OMRON to Introduce Four Series of Condition Monitoring Devices - Visualize Facility Condition That Could Not Have Been Seen -
November 20, 2017
OMRON Corporation (HQ: Shimogyo-Ku, Kyoto. President and CEO: Yoshihito Yamada) will introduce on November 29, 2017 and February 1, 2018, four series of condition monitoring devices to monitor operational status in manufacturing sites for workers; Motor Condition Monitoring Devices that predict a failure of 3-phase induction motors, Power Supplies with Network that can predict the service life and failures of a power supply installed in a control panel, Flow Sensors and Pressure Sensors that monitor hydraulic oil and cooling water used for press machines and molding machines, and Smart Condition Monitoring Amplifier that accelerate IoT of existing analog sensors installed in facilities or machines.
The release of condition monitoring devices is part of an OMRON's effort aiming at completing 100,000 IoT components lineup. The monitoring devices visualize facility and equipment condition constantly that could not have been seen, detect status errors of facilities in advance, and maintain production lines and productivity. With i-BELT, IoT service platform for manufacturing sites, the devices will store and analyze the collected data, reflect it on device control as a control algorithm and automate craftsmanship.
In recent years, manufacturing industry has a serious shortage of skilled workers due to expansion of optimal production locations and aging society. By contrast, maintenance operation is getting more and more complicated and difficult along with advanced high speed facilities. Under these circumstances, there is a growing need for visualizing production facility condition and collecting data in operation using IoT and other technologies to enhance operating ratio in sites. The lineup of devices to satisfy the need, however, has not been completed yet. Visualization of data has no uniformity or synchronization since each manufacturer develops and releases devices, this is why production sites are still in the process of trial and error.
OMRON has categorized facility configuration elements into the following three groups as a method of visualization to understand conditions of various positions on facilities and enhance the operating ratio.
1) Power: power source of facilities such as motors or pumps
2) Circulation: liquid to maintain facility performance such as cooling water or hydraulic oil
3) Mechanism: components to process products such as cylinders or actuators
We are going to release optimum condition monitoring devices that detect changes in each configuration element to predict the service life and solve issues that lead to failures.
The condition monitoring devices monitor changes in power system and circulation system of production facilities in real time. They inform replacement time of parts before failures through communications networks, and contribute to prevention of unexpected facility stoppages and quality abnormality of products. Anyone can easily capture a sign of abnormality of facilities and failures that have relied on experience and intuition of skilled workers. This enables to reduce opportunity loss due to unexpected facility stoppages and enhance the accuracy of maintenance plans.
OMRON set forth a strategic concept called "innovative-Automation!" *1 consisting of three innovations or "i's"--"integrated" (control evolution), "intelligent" (development of intelligence by ICT), and "interactive" (new harmonization between people and machines). We will expand the lineup of condition monitoring devices in the future, accelerate "intelligent" (development of intelligence by ICT) in manufacturing sites which is the key to realize "innovative-Automation!" with customer companies, and aims to enable significant productivity and quality improvements in manufacturing sites.
OMRON exhibits condition monitoring devices and other products, technologies, and solutions that contribute to IoT in manufacturing sites at System Control Faire 2017 at Tokyo Big Sight from November 29 (Wed.), to December 1 (Fri.), 2017.
Four series of condition monitoring devices to be sold
Motor Condition Monitoring Devices
(scheduled date of sale: November 29, 2017)
Motor Condition Monitoring Devices detect errors caused by aging deterioration of three-phase induction motors *2 used for many production facilities including conveyors, lifters and pumps. The monitoring devices detect errors by status changes in vibration, temperature, current, insulation resistors, monitor by display on the main unit or Ethernet/IP™ communications remotely, and solve the following issues.
- Minimize opportunity loss caused by unexpected facility stoppages
- Digitalize knowledge of skilled maintenance engineers and homogenize motor maintenance from a remote location
- Shift from periodical inspection to preventive inspection to significantly reduce inspection work
- Monitoring data
- Motor vibration, surface temperature, insulation resistance, current, degradation level *3
- Output method
- EtherNet/IP (monitorable by a dedicated tool operated on PC), alarm output, transistor output, bar indicator, monitor display
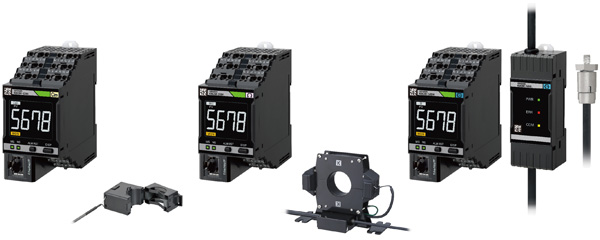
Power Supplies with Network
(scheduled date of sale: November 29, 2017)
Power Supplies with Network visualize necessary information to maintain and control power supply in addition to supply DC electricity to devices in facilities, which is a basic function of a power supply. This Power Supplies can visualize when to replace itself, information on output voltage/current, and boost current by remote control using Ethernet/IP communications and the main unit monitor, contributing to solve the following issues.
- Notify the power supply replacement time in advance to reduce unexpected facility stoppages due to a trouble of power supply
- Monitor the replacement time, total run time, voltage, and current of a power supply remotely to reduce maintenance work in sites
- Use in combination with the dedicated software Power Supply Monitoring Tool (scheduled to support soon) to visualize power supply condition on the derating curve *4. To extend the service life, you can consider and implement improving measures easily by improving installation environments and changing power supply capacity.
- Monitoring data
- Years until power supply replacement, total run time, output voltage/current, boost current, self-diagnostics (overheating, measured value error, memory error), product model, serial number
- Output method
- Ethernet/IP, Modbus/TCP, monitor display
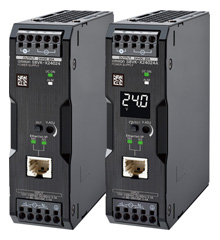
Flow Sensors, Pressure Sensors
(scheduled date of sale: February 1, 2018)
A single Flow Sensors can measure both flow rate and temperature of cooling water used for a welding or molding machine. Monitoring errors caused by temperature in addition to flow rate of cooling water enables to capture a sign of unexpected stoppages due to overheated current transformers, enabling to achieve more stable welding quality, and prevent defective molding.
Pressure Sensors visualize pressure and temperature of hydraulic oil for machining centers *5 and press machines simultaneously. They capture a sign of packing deterioration due to temperature rise and following hydraulic oil leakage. They also detect temperature changes due to deterioration of the hydraulic oil viscosity to maintain stable processing quality.
You do not need to install a pressure sensor and a temperature sensor on pipes separately, which halves number of sensors to be installed and installation work.
By sensing a plurality of measurement data elements such as "flow rate and temperature" and "pressure and temperature" by itself, these sensors can visualize facility condition at less cost, work, and space.
- Monitoring data
- Flow rate + temperature
Pressure + temperature - Output method
- Status output, control output, analog output, IO-Link, monitor display, status indicator
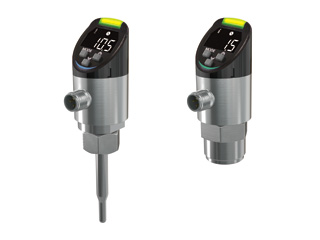
Smart Condition Monitoring Amplifier
(scheduled date of sale: November 29, 2017)
Smart Condition Monitoring Amplifier connect to general analog output sensors *6.
OMRON offers N-Smart *8 Next-generation Sensor Series that connect to fiber sensors and lase sensors. Now, Smart Condition Monitoring Amplifier that can connect to general analog output sensors are joining the lineup, enabling to build inexpensive and easy network with various sensors *7 used to understand facility condition.
Previously, obtaining data of analog output sensors required system up with expensive data loggers and measurement equipment. The sensor can synchronize up to 30 units at high speed of 1 ms, collect data at the timing of facility operation, capture subtle changes of facilities and correlation of signs reliably, enabling optimum machine control according to facility status changes.
- Connectable sensor heads
- Sensors which output and transmit measurement result by current (DC 4 to 20 mA) or voltage (1 to 5 VDC).
(Flow Sensors and Pressure Sensors are also connectable.) - Output method
- Control output, monitor display, compatible with open networks (EtherCAT®, CC-Link) by connecting to communications units.
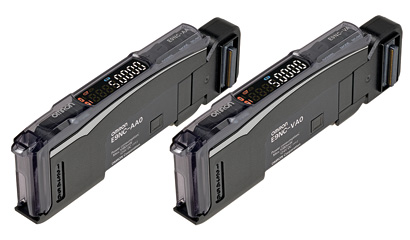
*1 "innovative-Automation!"
Recently, OMRON has developed a manufacturing innovation concept, called "innovative-Automation!" With this concept, OMRON is currently committed to bringing innovation to manufacturing sites through three key innovations, or three "i's." Through these innovations, OMRON aims to enable significant productivity improvements in manufacturing sites in order to enhance high-value-added manufacturing. With the first "i" "integrated" (control evolution), OMRON will seek to advance automated control technology so that virtually any operator, even inexperienced operators, can effortlessly perform work that previously required the expertise of experienced workers. With the second "i" "intelligent" (development of intelligence by ICT), OMRON seeks to create constantly evolving equipment and production lines. By adopting a wide range of control devices and artificial intelligence (AI), machines can learn through experience and contribute to optimal maintenance. For the third "i," "interactive" (new harmonization between people and machines), OMRON will pursue the development of a new harmonious relationship between human operators and machines. Working together in the same workspace, machines will be able to assist human operators by recognizing human intentions and behavior.
*2 An induction generator which use 3-phase AC power supply, send electric power from primary side (stator) to secondary side (rotor) by electromagnetic introduction, and generate power.
*3 It is an OMRON's unique index to show errors on the load side in addition to motors by measuring and analyzing motor current by a unique algorithm.
*4 Stipulate the use conditions by ambient operating temperature and load ratio under which specifications of a power supply can be guaranteed. Operation characteristics of internal circuits caused by temperature rise of internal parts and temperature environments are taken into account.
*5 Processing equipment that makes a hole and grind on metal or other materials.
*6 Sensors which output and transmit measurement result by current (DC 4 to 20 mA) or voltage (1 to 5 VDC).
*7 Air pressure sensors which monitor air suction state, or other sensors for pick and place of electrical parts
*8 Next-generation sensor series consisting of sensor communications units that integrate presence, detection and measurement data of fiber sensors, laser sensors, contact sensors, and proximity sensors. They are also compatible with EtherCAT and CC-Link (high-speed communications open network).
About OMRON Corporation
OMRON Corporation is a global leader in the field of automation based on its core technology of "Sensing & Control + Think." Established in 1933, OMRON has about 36,000 employees worldwide, working to provide products and services in 117 countries. The company's business fields cover a broad spectrum, ranging from industrial automation and electronic components to automotive electronics, social infrastructure systems, healthcare, and environmental solutions.
In the field of industrial automation, OMRON supports manufacturing innovation by providing advanced automation technology and products, as well as through extensive customer support, in order to help create a better society.
For more information, visit OMRON's website: https://www.omron.com/.
- EtherCAT® is a registered trademark and patented technology, licensed by Beckhoff Automation GmbH, Germany.
- EtherNet/IP™ is the trademark of ODVA.
- CC-link is a registered trademark of Mitsubishi Electric Corporation. The trademark is managed by the CC-link Partner Association.
- Contact (media):
- Corporate Communications Department
OMRON Corporation
TEL: +81-75-344-7175 - Contact (about Motor Condition Monitoring Devices/Power Supplies with Network):
- Component Division, Product Business Division HQ,
Industrial Automation Company,
OMRON Corporation
TEL: +81-75-344-7231 - Contact (about Flow Sensors, Pressure Sensors, and Smart Condition Monitoring Amplifier):
- Sensor Division,
Product Business Division HQ,
Industrial Automation Company,
OMRON Corporation
TEL: +81-75-344-7022