Core Technology
Core Technology
Zooming in on OMRON’s Digital Design and Transformation Technologies (Part 1 of 2)
—Driven by data, OMRON’s AI and Data Analysis specialists take on the challenge of digitally Transforming the Group’s entire engineering chain. -
Feb.13,2024
The COVID-19 pandemic has catalyzed the rapid expansion of initiatives to resolve social issues by transforming business and management through digital technology. Now that the global epidemic is behind us, a call has become even louder for efforts to make the most of cloud services and AI to create new value by integrating digital and physical technologies.
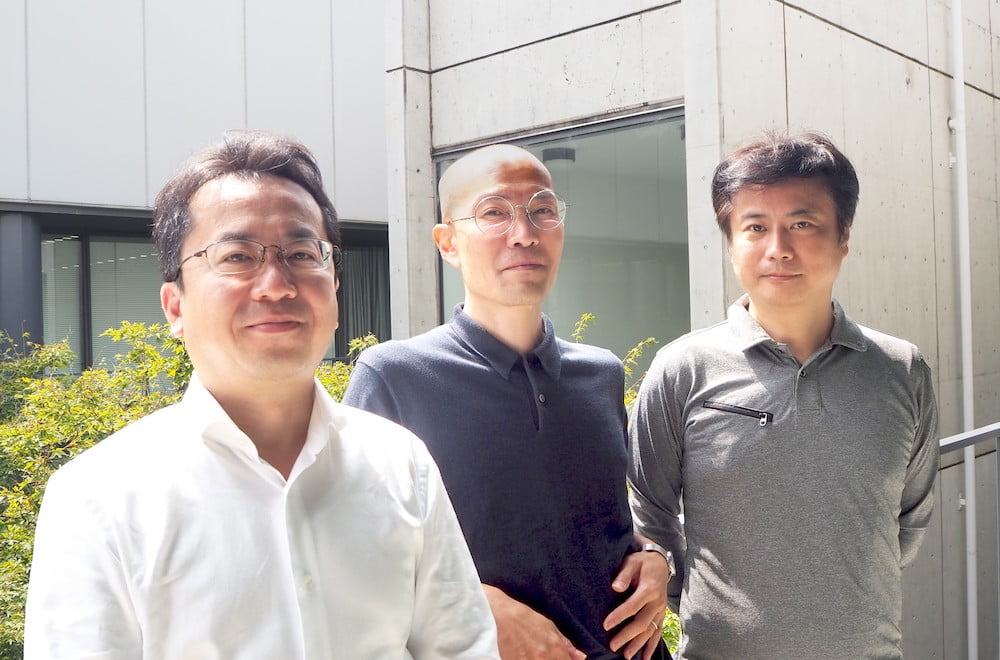
In response to this urgent call, in April 2022, OMRON established the Digital Design Center under the Technology and Intellectual Property H.Q., its corporate R&D division, in a bid to advance its digital technologies, which is essential for digital transformation (DX) of the Group’s engineering chain(1).
To roll out digital technologies that innovate OMRON’s manufacturing throughout the Group, the new center is taking a three-pronged approach of Data Analysis, CAE(2), and AI. Under the lead of Daisuke Matsubara, Naoki Tsuchiya and Akihiro Funamoto are taking on “Data Analysis and AI” and “CAE,” respectively, as they challenge themselves on a daily basis in pursuit of their chosen issues.
In this first story of a two-part series, General Manager Daisuke Matsubara of the Digital Design Center expounds on the vision and future his center aspires to realize, and Naoki Tsuchiya, who has spearheaded their activities since the center’s foundation, talks about “Data Analysis and AI” technologies, which are essential for realizing their aspirations.
(1) A series of business processes of manufacturing companies, from planning conception to design, preparation for production, production, and after-sale services
(2) Computer-Aided Engineering: Using computer software to perform technical calculations, simulation, and analysis
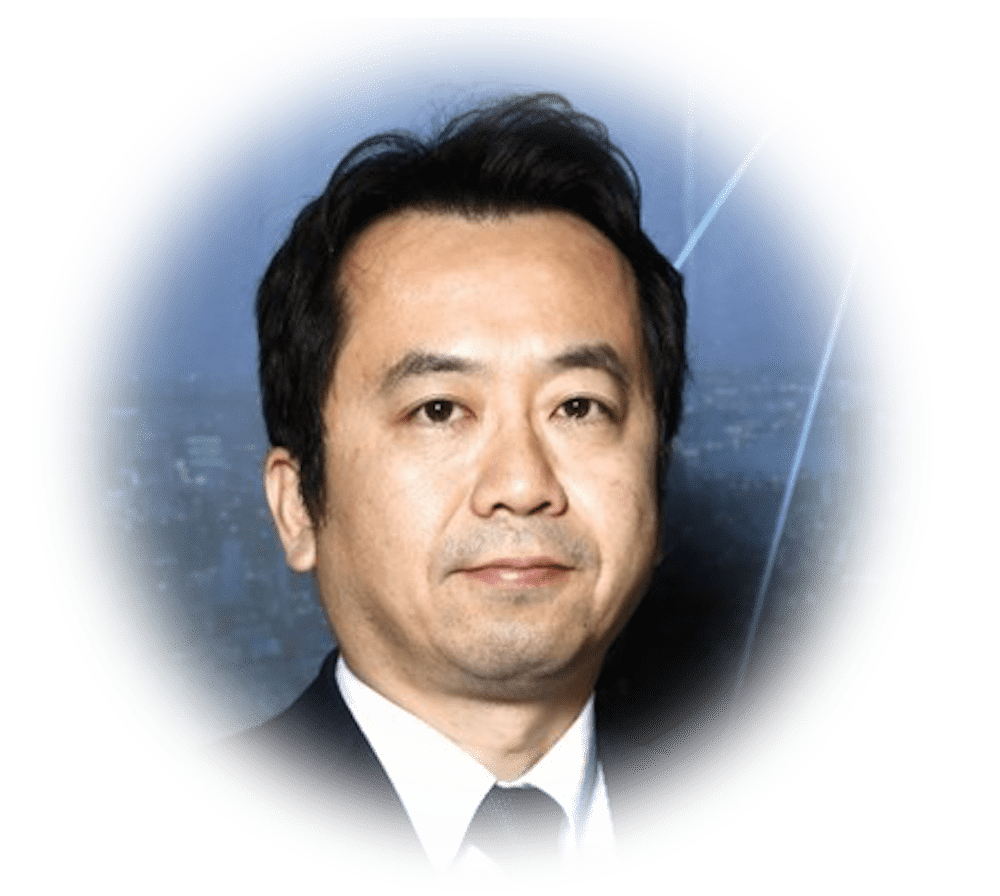
Daisuke Matsubara
General Manager, Digital Design Center
1988: Involved in R&D of data utilization for communication networks/services and IoT/AI at a research institute of a leading electronics manufacturer
2017: Involved in development of new services and start-up of corporate venture capital (CVC) funds through partnerships with start-up companies at a leading non-life insurance company
2019: Involved in development and operation of connected cars and mobility services at a leading auto manufacturer
2022: Joined OMRON to take the lead in promotion of DX for the Group by developing digital technologies (Data Analysis / CAE / AI)
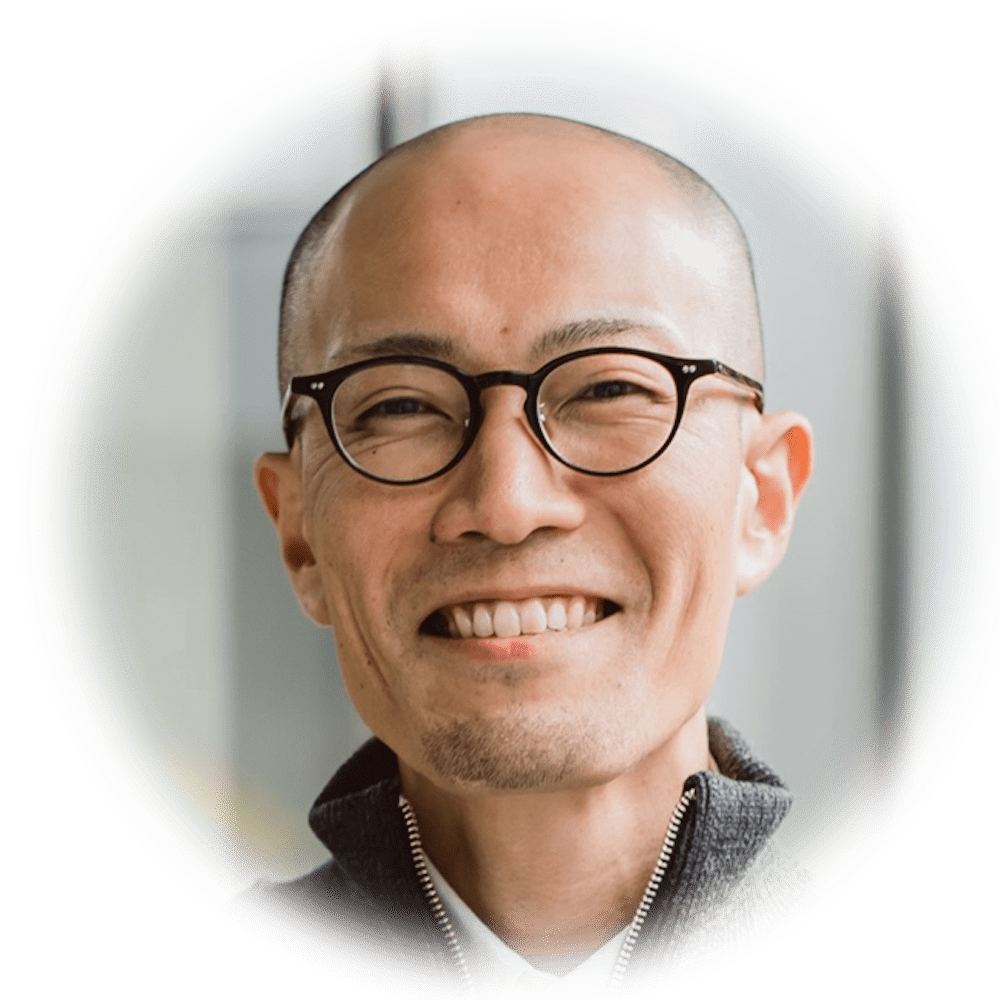
Naoki Tsuchiya
Manager, Digital Design Center
2001: Joined OMRON SOFTWARE Co., Ltd., where he gained experience in software engineering
2005: Transferred to OMRON Corporation to become involved in technological development and information processing in the healthcare field at the Technology and Intellectual Property H.Q.
2018: Took a leading position to manage an AI development base, which was established under the OMRON Tokyo Head Office in Shinagawa to accelerate utilization of AI. Committee member of Institute of Systems, Control and Information Engineering (ISCIE) (2018 – 2022). Committee member of Japan Society for Fuzzy Theory and Intelligent Informatics (SOFT)
2022: Navigating the Data Analysis / AI group at the Digital Design Center of the Technology and Intellectual Property H.Q. to expedite DX of internal operations
Data Analysis, CAE, and AI — The Three-Pronged Approach by the Digital Design Center
What kinds of technologies are you working on at the Digital Design Center?
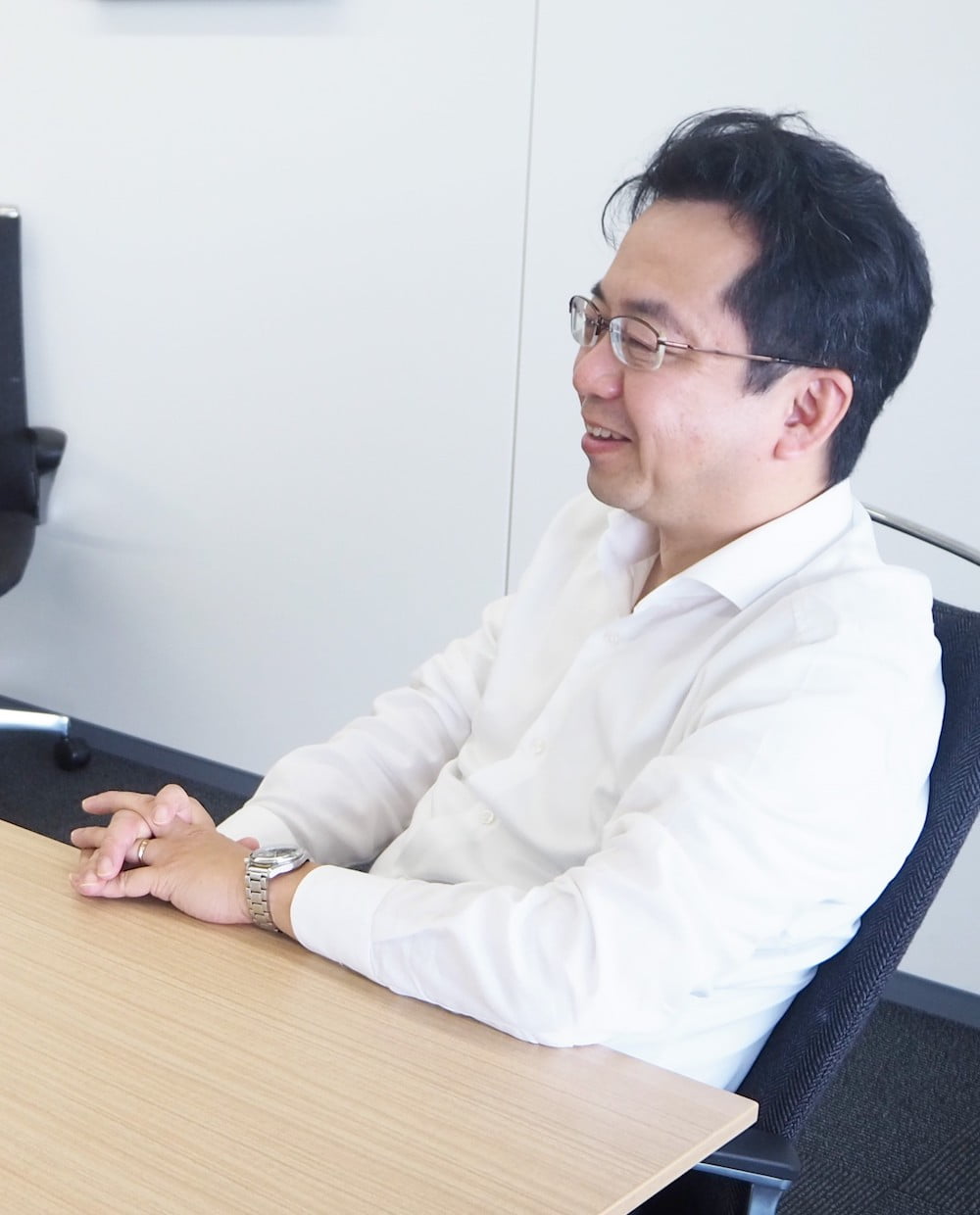
Matsubara: Our goal is to deliver digital technologies indispensable for DX of our engineering chain to every corner of the OMRON Group. I have long been involved in resolving social issues by analyzing data, and this experience has made me realize that we need technologies with which to respond quickly to a broad range of issues. Because we need to address a myriad of social issues that vary from one site to another, we must have a similarly diverse array of digital technologies to capably respond to each uniquely challenging issue.
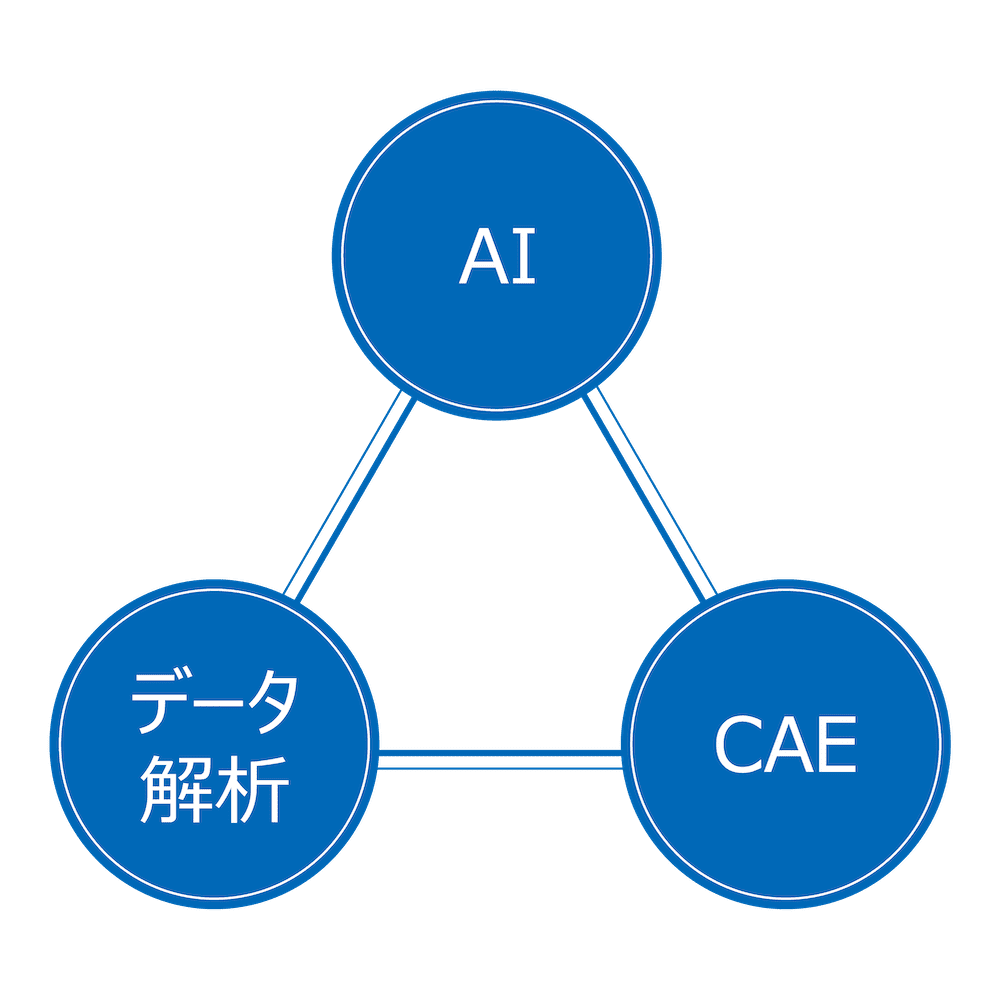
To successfully resolve these challenges, the OMRON Digital Design Center uses a three-pronged approach of “Data Analysis, CAE, and AI” to develop pertinent technologies (Fig. 1). If we possess AI, Data Analysis, and CAE technologies, which form the base of any digital technology, as well as advanced technologies that integrate them, I believe that we can quickly offer technological solutions to a wide variety of challenges.
I don’t see any reason for my team to be given a spot in OMRON’s corporate R&D division if we do not think like a manager and embrace a data-driven(3) approach to contribute to business management and at the same time think in terms of what we can do to contribute to business results by, say, utilizing data to increase efficiency in processes and product competitiveness. With this in mind, we are determined to fulfill the roles we are expected to play.
(3) To base decisions for business solutions on analysis findings of data (sales, marketing, etc.)
Realizing Automation by Making Full Use of Data Analysis and AI
Could you tell us what made you think of contributing to both management and business?
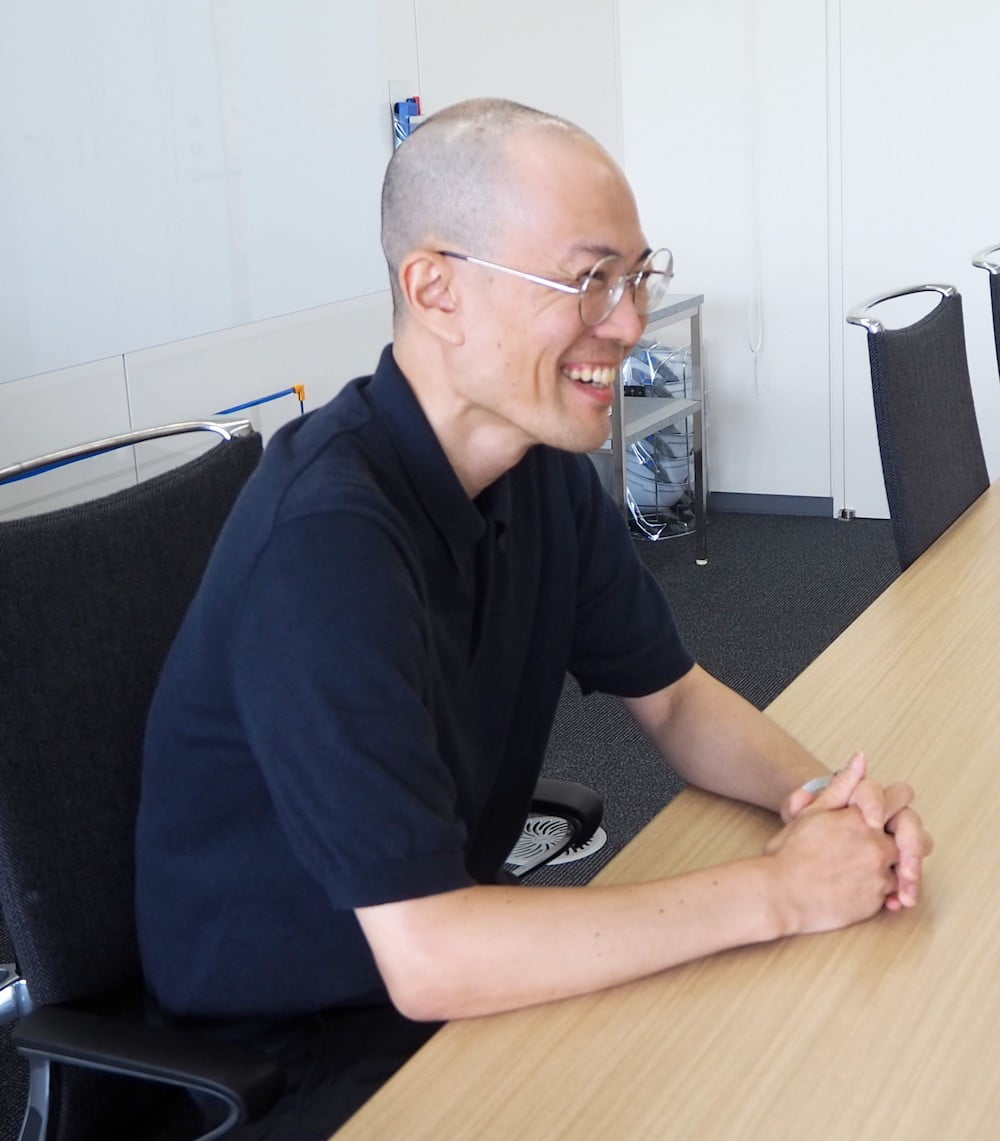
Tsuchiya: When it came time to decide what project themes we should design at the Digital Design Center, I had a series of discussions with many members of OMRON’s production and development teams. On one such occasion, I had the impression that now, as in the past, they often rely on their successful experiences or use the rule of thumb to avoid trouble on-site. Of course, they do so, believing that’s the best option they can choose for now. But it occurred to me that it would be better if they went a bit deeper to analyze and determine causes based on objective information (data). Doing so would help reduce dependence on particular persons and increase efficiency in processes, thus contributing to both business and management. If OMRON wishes to retain its reputation as a company that seriously confronts and finds solutions to social issues, I believe that we should be able to make quick decisions based on data and logic.
Could you give us some examples of what you have done in this regard?
Tsuchiya: Sure. One OMRON production team needed to launch a production facility outside of Japan. Because of the pandemic, however, there was no way they could travel overseas to help with the start-up process. Worse, no one there had the know-how to open a production facility. So, they decided to team up with us to collaboratively seek ways to start up the facility efficiently. We agreed to conduct causality analysis, which we are good at. We made a quantitative evaluation of the causal structure between a production facility and quality characteristics; based on its findings, they made adjustments while making objective decisions on-site, which was a bit of a challenge. At the end of the day, they reduced the time for starting up the facility by 75% from what it used to be.
Wow! A 75% reduction is something! What did you do to make it happen?
Tsuchiya: They take all sorts of data in the field. We make it a rule to immerse ourselves in their situation to fully comprehend what each piece of data means. Not only that, we work closely with our counterparts there to unravel the problems they wish to solve and identify their issues. Our collaboration continues until we assist them in incorporating what we have achieved together into their routine work. In the process, we strongly urge them to make a commitment, say, putting their resources into our joint endeavors, which we need to bring about DX seriously.
I see. What about this cooperative process is unique to OMRON?
Tsuchiya: For one thing, as I mentioned earlier, we work very closely with our counterparts in the field. Because they are very busy pursuing their targets every day, we let them know without fail what effects we think they can expect and convince them of the benefits as we gather data, so that we can build a collaborative framework. The common approach is to start analyzing data once we have all the field data, but our stance is never to hesitate to visit the site to collect data that we think is necessary to accomplish our objectives. Because of this close communication with those in the field, we can hypothesize in advance that, say, “We might not achieve our expected output if we do not obtain such and such data.” The other thing is that we are always looking for what can be commonized from a large variety of diverse products in our four business domains and consider creating digital technologies that can be utilized anywhere, both in and out of the OMRON Group. But this is easier said than done, as categories of data too can be so diverse. All the more so, we believe we can create highly versatile technologies if they can be realized. So, we have this “bounteous” environment, which we consider is where we can show our skills.
Matsubara: I’m on the same page with him. I reckon the core of our mission is to consolidate technologies that we derive as we work in close contact with those in the field, though they may have differences in details, into one single body that we all can share and roll out and implement throughout the OMRON Group.
Could you expand on the first point about working closely with your counterparts in the field? What do you do to get understanding from them?
Tsuchiya: When you visit a place where everyone’s busy doing something, it may not be a good idea to start by asking lots of questions and making requests, like, “Do you have any problems?” or “We would like to have your data,” because you almost always are kept at a distance. If you keep explaining to them what benefits they would get if they cooperate with us, however, they gradually begin to see our activities unravel their problems until their essential issues are revealed. If we go through this process together, it seems they get a sense of us going from one step to another. In this way, we align ourselves with each other to mutually develop a sense like, “I have a feeling that this is going to work out fine.”
What about the second point? You mentioned that commonization is something that lets you show your skills. What do you do to get this done?
Matsubara: OMRON’s operations are so diverse that every workplace has its own unique issues. This being the case, understanding each issue takes a lot of effort in the first place. Locating what is common within a random combination of such diverse issues is a real challenge for us.
Tsuchiya: In our team, each member has their own topic to work on and is held responsible for the outcome of their topics. Through their persistent efforts to maintain close communication, they manage to win the trust of those in the field. But this doesn’t mean that each member acts independently; they frequently exchange information within the team. When needed, they brainstorm on a chosen issue to get everyone within the team involved in drawing up solutions to a given risk.
Matsubara: We have deliberately chosen this methodology because we believe that’s the quickest way for every member to become an expert in their own right. When a problem occurs, I join them in working on solving it. Also, to find common traits among issues, we spare no time looking back into past cases to see if there was a similar one.
Tsuchiya: If I were to give you a tip on finding what is common, it is to see how technologies are used, like “What sorts of problems can this technology solve?” or “Can we apply technologies that we used in a similar field before, as we should be able to use a process of abstraction for this issue?” As a rule of thumb, we can find commonalities where we could reproduce a similar outcome by analogy.
What value do you expect to create through such initiatives?
Tsuchiya: In the case of launching a production line I mentioned earlier, a field leader told me that he thinks it’s important to spread throughout the production floor the process they followed then, namely, elucidating causes based on analysis findings, making decisions based on data, and taking action. Currently, they are taking on the new challenge of applying data-driven solutions to issues faced by other processes of their production lines.
It’s important to know that the effect of these activities cannot be measured in terms of time and cost alone. You also have the experience of successfully increasing efficiency, or learning things you previously didn’t know through the activities. That’s where they can see great value.
In the past, we tended to rely on successful experiences and rules of thumb to come up with the best solution. After the outbreak of the pandemic, however, we suddenly found ourselves unable to “feel” or “communicate,” which forced us to find solutions that were completely different from what we were used to. And I believe that data holds the key to this.
Could you tell us what we can expect from your future initiatives?
Matsubara: The rapid evolution of technology has significantly increased the variety of data that we have to deal with, which in turn makes issues that we need to address incredibly complicated. It’s not easy to cope with those issues in new and broader fields, but we will take on the challenge. Fortunately, we can keep pushing the initiative forward through close communication with people in the field. We are working hard every day with a sense of urgency.
Tsuchiya: Our ultimate goal is to see every single organization within the Group constantly make decisions as they handle relevant data. I believe that the Digital Design Center can be of great use in this process.
Finally, what is the most appealing part of working for OMRON Digital Design Center?
Matsubara: I can get experiences of confronting realistic issues from each workplace and then implementing their solutions in society. It also makes me feel that we are contributing our services to business and management. To reiterate my earlier statement, we are fortunate enough to have as many such experiences as there are job sites. Working for the center, I find it appealing to have such a diverse range of experiences, which concern the engineering chain of each focus domain of OMRON, namely, “Industrial Automation,” “Healthcare Solutions,” “Social Solutions,” and “Device & Module Solutions,” or business at each head office division.
Tsuchiya: Also, working closely with our peers in those fields gives me the experience of creating new value. To locate new issues, solve them, and find their commonalities, we need to keep looking for something new every day to seize the technologies that we need. Doing so gives me exposure to various experiences, which I hope will help sharpen my mind and make me more effective.
――――――――――――――――――――――――――――
What do you think of OMRON’s attempt at DX through the maximum use of data?
If you empathized/resonated with their efforts, why don’t you join them in their endeavor?
In the second part, you will read about CAE leader Funamoto’s aspirations.
We will continue to tackle our challenges. Stay tuned!
You may also like:
OMRON’s Digital Design to Support the Creation of Social Needs
https://www.omron.com/global/en/technology/omrontechnics/introduction/introduction_167.html