【Expository Articles】 Significance of Mass Balance Approach in the Dissemination of Biomass Plastics
- biomass plastics
- mass balance approach
- carbon neutral
- circular economy
- The Paris Agreement
In recent years, toward the realization of a carbon-neutral society, which is the Japanese government’s goal of achieving a carbon-neutral society by 2050, a movement to promote the spread of biomass plastics is becoming active. When switching from existing petroleum-derived plastics to biomass plastics, seamless switching in material properties and lead time is an issue, especially in the industrial world. In this paper, we describe the significance of the mass balance approach, which is being applied as the most realistic method among the multiple switching methods. In addition, concerns in the adoption of the mass balance approach will be examined from the viewpoint of materials technology.
1. Introduction
1.1 Overview of carbon neutrality
In recent years, attention has been gathering toward carbon neutrality measures intended to achieve substantially zero emissions, taking aim at the massive amounts of anthropogenic atmospheric carbon dioxide emissions from among greenhouse effect gases (GHGs) pointed out to be a factor responsible for climate change.
This concept is touted in the Paris Agreement1) adopted in 2015 as a long-term objective commonly shared worldwide. This Agreement provides for keeping the global average atmospheric temperature rise to well below 2°C relative to the preindustrial revolution level and pursuing efforts to suppress the rise within 1.5°C (2°C target). Following suit, the Japanese government presented long-term strategies2) aimed at achieving this objective by 2050.
Zero emissions are hard to achieve by simply reducing carbon dioxide emissions alone. By contrast, carbon neutrality is the concept of offsetting the residual portion through carbon dioxide absorption and fixation to achieve substantially zero emissions.
1.2 Carbon neutrality targets set by OMRON
In July 2018, OMRON specifically established “OMRON Carbon Zero” as its goal to realize a carbon-neutral society. The original policy was aimed to achieve Scope 1 and 2 zero GHG emissions (regarding the direct and indirect GHG emissions in our areas of activities) by 2050 according to the 2°C scenario. This goal was revised in March 2022 to a more ambitious one based on the 1.5°C scenario. This revision specifies a new goal of achieving an 18 percent emissions reduction by 2030 (relative to FY2016 based on the 2°C scenario) for Scope 3 (GHG emissions from our value chain)3). In this way, OMRON is promoting ambitious efforts toward realizing a carbon-neutral society.
1.3 Biomass plastics introduction targets set by the government
The government has presented policies for various sectors to promote carbon neutrality in Japan. For industrial materials, items related to plastic raw materials are included in the 14 focus areas of the Green Growth Strategies presented by the Ministry of Economy, Trade and Industry. One of these items targets the introduction of 2 million tons of biomass plastics annually and presents a roadmap toward its achievement. Currently, biomass plastics are being introduced primarily to consumer products. However, their usage remains low in industrial applications, leaving it to be desired that they be more widely adopted. Their high prices pose the most significant barrier to their adoption for industrial applications. For example, bio-polyethylene is priced three times higher than its petroleum-derived counterpart4). Besides, risks to performance may also be involved, such as switching over to new materials. Especially In the control equipment business, materials are often required to have high flame-retardant characteristics. Therefore, biomass plastics rarely stand a chance of joining a list of candidate materials to be considered. The current trend is to promote carbon neutrality through energy efficiency enhancement. On the other hand, OMRON has determined that it needs to contribute through materials and, since the early days, has been working on acquiring technologies related to the introduction of biomass plastics in the control equipment business.
2. Overview of biomass plastics
2.1 Definition of biomass plastics
Fig. 1 shows biomass plastics and their peripheral materials known as of now. Biomass plastics are defined as plastics manufactured using plants and other renewable organic resources (biomasses) as raw materials. Some plastics are called biodegradable plastics if they degrade into carbon dioxide or water via the action of microorganisms or the like in the environment. All these are collectively referred to as bioplastics. Then, it does not follow that all biomass plastics are biodegradable or that all biodegradable plastics are manufactured using biomass as the raw material as demonstrated by such examples as non-biodegradable biomass plastics (e.g., bio-polyethylene) or petroleum-derived biodegradable plastics (e.g., polybutylene succinate). Bioplastics may be further diversified, which may lead to reorganizing their designations in the future.
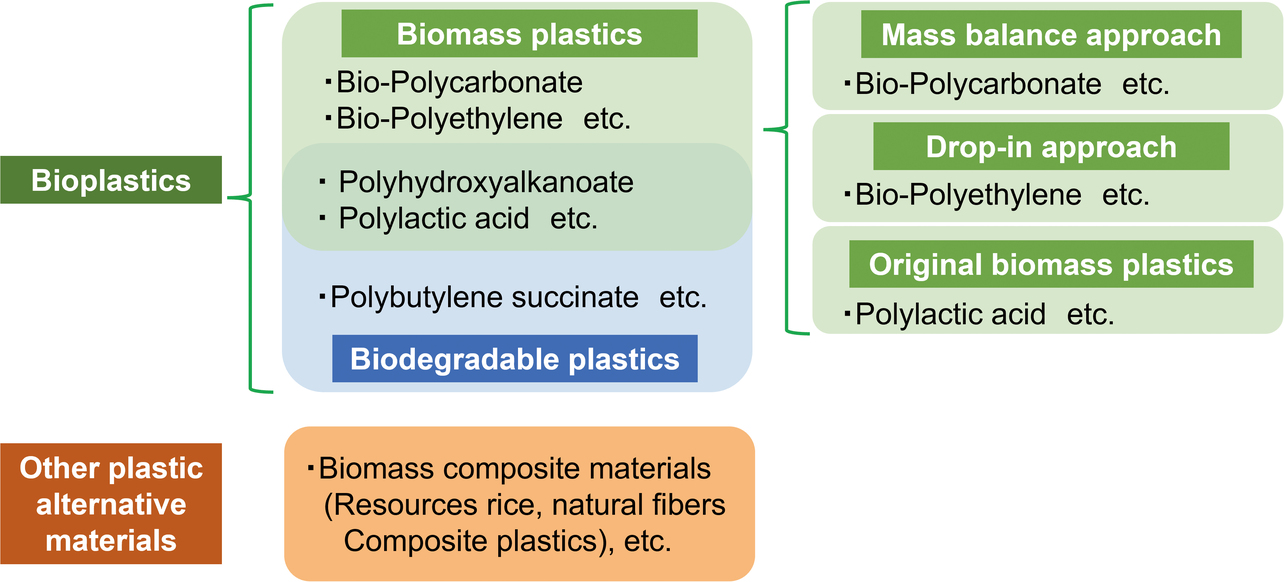
Biomass plastics are classified by their manufacturing methods, such as the mass balance approach used to manufacture new and existing materials of the same chemical structure in parallel in an existing plant and the drop-in approach (segregation approach) used to manufacture them separately in their respective dedicated plants. Moreover, some biomass plastics are custom-tailored to pursue functions unique to biomass-derived ones and can only be manufactured from specific biomass raw materials. The above classification is based on the characteristics of individual plastics, such as manufacturing methods or raw materials, and reflects the added values that were desired in different times.
Recently, composite materials have emerged one after another as combinations of biomass resources, such as resource rice, with existing plastics. In some cases, these composite materials are included in the kinds of bioplastics or biomass plastics. However, this paper excludes them because they are manufactured using no biomass raw materials as raw materials for polymers, the primary constituents of plastics.
2.2 Advantage of biomass plastics
Conventional plastics are manufactured using petroleum and other fossil resources as coarse raw materials. Petroleum is a fossil resource produced when the dead bodies of organisms that lived in time immemorial were turned into hydrocarbons by underground heat and pressure. Mankind mines and uses this resource as the raw material for plastics. When disposed of after use, plastics are generally incinerated and discharged as carbon dioxide. Hence, from the whole life cycle perspective, carbon fixed underground as a fossil resource is released as carbon dioxide into the environment, causing increases in atmospheric carbon dioxide concentrations. On the other hand, for biomass plastics, although similar in post-use behavior, plants used as their raw materials absorb atmospheric carbon dioxide for their growth, enabling a carbon cycle above the ground and allowing their exclusion from the considerations of factors responsible for increases in atmospheric carbon dioxide concentration5). Fig. 2 compares these petroleum-derived plastics and biomass plastics. Thanks to this advantage, biomass plastics can be regarded as materials that contribute to carbon neutrality.
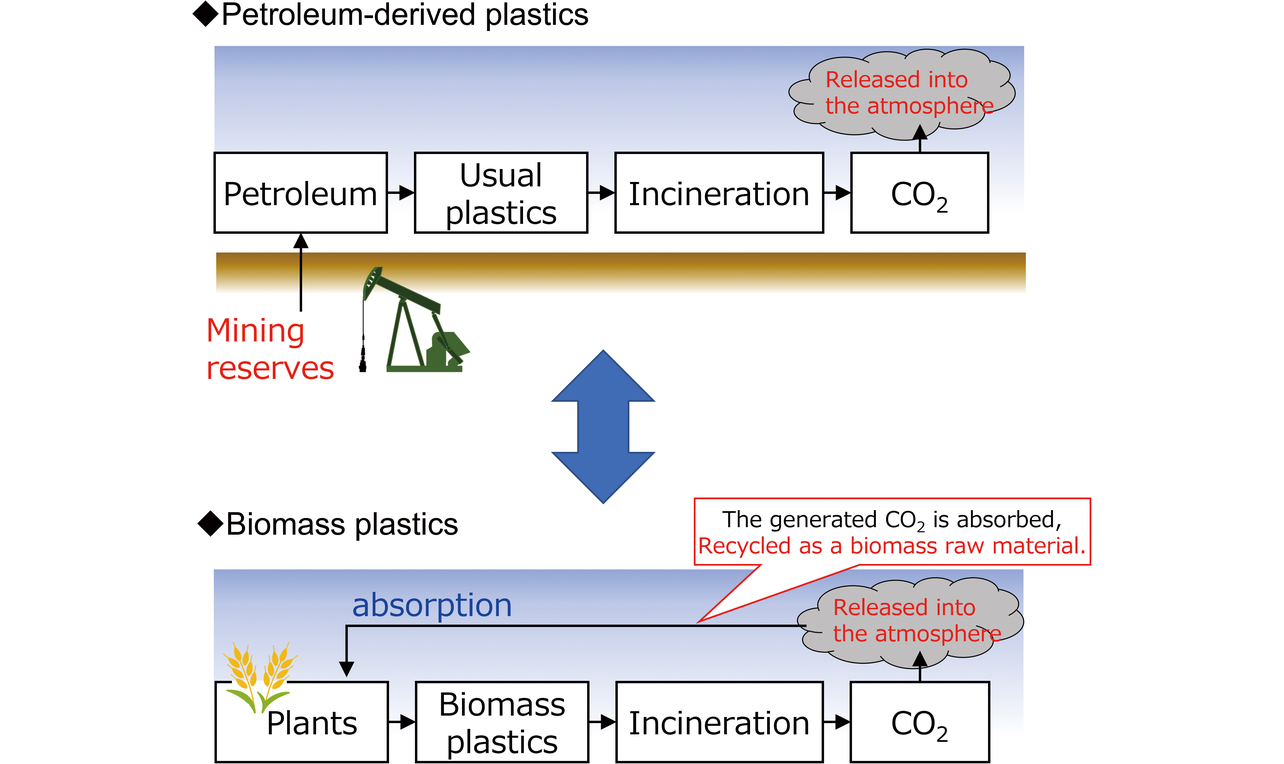
2.3 History of biomass plastics
In the early stages of developing biomass plastics, priority was given to creating new chemical materials utterly different from existing raw materials. Polylactic acid is a representative example of such materials. These materials were attempts to utilize unique chemical structures derivable from biomass raw materials but only had a limited market size because of their low usability and other factors. In recent years, however, moves toward market expansion have been observed as responses to the advances in handling technologies and the social demand for carbon neutrality.
Then, in response to the mounting concerns about the depletion of petroleum resources, solutions were explored to replace the raw material for polyethylene, an existing plastic, with biomass-derived one. In 2010, Braskem S.A. started commercial production of sugarcane-derived bio-polyethylene using the drop-in approach ahead of the rest of the world. This bio-polyethylene is still produced today and supplied only by Braskem S.A. Bio-polyethylene fared poorly in market expansion in the early stage because of its high price tag, although chemically structured the same as the existing polyethylene. However, it has been revalued because of recent expectations for its contribution to carbon neutrality, thereby experiencing increased demand.
Recently, attention has been gathering toward biomass plastics from such perspectives as spreading the SDGs across society or setting specific targets for realizing a carbon-neutral society. In Japan, Mitsui Chemicals has started manufacturing basic chemicals from biomass naphtha supplied by Finland’s Neste Corporation, the top supplier, and providing them to plastics manufacturers. Then followed the emergence of various biomass plastics6). In these cases, the mass balance approach was adopted, which triggered the rapid progress in the deployment of biomass plastics manufactured under the mass balance approach from 2021 onwards7).
3. Overview of mass balance approach-based biomass plastics
3.1 Concept of the mass balance approach
The present and subsequent subsections detail the mass balance approach, which, as mentioned above, is rapidly progressing. The mass balance approach is a method that assigns the characteristics of a specific raw material from among the introduced raw materials to some of the produced products proportionally to the input amount of that raw material. For example, when a conventional raw material and a new raw material with high environmental value are mixed and used in a seven-to-three ratio, 30 percent of the products are assigned with the characteristic of having been manufactured from the new raw material with high environmental value and the remaining 70 percent of the products are regarded as manufactured from the conventional raw material. This approach is applied in many industries, including palm oil refining or papermaking.
Fig. 3 shows a flow of biomass plastics manufacturing under the mass balance approach. This flow relates to naphtha as the coarse raw material for plastic materials. The naphtha derived from petroleum and biomass sources is mixed and loaded into a naphtha cracker to manufacture basic chemicals, including ethylene and propylene, from which plastics are manufactured. These products uniformly contain the respective raw material sources. As such, they are indistinguishable by raw material source. However, under the mass balance approach, the input amount of raw material with a particular characteristic (here, “being derived primarily from biomass”) is referenced to assign that characteristic to some of the produced products. Precise assignment requires a certification system that ensures traceability for the entire supply chain from coarse raw materials, raw materials, resins, and plastic products to the final products manufactured using them.
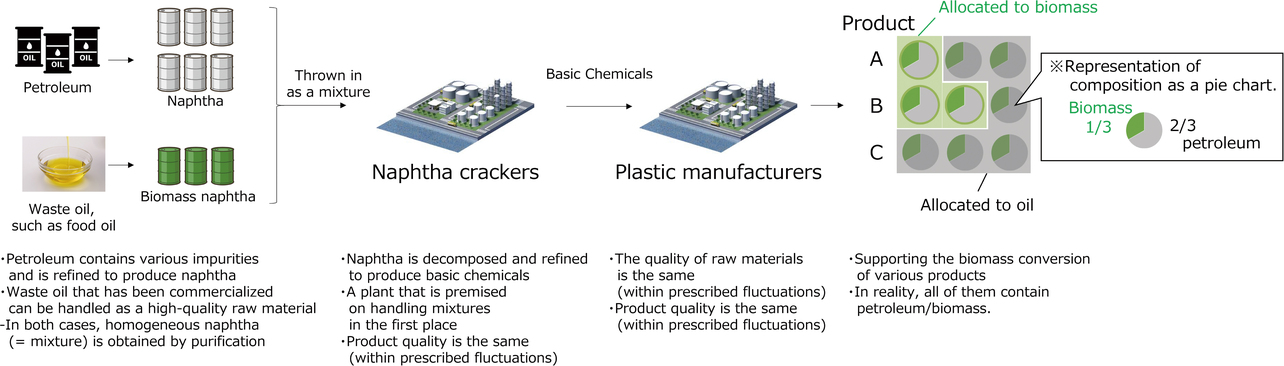
3.2 Advantages of the mass balance approach
3.2.1 Creation of products with 100 percent biomass content
The mass balance approach is adopted to allow the deployment of products as such with 100 percent biomass content, regardless of their actual biomass contents. As a result, it becomes possible to provide materials tailored to customer requirements as 100 percent biomass plastics, promoting the social penetration of biomass plastics.
The most significant advantage of adopting the mass balance approach is the ability to deploy the various plastic products. Conventional biomass plastics have been limited to the abovementioned polylactic acid and bio-polyethylene, plastics that can actually be manufactured from biomass-derived raw materials using the drop-in approach. Let us say that we are newly introducing the mass balance approach here. Then, previously technically unfeasible plastics can be assigned as biomass plastics. This solution does not directly overcome the technical challenge. However, it serves as a method of handling the deemed biomass plastics and can encourage the shift from various plastics to biomass. In addition, this method can provide opportunities for the user side to promote environmental values and for the supplier side to boost the sales volume. If adopted and introduced, the mass balance approach would promote the carbon neutralization of the whole society and would be highly worthwhile, society-wise.
3.2.2 Easy quality variation control
Under the mass balance approach, biomass plastics manufacturing uses naphtha manufactured from raw materials once refined, such as food oil. Contrary to petroleum, which has relatively large variations in quality, depending on the place of origin or the lot, food oils can be understood as a source with stable quality and, as such, are advantageous for production control.
Naphtha manufactured from biomass sources is a byproduct of sustainable aviation fuels (SAFs) manufactured under strict quality control and offers guaranteed stability in both quality and procurement against the background of the future prospective increase in SAF supply and demand. Moreover, the naphtha is loaded into a naphtha cracker to undergo chemical breakdown and then cyclic distillation until separated into basic chemicals, such as ethylene or propylene. As mentioned above, bio-naphtha to be loaded is manufactured from raw materials of relatively stable quality and hence also has the advantage of fluctuation control in the naphtha cracker plant. For quality control, the closest attention is paid to abrupt deviations in process control values when bio-naphtha is loaded into an existing plant premised on loading petroleum-derived naphtha. In the petrochemical industry, biomass sources still remain very limited and do not seem sufficient to replace the full capacity matching the current plant size immediately. Amid such circumstances, the mass balance approach will allow the manufacturer to adjust the input amount or ratio at their discretion, facilitating the introduction of biomass sources.
3.2.3 Less expensive capital investments
The mass balance approach assumes as the premise for its application that a homogeneous raw material source will be loaded. This premise makes it possible to mix a biomass-derived raw material in an existing plant operated on the premise of a petroleum-derived raw material.
The resulting advantage is, first and foremost, that new capital investment can be minimized by using an existing facility as is. Besides, no additional large equipment needs to be installed. Hence, the required construction and start-up periods will be shorter than otherwise, reducing the time lag from the introduction decision until the actual operation. Then, one of the advantages after introduction is the versatility with optional mixing of other raw material sources, eliminating the need to install a dedicated facility for each raw material source. Biomass sources will be diversified in the future, enabling flexible adaptation to situational changes.
To help consider the superiority of the mass balance approach, Fig. 4 shows the conditions of biomass plastics manufacturing not using it. In this case, an existing fossil-based plastic manufacturing plant operates in parallel with a newly installed biomass plastic manufacturing plant, giving rise to various issues in their respective manufacturing lines. The existing plant currently has a production scale sufficient for the total demand in society. If conventional plastics lose demand to emerging biomass plastics and are eventually all replaced with them, the existing plant will be shut down. Thus, the existing facility will suffer increased costs because of capacity utilization shrinkage and idling. Meanwhile, the biomass plastic manufacturing plant will need new capital investment as a dedicated facility and become an excessive cost component from the initial supply phase. There will also be a lead time to the start-up, which is often required to be a period on the order of years. Hence, the plant will fail to prepare to provide biomass plastics responsively to social situations.
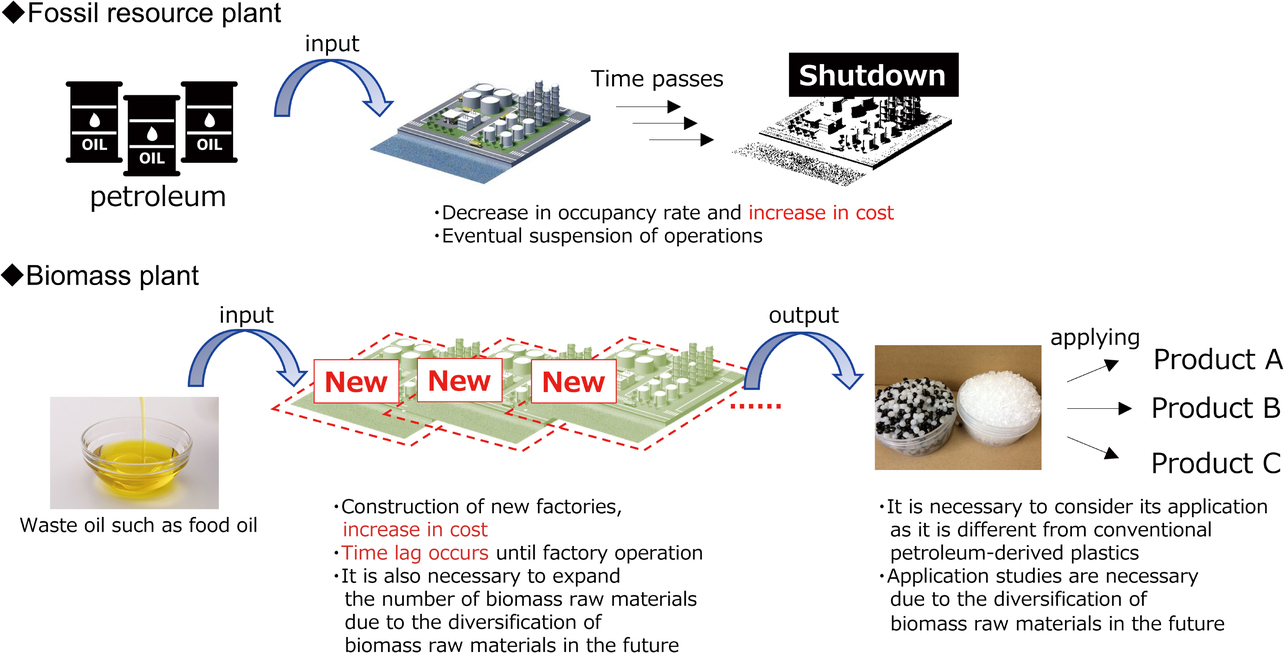
Moreover, when a new raw material source emerges, an additional dedicated facility must be installed accordingly. Even after this expansion, each facility must be operated independently according to the volume of supply or demand of the raw material sources. The user side must handle products manufactured in the respective manufacturing lines as different types, which leads to excessive increases in peripheral tasks, such as product testing or production control. As a result, biomass plastics will be seriously prevented from penetrating society. Given that the difficulties seen above co-occur on the two plants, it is not a practical measure at all to operate them in parallel. The mass balance approach can provide a highly effective solution to this challenge.
3.2.4 Easy production adjustment in response to social situations
The fourth advantage of the mass balance approach is that it allows optional adjustment of the input ratio of biomass-derived components according to society’s needs for biomass plastics. Currently, biomass plastics account for only a tiny portion of the total plastic volume produced. However, this approach will be able to optionally adjust the input ratio of biomass-derived components when demand expands in the future and, hence, will allow flexible responses to suit the situations. Events that can be expected when there is no determining how situations will change in the future include increased input ratios of biomass-derived components, diversified raw material sources, and multi-route introduction of raw materials. When the full capacity of the production line concerned is replaced with biomass plastics after a while, followed by the eventual adoption of the drop-in approach, all will be handled on the extension of the existing facility. Therefore, the mass balance approach is highly practical as a transitional measure.
3.3 Approach to risks in the mass balance approach
3.3.1 Impurity risk
When the mass balance approach is adopted, a production facility designed for use with a conventional petroleum-derived raw material is loaded with a mixture of differently sourced raw materials. Hence, a product quality-related risk will occur, which means that the product quality is affected when a difference originating from the biomass source becomes apparent outside the expectations of the quality standards designed for the petroleum-derived source. One of the specific examples that may apply is the presence of unexpected impurities. However, a naphtha cracking process chemically breaks down and fractionates naphtha, a mixture, into various components in the first place. Given this point, it follows that as long as the facility is operated and controlled to remain within process control limits, inclusions of impurities are prevented, in principle, producing homogeneous outputs.
3.3.2 Process variation risk
One of the risks inherent in process control per se is the process variation that results from mixing and loading a new biomass naphtha into an existing plant. The usual practice for this type of process is to set the process control values for manufacturing without limiting them to the quality parameter values for the output product and to control them within predetermined ranges to ensure stable production of a homogeneous product. However, if any process control value abruptly deviates from the mixing of the different raw materials, the process will become hard to control, resulting in a risk that falls outside the control value. Although the lot-to-lot quality variations of the naphtha to be loaded must be controlled similarly, raw materials used in the mass balance approach, such as bio-naphtha manufactured from food oils, are manufactured from coarse raw material artificially refined once and, therefore, are probably more advantageous in process control than petroleum-derived naphtha. Fig. 5 shows as an example the behavior of a quality-related process control parameter when a biomass-derived raw material was loaded into a facility operating as a continuous process based on a petroleum-derived raw material.
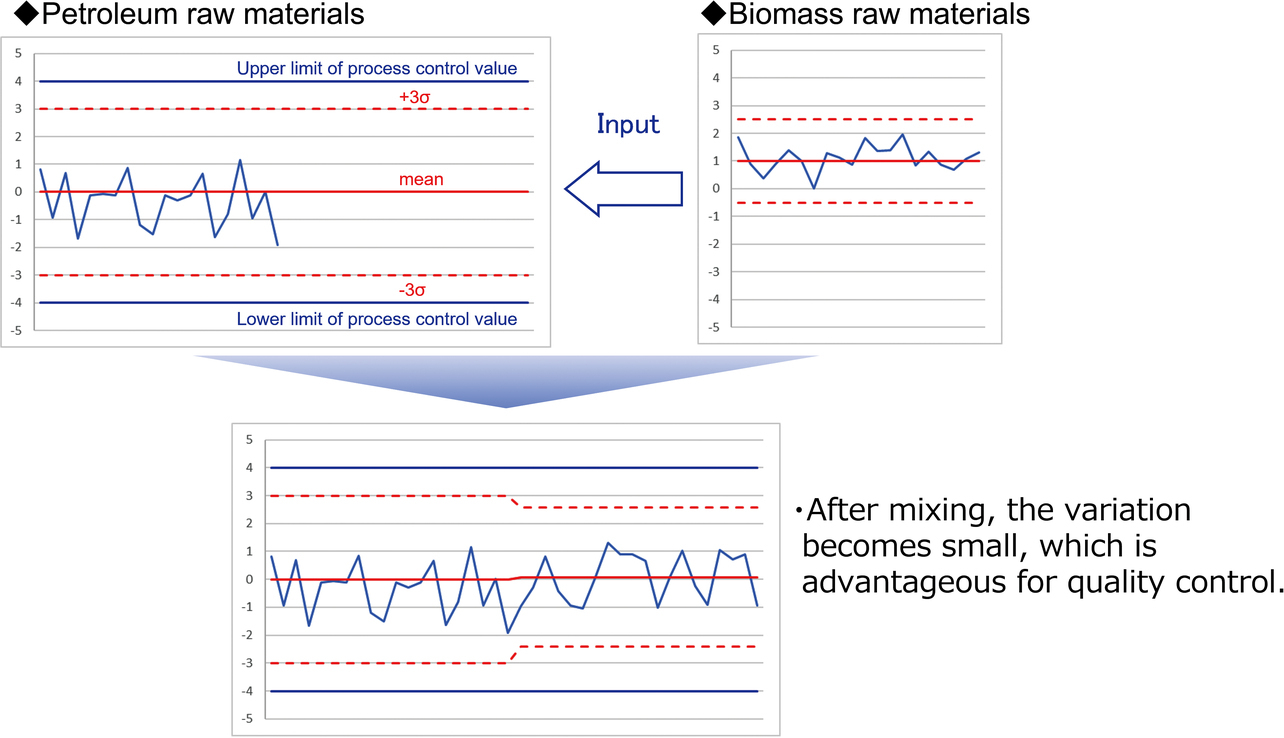
Before loading, naphtha is usually mixed and smoothed in the raw material tank and controlled to avoid abrupt fluctuations. Basic chemicals manufactured through such a process can be considered practically homogeneous regardless of the raw material source. Moreover, biomass plastics manufactured using them as raw materials can also be handled within standard quality control.
3.3.3 Handling of products assigned as petroleum-derived plastics under the mass balance approach
Products assigned as petroleum-derived plastics under the mass balance approach also contain biomass-derived components. Accordingly, even when continuously handling a petroleum-derived plastic before and after applying the mass balance approach, the supplier side must inform the user side of any impact on quality and ask for permission. While that plastic may be deemed quality-wise within the existing process control criteria and unaffected or superior control-wise, as explained above, its acceptability is an issue left to the user’s discretion. In the event of the user’s refusal to grant permission, if more than one manufacturing line exists, priority should be given to feeding to the line not involving raw material mixing. Otherwise, improvisations, such as prevention by changing the manufacturer, will become necessary.
When assigned within the same manufacturing lot, biomass naphtha and its petroleum-derived counterpart or biomass plastic and its petroleum-derived counterpart have no qualitative differences and can be considered practically homogeneous. However, consent must be obtained from the user side regarding quality variations resulting from changes in the input amount of the biomass-derived component relative to that of the existing raw material. Where the mass balance approach is applied, a biomass-derived component has a variable mixing ratio. Therefore, for example, when designing a product using a raw material lot with a high ratio of the biomass-derived component, the manufacturer must determine the acceptability of quality variations due to a drop in that component’s ratio. The impact of raw material quality variations is also true for existing petroleum-derived raw materials. As long as a raw material loaded complies with the standard applicable as of its loading, the raw material will be deemed within the controllable range and can be regarded as practically unaffected in terms of quality.
As seen above, only negligible impacts on quality will result from mixing in a biomass-derived component. However, given that this mixing is a new, unconventional process, it is vital to be ready to monitor the impact on quality relative to the input ratio continuously. It is advisable to be ready to share the input ratio information on each manufacturing lot across the whole supply chain and understand the correlation of each process with control conditions and quality standards until the eventual switchover to the drop-in approach.
3.4 Superiority of the mass balance approach
The preceding subsections described the advantages that the mass balance approach offers and the risks involved. Our examination of each risk identified no fatal impediment to introducing mass balance approach-based biomass plastics. These plastics would provide significant industrial advantages if handled with a certain level of consent.
4. Trends in biomass plastics mounting technology in OMRON’s Control Equipment Business
When introducing any mass balance approach-based biomass plastic, a manufacturer must be well-prepared to address wide-ranging technical issues, including fluctuations in the manufacturing process or material quality, besides the presence of candidate materials to be considered or the characteristic values of the material. Through elaborate verifications based on the technical findings obtained, as explained above, OMRON has developed a new theoretical framework for accepting mass balance approach-based biomass plastics in the control equipment business.
Regarding deploying biomass plastics to the products of the control equipment business, OMRON has already carried out prototype verification tests for multiple products and members. For each member concerned, their respective corresponding petroleum-derived plastic and mass balance approach-based biomass plastic were compared in terms of material property values and their changes during exposure to in-house prescribed environmental conditions; none showed any significant differences. The member-forming process properly formed both plastics under the same forming conditions. The product evaluation results also technically confirmed that the process can guarantee the same quality for both plastics. The petroleum-derived plastic and mass balance approach-based biomass plastic showed no differences as materials despite the differences in their manufacturing processes. We actually confirmed this point based on the results of the abovementioned considerations and concluded that both can be handled as homogeneous. Fig. 6 shows the enclosure of a control equipment product as an example of a prototype. This enclosure is indistinguishable from a conventional petroleum-derived plastic enclosure in all respects, including characteristics and appearance, showing its technical maturity suitable for mounting onto products.
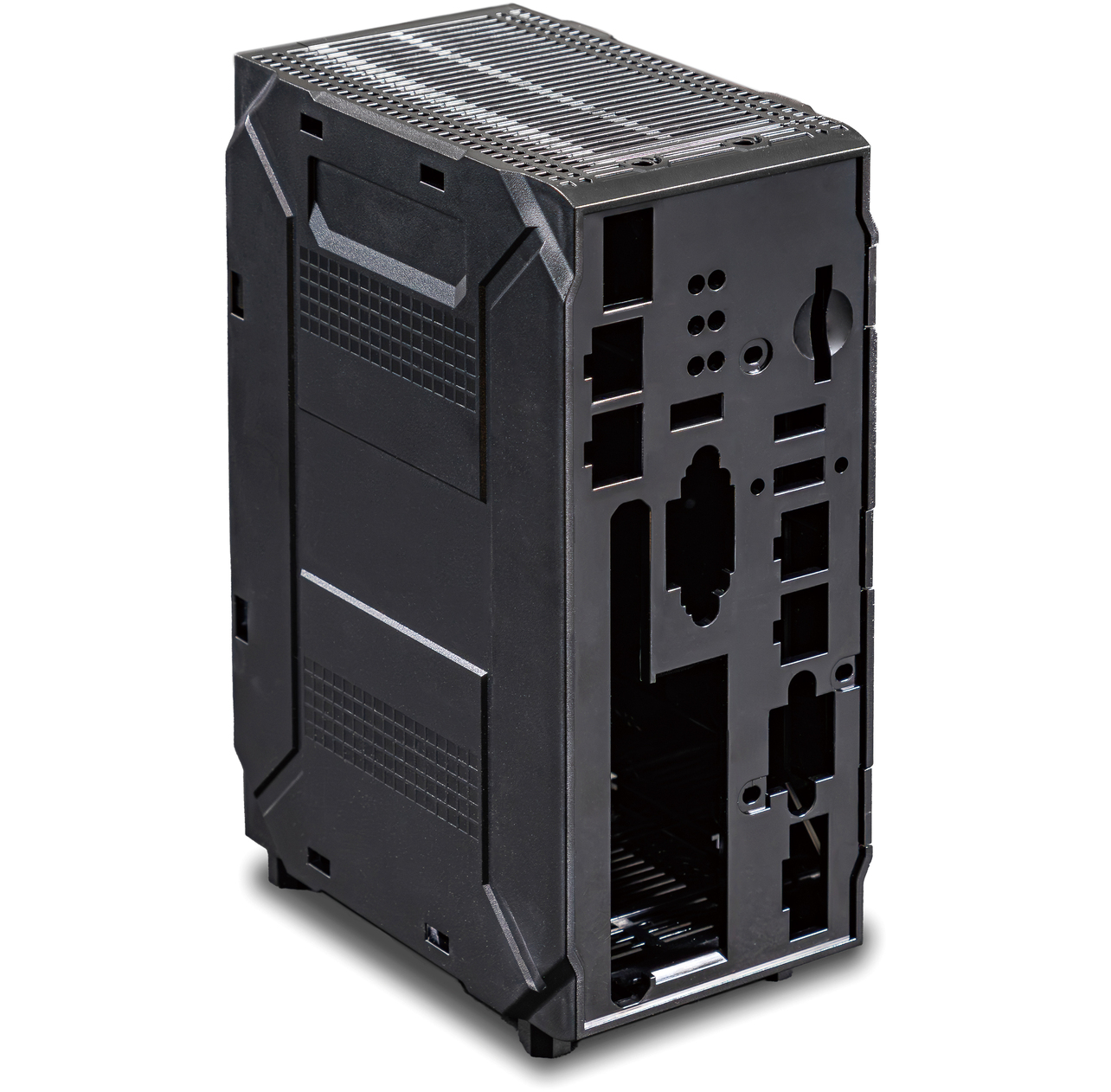
None of the ten domestic competitors of OMRON’s control equipment business has made any apparent move to promote technologies for actively introducing biomass plastics (as of May 2023). Our efforts are highly pioneering ones in the industry.
As seen above, the concept of the mass balance approach serves as a highly effective method for spreading the use of biomass plastics. In addition, the mass balance approach will be effectively applicable to the fields of plastic recycling without being limited to biomass plastics.
The global demand for plastics is expected to increase with an increasing global population. Cyclical use through recycling and society-wide efforts to build up plastic resources will be necessary, besides the shift of raw material sources to biomass, for a carbon-neutral society to become a reality. Plastic recycling is divided into the following: material recycling, which remelts and turns after-use plastics into new products; chemical recycling, which chemically breaks down plastics into raw materials for reuse; and thermal recycling, which makes effective use of the heat from waste plastic disposal by incineration. These recycling methods follow this order of priority with material recycling efforts underway ahead of the rest. Hard-to-material-recycle plastics used to be disposed of primarily by incineration. On the other hand, chemical recycling technologies have made advances in recent years, expanding their applicability, and will become increasingly sophisticated in the future. In chemical recycling, such plastics are handled at the molecular level and originate from a highly diverse spectrum of raw material sources. Therefore, the mass balance approach is as effective for these plastics as when applied to biomass plastics.
5. Conclusions
The present paper has explained the significance of adopting the mass balance approach when intending to spread the use of biomass plastics. At the same time, the present paper considered risks likely to be involved in the actual application of this approach and explained that the approach can be used practically problem-free. The significance of introducing the mass balance approach will be as follows: it can be extensively utilized for application to materials indicative of environmental values, such as chemical-recycled materials, without being limited to biomass plastics, and it will be widely utilized in the future and will be able to become one of the promising measures for realizing a carbon-neutral society. Under the policy presented above, we will actively work on verifying the applicability of chemical-recycled materials in addition to biomass plastics and the impacts of their combined use to support the realization of a carbon-neutral society in the control equipment business.
References
- 1)
- Ministry of Foreign Affairs. “Paris Agreement.” (in Japanese). https://www.mofa.go.jp/mofaj/ila/et/page24_000810.html (Accessed: Nov. 17, 2023).
- 2)
- Cabinet Decision of Oct. 22, 2021. “Long-Term Strategies as Growth Strategies Based on the Paris Agreement.” (in Japanese). https://www.mofa.go.jp/mofaj/files/100305868.pdf (Accessed: Nov. 17, 2023).
- 3)
- OMRON Corporation. “OMRON Integrated Report 2022.” (in Japanese). https://www.omron.com/jp/ja/ir/irlib/pdfs/ar22j/OMRON_Integrated_Report_2022_jp_A4.pdf (Accessed: Nov. 17, 2023).
- 4)
- Ministry of Environment, Ministry of Economy, Trade and Industry, Ministry of Agriculture, Forestry and Fisheries, and Ministry of Education, Culture, Sports, Science and Technology. “Roadmap for Introducing Bioplastics.” (in Japanese). https://www.env.go.jp/content/900534511.pdf (Accessed: Nov. 17, 2023).
- 5)
- Y. Kikuchi et al., “Life Cycle Assessment of Biomass-Derived Polyethylene,” (in Japanese), in Abstracts for 6th ILCAJ Meeting, 2021, pp. 204-205.
- 6)
- K. Taki and N. Kawashima, “Trends in Biomass plastic and Efforts for a Development of Bio-polypropylene,” (in Japanese), J. Soc. Rubber Sci. Technol., Jpn., vol. 95, no. 5, pp. 145-152, 2022.
- 7)
- Workshop on the Mass Balance Approach FY2022. “Reference Document (Domestic and Overseas Situations Surrounding the Mass Balance Approach).” (in Japanese). Ministry of Environment. https://www.env.go.jp/content/000143869.pdf (Accessed: Nov. 17, 2023).
The names of products in the text may be trademarks of each company.