Dimensional Stabilization by Controlling the Higher-order Structure of Polyester Polymers in Electronic Components
- Polymers
- High-order structure
- Dimensional stabilization
- Electronic components
- Evaluation technology
In mechanical devices such as relays and switches, polyester-based polymer molded products are used because of their excellent mechanical/electrical characteristics. On the other hand, it is important to control the dimensions of the molded product because the dimensions of the polyester-based polymer molded product change due to the application of heat. In this paper, we have found that coarsening of polymer crystal sizes is effective as a factor that controls the dimensions of molded products. By heat-treating the polymer in the polyester at a temperature higher than the temperature at which the phase transition occurs, the crystal size becomes coarse and the shape change of the molded product can be suppressed. Changes in dimensions and crystal size were clarified by the amount of linear expansion and X-ray diffraction.
1. Introduction
In recent years, needs have been increasing for electromechanical devices and other electronic components available in ultra-compact bodies or as ultra-thin membranes. Accordingly, precise dimensional accuracy is a requirement for all portions of injection-molded articles. Excellent in mechanical and electrical characteristics and highly moldable and flame-retardant, polyester polymers with glass filler have a wide range of use as molded articles for small electronic components. Our company also uses these materials for electromechanical devices, such as relays and switches1).
On the other hand, resin materials expand and contract due to thermal change more significantly than metal materials. Hence, deformed resin moldings may affect the characteristics of small electromechanical devices2). Regarding the dimensional stability of molded articles, the conventional practice has been, e.g., to adjust molding conditions on production sites or adjust production characteristics to parts窶 dimensions to achieve stable dimensional quality.
We approached the problem of dimensional stability of molded articles from the perspective of polymeric physics and polymeric structural engineering. A polymer heavily depends for its characteristics on its internal molecular geometry and the size of the so-called crystal higher-order structure. Generally speaking, thermal stability increases with a coarser crystal size3). We hypothetically assumed that an increased size of crystal higher-order structure leads to improved thermal characteristics, contributing to dimensional stability.
We devised a preliminary heat treatment process for coarsening the crystal size of polyester polymers. More specifically, we elucidated thermal property differences resulting from the higher-order structure based on the linear expansion measurement and X-ray diffraction analysis before and after heat treatment. In conclusion, it turned out that preliminary heat treatment can coarsen the crystal size of polyester polymers, improving their dimensional stability. In what follows, we report our findings.
2. Experimental Section
2.1 Preparation of molded articles
We prepared two types of molded parts made of a polyester polymer with glass filler to compare them in terms of shape and material properties. Fig. 1 shows the shape of the molded article for part dimension measurement, while Fig. 2 shows the testpiece (3 mmテ20 mmテ0.75 mm t) for material property evaluation cut from a flat sheet (60 mmテ60 mmテ0.75 mm t). The molded article and the flat sheet were molded using an injection molding machine. Besides, the testpiece for material property evaluation was cut at ordinary temperature to the size stated above to minimize thermal effects.
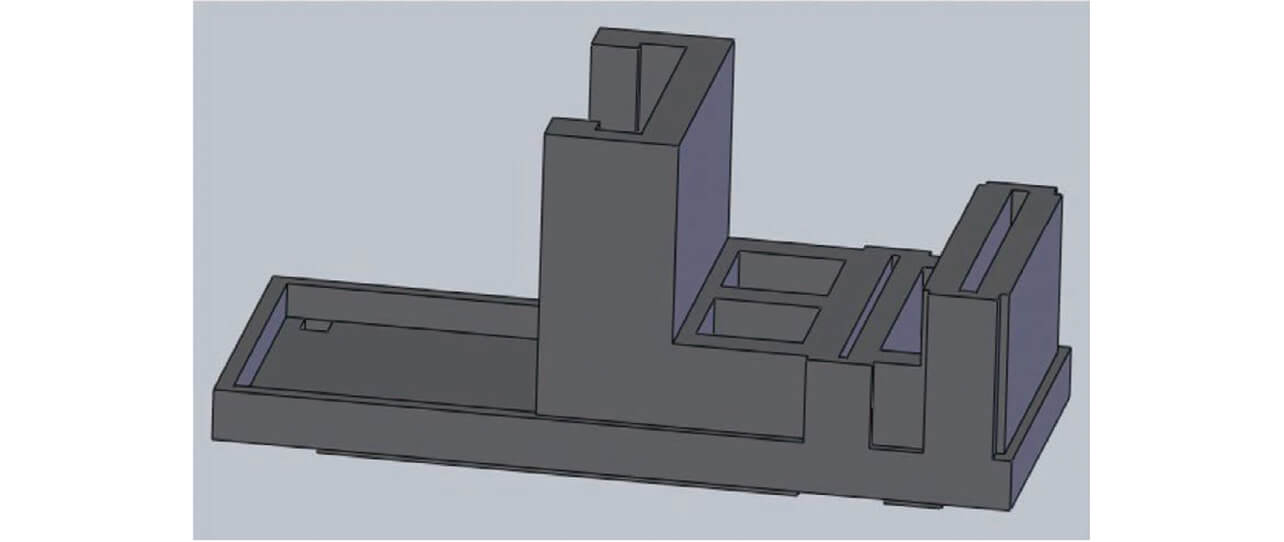
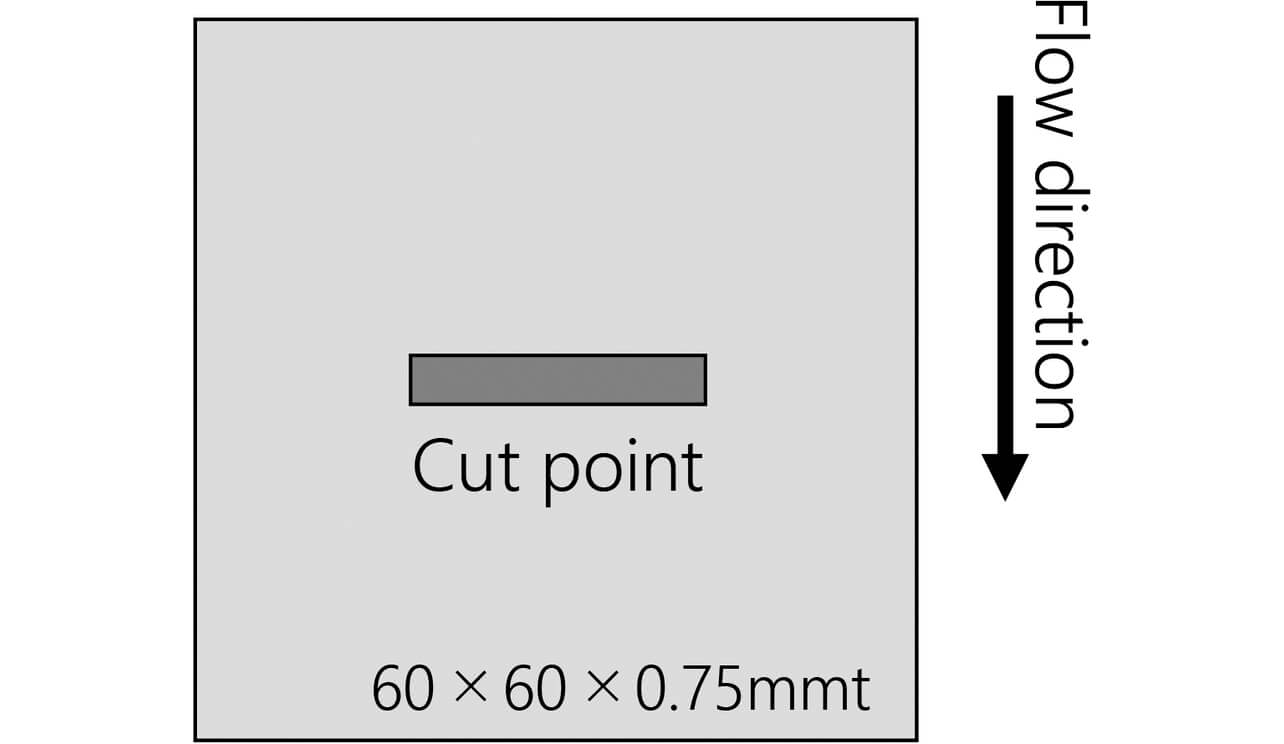
2.2 Measurement
The specimen used for the measurement of the molded article (for part dimension measurement) underwent pre-treatment according to the heat treatment requirements in Table 1 and then further heat treatment. The treated specimen was allowed to cool to the ordinary temperature. Its dimensions were measured at the measurement points in Fig. 3 after pre-treatment and after heat treatment to determine the amount of change.
Pre-treatment conditions | Heat treatment conditions | |||
---|---|---|---|---|
Temperature | Time | Temperature | Time | |
Molded Article 1 |
W/o pre-treatment | W/o pre-treatment | 120ツーC | 30 min |
Molded Article 2 |
140ツーC | 30 min | 120ツーC | 30 min |
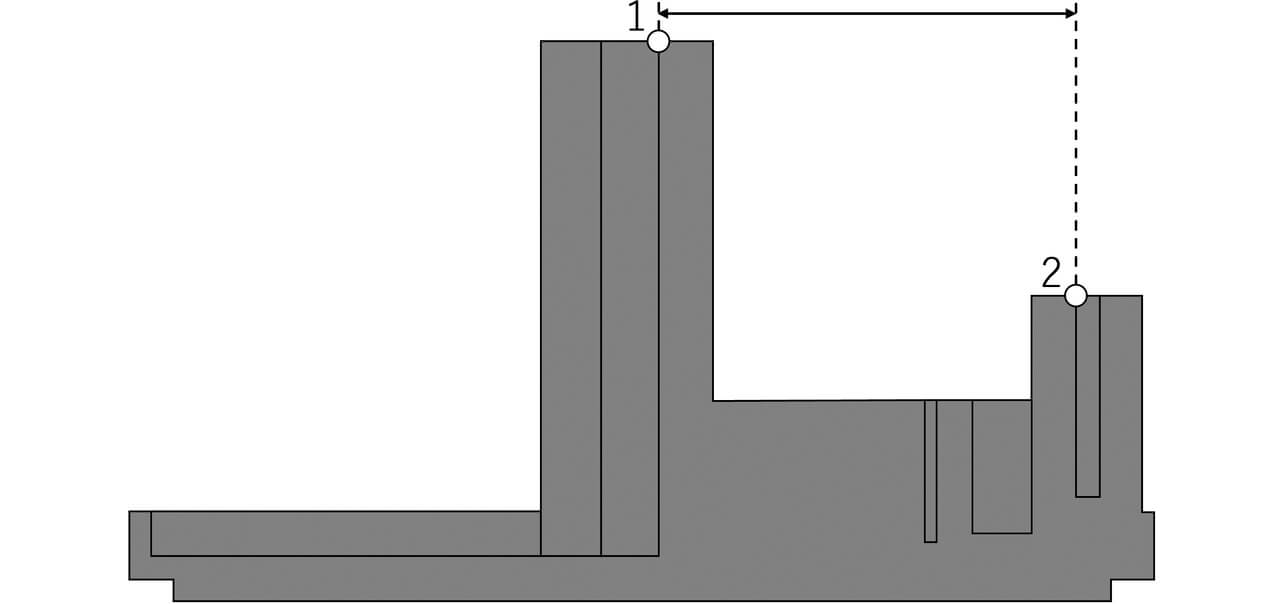
We prepared two testpieces for material property evaluation with different heat treatment requirements (Table 2). The material property evaluation involved linear expansion measurement (TMA) and X-ray diffraction (XRD) analysis.
With or w/o heat treatment | Heat treatment requirements | ||
---|---|---|---|
Temperature | Time | ||
Testpiece A | Without heat treatment | 窶 | 窶 |
Testpiece B | With heat treatment | 140ツーC | 30 min |
The linear expansion measurement (TMA) was performed using an SS6100 Thermomechanical Analyzer manufactured by SII. With the measurement conditions in tensile mode, measurement was taken of the dimensional change during heating from 25ツーC to 200ツーC. Two identical specimens were measured under the same conditions for comparison regarding the effect of heat treatment.
The X-ray diffraction analysis was performed using a Bruker AXS DS Discover X-Ray Diffractometer with a CuKa radiation source (= 1.5418) within a diffraction angle range of 2θ = 5ツー to 60ツー. The crystal size of the polyester polymer material was calculated using Eq. (1) below4):
where the coefficients are as follows: λ = X-ray wavelength (= 0.154 nm); βe = full width at half maximum diffraction peak; β0 = corrected FWHM value (= 0.13ツー); K = Scherrer constant (= 0.9).
3. Results and Discussion
3.1 Results
3.1.1 Dimensional measurement results for molded articles (for part dimension measurement)
Fig. 4 shows the results of measuring the amounts of dimensional change in the specimens in Table 1 before and after heating. Fig. 4 reveals that 窶廴olded Article 1窶 without preliminary heat treatment (pre-treatment) decreased in dimensions, which means that the molded article underwent deformation (dimensional change). Meanwhile, 窶廴olded Article 2窶 with pre-treatment showed little dimensional change. These results indicate that pre-treatment can reduce dimensional change. The following subsections describe how to control dimensional change by preliminary heat treatment (pre-treatment).
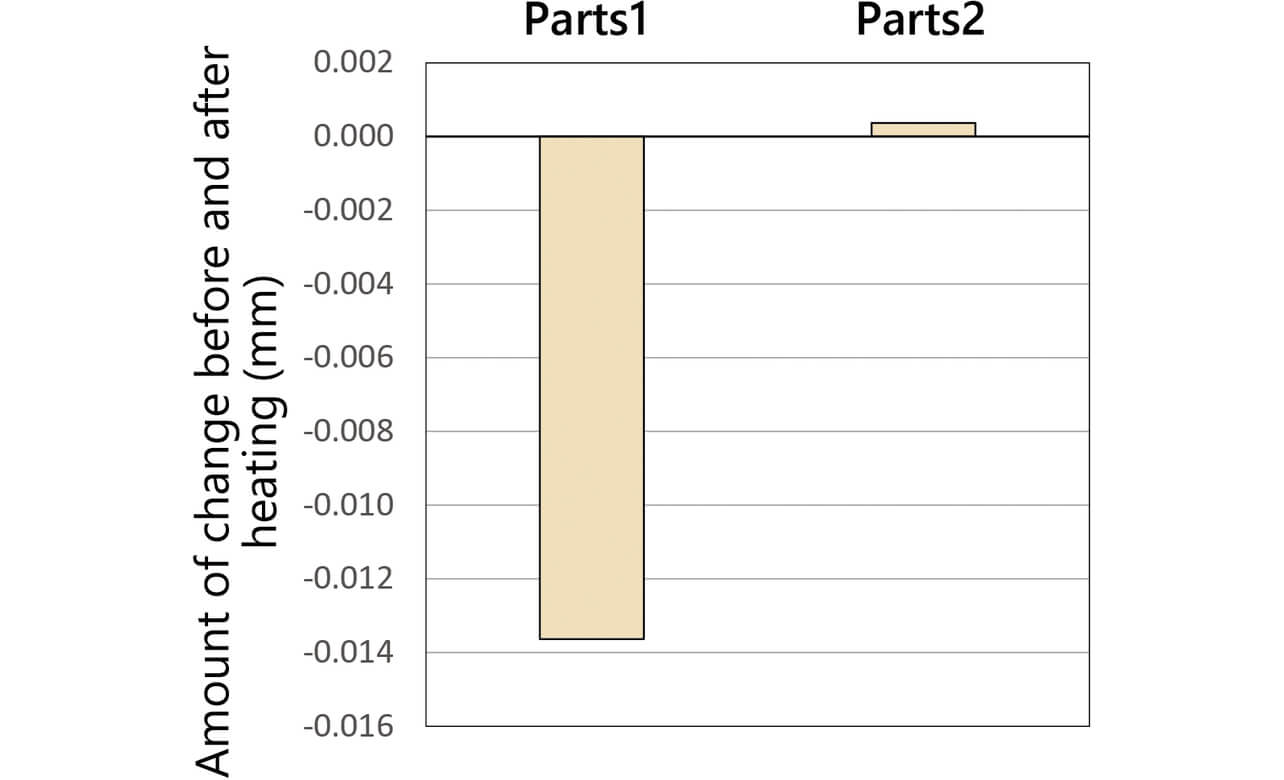
3.1.2 Linear expansion measurement results
This subsection presents how the change caused by heat treatment to the polyester polymer used for the molded articles (for part dimension measurement) in the last section was verified using testpieces. Testpiece A, shown in Table 2, was measured for linear expansion as heated from 25ツーC to 200ツーC; it was then allowed to cool back to ordinary temperature. Defining this series of actions as one single process, we performed this process twice. Fig. 5 shows the obtained results.
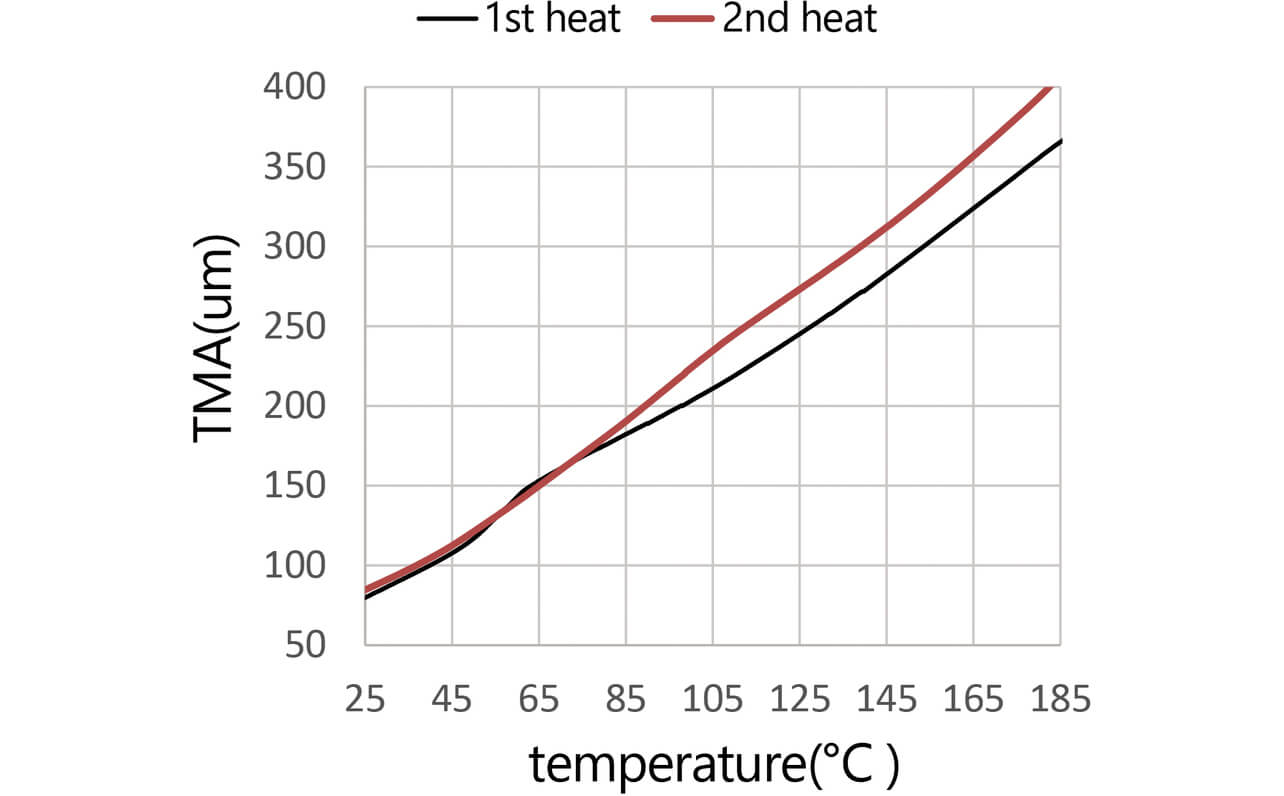
Fig. 5 confirms that the testpiece showed an increasing linear expansion tendency at any point in the two heating sessions with rising temperature. Besides, the testpiece showed different linear expansion tendencies from 65邃 to near 100邃 for the first and second heating sessions, with a reduced expansion slope for the first.
Then, we performed the same evaluation on Testpiece B as Testpiece A to verify the effect of heat treatment history on linear expansion. Fig. 6 shows the obtained results. Fig. 6 reveals that the two testpieces behaved identically with the same amount of linear expansion until near the heat treatment temperature of 140ツーC, after which the two exhibited different linear expansion tendencies.
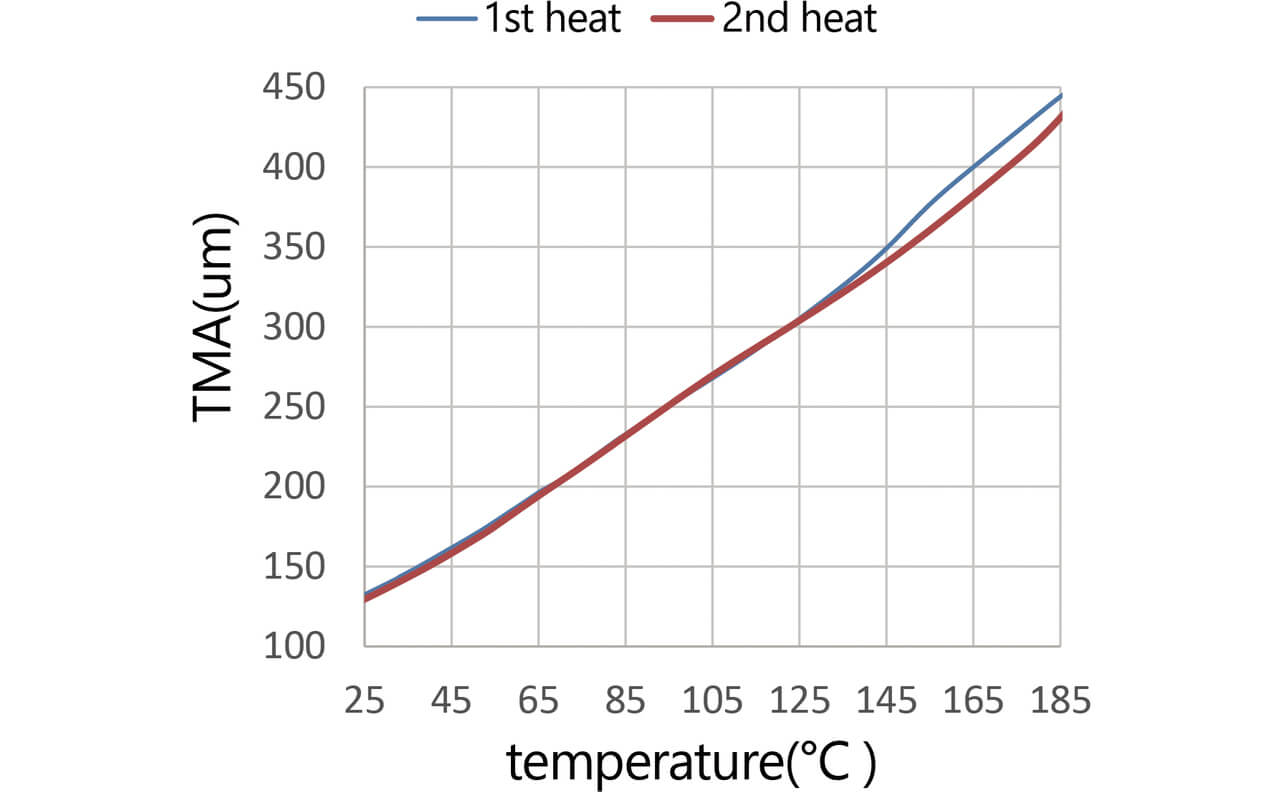
To help examine specific changes in behavior, Fig. 7 shows the results of plotting the linear expansion slopes during the first heating session for Fig. 5 (without heat treatment) and Fig. 6 (with heat treatment). In Fig. 7, Testpiece A (without heat treatment) exhibited a near-60ツーC (55ツーC) peak (phase transition peak), indicating the glass transition temperature of the polyester polymer, while Testpiece B showed no phase transition peak near the glass transition temperature.
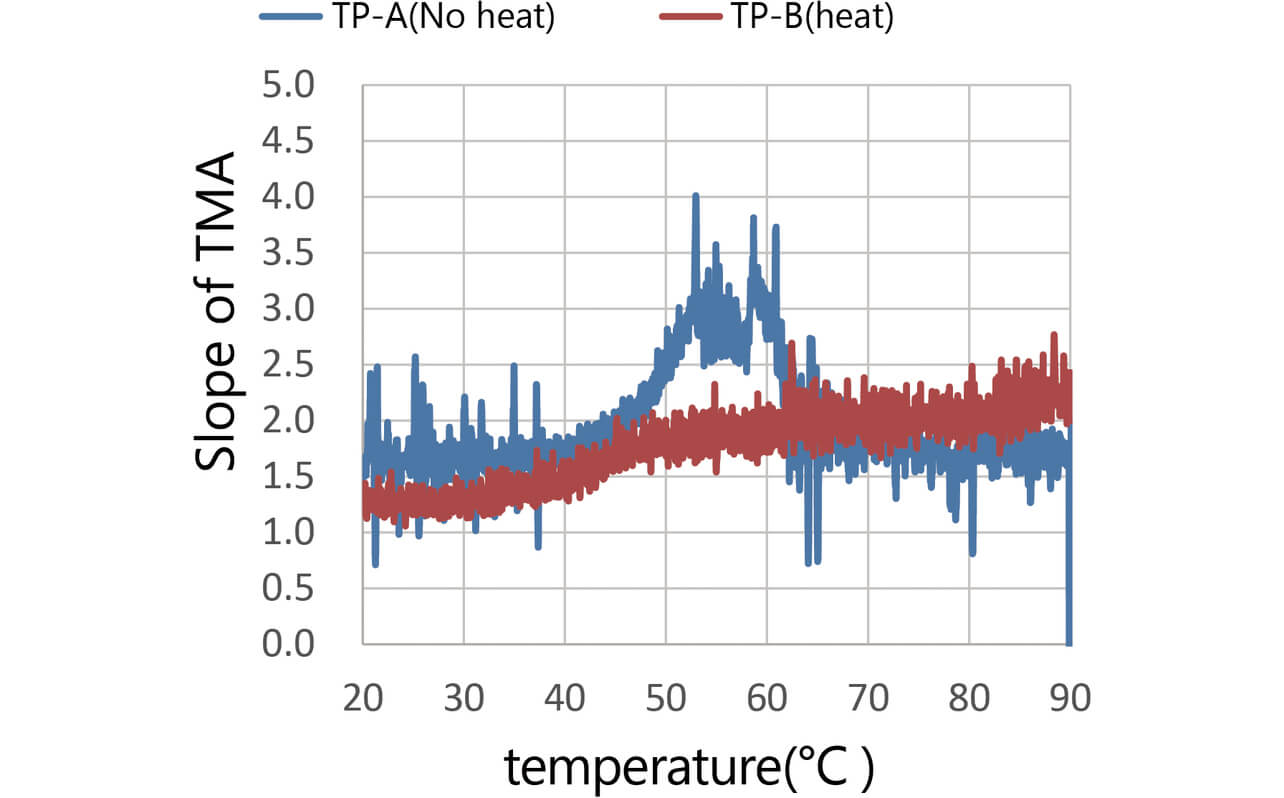
It turned out from the above tendencies that heat treatment can suppress phase transition at the glass transition temperature. This result allowed us to reproduce the dimensional change behavior of each molded article as material properties.
3.1.3 X-ray diffraction measurement results
We performed an X-ray diffraction analysis to identify the factor responsible for the suppression of the phase transition at the glass transition temperature in the last subsection. Fig. 8 shows the X-ray diffraction patterns for two specimens with different heat treatment requirements (without heat treatment (Testpiece A) and with heat treatment and 140ツーC (Testpiece B), as shown in Table 2). A peak attributable to the α crystal of the polyester polymer is visible near 2θ = 15ツー to 25ツー. Note that the acute peak is attributable to the glass filler or additive.
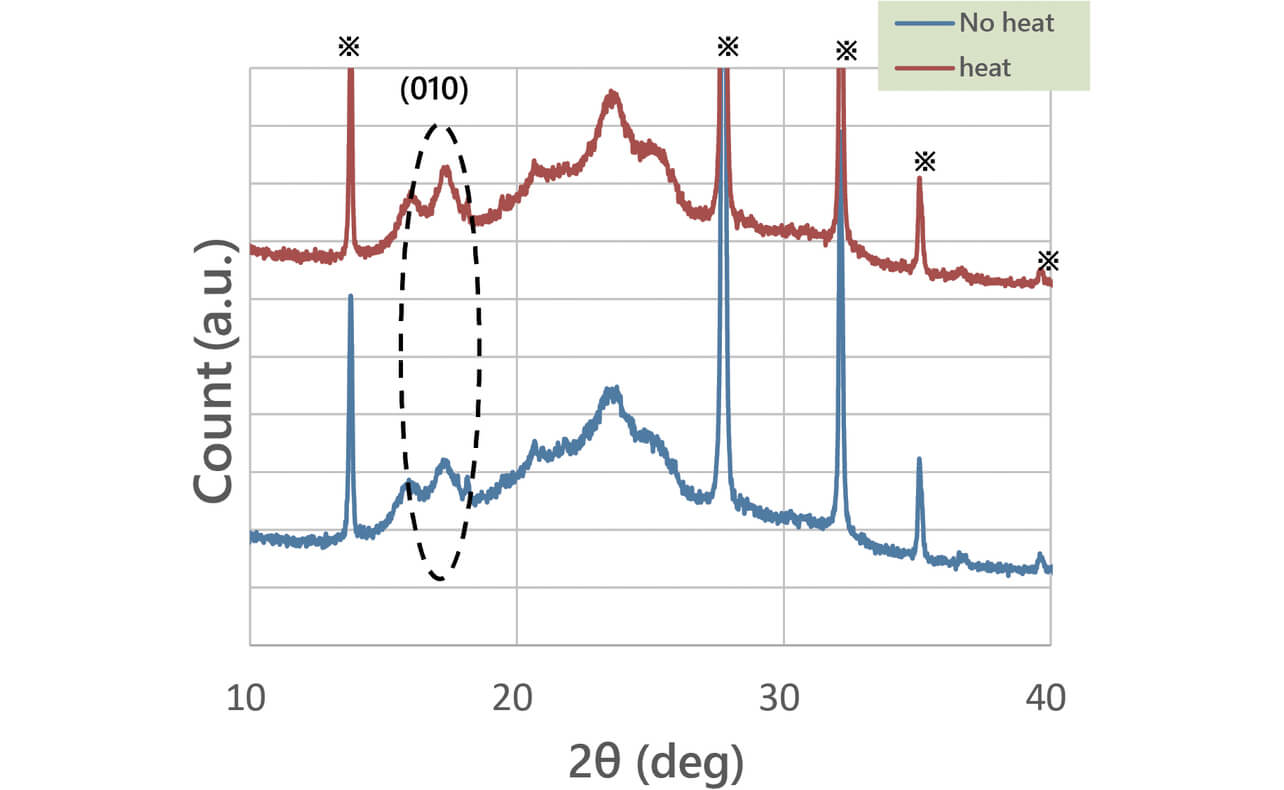
(Note: Asterisks (*) = peaks attributable to the glass filler or additive contained in the polyester)
Our discussion here revolves around the (010) facet near 17.3ツー, the peak characteristic of polyester4). After heat treatment, this peak became sharper, with the FWHM5) reduced from 0.940 to 0.858.
Besides, based on this FWHM, we calculated the crystal size using Eq. (1). The crystal size measured 8.5 nm and 9.6 nm before and after heat treatment, respectively, which means that the heat treatment resulted in an approximately 10% coarsening of the crystal size. In other words, the heat treatment-induced coarsening of the crystal size of the polyester polymer was shown to have caused the change in the dimensions of the molded article itself.
3.2 Discussion
The testpiece with preliminary heat treatment (pre-treatment) showed the same linear expansion tendency after the first and second heating sessions, whereas the one without preliminary heat treatment (pre-treatment) exhibited a change in linear expansion tendency. This contrast can be explained by the crystal size coarsening detected by the X-ray diffraction analysis. With the crystal size coarsened by heating, the free volume between polymer molecules was reduced, increasing the density of the polymer, resulting in a reduced linear expansion slope. After preliminary heat treatment (pre-treatment), the subsequent heating caused no change in the crystal size, leaving the linear expansion tendency unchanged. On the other hand, when heated without preliminary heat treatment (pre-treatment), the crystal size was coarsened, causing a change in linear expansion. These results led us to attribute the difference in dimensional change between molded articles with and without preliminary heat treatment (pre-treatment) to the change in linear expansion due to a coarsened crystal size. A reinterpretation at the higher-order structure level would have it that with preliminary heat treatment, the crystallized size of the polyester polymer became coarser and insensitive to the effect of the glass transition temperature. Hence, the polymer underwent a reversible change without a dimensional change.
4. Conclusions
Polyester polymer molded articles used for electromechanical devices, such as relays and switches, are prone to show dimensional changes when exposed to heat. Hence, it is important to ensure that molded articles have thermally stable dimensions. From the thermally-induced dimensional change behavior of molded articles/parts (for part dimension measurement), we found the possibility of dimensional stabilization through preliminary heat treatment (pre-treatment) and sought to identify the cause. We applied a higher-order structural analysis technique based on linear expansion measurement and X-ray diffraction analysis to the polyester polymer of interest to elucidate the relationship between dimensional changes and higher-order structural analysis. More specifically, based on the linear expansion measurement and X-ray diffraction analysis before and after heat treatment, we clarified the thermal property differences resulting from the higher-order structure.
In conclusion, we found that polyester polymers have their crystal size coarsened as exposed to high temperatures. We expect that polyester polymers with their crystal size coarsened by subjection to preliminary heat treatment will show stable dimensional changes in high-temperature ranges and contribute to product quality enhancement. Going forward, we will address quality improvement of other products through technology deployment to other crystalline resins.
References
- 1シ
- S. Yamao, 窶廡undamentals of Thermoplastic Resins,窶 (in Japanese), J. Jpn. Inst. Electron. Packag., vol. 7, no. 2, pp. 186-193, 2004.
- 2シ
- K. Soda, Y. Yokote, and I. Takegahara, 窶弋hermal Deformation Prediction Technology of Resin Parts Using Anisotropic Materials,窶 (in Japanese), OMRON TECHNICS, vol. 52, no. 1, pp. 92-98, 2020.
- 3シ
- Y. Matsushita, et al., Structures and Physical Properties of Polymers, 1st ed., Tokyo, Kodansha (in Japanese), 2013, 560p., 978-4-06-154380-5.
- 4シ
- Japan Society of Polymer Processing (ed.), Introduction to Higher-order Structural Analysis of Plastic Moldings, 1st ed., Tokyo, Nikkan Kogyo Shimbun, Ltd. (in Japanese), 2006, 192p., 978-4-52-605604-8.
- 5シ
- Konica Minolta Japan, Inc., 窶廴easurement Wavelength Interval/Full Width at Half Maximum,窶 Key Information Available from Specification Tables-3 (in Japanese), 2011, https://www.konicaminolta.jp/instruments/knowledge/color/section4/05-3.html, 2022 (accessed Feb. 25, 2022).
The names of products in the text may be trademarks of each company.