Core Technology
Core Technology
Zooming in on OMRON’s Digital Design and Transformation Technologies (Part 2 of 2)
— Shaping the future society with advanced simulation technology -
Feb.13,2024
For better or worse, the COVID-19 pandemic has catalyzed the rapid expansion of initiatives to resolve social issues by transforming business and management through digital technology. Now that the global epidemic is behind us, a call has become even louder for efforts to make the most of cloud services and AI to create new value by integrating digital and physical technologies.
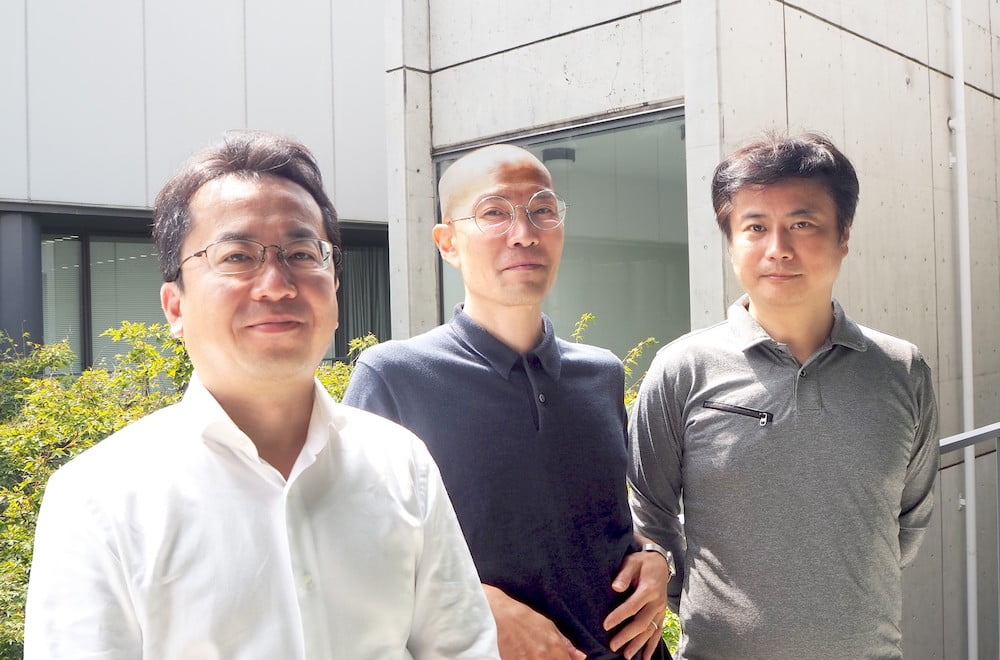
In response to this urgent call, in April 2022, OMRON established the Digital Design Center under the Technology and Intellectual Property H.Q., its corporate R&D division, in a bid to advance its digital technologies, which is essential for digital transformation (DX) of the Group’s engineering chain(1).
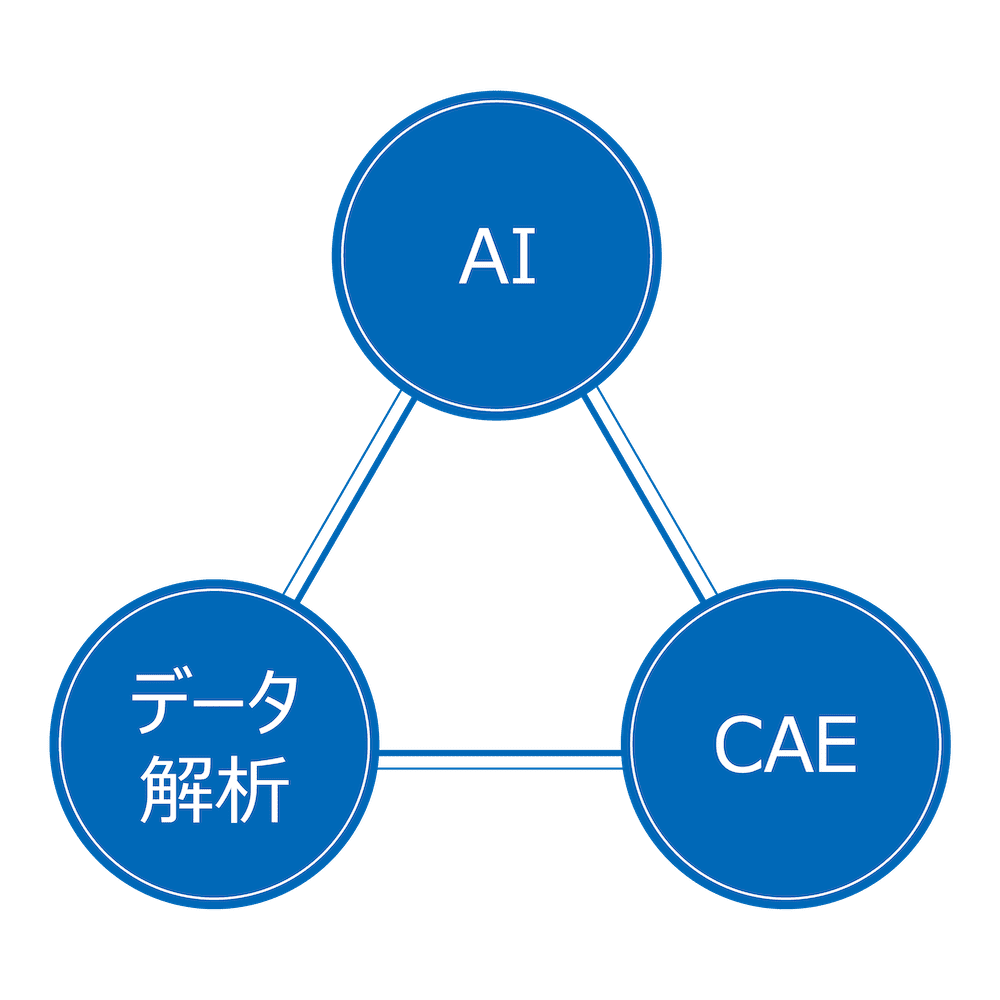
To roll out digital technologies that innovate OMRON’s manufacturing throughout the Group, the new center is taking a three-pronged approach of Data Analysis, CAE(2), and AI. Under the lead of Daisuke Matsubara, Naoki Tsuchiya and Akihiro Funamoto are taking on “Data Analysis and AI” and “CAE,” respectively, as they challenge themselves on a daily basis in pursuit of their chosen issues.
(1) A series of business processes of manufacturing companies, from planning conception to design, preparation for production, production, and after-sale services
(2) Computer-Aided Engineering: Using computer software to perform technical calculations, simulation, and analysis
In the first part, “Driven by data, OMRON’s AI and Data Analysis specialists take on the challenge of digitally Transforming the Group’s entire engineering chain,” we featured the vision and future that the Digital Design Center aspires to realize and their initiatives for “Data Analysis” and “AI,” which are essential for realizing their aspirations.
In this second part, we asked Akihiro Funamoto, who is taking the lead in “CAE,” the third element of their three-pronged approach, about the rationale of their initiatives, the vision they seek to realize, and approaches unique to OMRON.
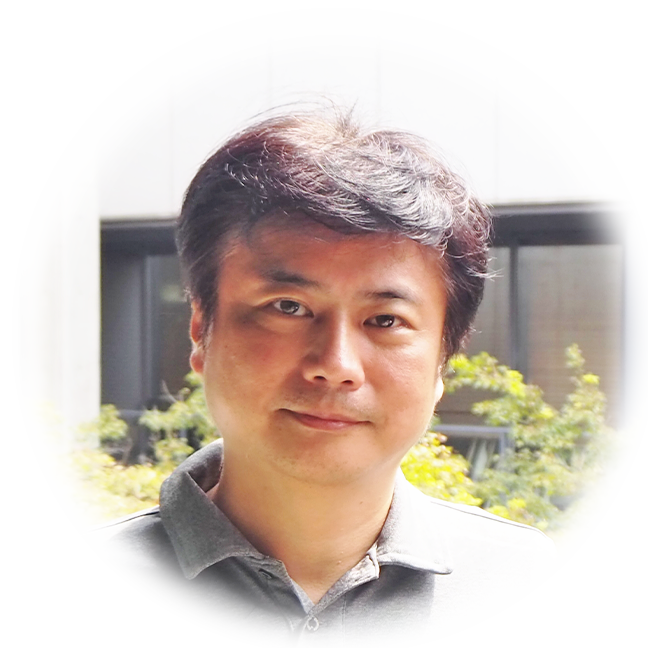
Akihiro Funamoto
Manager, Digital Design Center
1997: Joined OMRON Corporation. Worked on the development of devices at the Technology and Intellectual Property H.Q. and the Device & Module Solutions Company, which is responsible for OMRON’s electronic components business, using CAE in the development process in his own way
2009: Transferred to OMRON Environmental Solutions Business H.Q., where he was engaged in R&D of power conditioners for photovoltaic power generation systems and storage systems
2022: Facilitating DX of internal operations by CAE technologies at the Digital Design Center, Technology and Intellectual Property H.Q.
What do you think are the roles CAE should play at the Digital Design Center?
In its long-term vision of “Shaping the Future 2030 (SF2030),” OMRON has chosen three social issues that it will address toward fiscal 2030, namely, “Achievement of carbon neutrality,” “Realization of a digital society,” and “Extension of healthy life expectancy.” To find reliable solutions to these issues, we take it as the mission of the Digital Design Center to deliver “what is good” “quickly.”
The world is becoming increasingly uncertain; components are hard to get, and the needs keep diversifying. Under such circumstances, we are trying hard to enhance our technological prowess and increase development productivity to deliver better products in a shorter time. That’s our aspiration.
CAE and other digital technologies have made it possible to reproduce products on the computer screen, but the team of human developers is still often working on design and prototype studies based on their past experiences of success and rules of thumb. For instance, when considering new components, we often use the rule of thumb and just give it a try, assuming that it will work. But this approach may or may not work, and we have to go back to previous processes. And I must admit that we still have a gap between our aim and actual results. If we are to digitalize rules of thumb that are in the head of experienced operators, like, if you use this component, you will get this, and do a simulation, we could verify the process without making physical prototypes, with the result that we can develop excellent products faster.
I heard the Digital Design Center is taking a three-pronged approach of Data Analysis, CAE, and AI. What does that entail?
I said earlier that you could do a simulation if you have components, successful experiences, and rules of thumb of experts. Our approach is to use past data to increase the probability of success. That is what the three-pronged approach of Data Analysis, CAE, and AI means. Using purchased simulation software is not enough; we add data and ideas to the process so we can train it. OMRON’s strength here lies in the fact that we have experienced all manners of manufacturing and accumulated a huge stock of data and know-how from the field.
In some ways, OMRON is still fumbling its way to utilize digital technologies. In addition to how to make good use of the limited data that can be acquired, we are trying to take the approach of creating new expertise by making hypotheses in advance and working with the team to acquire data and analyze that data closely.
I see. You’re leveraging OMRON’s strength in that approach. Now, we would like to ask more specifically about CAE. Could you share some example cases with us?
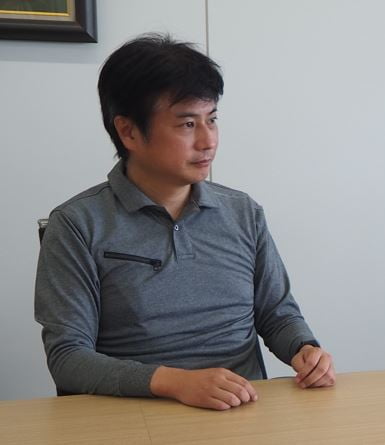
I have one example at the Technology and Intellectual Property H.Q. In the power electronics field, we use CAE to analyze electricity and magnetism. Furthermore, as a way to apply CAE, we introduced optimization technology,(3) which led to a significantly shortened design lead time. There is constant pressure for greater compactness and lower cost for power electronics products, so designing them is highly challenging and time-consuming.
In the past, we had to go through multiple rounds of design and prototype study processes, relying on successful experiences and rules of thumb. By introducing CAE-enabled optimization technology, however, we were able to reduce the number of prototype studies or speed up the optimization execution time by using a surrogate model.(4) The result was a 75% improvement in the total development human-hours. This is exactly what we expect from high-cycle management.
To adopt such an approach and get the result that we desire, it’s vital that we think the same way as those in the field. If we become fixated on digitalizing the process, we may lose track of what we were aiming at. So, under the shared desire to release good products early, we make it a rule to remain on the same page with them as to exactly what outcomes we expect to see and when.
(3) A technology that helps pick the optimal choice from among various combinations of analysis conditions in order to achieve the desired analysis
(4) A technique for computing/predicting phenomena by using machine learning (neural network, etc.) in place of numerical simulation
What value can such initiatives offer?
As in the case I touched on earlier, the biggest value we can offer is contribution to development productivity. While we work on the enhancement of development productivity, we end up conceiving new simulation techniques or incorporating state-of-the-art technologies, which in turn help us grow substantially. And when we become better, the productivity of the development team itself increases, and the cycle will continue to spiral upward. Also, by working closely with the field staff to ask them to take necessary data beforehand without fail, we can accumulate other data that may prove useful in the future when we try new simulation rounds.
Could you tell us what we can expect from your future initiatives?
For us to fulfill the roles CAE is expected to play, which I mentioned at the outset, we are hoping to establish a digitalized development process soon so we can roll it out throughout the Group. To make this happen, I believe we need to strengthen “technology,” “tools,” and “human resources,” respectively.
We want to develop more new CAE technologies and deliver the latest digital tools, which we hope will help our peers improve their skills as they use them. That’s the cycle we hope to establish in collaboration with every development division of the OMRON Group.
OMRON has a proud history of having various divisions work on CAE through horizontal connections, and I cannot stress enough that we have a human network that covers the entire Group, which is one of the sources of our strengths. The Digital Design Center collaborates with different divisions to establish a method and shares the same throughout the Group. This is a tactic that we will continue to pursue. Digitalization doesn’t mean anything unless we keep gathering data and putting it into use. The key going forward is how we make one successful case after another to maintain this virtuous cycle.
Finally, what is the most appealing part of working for OMRON Digital Design Center?
One aspect of OMRON’s corporate culture is encouraging its members to take on new challenges to solve social issues. The Technology and Intellectual Property H.Q., in particular, takes one step further to allow its engineers to work on their projects in constant contact with the latest technologies, which I find very intriguing. Also, OMRON has so many different departments to which they can deliver their new technologies. I think it is also appealing that we can all have a sense that we make contributions to society by solving social issues.
We have one last question for Daisuke Matsubara, who is taking the leading role in the Digital Design Center.
With all these features you’ve just walked us through, what kind of a future does the Digital Design Center wish to achieve?
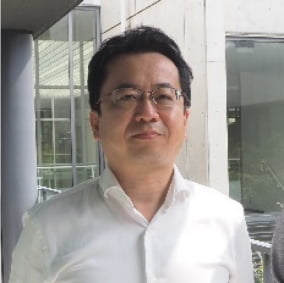
Matsubara: By supporting DX of the Group’s entire engineering chain, we hope to accelerate the process of delivering and implementing the value that OMRON has to offer to society. We also hope to speed up the cycle of providing one new value after another. By doing so, we wish to contribute to the early resolution of social issues that OMRON has chosen to address.
What do you think of OMRON’s attempt at DX through the maximum use of data? Our adventurous journey will continue further. If you empathized/resonated with their efforts, why don’t you join them in their endeavor?
You may also like:
Zooming in on OMRON’s Digital Design and Transformation Technologies (Part 1 of 2)—Driven by data, OMRON’s AI and Data Analysis specialists take on the challenge of digitally Transforming the Group’s entire engineering chain
https://www.omron.com/jp/ja/technology/activities/14/
OMRON’s Digital Design to Support the Creation of Social Needs
https://www.omron.com/global/en/technology/omrontechnics/introduction/introduction_167.html