The progress in displacement sensor technology by the change of application scene in manufacturing
- Displacement sensor
- High precision
- High speed
- Optical design
- Algorithm
Conventional triangulation method has been the mainstream for displacement sensors, but on leading-edge manufacturing of customers, there have been the problems of the tuning difficulties when setting by the triangulation method and the errors due to the measuring objects’ differences. In response to these issues, we will release the new Coaxial displacement sensor based on white light confocal principle (ZW) which can measure easily by anyone without material in 2012. As a result, we will release the product of the digital industry’s smartphone assembled It has been adopted mainly for inspection. However, due to the increase in the number of inspection points by the lighter, thinner, shorter and smaller packages of smartphones accompanying the slimness and higher performance of the smartphone and the evolution of product design, it is required to realize higher precision inspection at high speed. In order to cope with such changes in the manufacturing site, we have established a technology to dramatically improve the speed and accuracy in scanning, so I will introduce it here.
1. Introduction
The purpose of a displacement sensor is to conduct inspections (shape, thickness, height, etc., of a product) at a manufacturing site and to measure positioning errors on the order of micrometers. The use of the sensor leads to improvements in precision inspections and control, which allows high-quality manufacturing at a high level. Thus far, triangulation type laser displacement sensors have typically been used, but some problems at leading-edge manufacturing sites have arisen from the difficulty in adjustment during installation, resulting in errors depending on the materials being measured. To solve such problems, we commercialized a coaxial white light confocal displacement sensor (model: ZW) based on a new principle from 2012. The sensor is compact and simple to install, resulting in higher accuracy in measuring distance regardless of the materials being measured.
Recently, more accurate inspections conducted at higher speeds are necessary because of the increase in the number of precision parts and inspection items due to the reduction in weight and size and improvements in product design of thinner smartphones offering higher performance.
2. Principle of white light confocal measurement
This product is a sensor (white light confocal displacement sensor) that can measure the distance to an object being measured by focusing light of different wavelengths in the direction of the height of the object and receiving only light of wavelengths focusing on the object with the CMOS of a spectroscope1).
This system consists of a light source, branch coupler, fiber, sensor head, spectroscope, and CPU as shown in Fig. 1. The sensor head contains a diffractive lens and an objective lens, and the spectroscope contains a diffraction grating and a CMOS.

The light from the white light source enters the sensor head via the branch coupler and fiber. The light is separated in the direction of the height of the object by the diffractive lens in the sensor head. Only light of a specific wavelength focusing on the object condenses on the fiber connected to the sensor head and enters the spectroscope because the sensor head is a confocal optical system in which the light reflected from the object is focused on the fiber. For example, in the case of Fig. 1, only green light enters the spectroscope because green light condenses on the object being measured. On the other hand, red and blue light are not condensed on the object so light is not condensed on the fiber and does not enter the spectroscope. The light entering the spectroscope is separated by the diffraction grating, and the distance to the object can be calculated by obtaining the pixel position condensed on the CMOS and by using the correction data in which the pixel position is already associated with the distance.
This principle has the following advantages in comparison with the conventional technique:
- (1)
- The white light confocal distance sensor is a coaxial optical system, so the shape, even with a steeper angle on a glossy surface, can be measured in comparison with the conventional laser displacement sensor. Fig. 2 shows the results of measuring lens shape. We found that measurement with an expanded shape measurement range could be performed in comparison with the conventional type. Accordingly, even for a flat object, measurements with simple installation can be performed.

- (2)
- With the conventional laser displacement sensor, the light receiving waveform varies depending on the materials, and measurement errors can occur because light intensity distribution in the beam spot on the object directly projects on the CMOS. Conversely, with the white light confocal displacement sensor, the light intensity distribution at any given point is not a concern, and even if the material is not the same, measurements can be performed with the same accuracy because distance is calculated from the wavelength of the reflected light. Fig. 3 shows the results of comparing the linearity (the difference between the distances of stage movement in the height direction and measurement values) of different materials.
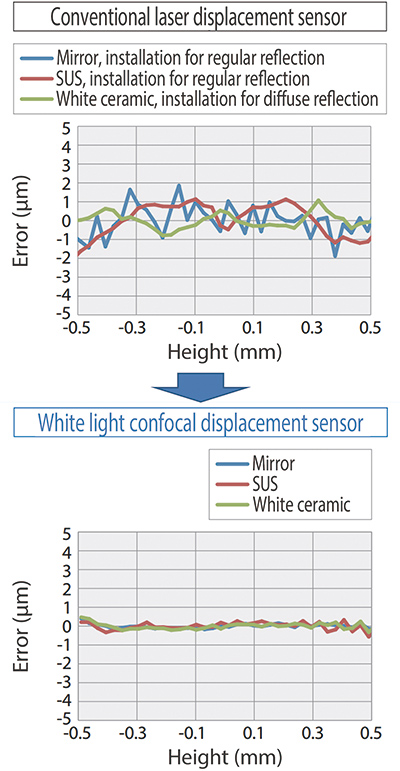
3. Technical issues
For example, in inspecting the state of assembly of smartphones, higher speed and higher accuracy are required because assembly accuracy is needed even more than before, and the number of inspection points has increased due to the reduction in weight and size. To respond to customer needs, we must improve white light confocal technology and develop a displacement sensor with higher speed and higher accuracy.
3.1 Issue concerning highly accurate measurement in white light confocal technology
Fig. 4 shows the results of scanning measurements of a stainless steel material (described as SUS) with a maximum surface roughness of 3.2μm Rz. The issue was that when the surface roughness of the measured object was 3.2μm or higher, a measurement error occurred, and measurement could not be stably conducted at scanning. In this document, the quadruple (4σ) of the standard deviation of measurement errors occurring with the actual surface roughness value or higher is defined as dispersion of scanning measurement.
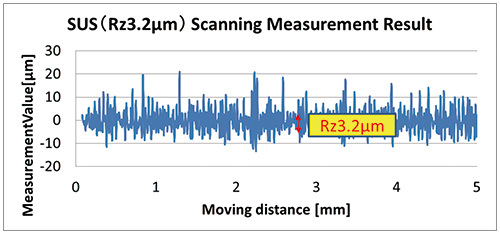
3.2 Issue concerning high-speed measurement in white light confocal technology
The white light confocal method uses light less efficiently because of the principle that only a specific wavelength element corresponding to the distance is used among the wavelength elements of irradiated light. For example, if the sampling speed is enhanced to inspect the surface shape of an object at higher speed, there is the issue that a sufficient amount of the receiving light necessary for measurement cannot be secured. In the case of an object being measured with 10% reflectance, 500μsec was needed to secure a sufficient amount of receiving light in the past. Thus, the critical moving speed was 20 mm/s to conduct the scanning measurement at a 10μm pitch. To solve this issue, an approach to enlarge the core of the optical fiber constituting the light guiding unit can be considered. An enlarged core allows a larger amount of light to be propagated, but according to the principle of the white light confocal method, the halfvalue width of the receiving light waveform becomes larger. The larger the half-value width, the larger the dispersion in the measurement value, and accordingly, the disadvantage of deteriorating measurement accuracy occurs.
4. Technical details
In this section, the following three themes are considered as methods for enhancing the accuracy to reduce dispersion of measurement:
- (1)
-
Reduction in the depth of field
A decrease in the half-value width of the receiving light waveform reduces the measurement error. - (2)
-
Error correction by waveform slope algorithm
A measurement error is corrected by using the slope of the receiving light waveform. - (3)
-
Use of multi-fiber2)
An increase in the measurement range of an object levels the unevenness of the object and reduces any measurement error.
We also considered the use of multi-fiber, the enhancement of light source luminance, and a reduction in noise from the light receiving element as methods of increasing speed. The technical details are described below.
4.1 Reduction in depth of field for measurement with higher accuracy
Regarding the white light confocal displacement sensor, a light projection beam is separated in the direction of the height of the object being measured, and accordingly, when the depth of field is small, the width of the wavelength of the light received is small. Therefore, we considered that the half-value width of the receiving light waveform became thinner, and the measurement error was reduced. As a result of the experiment, we found that an increase in the depth of field enlarged the dispersion of scanning measurement as shown in Fig. 5.
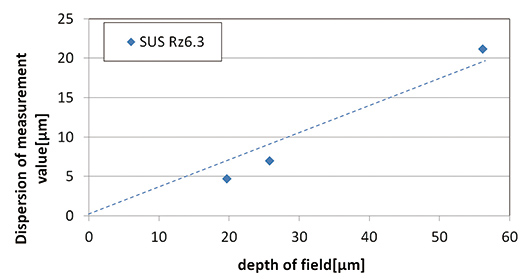
Consequently, the depth of field expressed by the following formula needs to be decreased to receive only light of a specific wavelength in the confocal optical system:
Fig. 6 shows design parameters related to the depth of field.
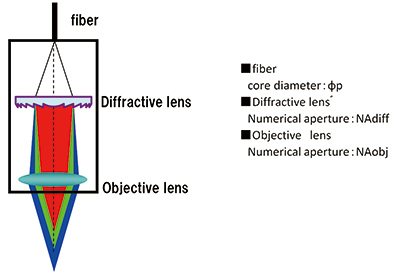
According to the formula described above, a decrease in the NA of the diffractive lens and an increase in the NA of the objective lens are desirable for an increase in the depth of field. Once the measuring center distance between the sensor head and the object (for a displacement sensor with a measuring range of 19 to 21 mm, it is expressed as a displacement sensor with a measuring center distance of 20 mm) is decided, the focal distance of the objective lens is decided, and then the NA of the objective lens is determined according to the manufacturing limit. Accordingly, the external dimensions are determined, and the NA of the diffractive lens is determined.
Table 1 shows the tentative calculation results when the depth of field is reduced to 0.27 times the case of using the sensor head with a measuring center distance of 20 mm.
Design parameter | Ratio to conventional type |
---|---|
NA of diffractive lens | 0.65 times |
NA of objective lens | 1.54 times |
Depth of field | 0.27 times |
4.2 Algorithm for correcting waveform slope in highaccuracy measurement
In Section 4.1, improvement in the accuracy of the optical system was described and the use of the algorithm was also considered. Regarding dispersion of scanning measurement, the wavelength of the reflected light from the object being measured varies because of the unevenness of the object as shown in Fig. 7; consequently, distortion is created in the receiving light waveform, and measurement errors are assumed to be generated.
Therefore, we considered if the distortion of the receiving light waveform could be quantified, the error could be corrected and reduced. We then calculated the waveform slope from the receiving light waveform. Specifically, we obtained the center positions of lines with 70% and 30% of the peak power of the receiving light waveform as shown in Fig. 8 and then defined the slope of the straight line passing through those coordinates as the waveform slope.
We found a high correlation (correlation coefficient: R=0.94) between the slope of the receiving light waveform and four times the standard deviation (dispersion of scanning measurement) of the measurement errors as shown in Fig. 9. Therefore, we invented an algorithm to reduce the measurement errors by calculating the slope of the receiving light waveform, presuming a measurement error on the basis of the slope, and then subtracting the calculated value from the measurement value.
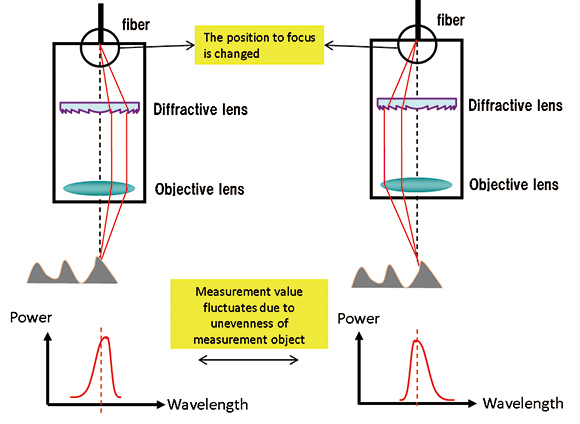
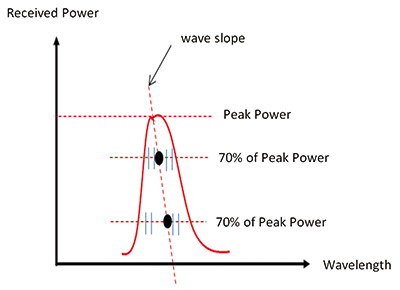
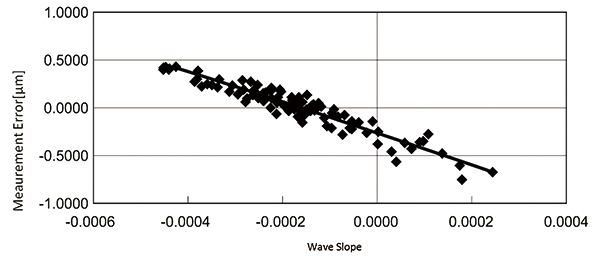
4.3 Multi-fiber for high-speed and high-accuracy measurement
This section describes multi-fiber, which has the advantage of both high speed and high accuracy. With this technique, we considered that the received power could be increased, slight unevenness of the object being measured could be leveled, and measurement could be stably conducted by using multiple fibers with the fiber core maintained. Fig. 10 shows the system configuration of this technique.
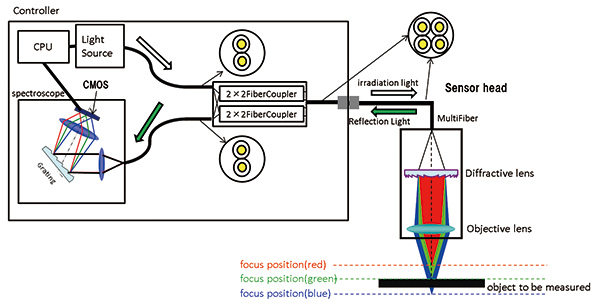
In other words, we can expect that the use of four fibers quadruples the amount of light received, and the effect of leveling four fibers improves the dispersion of scanning measurement two-fold.
4.4 Enhancement of luminance and reduction in noise for high-speed measurement
In addition to the quadrupled amount of light received from the use of multi-fiber, we considered enhancement of luminance and reduced the noise from the white LED/light receiving element to further increase the amount of light received. Highspeed measurement at 20μsec at maximum was achieved by selecting a receiving light element device capable of high-speed imaging and by using a field-programmable gate array (FPGA) for the entire measurement process, because an increase in the amount of light received alone could not achieve high-speed measurement. Fig. 11 shows the LED luminance of the conventional sensor and that of the new sensor. Up to 5.1 times the enhancement of high luminance in comparison with the conventional model has been achieved by raising the current applied to the LED through the use of a heat radiation design.
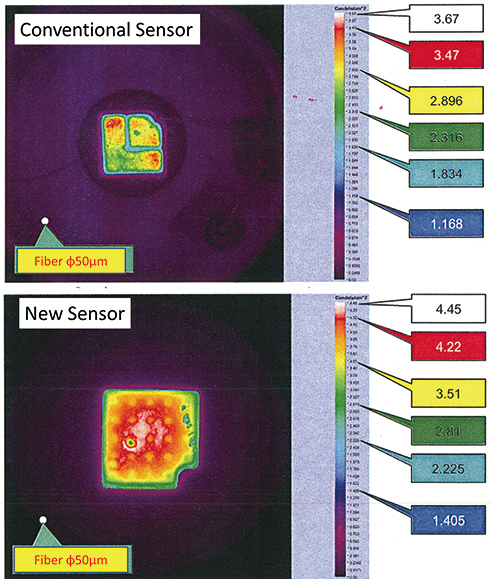
Fig. 12 shows the results of comparing the noise from the conventional sensor with the noise from the light receiving element to be used (the new sensor). The noise from the light receiving element was reduced by approximately 0.66 times in comparison with the conventional sensor, and accordingly, the S/N ratio was improved by 1.5 times. In addition, the amount of light received was proportional to the square of the S/N ratio, and the effect of approximately 2.3 times could be obtained as expressed by the amount of light received.
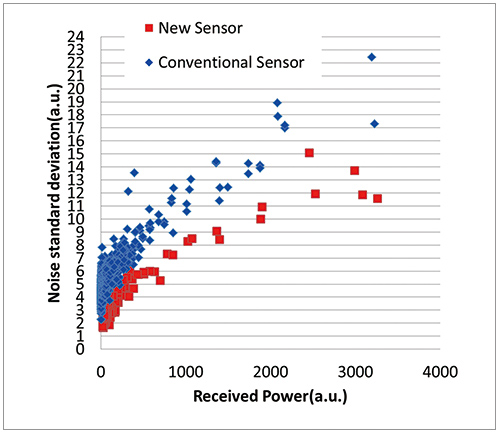
5. Effect
5.1 Effect of high-accuracy enhancement by use of multifiber and reduction in depth of field
Fig. 13 shows the dispersion of scanning measurement results of scanning measurements for a standard roughness piece with 3.2 μm Rz using the conventional sensor with a single core fiber and a sensor head with four-core multi-fiber for which the depth of field was reduced. The dispersion of scanning measurement was improved by approximately 5.7 times because the dispersion of scanning measurement value of 4σ was 18.1 μm with the conventional sensor and was 3.1μm with the new sensor. Moreover, the results of the new sensor were almost the same as the 3.2 μm RZ, value of the standard piece, which led us to believe the shape was properly measured.
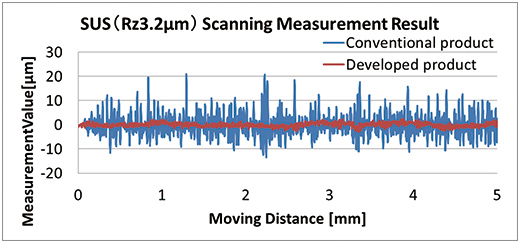
5.2 Results of high-accuracy enhancement by algorithm for correcting waveform slope
Fig. 14 shows the results of the measurement value correction after the scanning measurement of a standard roughness piece of 3.2 μm Rz and determining the correction value according to the slope of the receiving light waveform. We confirmed that the dispersion of scanning measurement values was approximately 9 μm between the maximum and minimum values before correction and became 3μm after correction, which meant that accuracy was improved by approximately three times.
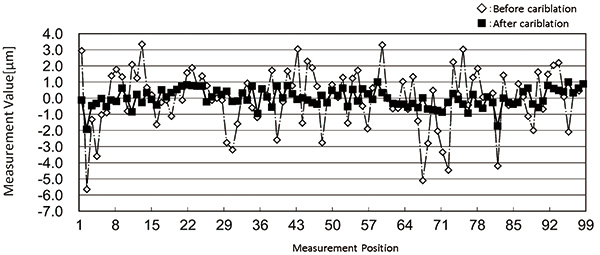
5.3 Results of increase in speed
Table 2 shows the results of the increase in speed expressed by the amount of light received with each device. The results achieved 11.7 times the conventional amount in total. Table 3 shows the amount of light received and the fastest sampling time for measuring a mirror. The amount of light received was 12.5 times the conventional amount, which was almost the same as the total amount of light received by each device, and that value could be measured for 20 μsec, which was the fastest sampling time. For an object with 10% of the reflectance being measured, only 20 μsec was necessary to receive the amount of light required for measurement. Therefore, even though the scanning measurement was conducted at the moving speed of 500 mm/s, an object being measured could be measured at a 10 μm pitch.
Item | Amount of light received |
---|---|
White LED luminousness | 5.1 times compared to conventional model |
Multi-fiber | 4 times compared to conventional model |
Low-noise CMOS | 2.3 times compared to conventional model |
Transmissivity of sensor head | 0.25 times compared to conventional model |
Total | 11.7 times compared to conventional model |
Received power/μsec | Fastest sampling time | |
---|---|---|
Conventional sensor | 48 | 500μs |
New sensor | 600 | 20μs |
6. Conclusion
We achieved high-accuracy measurements of 5.7 or more times compared to conventional models and sampling speeds as high as 20 μsec, which was 25 times faster than conventional models as shown in Section “5. Effect” by introducing multi-fiber and an algorithm to reduce the depth of field and correct the waveform slope as coaxial white light confocal technology, and we then commercialized the displacement sensor type, the ZW-7000 series (see Fig. 15), based on this technology in April 2016.
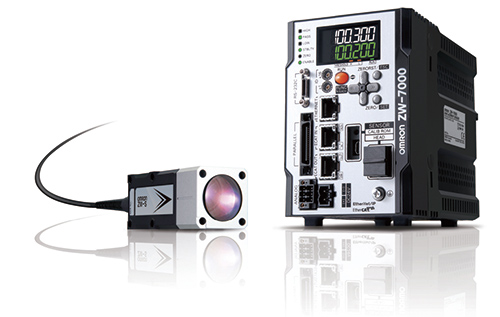
We established the technique of reducing the depth of field, created an algorithm to correct waveform slope, and developed a multi-fiber technique to improve the stability of scanning measurements in enhancing the high accuracy and high speed for displacement sensors. With the use of the algorithm for
correcting waveform slope, the mechanical acquisition of waveform slopes and errors allows corrections to be made, and artificial intelligence (AI) reduces measurement errors by the sensor. In addition, although a doublet has been conventionally used as an objective lens to control aberrations for higher accuracy, even a single lens can enhance high accuracy by using the algorithm for correcting waveform slope, which can be one of the measures to reduce costs.
In order to respond to customer needs such as reduction in weight and size and increase in inspection items, we would like to promote further reductions in size, the enhancement of high accuracy, and improvements in longer distance-measuring with the displacement sensor on the basis of this technology in the future.
References
- 1)
- Omron. Confocal measurement device. Japan patent JP5790178B.
- 2)
- Omron. Optical measuring device. Japan patent JP2017-102067A.
The names of products in the text may be trademarks of each company.