0402から大型部品までの混載実装を可能にするはんだ振動印刷技術
工業製品の高機能化により、製品を構成する基板上に実装される部品サイズは、従来の1608(1.6×0.8mm)や1005(1.0×0.5mm)から、0603(0.6×0.3mm)や0402(0.4×0.2mm)が主流になると予想される。FA機器でこれらの部品を使用するには、大型部品との混載が不可欠である。部品と基板配線を電気的に接続するはんだは、大型部品が求める量から0402 が求める少量までを安定供給する事が求められる。この高アスペクト比のはんだ供給を印刷工法で行うため、はんだ特性、マスク表面加工、基板パターン寸法、振動印刷技術を評価した。本取り組みでは、材料の選定要素と振動印刷技術の効果を求めることで、前回取り組み1)の2.4 を超えるアスペクト比2.7(マスク厚0.12mm、開口寸法Φ 0.18mm)で体積率Cpk1.80 を達成した。
1.まえがき
工業製品の最近の情勢は、通信機能やAI 処理機能の追加、処理情報量の増加により、電子機器の高機能化・高付加価値化が図られている。そのため、電子機器を構成するプリント配線板は小さくなり、搭載する部品点数は増加する。これにより、搭載部品の寸法は小さくなり、0603 や0402 といった部品が主流になってくる2)。FA 機器においては、0402からコネクタなど大型部品までを、混載することが求められる。混載の課題の一つに、はんだ印刷工法による高アスペクト比の安定印刷が挙げられる。そのため、前回はアスペクト比2.4 の安定はんだ印刷に取り組んだ。
本稿では、アスペクト比2.7 のCpk1.80(印刷結果の体積率の工程能力指数を表し、基準は下限50%の上限170%とした)を目標とした取り組みについて記載する。振動印刷の取り組みについては、実際の振動現象を測定して、振動量と印刷性の関係性を評価した。
2.高アスペクト比のはんだ印刷課題
はんだ印刷は、マスク開口にペースト状はんだ(以下、はんだと表記)を供給(以下、充填と表記)し、プリント配線板(以下基板)を下降させて、電極パターンの上にマスク開口形状のはんだを転写する。この際、図1に示すように、はんだが基板の電極パターンに粘着する力と、マスク開口内壁に粘着して基板下降時(以下、版離れと記載)のマスクとはんだ間に生じる摩擦力(以下、ずり応力と記載)とのバランスにより、安定した印刷が行えるかが決まる。これらの力は、はんだの接触する面積に比例し、この面積比をアスペクト比として表す(図2 参照)。はんだ印刷技術においてはアスペクト比が重要な因子であり、この値が大きくなると印刷難易度が増すことが知られている3)。はんだが基板に接触する面積よりもマスクと接触する面積が増すことで、ずり応力が大きくなる。これにより、マスク開口内部にはんだが残りやすくなり、基板に転写する体積が減少する。アスペクト比を小さくするには、マスクを薄くすることが有効である。しかし、同一基板上にリード高さバラツキの大きいコネクタなどが搭載される場合、これらの部品の供給はんだ量不足により接合強度が低下する問題が生じる。そのため、小型部品を印刷する場合にマスク厚を薄く出来ない。FA 機器ではマスク厚0.12 mm が主流であり、0402 の開口面積で印刷する際のアスペクト比は2.4 となる。
前回の取り組みでは、レオメータではんだの粘弾特性を測定して、ずり応力を低減させるように版離れ速度を最適化した。この取り組みの中で、はんだ特性に応じて、マスク表面コートや版離れ制御などの印刷条件を最適化することが重要だとわかった。一方、アスペクト比が2.7 と大きくなると、図3に示すように、はんだ高さの低下とマスク開口のはんだ目詰まりが多くなる。これは、はんだが基板パターンに十分に接触しないため、基板とはんだが粘着する力が不足することが原因と考える。この課題に対応するため、はんだ特性とマスク表面コート、基板パターンとマスク開口寸法の関係性、振動を用いた印刷法について評価した。
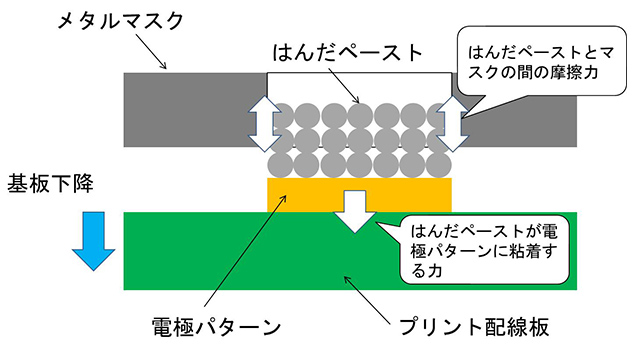
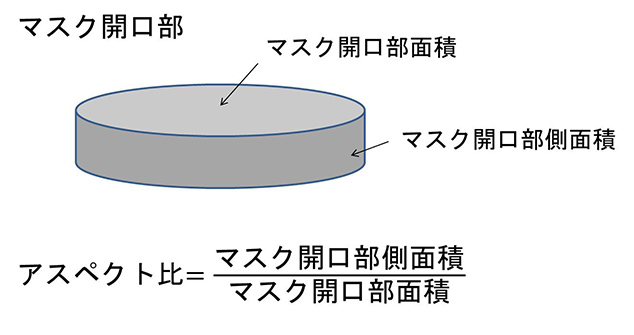
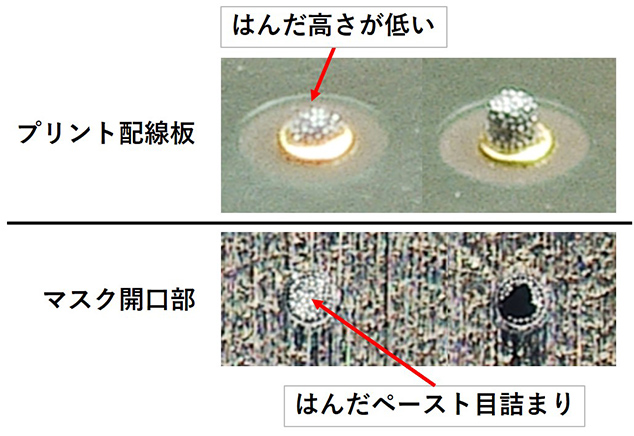
3.はんだ、マスク表面コートおよび基板パターン設計の印刷影響評価
3.1 評価内容
はんだは新たに評価するAと、前回の取り組みで使用したはんだBを、マスク表面コートは、はんだとの摩擦力を評価するために親水(親油)コートと撥水(撥油)コートを用いた。基板は、マスクとパターンをより密着させるためソルダレジスト厚を銅箔厚より薄くし、マスク開口を基板パターンより大きくした。
はんだの仕様を表1、基板を表2 に、評価した基板パターンとマスク開口の寸法関係を表3 に示す。
はんだ | 粒径 | 粘度Pa・s | フラックス含有量Wt% |
---|---|---|---|
A | 20-38μm | 117 | 11.5 |
B | 10-15μm | 183 | 11.5 |
項目 | 内容 |
---|---|
寸法(mm) | 115×180 t1.6 |
パターンサイズ(mm) | ϕ0.16、ϕ0.18、ϕ0.20、ϕ0.22、ϕ0.24、ϕ0.26、ϕ0.28、ϕ0.30、ϕ0.32 |
ソルダレジスト厚 | 25μm |
銅箔厚 | 35μm |
表面処理 | 無電解薄付けAuめっき |
シルク | 無し |
評価基板 | パターン径mm | 0.20 | 0.22 | 0.16※ | 0.18※ | |
---|---|---|---|---|---|---|
マスク | 開口径mm | 0.16 | 0.18 | 0.16 | 0.18 | |
加工基準面のアスペクト比狙い | 基盤 | 3.0 | 2.7 | 3.0 | 2.7 | |
スキージ | 2.8 | 2.5 | 2.8 | 2.5 |
※基板パターン径とマスク開口径が同径(従来の設計)
3.2 実験条件
評価で用いた印刷条件を表4 に示す。はんだ印刷時の基板の反りの影響を排除するため、印刷時は装置の基板吸着機能を用いて矯正し、基板が平面となるようにした。印刷結果は、はんだ印刷検査機(CKD製VP-6000M)でレジスト開口パターンについて定量化した。実験は、条件毎にマスクの洗浄を行い、マスクに付着したはんだ残渣の影響を排除した。基板を8 シート印刷して、印刷が安定する3シートから8 シート目までの6 シート分のデータにより印刷性を評価した。
印刷機 | Panasonic製:SP-60 |
---|---|
スキージ | メタル(出代10mm) |
基板バックアップ | ベタ冶具、専用吸着BOX |
印刷速度 | 50mm/sec |
印圧 | 35×10-2N |
アタック角度 | 60° |
クリアランス | -0.2mm |
版離れ | 等速10mm/s |
ストローク 3mm | |
下受け優先 | |
版離れ待ち時間 | 0 |
3.3 評価結果
各はんだと各マスクを組み合わせて評価した体積率のCpk を表5 に示す。はんだの差は、マスク表面コートとアスペクト比に関係なく、A がB よりCpk の値が高くなり、優位性があると考える。マスク表面コートは、アスペクト比が2.7 より大きい場合に、はんだに関係なく親水コートが撥水コートより高くなった。
表6 に、アスペクト比2.7 の体積率のCpk を示す。この結果から、はんだに関係なく基板パターンをマスク開口より大きくしたことにより、Cpk が向上していることがわかる。
これらの因子の最適な組み合わせで印刷した結果、体積率のCpk は0.87 であった。
設計アスペクト比 | |||||
---|---|---|---|---|---|
はんだ | マスク | 3.0 | 2.8 | 2.7 | 2.5 |
A | 撥水コート | 0.14 | 0.18 | 0.69 | 1.47 |
親水コート | 0.23 | 0.34 | 0.87 | 1.90 | |
B | 撥水コート | 0.00 | 0.00 | 0.21 | 0.54 |
親水コート | 0.00 | 0.00 | 0.26 | 0.39 |
※スペック 50%<印刷体積<170%
はんだA | はんだB | |||
---|---|---|---|---|
寸法関係 | 基板=マスク同径 | 基板>マスク | 基板=マスク同径 | 基板>マスク |
撥水コート | 0.62 | 0.69 | 0.09 | 0.21 |
親水コート | 0.84 | 0.87 | 0.18 | 0.26 |
※アスペクト比2.7 が対象。
3.4 考察と課題
マスク表面コートの結果について考察する。撥水コートに対する、親水コートの高さと面積率の増減を表7 に示す。親水コートは、撥水コートに比べて面積率は増加し、高さは減少した。このことから親水コートは、充填時にはんだがマスク開口に流れ込みやすくなり、基板パターンの濡れ広がりが大きくなる。これにより、接触面積が増加して高さが減少したと考える。撥水コートは、はんだとマスクが反発するため、マスク開口が小さい場合は、はんだが流れ込みにくくなると考える。これらのことから、親水コートは高アスペクト比の印刷で優位性があったと考える。
次に、基板パターンの効果について考察する。基板パターンとマスク開口が同径に対して、基板パターンを大きくした場合の、高さと面積率の増減を表8 に示す。この結果、はんだとマスク表面コートに関係なく面積率が増加した。これは、基板とマスクを密着させて、はんだを基板パターンに十分接触させることを狙った通りの結果であった。
これら高アスペクト比の印刷に優位な材料選定と基板設計を行っても、アスペクト比2.7 の印刷では依然としてマスク開口内部のはんだ目詰まりが発生する。これは、基板パターンとはんだの粘着する力が不足しているためと推定し、よりはんだを基板パターンに十分接触させるための推進力(エネルギー)の向上が必要と考えた。
はんだA | はんだB | |
---|---|---|
高さ平均 | 3%減少 | 増減なし |
面積率平均 | 2%増加 | 5%増加 |
※撥水コート印刷結果に対する、親水コートの増減を表す。
はんだA | はんだB | ||
---|---|---|---|
撥水コート | 高さ平均 | 6%減少 | 5%増加 |
面積率平均 | 20%増加 | 16%増加 | |
親水コート | 高さ平均 | 6%減少 | 1%減少 |
面積率平均 | 18%増加 | 12%増加 |
※寸法同径の設計(基板=マスク)に対する、基板>マスク設計の増減
4.振動を用いた印刷評価
4.1 評価内容
充填するはんだ量を増やすための因子として、印刷機はスキージのアタック角、移動速度、印圧などの印刷条件と、はんだは粘度が挙げられる。しかし印刷条件を最適化しても、高アスペクト比においては、基板パターンにはんだを十分接触させるための推進力は得られないと考える。また、はんだの粘度は低くするほど、はんだの滲みやダレなど、印刷形状が悪化する。そこで、この推進力を得るために材料を振動させてはんだの流動性を向上させることを目的に、超音波振動の付加を評価した。これは、高周波の超音波振動により一時的にはんだの粘度を低下させた先行技術4)を参考にした。振動を用いた評価内容を表9 に示す。
振動を与えるため、図4 に示すように、振動子を基板ステージに取り付ける治具を作製し、振動子の負荷電圧を30V と100V に変更した場合の、振動の量を評価した。これには、レーザードップラー振動計を用い、基板ステージと評価基板およびマスクの、垂直方向の振動の量を測定した。
次に、振動の量と印刷の関係を求めるため、振動を付加しない場合(以下、負荷電圧0V と記載)と、負荷電圧を30V および100V に設定した場合で、3.2 項と同じ評価を行った。振動については、スキージが下降してマスクに接触してから版離れが完了するまで与えた。
また、マスク表面コートの影響を確認するため、親水コートと撥水コートについて、負荷電圧100V で評価した。
○···測定、評価の対象 | 負荷電圧V | |||
---|---|---|---|---|
0 | 30 | 100 | ||
振動の測定 | レーザードップラー振動計 | ○ | ○ | |
印刷評価 | はんだ:A マスク:コートなし |
○ | ○ | ○ |
はんだ:A マスク:親水コート |
○ | |||
はんだ:A マスク:撥水コート |
○ |
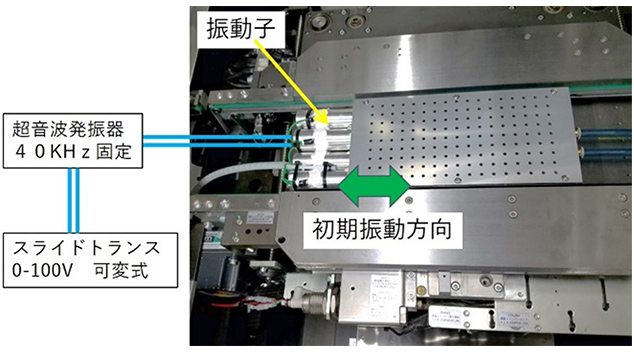
4.2 評価結果
振動測定の結果、基板ステージと評価基板およびマスクが振動していることが確認できた。アスペクト比2.7 の基板パターン位置の振動測定結果を表10 に示す。各測定部位の振動の量は、負荷電圧100V の時に、評価基板、基板ステージ、マスクの順に大きい。評価基板は、ガラスエポキシ樹脂と銅箔で構成され、これらの固有振動数が異なるため振動が増幅されて、評価基板の値が最も大きくなったと思われる。また負荷電圧30V では、評価基板と基板ステージが同じ振動の量となり、マスクが最も小さくなる。
振動量 | |||
---|---|---|---|
負荷電圧30V | 負荷電圧100V | ||
基板ステージ | 0.06μm | 0.10μm | |
評価基板 | 0.06μm | 0.20μm | |
マスク | 0.03μm | 0.06μm |
次に、負荷電圧により振動の量を変えた場合の印刷性を評価した。アスペクト比2.7 の印刷結果を、面積率を図5に、高さを図6に示す。負荷電圧を上げるほど、面積率は増加し、高さは減少することから、振動の量が大きくなると、はんだが濡れ広がると考えられる。また図7 に示すように、マスク開口部のはんだ目詰まりが負荷電圧100V の印刷で減少したことでも、はんだが基板パターンに十分に接触する面積が増加したと考えられる。
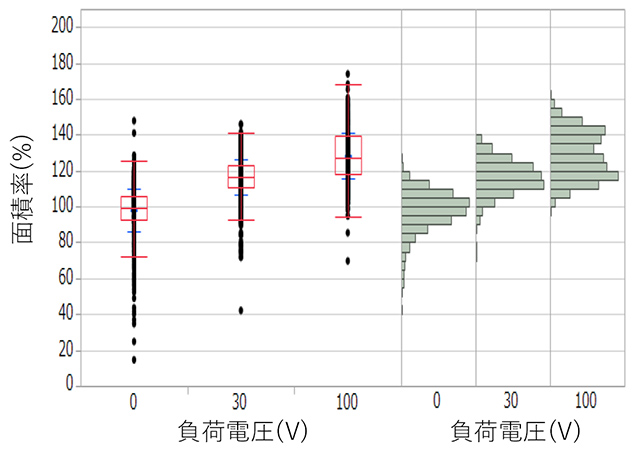
負荷電圧 | 平均(%) | 標準偏差(%) |
---|---|---|
0V | 97.8 | 12.0 |
30V | 116.4 | 9.8 |
100V | 128.3 | 12.9 |
図5 負荷電圧による、面積率平均の増減
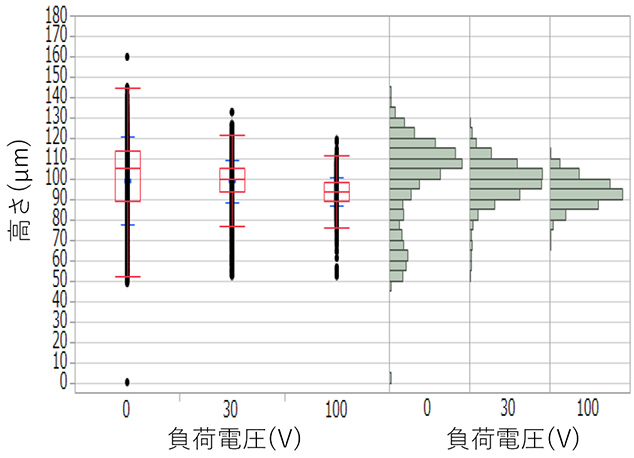
負荷電圧 | 平均(μm) | 標準偏差(μm) |
---|---|---|
0V | 99.1 | 21.7 |
30V | 98.7 | 10.1 |
100V | 93.5 | 6.9 |
図6 負荷電圧による、高さ平均の増減
使用後のマスク開口 | |
---|---|
負荷電圧0V | 負荷電圧100V |
![]() |
![]() |
図7 振動によるマスク開口のはんだ目詰まりの減少
マスク表面コート別の印刷結果を図8 に示す。表面コートに関係なく、負荷電圧100V 時のCpk は負荷電圧0V の場合よりも1.0 程度向上しており、振動の効果に差はない。はんだ特性とマスク表面コート、および基板設計を最適な条件で組み合わせて振動を与えた結果、アスペクト比2.7 のCpk は1.92 であった。
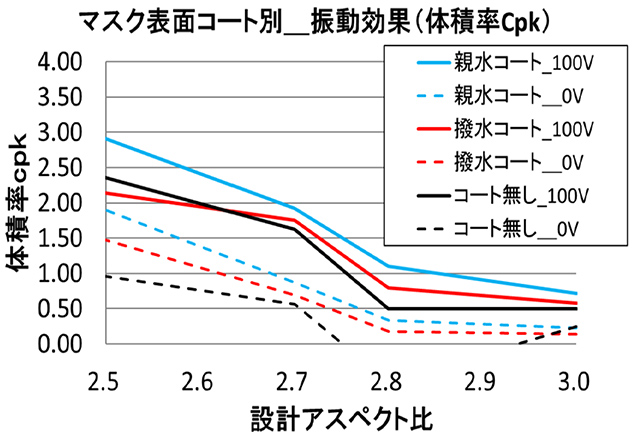
設計アスペクト比 | ||||||
---|---|---|---|---|---|---|
はんだ | マスク | 負荷電圧 | 3.0 | 2.8 | 2.7 | 2.5 |
A | 親水コート | 0V | 0.23 | 0.34 | 0.87 | 1.90 |
100V | 0.72 | 1.10 | 1.92 | 2.91 | ||
A | 撥水コート | 0V | 0.14 | 0.18 | 0.69 | 1.47 |
100V | 0.58 | 0.80 | 1.75 | 2.13 | ||
A | コートなし | 0V | 0.25 | 0.00 | 0.56 | 0.96 |
100V | 0.49 | 0.50 | 1.62 | 2.35 |
図8 マスク表面コート別 振動の効果
4.3 振動効果のまとめ
アスペクト比2.7 の印刷で必要となるはんだを基板パターンに接触させるための推進力を得るため、超音波振動によるはんだ流動性向上の効果を評価した。基板ステージや評価基板およびマスクは振動することで、印刷の面積率は増加し、高さは減少した。また、マスク開口のはんだ目詰まりは減少した。これらの結果から、振動を与えることではんだの流動性が増し、印刷性が向上する効果があると考える。
5. むすび
0402 から大型部品までの混載実装を実現するためには、大型部品の接合強度が低下しないアスペクト比で、0402の供給はんだ量を安定させて印刷することが求められる。
本取り組みでは、前回の2.4 を超えるアスペクト比2.7の体積率Cpk1.8 を目標に取り組んだ。高アスペクト比の印刷には、はんだと基板パターンを十分接触させ、両者の粘着する力を増やすことが重要だとわかった。そのため、はんだ特性やマスク表面コート、および基板パターン設計について、はんだがマスク開口に流れ込みやすい条件の選定が求められる。しかし、これらを最適な組み合わせで選定しても、アスペクト比2.7 のCpk は0.87 が限界であった。そこで振動エネルギーを付加して、はんだを基板パターンに接触させるための推進力を増加させることで、Cpk が1.92 まで向上した。このように振動印刷は、高アスペクト比の印刷に有効であると考える。
振動印刷の評価は基礎データの収集と印刷評価を開始したばかりであり、振動の繰り返し精度、基板面内の安定性、レジスト開口以外のパターンの効果、実装部品への影響をはじめ、多くの評価が今後必要な技術である。FA 機器における0402 と大型部品の混載基板の安定量産を行う上でも、更に評価を行い、実用化を目指していく。
参考文献
- 1)
- 山口浩二.0402 部品から大型部品までの混載実装を可能にする高アスペクト比はんだ印刷技術.OMRON TECHNICS. 2019,Vol.51, No.1, p.149-154.
- 2)
- Jisso 技術ロードマップ専門委員会.“第4 章電子部品”.JEITA2017 年度実装技術ロードマップ.一般社団法人 電子情報技術産業協会,2017,p.257.
- 3)
- 古賀裕一,八甫谷明彦,山本展大,Thin & Light PC の基板小型化技術.東芝レビュー.Vol.60, No.8, p.17-18.
- 4)
- ナミックス株式会社 飯田英世.スクリーン印刷方法及びその装置.特開2010-149301(P2010-149301A)
本文に掲載の商品の名称は、各社が商標としている場合があります。