機構デバイス向けの低温短時間加熱硬化と高耐熱機能を有する一液性エポキシ樹脂の開発
- 一液性エポキシ樹脂
- 熱分析
機構デバイスに使用される異種材接合用接着剤として、一液性エポキシ樹脂はその高い強度および使いやすさの観点から広く利用されている。当社においても一液性エポキシ樹脂をリレーやスイッチなどの機構デバイスに採用してきた。近年、有害化学物質の排除という観点から、鉛フリーはんだ実装の普及に伴う実装温度の上昇により、機構デバイスの耐熱性向上も求められている。一方、環境への配慮が高まる中、製造工程における低エネルギー消費が求められており、低温短時間での加熱硬化が必要とされている。本研究では、主剤と硬化剤の反応機構に基づいて一液性エポキシ樹脂の配合を調整し、耐熱性および低温短時間硬化を実現した。本論文はその技術内容について報告する。
1. まえがき
リレーやスイッチなどの機構デバイスは、家電機器、車両、通信機器など様々な用途に使用される制御部品として不可欠なものである。リレーには、開放タイプと気密タイプの2種類が存在する。開放タイプのリレーはケースがない、またはケースが接着されていないものである。気密タイプのリレーはケースとベースが接着され、密封されている。この気密タイプのリレーは、基板実装時のハンダフラックスや周囲環境からの異物、腐食ガスなどの侵入による接触障害を防止するために、接着剤で気密封止されている。気密性以外にも、塗布および硬化の生産性、基材との接着性、絶縁物の表面に生じる放電によるトラッキングを防ぐ耐トラッキング性などが求められる。当社でも、これらの特性を満たす一液性エポキシ樹脂の接着剤を利用している1-3)。
一液性エポキシ樹脂は、一般的に液状の主剤、固形の硬化剤、無機物のフィラーから構成される。主剤と硬化剤は加熱によって化学反応を起こし、液体から固体へと変化して固化する。この固化により、成形体同士を接着させることが可能となる。我々は、これらの成分を改良し、機構デバイスの要求特性に適合する一液性エポキシ樹脂をこれまでに開発してきた4-6)。
近年、有害化学物質の排除を目的とした表面実装の普及に伴い、実装工程の処理温度が高くなっている。また、従来主流であったスルーホール実装では、基板の一部が数秒程度溶融はんだに接触するだけであったが、表面実装では、リフローと呼ばれる加熱工程において基板全体を30秒以上はんだ溶融温度に保つことが求められる。したがって、表面実装用の電子部品に用いる一液性エポキシ樹脂には、リフロー工程に耐える高耐熱性が要求される。一方で環境負荷低減の観点から、一液性エポキシ樹脂の硬化時におけるエネルギー消費の削減も重要な課題となっており、低温短時間で硬化できる性能も求められる。
リフロー工程における耐熱性の確保を目的として、一液性エポキシ樹脂に高耐熱性を付与するためには、樹脂そのものの耐熱性を向上させる必要がある。つまり一液性エポキシ樹脂を構成する主剤または硬化剤の改良アプローチが考えらえる。これまで耐熱性を向上させる方法として、主剤側の改良が選択されてきた。具体的には、フェノールやナフタレン骨格を持つ芳香族を多く含む主剤を用いることで、硬化物の耐熱性を向上させることが報告されている1)。しかし、これらの主剤は固体であるため、主剤を溶解してから硬化反応を行う必要があり、その結果として硬化温度が高くなる。このように耐熱性と低温短時間硬化は共に要求される特性であるが、相反する特性でもある。
これらの相反する特性を両立する既存の方法が提案されているが、いずれも樹脂や製造工程の大幅な変更が求められる上、実用上の課題もある。例えば、二液性エポキシ樹脂は、主剤と硬化剤を常温で混合するだけで固化し、エネルギー消費が低いという利点がある。また、UV硬化型樹脂は、樹脂内で光重合反応が起こり、液体が固体に変わる化学反応である。UV硬化型樹脂の構成要素は主剤(液体)と光開始剤から構成される。UV照射による光エネルギーを受けると、室温下でも光開始剤がモノマー(液体)に作用し、光ラジカル重合と呼ばれるモノマー同士を高速で反応させる重合タイプであるため、樹脂(固体)へと瞬時に変化する。このように、室温下でも硬化速度が非常に速い特性を持つため、短時間での硬化およびエネルギー消費の削減1)につながるという利点がある。しかし、二液性エポキシ樹脂と光硬化型樹脂ともに、十分な強度や耐熱性を確保できないため、現状では機構デバイス向けの接着材としては用途が限定される。さらに、光硬化樹脂においては、光が照射されない影の部分が硬化しないため、UVが届かない場所では樹脂が未硬化となり、強度不足などの問題を引き起こす可能がある。
以上より耐熱性と低温短時間硬化の相反する特性を両立するためには、新しいアプローチで一液性エポキシ樹脂での改善が必要不可欠と考えた。本研究では主剤と硬化剤の反応機構に基づき、一液性エポキシ樹脂に含まれる硬化剤の成分を検討し、耐熱性および低温短時間硬化を実現した。本論文はこの技術内容について報告する。
2. 一液性エポキシ樹脂の組成と評価方法
2.1 一液性エポキシ樹脂の作製
一液性エポキシ樹脂は、樹脂成分である主剤および硬化剤、強度を補強するための無機フィラー、ならびに各種添加剤で構成される。本研究は、化学反応と効果を明確にするために、主剤と硬化剤のみを用いて組成を検討した。主剤には、ビスフェノールA型の一般的なエポキシ樹脂(以下、エポキシ樹脂モノマーと称する)を使用した。硬化剤は、エポキシ樹脂用の一般的なアミンアダクト系硬化剤、シアナミド系硬化剤およびイミダゾール系硬化剤の三種類を用いた。
アミンアダクト系硬化剤は潜在性硬化剤と呼ばれ、比較的低温で硬化が促進される特性を有する硬化剤である。シアナミド系硬化剤は、二級アミン型の付加反応を引き起こすことで知られており、耐熱性および金属との接着性を付与することが可能である1)。なお、アミンアダクト系硬化剤は、低温でエポキシ樹脂を硬化させることができる硬化剤としてよく知られている。
イミダゾール系硬化剤は連鎖移動型アニオン重合反応を誘起するため、触媒作用により少量の添加でもエポキシ樹脂モノマーに対して、3次元的に高分子反応が進む。そのために耐熱性の付与が期待できる硬化剤の1つである1)。
シアナミド系硬化剤は熱硬化性樹脂の典型的な硬化剤である7)。一液性でポットライフが長く、エポキシ樹脂内のヂシアンヂアミドは三次元で非常に密接しており、硬化物の機械的、化学的特性に優れ、電子部品向けの接着剤の硬化剤として利用される。この硬化剤は高温まで上げないと、硬化が進まないとされる。
上記の硬化剤の特性より、Sample 1から3の組成はそれぞれの低温での硬化性を見極めることとした。Sample 4から6の組成は、低温での硬化が優位とされるアミンアダクト型硬化剤とその他の硬化剤を併用する配合とした。
樹脂の作製方法について述べる。表1に示す重量比率を基に主剤と硬化剤の総重量が3 kgになるようにプラスチック容器に計量した。その後、エポキシ樹脂モノマーの液体と硬化剤などの粉末が均一に分散するよう攪拌機と三本ロールで混合した。なお、比較のため機構デバイス用市販品の一液性エポキシ樹脂も評価しデータを取得した。
エポキシ樹脂の組成 (重量部) |
Sample | ||||||
---|---|---|---|---|---|---|---|
1 | 2 | 3 | 4 | 5 | 6 | ||
主剤 | ビスフェノールA型 エポキシ樹脂 |
100 | 100 | 100 | 100 | 100 | 100 |
硬化剤 | アミンアダクト系 硬化剤 |
3 | 3 | 3 | 3 | ||
シアナミド系 硬化剤 |
3 | 3 | 3 | ||||
イミダゾール系 硬化剤 |
3 | 3 | 3 |
2.2 評価方法
低温短時間硬化および耐熱性機能について、一液性エポキシ樹脂を以下の方法で評価した。
2.2.1 低温短時間硬化の評価方法
一液性エポキシ樹脂の化学反応を詳細に分析するため、示差走査熱量分析装置(DSC)と赤外線分光装置(FT-IR)を用いて解析した。
(1)DSC
一般的にエポキシ樹脂モノマーと硬化剤に熱を加えることで発熱反応を引き起こし、樹脂は硬化する。DSCは試料の吸熱・発熱に伴う熱流の変化を検知し、この発熱反応を検出することができる。さらにDSCの温度条件を工夫することで、一液性エポキシ樹脂の化学反応の温度依存性を解析することが可能である。例えば、オーブンの温度を一定に保つことで、一定温度での反応終了時間を明らかにすることができる。また、温度を室温から高温域に昇温することで、反応の開始温度も検出可能である。本研究では、熱分析の温度条件として以下の2つのプロファイルを採用した。
- 120℃一定
- 50℃から200℃までの昇温
低温短時間硬化の温度を120℃に設定した理由は以下の通りである。一般に温度を上げるほど短時間で硬化が可能となるが、同時に環境負荷も増加する。そのため、低温での硬化を優先的に考慮し、一般的に硬化剤の融解が終了する温度である120℃を熱硬化温度として設定した。なお、低温短時間硬化の目標値は、120℃温度一定の条件下で市販品より短い時間で硬化反応を終えることとした。
(2)FT-IR
FT-IRは試料に赤外光を照射し、透過または反射した光量を測定する。赤外光が分子結合の振動や回転運動のエネルギーとして吸収されるため、FT-IR測定によって分子の構造や官能基の情報をスペクトルから得ることができ、物質の同定に関する有効な情報を得ることができる。また、吸収する光量は物質の濃度や厚みに比例することから、スペクトル上のピークの高さや面積を用いて特定の分子の定量もできる。
FT-IR測定からエポキシ基の反応に関与するエポキシ環のピークは赤外領域の918 cm-1付近で検出され、そのピークの変化を通じて化学反応(硬化反応)の進行を追跡することが可能である。具体的には加熱によりエポキシ樹脂モノマーが化学反応を進行させる過程で、エポキシ基が開環してエポキシ樹脂モノマー同士が結合するため、このエポキシ環のピークは減少する。さらに化学反応が進行すると、このピークは最終的に消失し、エポキシ樹脂が完全に固化したことを示す。FT-IR分析はKBr透過法により、500から2000 cm-1までの赤外線スペクトルを取得した。
2.2.2 耐熱性の評価方法
耐熱性は、材料の観点と実機での両方の評価が必要と考え、動的粘弾性測定(DMA)およびリフロー耐熱性試験を実施した。
(1)DMA
DMAは試験片に時間変化する歪みまたは応力を与え、その結果生じる応力または歪みを測定することで、試料の力学的特性を評価する手法である。この測定により、力学特性の温度依存性に基づく一液性エポキシ樹脂の耐熱性を明らかにすることができる。具体的には、DMAを用いて試験片の粘弾性特性である貯蔵弾性率(E’)、損失弾性率(E”)、および損失正接(tanδ = E”/E’)の温度依存性および周波数依存性を測定した。貯蔵弾性率(E’)の変化から樹脂の耐熱性を評価できるため、本研究ではE’ の温度依存性に着目した。実際の試験では、3 mm×5 mm×1.5 cmのフィルム状の試料を用い、25℃から250℃まで加熱しながら動的粘弾性を測定した。なお、耐熱性の目標値は市販品よりも優れていることとした。具体的には、力学特性E’の値が1.0×108 MPa以下に低下する温度を強度低下の閾値と設定し、この温度が市販品よりも高いこととした。
(2)リフロー耐熱性試験方法
リフローに対する耐熱性については、実機リレーを用いて評価を行った。実際の試験では、一液性エポキシ樹脂をリフロー耐熱性が要求される車載用リレーに塗布し、リフロー試験によりその耐熱性を評価した。温度条件はJIS C 60068-2-58:2020に準拠とした。リフロー試験後、気密性を確認するために90℃の高沸点フッ素系不活性液に浸漬し、発生する気泡の有無を観察した。このリフロー試験を3回繰り返し、一液性エポキシ樹脂のリフロー耐熱性を評価した。なお、リフロー耐熱性の目標値はJIS C 60068-2-58:2020の条件下で気密性試験をクリアーすることとした。
3. 評価結果と考察
3.1 DSCによる低温短時間硬化の評価結果と考察
120℃での硬化時間を評価するために、DSCの温度条件を120℃で1時間保持するように設定し、発熱エネルギーを測定した(図1(a))。なお、DSC測定装置は温度を120℃に短時間で到達させることが困難であるため、25℃から120℃までの昇温に約7分を要するよう設定した(図1(b))。図1(a)では、横軸に図1(b)の温度プロファイルに基づいた120℃の保持時間を示し、縦軸に発熱量を示している。この図から、一液性エポキシ樹脂の反応開始時間および終了時間を、発熱ピークの変化を通して読み取ることができる8)。
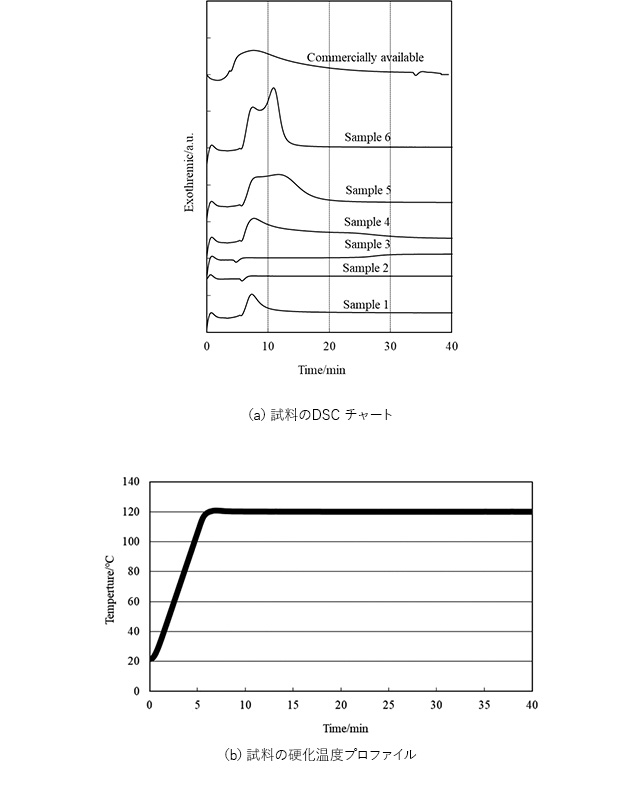
Sample 1では、約7分付近に急激な発熱ピークの立ち上がりが確認された。その後、発熱エネルギーが約15分まで緩やかに減少した。これにより、15分付近で化学反応が終了したことが示唆される。一方、Sample 2およびSample 3では発熱ピークが全く確認されなかった。これは、これら2つの硬化剤を単独で使用した場合、120℃では一液性エポキシ樹脂が反応しないことを示唆する。
二種類の硬化剤を用いたSample 4とSample 5では、アミンアダクト系硬化剤の硬化反応に由来する約7分付近の発熱ピークの立ち上がりが確認され、40分および25分付近でそれぞれ発熱エネルギーの消失が認められた。これは、アミンアダクト系硬化剤の添加により、イミダゾール系硬化剤とシアナミド系硬化剤の両方の反応が促進されたことを示唆している。三種類の硬化剤を添加したSample 6でも、7分付近に急激な発熱ピークの立ち上がりが確認され、15分付近で発熱エネルギーの消失が認められた。
以上の結果より、硬化に必要な時間はSample 1とSample 6が最も短く、以下、Sample 5、Sample 4の順であった。なお、市販品の一液性エポキシ樹脂を同様の温度プロファイルで測定した結果(図1:commercially available)では、発熱エネルギーの減衰に約40分を要した。したがって、Sample 1、Sample 5およびSample 6の一液性エポキシ樹脂は、市販品よりも低温短時間硬化において優位性があると判断した。
さらに、硬化剤の反応性要因を明確にするため、Sample 1からSample 6までの一液性エポキシ樹脂を50℃から250℃まで10℃/minで昇温し、反応開始温度を分析した(図2)。
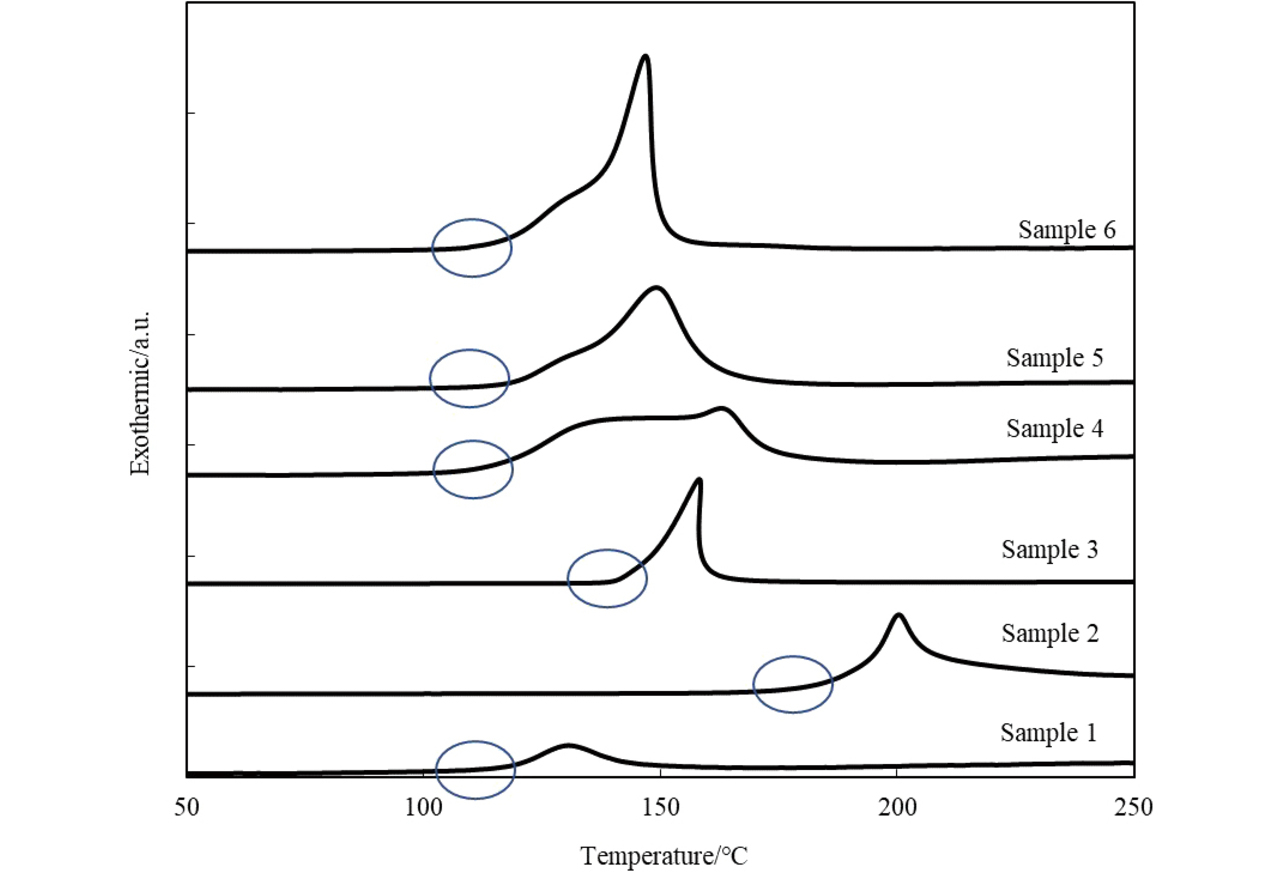
図2は、横軸に温度、縦軸に発熱エネルギーを示している。Sample 1からSample 3のDSC測定結果から、発熱ピークの立ち上がりがそれぞれ100℃、180℃、140℃で観察された。Sample 2およびSample 3では、120℃以下で発熱ピークは観察されなかったため、120℃の温度条件下では硬化反応が進まないことが示唆された。これは、図1(a)に示すように、120℃一定条件下で発熱ピークが観察されなかった結果と一致している。
Sample 4および、Sample 5、Sample 6はSample 1と同様に、100℃から110℃付近での発熱ピークの立ち上がりが観察された。これらの共通点は、アミンアダクト系硬化剤を含んでいることであり、この硬化剤を用いると反応開始温度が低下することが確認された。Sample 1でも発熱エネルギーは認められるものの、発熱ピーク面積が小さいこと、また硬化物がゲル状であったことから、エポキシ樹脂の化学反応が十分に進行しなかったと推定される。これを確認するために、次にFT-IR測定で硬化度合いを確認した。なお、Sample 2およびSample 3については、120℃での硬化が不十分であるため、以後の検討から省略する。
3.2 FT-IRによる低温短時間硬化の評価結果と考察
Sample 1とSample 4からSample 6の各種試料を120℃1時間で加熱したときのFT-IRチャートを図3(a)から(d)に示す。なお、図の左に記載されている数値は加熱時間を示す。
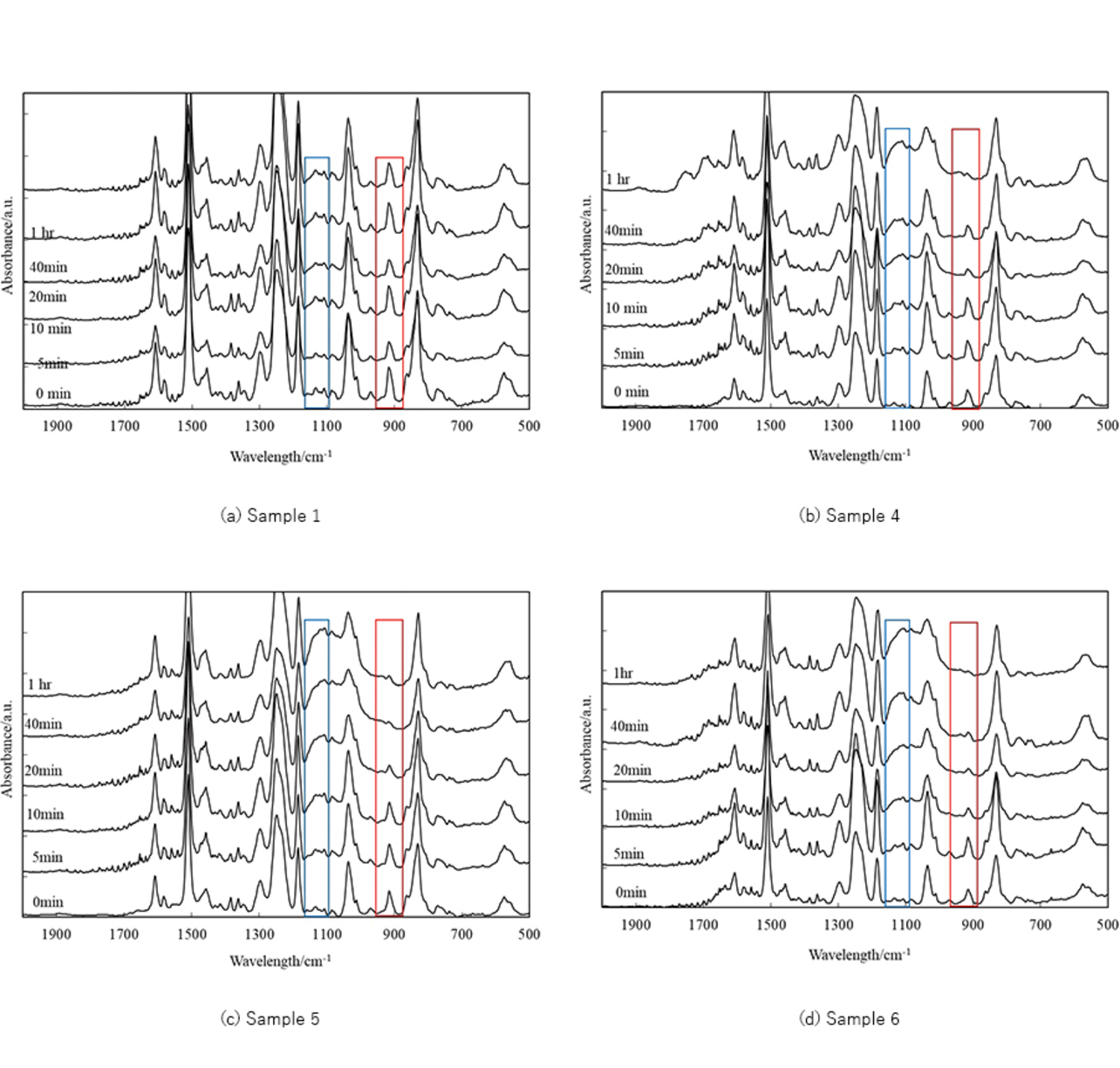
硬化剤としてアミンアダクト系硬化剤のみを含むSample 1のFT-IRチャートを図3(a)に示す。Sample 1では、40分以降でも918 cm-1のピークが多く残存しており、未反応のエポキシ樹脂が存在していることが確認された。従ってアミンアダクト系硬化剤のみでは局所的な反応に留まり、硬化が不十分であった。
次に、アミンアダクト系硬化剤とシアナミド系硬化剤またはイミダゾール系硬化剤を含むSample 4およびSample 5のFT-IRチャートを図3(b)および図3(c)に示す。Sample 1と同様に、エポキシ基の開環反応を示す918 cm-1のピークの減少と、エーテル基由来の1190 cm-1付近のピークの増加が確認され、化学反応の進行が示唆された。さらに、Sample 4およびSample 5では、加熱20分後にはエポキシ環に由来するピークが大きく減少した。加えて、3種類の硬化剤を含むSample 6(図3(d))においても、918 cm-1のピークの減少が確認され、同様に化学反応が進んでいることが示唆された。
3.3 耐熱性の評価結果と考察
次に、一液性エポキシ樹脂の耐熱性を評価するために、DMA測定をした(図4)。
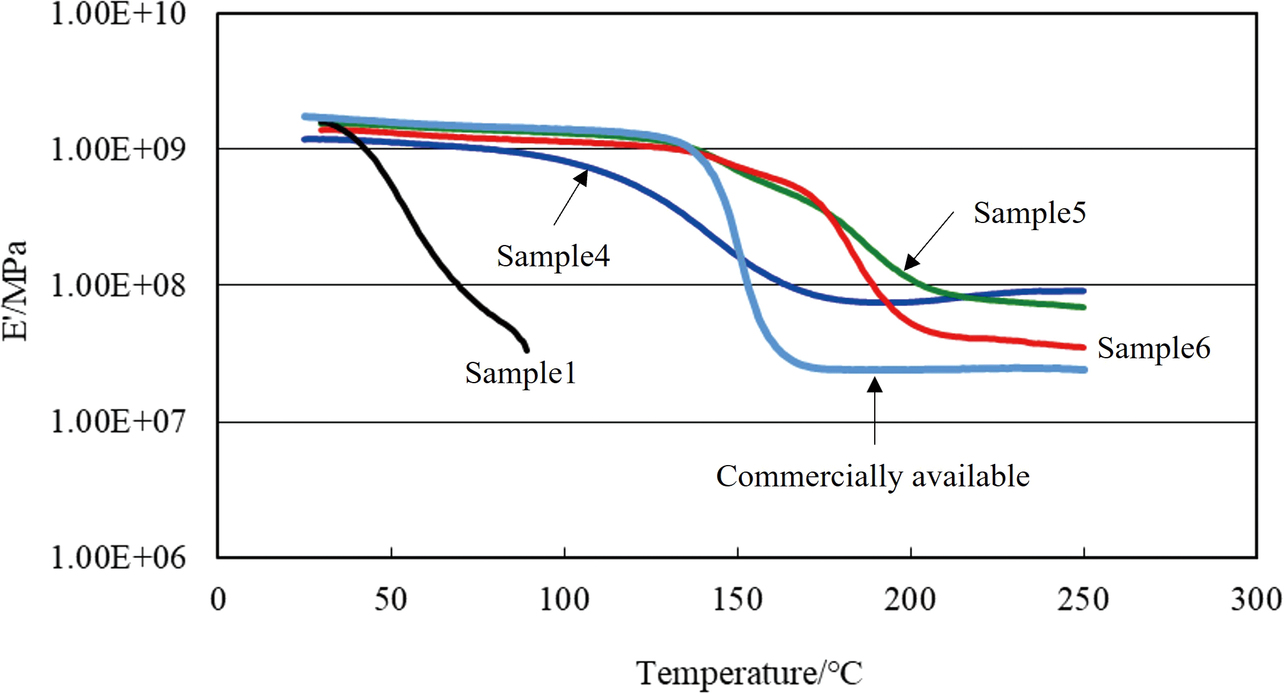
図4に、力学特性を示す貯蔵弾性率(E’)の温度依存性データを示す。力学特性E’の値が1.0×108 MPa以下に低下する温度を強度低下の閾値と設定した。Sample 1では、室温付近からE’が低下し、70℃付近でE’の値が1.0×108 MPa以下になった。一方、Sample 4では150℃付近、Sample 5およびSample 6では、それぞれ200℃および190℃付近でE’の値が1.0×108 MPa以下に低下した。
Sample 4とSample 5の耐熱性の違いは、それぞれの硬化剤の特徴によると考えられる。イミダゾール系硬化剤は連鎖移動型の硬化剤であり、主剤の重合度を上げることができる。このため、一液性エポキシ樹脂の架橋が高密度化し、耐熱性が向上したと推測される。一方、シアナミド系硬化剤は連鎖移動型の硬化剤ではないため、同様の耐熱性向上効果が得られなかったと推測される。
3.4 低温短時間硬化と耐熱性との関係
表2に、これまでの低温短時間硬化と耐熱性の関係をまとめた。表2より、これらの2つの特性を両立する一液性エポキシ樹脂として、3種類の硬化剤を混合したSample 6が最も望ましいと判断した。さらに、市販品と比較しても、Sample 6が優れた特性を有していた。
要求性能 | Sample 1 | Sample 2 | Sample 3 | Sample 4 | Sample 5 | Sample 6 | 市販品 |
---|---|---|---|---|---|---|---|
低温短時間硬化 | × | × | × | △ | △ | ◯ | △ |
耐熱性 | × | ― | ― | × | ◯ | ◯ | × |
3.5 リフロー耐熱性試験
低温短時間硬化と耐熱性を両立したSample 6を用いて、リレーのリフロー耐熱性試験を実施した。試験に先立ち、リレーのベース表面にこの一液性エポキシ樹脂を塗布・硬化させた。試験の結果、3回繰り返しても気泡漏れは認められず、気密性は維持された。従って、実機評価においても高い耐熱性を維持できる一液性エポキシ樹脂であることが証明できた。なお市販品では、同じ気密試験の目標値を満足できなかった。
4. むすび
有害化学物質の排除および環境への配慮といった社会の要請に応えるため、異種材接合用接着剤において耐熱性の向上と低温短時間硬化の両立が課題であった。本研究では、機構デバイスの異種材接合用接着剤として使用される一液性エポキシ樹脂を対象とし、この配合を調整することで課題解決した。アミンアダクト系硬化剤の触媒作用により120℃付近での化学反応を促進させ、シアナミド系硬化剤およびイミダゾール系硬化剤を併用することで、120℃において20分以内で硬化する方法である。また、イミダゾール系硬化剤の連鎖移動型触媒作用により耐熱性を190℃付近まで向上し、硬化剤の特徴をもとに耐熱性と低温短時間硬化を両立できる一液性エポキシ樹脂を開発した。さらに、耐熱性においては、実機リレーを用いたリフロー試験で気密性の維持も確認した。
以上より、化学反応の原理に基づいた一液性エポキシ樹脂の設計が、優れた特性を持つ製品の開発に寄与することを示した。当社では、同様のアプローチで開発した一液性エポキシ樹脂を商品で利用している。
今後、さらなる環境負荷低減を目指すためには熱硬化性樹脂を用いるのではなく、1章で述べたUV硬化型樹脂および二液性エポキシ樹脂などの開発が必要と考える。このためには、主剤や硬化剤の分子構造などの改良から必要であり、今後の課題である。
参考文献
- 1)
- 垣内弘, エポキシ樹脂, 第1~4巻. エポキシ樹脂技術協会, 2003.
- 2)
- 桑原涼 他, “長期高精度塗布SMD接着剤の開発,” Matsushita Tech. J., vol. 54, no. 1, pp. 19-23, 2008.
- 3)
- 福原智博, “エレクトロニクスデバイスにおける接着技術,” 電子情報通信学会技術研究報告, 2009, OPE2009-104.
- 4)
- 福原智博, “機構デバイスにおける封止信頼性,” 電子情報通信学会技術研究報告, 2009, R2009-34.
- 5)
- 森井真喜人, “接着剤の接合信頼性評価に関する検討,” 電子情報通信学会技術研究報告, 2007, R2006-47.
- 6)
- 達野陽介 他, “ポリカーボネートケースを使用したリレーの封止信頼性の改善,” 電子情報通信学会技術研究報告, 2012, R2011-42.
- 7)
- M. D. Gilbert et al., “Mechanism of the dicyandiamide/epoxide reaction,” Macromolecules, vol. 24, no. 2, pp. 360–369, 1991.
- 8)
- 神戸博太郎, 小沢丈夫, 熱分析, 講談社, 1992.
本文に掲載の商品の名称は、各社が商標としている場合があります。