Development of One-component Epoxy Resin with Short-time Curing and High Heat Resistance for Mechanical Devices
- One Part Epoxy Resin
- Thermal analysis
As an adhesive for bonding dissimilar materials used in mechanical devices, one-component epoxy resins are widely used from the viewpoint of high strength and ease of use. We have also used one-component epoxy resins for mechanical devices, such as relays and switches. In recent years, from the viewpoint of eliminating hazardous chemical substances, there has been a demand to improve the heat resistance of mechanical devices because of the increase in mounting temperature due to the spread of lead-free solder mounting. On the other hand, as environmental considerations increase, low energy consumption in the manufacturing process is required, and heat curing at low temperatures and in a short time is required. In this study, the composition of the one-component epoxy resin was adjusted on the basis of the reaction mechanism of the main agent and the curing agent, and heat resistance and low-temperature short-time curing were achieved. This paper reports on the technical contents.
1. Introduction
Relays, switches, and other electromechanical devices are indispensable control components used in diverse applications, including home appliances, vehicles, and communications equipment. Relays are classified into two types: open and airtight. Open-type relays are caseless or come in an unglued case. Airtight-type relays come in a sealed case glued to a base. These airtight-type relays are hermetically sealed with adhesive to prevent contact failures due to the ingress of impurities, such as solder flux from PCB mounting, extraneous substances from the surrounding environment, and corrosive gases. Besides airtightness, the adhesive is required to excel in such properties as application/curing productivity, adhesion to the substrate, and tracking resistance against tracking due to insulation surface discharge. Our company also uses one-component epoxy resin adhesives that meet these properties1-3).
A one-component epoxy resin generally comprises a liquid main agent, a solid curing agent, and an inorganic filler. The main and curing agents undergo a chemical reaction under heating to solidify from a liquid to a solid. This solidification enables the bonding between mold parts. We have improved these components and developed one-component epoxy resins to suit the required properties of electromechanical devices4-6).
Following the recent widespread use of surface mounting intended for the elimination of hazardous chemicals, increasingly higher processing temperatures are used in the mounting processes. A PCB only partially contacts the molten solder for several seconds in conventional mainstream through-hole mounting. In surface mounting, however, the whole PCB must be held at the solder melting temperature for 30 seconds or more in the so-called reflow heating process. Therefore, one-component epoxy resins used for surface-mount electronic parts must be highly heat-resistant for reflow processing. On the other hand, important challenges from the perspective of environmental load reduction include reducing the energy consumed during one-component epoxy resin curing, whereby one-component epoxy resins are required to have low-temperature fast curability.
Where the intent of imparting high heat resistance to a one-component epoxy resin is to ensure its heat resistance to reflow processing, the heat resistance of the resin itself must be improved. In other words, one possible approach is to improve the main or curing agent constituting the one-component epoxy resin. Conventional methods adopted for enhancement of heat resistance have been related to improving the main agents. More specifically, using the main agents richly containing aromatics with a phenol or naphthalene skeleton reportedly improves the heat resistance of the cured products1). However, these main agents are solid and must be melted before the curing reaction, increasing the curing temperature. Thus, heat resistance and low-temperature fast curability are both required properties, which, at the same time, are also mutually contradictory.
Proposals have been made to use existing methods to reconcile these mutually contradictory properties. However, these methods all involve not only significant changes in the resin or manufacturing process but also practical challenges. For example, two-component epoxy resins solidify just by mixing the main and curing agents at ordinary temperatures, offering low energy consumption advantages. Meanwhile, UV-curable resins solidify through an internal liquid-to-solid chemical reaction, also known as the photopolymerization reaction. A UV-curable resin comprises a main agent (liquid) and a photoinitiator as its components. Upon exposure to light energy from UV irradiation, the photoinitiator acts on the monomer (liquid) even at room temperature, causing a type of polymerization known as photo-radical polymerization, whereby the monomer molecules rapidly react and instantaneously turn into resin (solid). Thus, UV-curable resins have very fast-curing properties even at room temperature. Hence, their use can be advantageous because it leads to a short curing time and reduced energy consumption1). However, neither two-component epoxy nor photo-curable resins provide sufficient strength or heat resistance. As such, they presently have a limited range of application as adhesives for electromechanical devices. Moreover, photo-curable resins are only partially cured if any part is shaded and unirradiated with light. Hence, where unreachable by UV light, the resin remains uncured and may cause a problem, such as insufficient strength.
From the above, we considered it essential to take a new approach to improving one-component epoxy resins to reconcile the mutually contradictory properties of heat resistance and low-temperature fast curability. Based on the reaction mechanism between the main and curing agents, this study considered the components of the curing agents contained in a one-component epoxy resin and successfully reconciled its heat resistance and low-temperature fast curability. This paper reports on the content of this technology.
2. One-component epoxy resin compositions and evaluation method therefor
2.1 One-component epoxy resin sample preparation
A one-component epoxy resin comprises a main agent (resin component), a curing agent, a strength-enhancing, inorganic filler, and various additives. This study used only the main and curing agents in its compositional investigation to highlight the chemical reactions and their effects. We used a typical bis-phenol A-type epoxy resin (hereinafter referred to as the 窶彳poxy resin monomer窶) as the main agent. We used the following three types of curing agents: typical amine adduct, cyanamide, and imidazole curing agents for epoxy resins.
Amine adduct curing agents, also known as latent curing agents, exhibit cure-accelerating properties at relatively low temperatures. Cyanamide curing agents are known to induce secondary amine addition reactions and can impart heat resistance and adhesion to metals1). Amine adduct curing agents are well-known for curing epoxy resins at low temperatures.
Imidazole curing agents induce chain-transfer anionic polymerization reactions. As such, they undergo a three-dimensional polymeric reaction with epoxy resin monomers via catalysis, even when added in a small amount. Therefore, they are among the curing agents promising to impart heat resistance1).
Cyanamide curing agents are representative of curing agents for heat-curable resins7). They are one-liquid and have a long pot life. Cyanamide in epoxy resins are highly dense three-dimensionally and add excellent mechanical and chemical properties to cured products. As such, they are used as curing agents for adhesives for electronic parts. Curing with curing agents of this type supposedly does not start until a high temperature is reached.
Considering the aforementioned properties of the curing agents, we chose to evaluate the compositions of samples 1 to 3 for low-temperature curability, respectively. Samples 4 to 6 were prepared in compositions that blended an amine adduct curing agent supposedly superior in low-temperature curing performance with other curing agents.
We prepared the resin samples as follows: Based on the weight ratios shown in Table 1, the main and curing agents were weighed to a total weight of 3 kg in a plastic container. Then, the epoxy resin monomer liquid and the powders, including the curing agent, were mixed and homogeneously dispersed using a stirrer and a three-roll mill. A commercially available one-component epoxy resin for electromechanical devices was also evaluated to obtain data for a comparison.
Epoxy resin composition (pbw) | Sample | ||||||
---|---|---|---|---|---|---|---|
1 | 2 | 3 | 4 | 5 | 6 | ||
Main agent | Bis-phenol A-type Epoxy resin |
100 | 100 | 100 | 100 | 100 | 100 |
Curing agent | Amine adduct curing agent | 3 | 3 | 3 | 3 | ||
Cyanamide curing agent | 3 | 3 | 3 | ||||
Imidazole curing agent | 3 | 3 | 3 |
2.2 Evaluation methods
This subsection presents the methods we used to evaluate the one-component epoxy resin for low-temperature fast curing and heat resistance functions.
2.2.1 Low-temperature fast curability evaluation methods
We used a differential scanning calorimeter (DSC) and a Fourier transform infrared (FT-IR) spectroscope to analyze in detail the chemical reactions of the one-component epoxy resin.
(1) DSC
Generally, an epoxy resin monomer and a curing agent are heated to induce an exothermic reaction, resulting in a cured resin. A DSC detects this exothermic reaction by sensing variations in the heat flow due to the heat absorption/emission by the sample. Moreover, creative adjustments of the DSC temperature conditions allow the temperature dependence analysis of one-component epoxy resin窶冱 chemical reaction. For instance, keeping the oven temperature constant enables finding the reaction finish temperature under constant temperature conditions. In addition, with a temperature rise from room temperature to the high-temperature region, the reaction start temperature can also be detected. This study employed the following two profiles as the temperature conditions of thermal analysis:
- Constant temperature of 120ツーC
- Temperature rise from 50ツーC to 200ツーC
We set the low-temperature fast curing temperature at 120ツーC for the following reason. Fast curability generally increases at higher temperatures, albeit with a concurrently increased environmental load. Hence, with low-temperature curing being our priority consideration, we set the thermal curing temperature to 120ツーC, at which curing agents generally melt entirely. For low-temperature fast curability, we set such a target value that the resin samples would complete the curing reaction in a shorter time under the constant temperature condition of 120ツーC than the commercially available product.
(2) FT-IR
An FT-IR spectroscope irradiates a sample with infrared light and measures the amount of transmitted or reflected light. Infrared light is absorbed as the oscillatory or rotational motion energy of the molecular bonds. This absorption enables spectrally obtaining information on molecular structures or functional groups by FT-IR measurement, in other words, helpful information for substance identification. Moreover, this instrument can quantify specific molecules using spectral peak heights and areas because the amount of absorbed light is proportional to the concentration and thickness of substances.
Our FT-IR measurement detected the peak of the epoxy ring involved in the epoxy group reaction around 918 cm窶1 in the infrared region, enabling tracking the progress in the chemical reaction (curing reaction) through the change in the peak. More specifically, during the chemical reaction process undergone by the epoxy resin monomer under heating, the epoxy group ring-opened, allowing epoxy resin monomers to bond together. Hence, the peak of this epoxy ring decreased. This peak eventually disappeared when the chemical reaction proceeded further, indicating that the epoxy resin was fully solidified. Our FT-IR analysis was performed using the KBr transmission method to obtain infrared spectra from 500 to 2000 cm窶1.
2.2.2 Heat resistance evaluation methods
Considering that the one-component epoxy resin should be evaluated for heat resistance as the material and as applied to actual devices, we performed a dynamic viscoelasticity measurement (DMA) and a reflow heat resistance test.
(1) DMA
The DMA method evaluates the mechanical properties of samples by measuring the resultant stress or distortion from time-varying distortion or stress applied to the test pieces. This measurement can find the heat resistance of one-component epoxy resins based on the temperature dependence of the mechanical properties. In our specific case, we used DMA to measure the temperature and frequency dependences of the viscoelastic properties of the test pieces, in other words, storage elastic modulus (E窶イ), loss elastic modulus (E窶ウ), and loss tangent (tanδシ戲窶ウ/E窶イ). Because a resin can be evaluated for heat resistance based on the change in the storage elastic modulus (E窶イ), this study paid attention to the temperature dependence of E窶イ. The actual test used 3 mmテ5 mmテ1.5 cm film-like samples to measure the dynamic viscoelasticity during heating from 25ツーC to 250ツーC. We set such a target value for heat resistance that our resin would outperform the commercially available product. More specifically, the temperature at which the mechanical property E窶イ value decreased to or below 1.0テ108 MPa was defined as the strength loss threshold, thereby requiring that this temperature be higher than achievable by the commercially available product.
(2) Test method for reflow heat resistance
We used actual relays to evaluate the resin窶冱 heat resistance to reflow processing. Our actual reflow test evaluated the heat resistance of the one-component epoxy resin as applied to automotive-purpose relays, which are required to be resistant to reflow heat. The temperature conditions complied with JIS C 60068-2-58:2020. After the reflow test, the actual relays were soaked in a high-boiling fluorine inert liquid at 90ツーC and checked for airtightness by observing the occurrence/nonoccurrence of bubbles. This reflow test was repeated three times to evaluate the reflow heat resistance of the one-component epoxy resin. For reflow heat resistance, we set such a target value that the resin would pass the sealing test under the conditions specified in JIS C 60068-2-58:2020.
3. Evaluation results and discussions
3.1 Evaluation results and discussion on DSC analysis of low-temperature fast curability
To evaluate the curing time at 120ツーC, we measured the exothermic energy with the DSC temperature conditions set and maintained at 120ツーC for one hour (Fig. 1(a)). The DSC measurement apparatus has difficulty reaching the temperature of 120ツーC quickly. Hence, we set the apparatus to take approximately 7 minutes for a temperature rise from 25ツーC to 120ツーC (Fig. 1(b)). In Fig. 1(a), the x-axis represents the retention time at 120ツーC based on the temperature profile in Fig. 1(b), while the y-axis represents the exothermic calorific value. This figure is intended to read the one-component epoxy resins窶 reaction start and finish times through exothermic peak variations8).
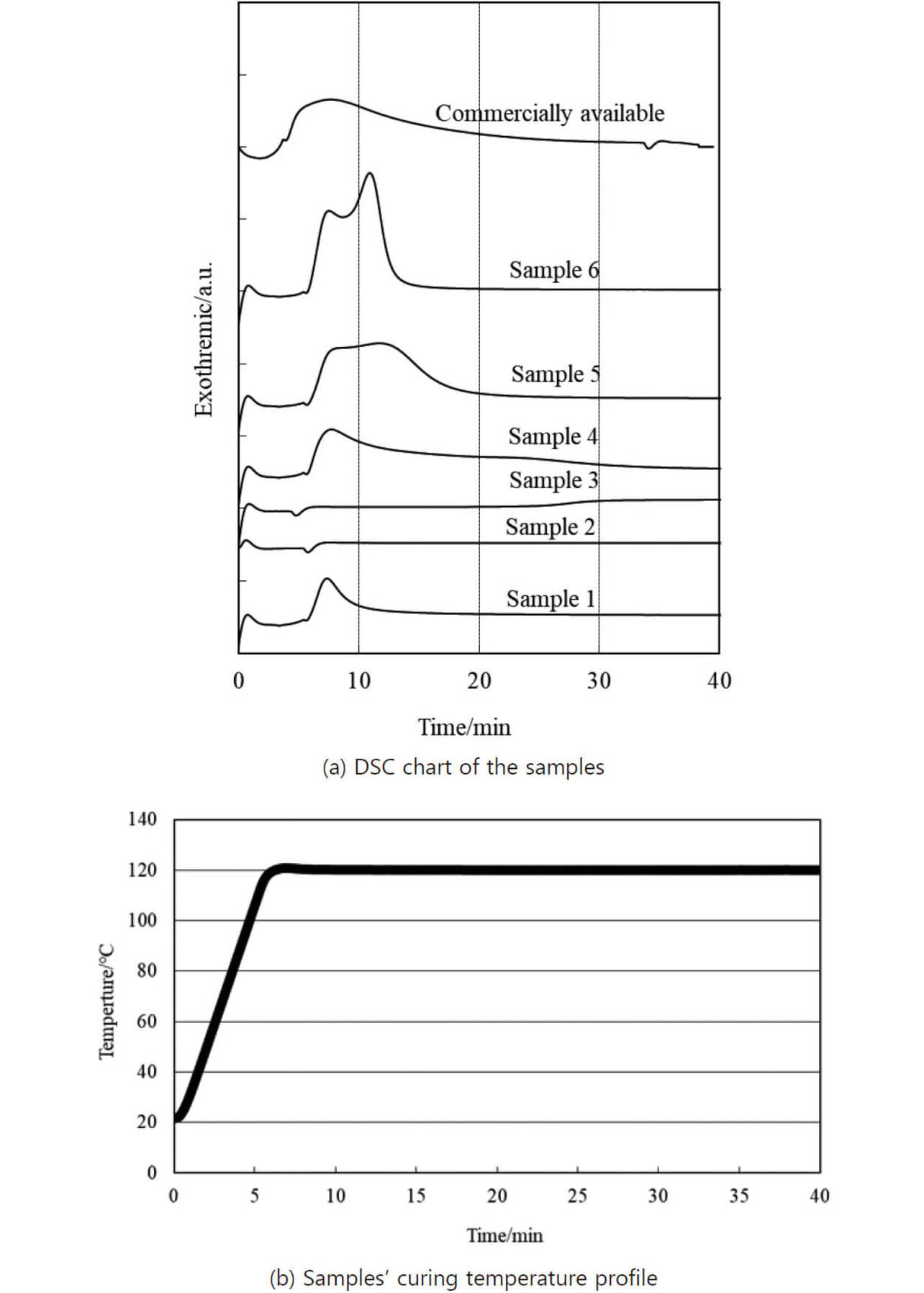
Sample 1 exhibited a steep leading edge of an exothermic peak around approximately 7 minutes. Then, the exothermic energy gradually decreased until approximately 15 minutes, suggesting that the chemical reaction ended at around 15 minutes. Meanwhile, samples 2 and 3 showed no exothermic peak at all, suggesting that if either one of these two curing agents were used separately from the other, the one-component epoxy resin would not react with either at 120ツーC.
Samples 4 and 5, containing two types of curing agents, showed the leading edge of an exothermic peak around approximately 7 minutes due to the curing reaction of the amine adduct curing agent. Samples 4 and 5 exhibited the disappearance of exothermic energy around 40 and 25 minutes, respectively, suggesting that adding the amine adduct curing agent accelerated the reactions with both imidazole and cyanamide curing agents. Sample 6, added with the three types of curing agents, also showed a steep leading edge of an exothermic peak around 7 minutes and the disappearance of exothermic energy around 15 minutes.
The above results show that samples 1 and 6 required the shortest curing time, followed in order by samples 5 and 4. The results of measuring a similar temperature profile of the commercially available one-component epoxy resin (Fig. 1: commercially available) show that the exothermic energy took approximately 40 minutes to attenuate. Therefore, we determined that the one-component epoxy resin samples 1, 5, and 6 outperformed the commercially available product in low-temperature fast curability.
Moreover, the one-component epoxy resin samples 1 to 6 were subjected to a temperature rise at 10ツーC/minute from 50ツーC to 250ツーC for a reaction start temperature analysis to identify the reactive factors of the curing agents (Fig. 2).
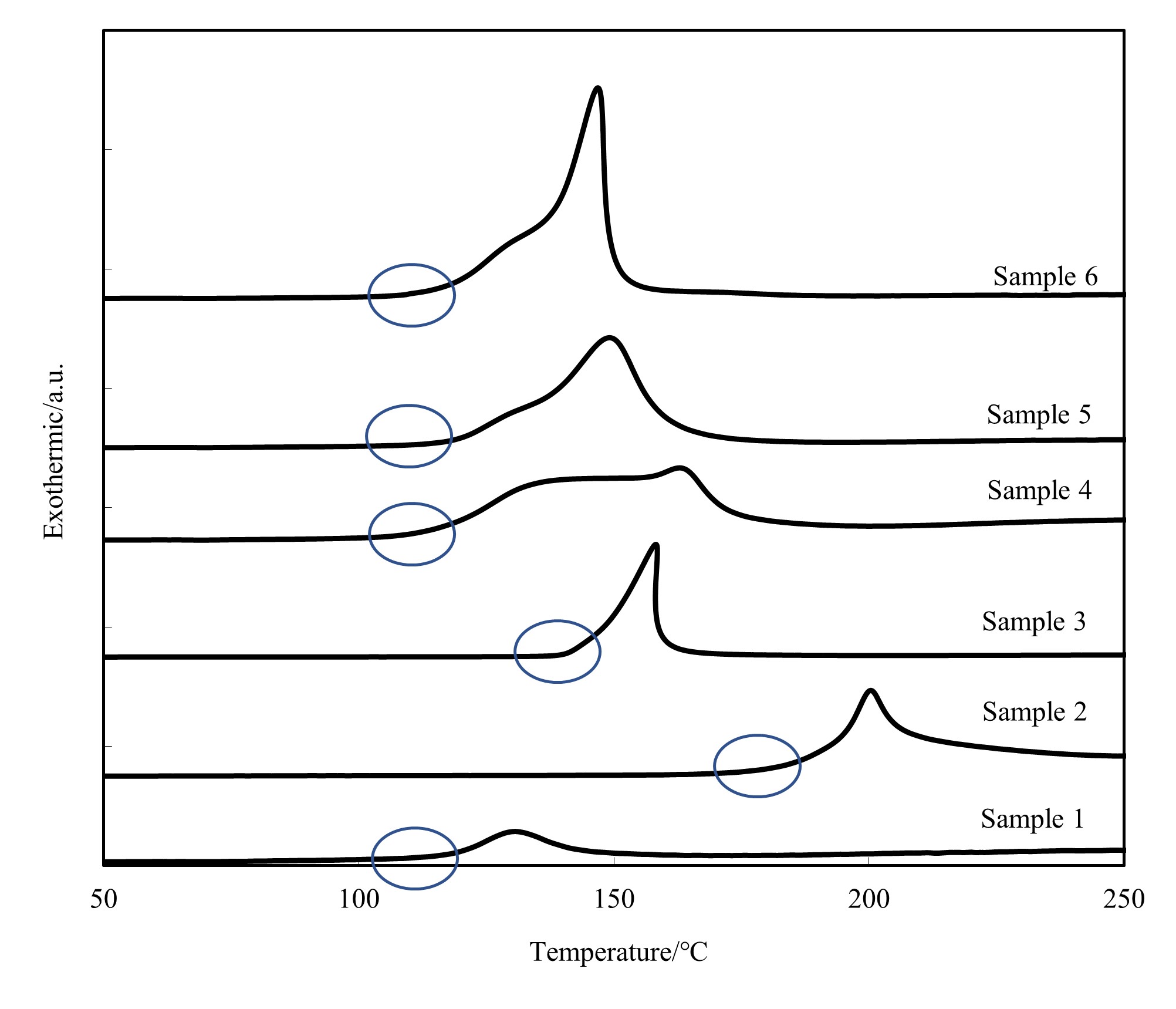
In Fig. 2, the x- and y-axes represent temperature and exothermic energy, respectively. The DSC measurement results for samples 1 to 3 show the leading edge of the exothermic peak at 100ツーC, 180ツーC, and 140ツーC, respectively. Samples 2 and 3 showed no exothermic peak at and below 120ツーC, suggesting that the samples窶 curing reactions did not progress under the temperature of 120ツーC. These results agree with the results that no exothermic peak was observed under the constant temperature condition of 120ツーC, as shown in Fig. 1(a).
As well as sample 1, samples 4 to 6 exhibited the leading edge of an exothermic peak from around 100ツーC to 110ツーC. They shared in common that they contained an amine adduct curing agent, confirming that using this curing agent decreased the reaction start temperature. Although exothermic energy was observed with sample 1, its small exothermic peak area and gel-like cured product suggest that its epoxy resin did not fully undergo the chemical reaction. To confirm this point, we performed FT-IR measurements to examine the samples for the degree of curing. Samples 2 and 3, insufficiently cured at 120ツーC, are excluded from the considerations below.
3.2 Evaluation results and discussion on FT-IR analysis of low-temperature fast curability
Figs. 3(a) to (d) show the FT-IR charts for samples 1 and 4 to 6 as heated at 120ツーC for one hour. The numerical values along each chart窶冱 inner left edge indicate the heating time.
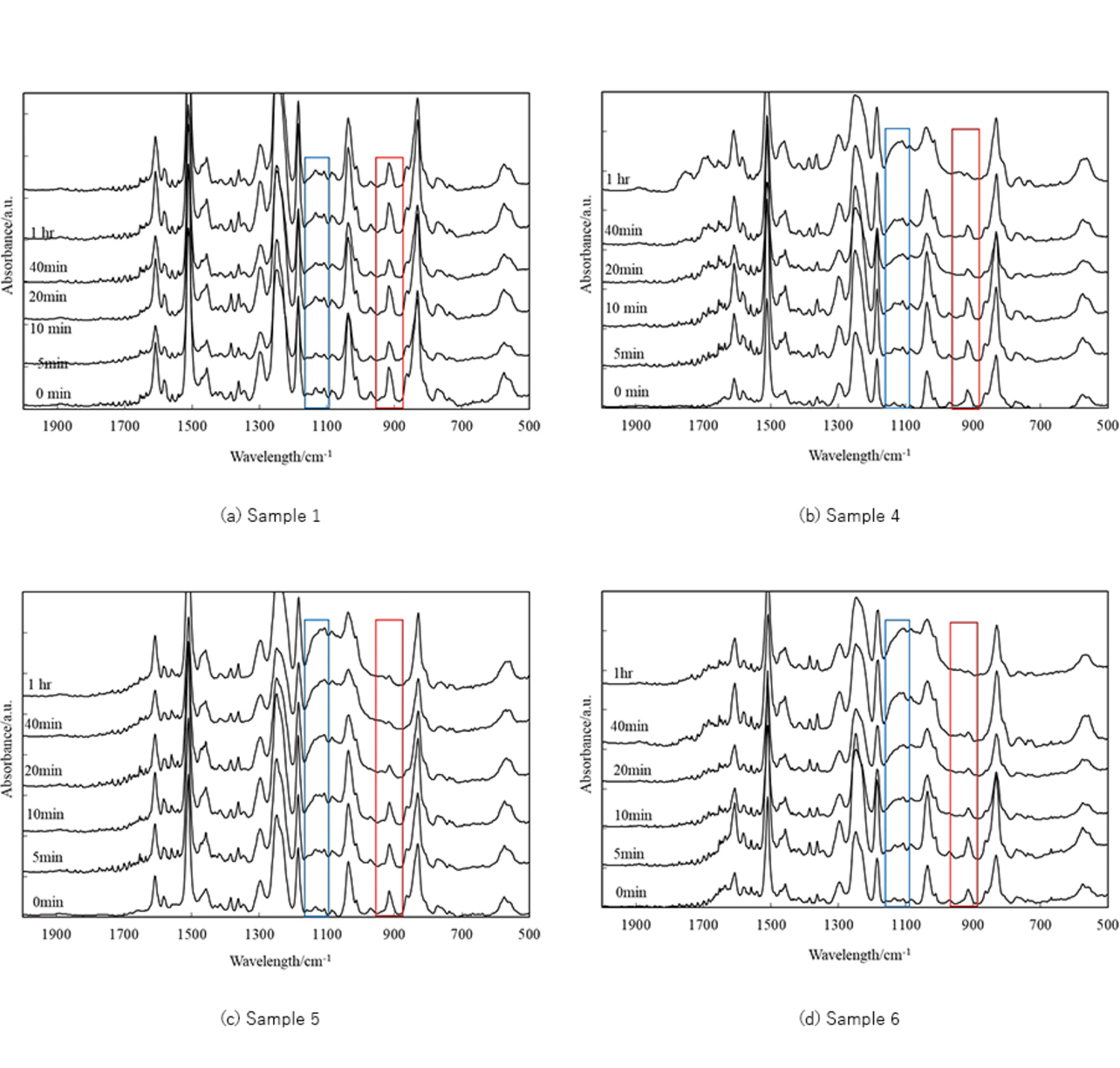
Fig. 3(a) shows the FT-IR chart for sample 1, which contained the amine adduct curing agent as its only curing agent. For sample 1, the peak at 918 cm窶1 remained high even after 40 minutes, confirming the existence of uncured epoxy resin. Then, it follows that the amine adduct curing agent alone only induced local reactions, resulting in insufficient curing.
Then, Figs. 3(b) and (c) show the FT-IR charts for samples 4 and 5, which contained the amine adduct curing agent and the cyanamide or imidazole curing agent. Similarly to sample 1, samples 4 and 5 showed decreases in the peak at 918 cm窶1, indicative of the ring-open reaction of epoxy groups, and increases in the peak around 1190 cm窶1 due to the ether groups, suggesting that progress occurred in the chemical reactions.
Moreover, samples 4 and 5 exhibited a significant decrease in the peak due to the epoxy ring 20 minutes after heating. In addition, sample 6 (Fig. 3(d)), containing the three types of curing agents, also showed decreases in the peak at 918 cm窶1, similarly suggesting that progress occurred in the chemical reactions.
3.3 Evaluation results and discussion on heat resistance
Then, we performed a DMA measurement to evaluate the heat resistance of the one-component epoxy resin (Fig. 4).
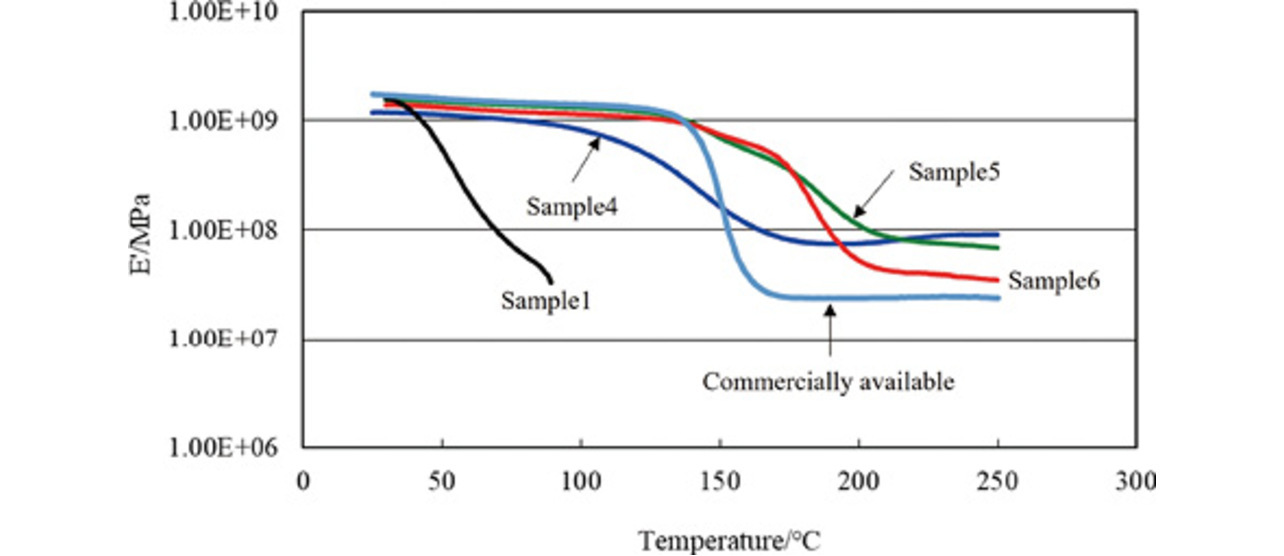
Fig. 4 shows the temperature dependence data of the storage elastic modulus (E窶イ) indicative of mechanical properties. We defined the temperature at which the mechanical property E窶イ value decreased to or below 1.0テ108 MPa as the strength loss threshold. For sample 1, the E窶イ value decreased around room temperature to or below 1.0テ108 MPa around 70ツーC. Meanwhile, for samples 4 to 6, the E窶イ value decreased to or below 1.0テ108 MPa around 150ツーC, 200ツーC, and 190ツーC, respectively.
The difference in heat resistance between samples 4 and 5 was probably due to the characteristics of their respective curing agents. The imidazole curing agent was a chain-transfer curing agent, enhancing the main agent窶冱 polymerization degree. This advantage probably enabled the one-component epoxy resin to achieve high-density cross-linking, improving its heat resistance. On the other hand, the cyanamide curing agent failed to achieve a similar heat resistance improvement effect, probably because it was not a chain-transfer curing agent.
3.4 Relationship between low-temperature fast curability and heat resistance
Table 2 summarizes the above relationship between low-temperature fast curability and heat resistance. Table 2 determines that sample 6, mixed in with the three types of curing agent, was the most desirable as a one-component epoxy resin capable of reconciling these two properties. In addition, sample 6 showed superior properties compared with the commercially available product.
Required performance | Sample 1 |
Sample 2 |
Sample 3 |
Sample 4 |
Sample 5 |
Sample 6 |
Commercially available product |
---|---|---|---|---|---|---|---|
Low-temperature fast curability | テ | テ | テ | 笨 | 笨 | 笨+ | 笨 |
Heat resistance | テ | 窶 | 窶 | テ | 笨 | 笨 | テ |
3.5 Reflow heat resistance test
Using sample 6, which reconciled low-temperature fast curability and heat resistance, we performed a reflow heat resistance test on relays. Before the test, this one-component epoxy resin was applied and cured on each relay窶冱 base surface. The results of repeating this test three times confirmed that the relays remained sealed airtight, showing no visible bubble leak. Thus, the actual device evaluation results also demonstrated that the one-component epoxy resin used maintained high heat resistance. In contrast, the commercially available product did not meet the target value of the same sealing test.
4. Conclusions
Reconciling the heat resistance improvement and low-temperature fast curability of dissimilar material-bonding adhesives has been one of the challenges in addressing social needs, such as hazardous chemicals窶 elimination and environmental considerations. This study dealt with a one-component epoxy resin used as a dissimilar material-bonding adhesive for electromechanical devices and adjusted its recipe to solve the challenge. Our method went as follows: accelerate the chemical reaction around 120ツーC by the catalysis of an amine adduct curing agent and use a cyanamide and an imidazole curing agent in combination to achieve complete resin curing at 120ツーC within 20 minutes. Moreover, we improved the resin窶冱 heat resistance to around 190ツーC, exploiting the chain-transfer catalysis of the imidazole curing agent. Based on the curing agents窶 characteristics, we developed a one-component epoxy resin capable of reconciling heat resistance and low-temperature fast curability. Moreover, we demonstrated the resin窶冱 heat resistance retention by performing a reflow test to check actual relays窶 sealing for airtightness.
Based on the above, we showed that one-component epoxy resin designs based on the principles of chemical reactions contribute to developing products with excellent properties. Our company applies one-component epoxy resins developed by similar approaches to its products.
We consider that UV-curable resins and two-component epoxy resins mentioned in Section 1 and other alternatives to heat-curable resins should be developed to pursue further environmental load reduction. This objective requires improving the molecular structures of main and curing agents, among other aspects, posing a challenge for the future.
References
- 1シ
- H. Kakiuchi, Epoxy Resins, vol. 1 to 4, (in Japanese), Jpn. Soc. Epoxy Resin Technol., 2003.
- 2シ
- R. Kuwabara et al., 窶廛evelopment of SMD Adhesive with Stable Dispensing during Longtime,窶 (in Japanese), Matsushita Tech. J., vol. 54, no. 1, pp. 19-23, 2008.
- 3シ
- T. Fukuhara, 窶廣dhesive Technology of Electronics Devices,窶 (in Japanese), IEICE Tech. Rep., 2009, OPE2009-104.
- 4シ
- T. Fukuhara, 窶弋he Sealing Reliability of Electronics Mechanical Devices,窶 (in Japanese), IEICE Tech. Rep., 2009, R2009-34.
- 5シ
- M. Morii, 窶弋he Evaluation Is Researched the Joint Strength of the Adhesive,窶 (in Japanese), IEICE Tech. Rep., 2007, R2006-47.
- 6シ
- Y. Tatsuno et al., 窶弋he Improvement of the Sealing Reliability of Relays Which Uses Polycarbonate for the Case,窶 (in Japanese), IEICE Tech. Rep., 2012, R2011-42.
- 7シ
- M. D. Gilbert et al., 窶廴echanism of the Dicyandiamide/Epoxide Reaction,窶 Macromolecules, vol. 24, no. 2, pp. 360-369, 1991.
- 8シ
- H. Kanbe and T. Ozawa, Thermal Analysis, (in Japanese), Kodansha Ltd., 1992.
The names of products in the text may be trademarks of each company.