学習用ロボットは停止精度のばらつきが大きいためEMC商品の生産では使えない。両者の良いところを合わせもった安い市販ロボットは無いため、自社製作を行った。
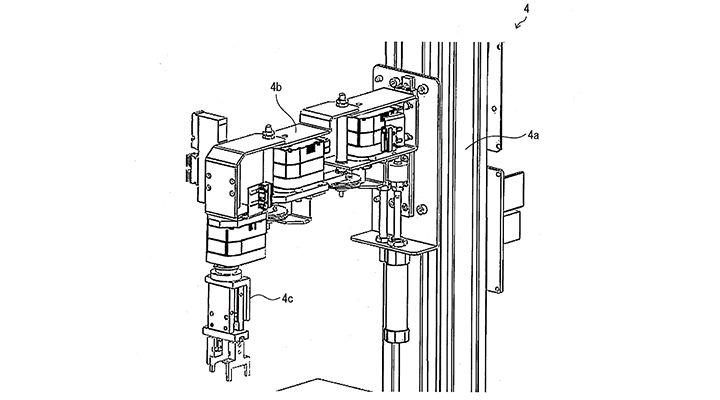
- 4
- LCPP
- 4a
- 支柱
- 4b
- 連結アーム
- 4c
- エンドエフェクタ
軽いものをゆっくり運べることができればよいが、位置決め精度は市販ロボット並みの性能が必要となる。ここではホビーロボットで良く使用されるコマンドサーボを用い、外部に減速ギヤにより停止精度を高めた。ギヤ比を上げれば停止精度はよくなるが、スピードが遅くなるというトレードオフの関係にある。できるだけスピードが速く、剛性の高いコマンドサーボを選定し必要な性能を確保した安価な水平多関節ロボットを製作した。
自走プラテン、LCPPともに民生用の部品を使用しているため寿命目標に対する評価も実施したうえで実際の量産ラインで使用している。
自走プラテンもLCPPも必要な性能に絞って安価な装置としたことで、交換部品も安く摩耗の多いタイヤはOリングを使用し1年ごとの定期交換とした。交換部品が高価であれば問題が起きるまで使うが安価な部品であることで定期交換がしやすくなり安定した性能の状態で使用できることで生産ラインでのチョコ停などのトラブルも少なくなる。
4.3 自走プラテン・LCPPを組み合わせた搬送供給システム
自走プラテンとLCPPの開発については前述のとおりだが、自走プラテン自体が直進すること、カーブを曲がる機は持ち得ていない。寸分の違いなく直進やカーブができる機能を自走プラテン自体に持たせると高価になるためだ。自走プラテンの走行は"走って止まる"という単純な機能をもち直進やカーブは玩具メーカが販売している軟質プラスチック製のレールをガイドとして走行させることとした。
安価なレールの組み合わせで様々な経路で走らせることができるため設備架台上のエリアを有効に活用できるようになった。図5にその基本構成を示す。
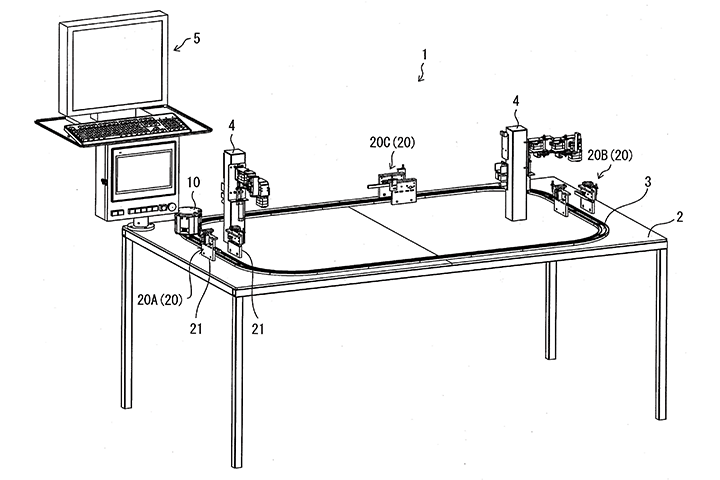
- 1
- 無人搬送システム
- 2
- 作業台
- 3
- 搬送レール(軟質プラスチック)
- 4
- LCPP
- 5
- パーソナルコンピュータ〔パソコン〕(制御装置)
- 10
- 自走プラテン(自走搬送車)
- 20
- 充電ステーション(充電装置)
- 20a
- 第1通信/充電ステーション
- 20b
- 第2通信/充電ステーション
- 20c
- 第3通信/充電ステーション
- 21
- 立設板
5. 開発成果とその効果
5.1 実用化事例
本生産システムを実用化し、稼働開始したのは2016年。対象としたのは、"スイッチ"の組立である。
スイッチの組立工程の特徴として、動作部へのグリス塗布が欠かせない事がある。そして、塗布箇所が多岐にわたるため、部品組立とグリス塗布を繰り返す工程順となっている。また、生産能力を確保するため作業を分割する必要があり、従来の自動機ではグリス塗布の装置を複数設置し、工程順に配置していた。そのため、工程間をつなぐ搬送装置がその工程数分必要とし、搬送機能にかかる費用割合が高くなり、設備全体の架台も強固で大型のものが必要にならざるを得なかった。
これに対し、今回の実用化(図6)では以下の効果が得られた。
・設備投資額 1/2
・設備製作期間 1/2 (10ヶ月→5ヶ月)
・設置スペース 2/3 (36 m2→24 m2)
以下に、設備投資額低減と、設備製作期間短縮の概要を説明する。
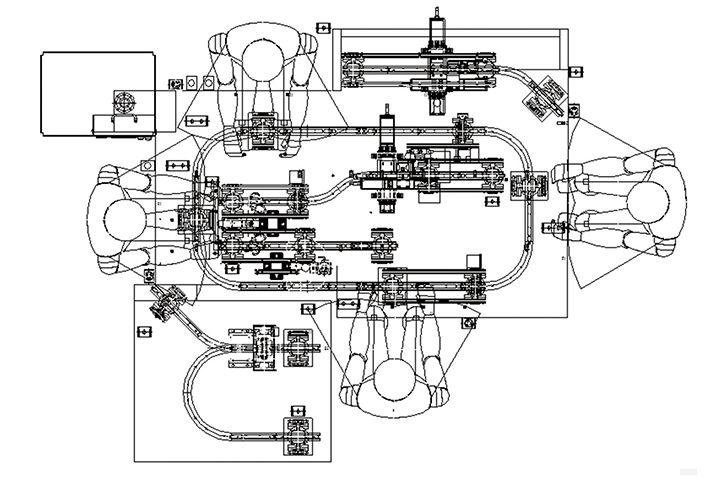
5.2 設備投資額低減
従来の自動機に用いられるベースマシンは、プラテンを連結して搬送させる方式であり、大型の駆動装置と専用の連結部品が必要となる。
これに対し、本システムでは、大型の専用加工品が一切不要となることと、非同期搬送を可能としたことで無駄なく必要最小限の自走プラテンを配置することができた。さらには、搬送経路の自由度を活用し、グリス塗布などの加工装置を集約させて工程を配置することも可能となった。これは、設備を構成する部品点数も少なくなり、コンパクト化につながった。これらにより、同一工程数で採用する条件で比較した場合、上述の低減効果を得られる事を算出できている。
5.3 設備製作期間短縮
従来の自動機に用いられるベースマシンは、大部分が専用設計となり設計期間を要する。そして最も時間を要するのは組立・調整であり、連結方式であるが故の全体調整が必要であることがその要因である。具体的には、ひとつ調整が必要な場合、それが全体に影響するため、作業が難航するケースが多い。
これに対し、本システムでは、専用設計するのは部品を保持する治具機構のみであり、設計期間が大幅に短い。また、連結ではなく、精度の必要な部分は工程毎に個別化しており、個別調整が可能であることと、調整箇所が必要最小限で済んだ。これらにより、同一工程数で採用する条件で比較した場合、上述の低減効果を得られる事を算出できている。
5.4 品質力向上活用事例
設備投資額低減ができ、非同期による自由度の高い搬送が可能なため、非付加価値の投資を必要最小限にすることで付加価値工程に費用を充てることができる。この費用は自動化による品質力向上に活用している。以下に事例を紹介する。
スイッチの生産は、自動機ラインはまだ一部であり、手組ラインが主流である。手組ラインでは、横に作業者を配置する直線ラインとしていることもあり、グリス塗布の装置を複数必要としていた。また、装置といっても一定量塗布するディスペンサ単体を準備するのが投資的に限界であり、作業は基本的に手作業。塗布量は装置で制御するものの塗布行為そのものの作業ミスにつながりかねない状態が課題視されていた。
ここで、設備の工程設計を考えるときに、自走プラテンの非同期搬送機能と柔軟なレイアウトが可能な事を活かした。自動装置を最大活用する"工程シェア"である。
複数にわたり手作業を必要とする塗布装置しか投資できなかったものを、完全自動塗布装置に集約することができた。具体的には、前半工程から搬送する部品と、後半工程から搬送する部品のそれぞれを自動塗布装置に順番に、それも一方向ではなく両方向から自走プラテンで搬送する。
そして、この工程シェアの活用方法は、必要な装置数を最小限にすることができる方法であるため、投資の集約のみならず、品質管理の集約になる。自動化促進による品質安定化に加え、品質バラツキの抑制にも効果がある品質向上の活用方法と言える。
5.5 顧客の期待・価値向上
本システムが顧客から期待を得て、強力なパートナとしての関係継続に結び付いた事例を紹介する。
これまで、スイッチの顧客A社からは、従来の手組ライン起因による品質課題により、改善要求を受け続けていた。例えば、主力の機種は増産を繰り返しているものの、手組の人員増加で対応しており品質問題は変わらない状況が続いている。改善は続けているものの大きく状況を変えることができず、このまま問題を抱えたまま手組を続けるのであれば、"オムロン以外のメーカを検討する"という打診を受けるところまできていた。そのような状況の中、顧客への説明会を実施した。説明会では、具体的に実用化設備を用いながら従来との比較で説明し、革新性を認めていただけることができた。そして自動化を進めることによる品質向上の期待から、今後の強固なパートナ関係の構築につながった。また、設備製作期間が短いという優位性も理解され、事業計画に反映されている。今後、要求にいかに早く対応するかという"on demand"に価値が見出されている観点からも、本システムの優位性は大きい。
6. 今後の展開
6.1 展開性
今回、確かな効果が得られる事が実証できたことから、積極的に活用を促進していく計画である。
今回開発した搬送・供給システムは、専用加工装置などとは違い汎用性が高い。今回適用したスイッチ以外も含めたオムロン商品全般の生産ラインを対象として活用する事を、各事業、各生産拠点から期待されている。具体的には、中国、インドネシアなどの海外拠点での活用を2018年度よりすすめる。そして、スイッチに限らずEMC関係の全拠点へ展開、さらには、EMCの電子部品の生産のみならず、FA商品の組立ラインへの活用についても事業を超えて検討を始めている。FA商品の生産が得意としている手組セル生産の管理技術と本システムを融合し、更なる進化を模索している。
6.2 混流生産
今後は「数量に見合った軽い立上げ」を更に追求し、1台の設備で複数の商品を生産できる混流生産への活用にむけて、開発を継続している。
4項で架台上レイアウトに自由度があることを説明したが、経路変更を可能とすることで更に活用範囲が広がる。具体的には、自走プラテンの固有ID情報を利用し、搬送する部品と各工程の作業・加工内容を生産機種に応じてデータを一致させ動作させる。そして、各工程の作業・加工が終わり次工程に搬送する時に、プログラムで経路変更情報を書き込み、対象の工程まで搬送させる。この混流生産システムで狙う効果は、さらなる設備投資額削減、設備製作期間短縮である。
6.3 最後に
本システムは柔軟性が高く、まだ気づいていないものも含めて大きな可能性を秘めている。今回の取組み成果を一つのきっかけとし、更に良いシステムへとステップアップさせていく。そして、オムロン全ての事業・カンパニーとの検討・議論を通じて、事業成果のみならず、全社員の挑戦意欲向上と成功体験による誇り・自信・行動につなげていきたい。
参考文献
- 1)
- 日本機械学会 生産システム部門 技術ロードマップWG
「生産システム部門 技術ロードマップ」(2016)